Основные направления в развитии теплотехнологических процессов
Федеральное агентство по образованию
Государственное образовательное учреждение
высшего профессионального образования
«Белгородский государственный технологический университет
им. В.Г. Шухова»
Т. И. Тихомирова
И. А. Щетинина
ТЕПЛОФИЗИЧЕСКИЕ ОСНОВЫ И ОРГАНИЗАЦИЯ ТЕХНОЛОГИЧЕСКИХ ПРОЦЕССОВ
Для студентов специальности 10800
Белгород
2010
УДК 666.1.03(075)
ББК 35.41 я7
Ж60
Р е ц е н з е н т:
доктор технических наук, профессор Белгородского государственного технологического университета им. В.Г. Шухова
А.И. Шутов
Жерновая Н.Ф
Ж60 Химическая технология стекла и стеклокристаллических материалов. Ч.2. Физико-химические основы технологии: учебно-практическое пособие/Н.Ф. Жерновая. – Белгород: Изд-во БГТУ, 2009. – 162 с.
В пособии рассмотрены физико-химические основы технологических процессов производства стекла и стеклокристаллических материалов: приготовления шихты, способов её активации, стекловарения, формования и различных способов обработки стекла. Наряду с теоретическими сведениями пособие включает примеры расчетов технологических параметров стадий производства, помогающие понять сущность происходящих процессов и выявляющие их зависимость от различных факторов: способа приготовления шихты, химического состава стекла, температуры, времени и др. Для закрепления теоретических знаний по каждому разделу разработан лабораторный технологический практикум, имеющий исследовательскую направленность, что позволяет студентам приобрести необходимые для будущей работы практические навыки.
|
|
Пособие содержит контрольные вопросы к каждому разделу, итоговые тестовые задания, позволяющие студенту осуществлять самоконтроль.
Учебно-практическое пособие предназначено для студентов дневной, заочной и дистанционной форм обучения специализаций 250806 – Технология стекла, а также может быть использовано при выполнении курсовых, научно-исследовательских и выпускных квалификационных работ.
.
Табл. 41. Ил. 39. Библиогр.: 15 назв.
УДК 666.11.01
ББК 35.41-7
Ó Белгородский государственный технологический университет (БГТУ) им. В.Г. Шухова, 2009
Оглавление
1. Сырьевые материалы и шихта……………………………..5
1.1 Основные правила расчета стекольных шихт………………………5
Работа 1.1 Расчет шихты…………………….……………...……8
1.2. Анализ и оценка результатов расчета шихты.. 11
1.3. Приготовление стекольных шихт. 13
Работа 1.2. Приготовление сыпучей стекольной шихты.. 17
Работа 1.3. Брикетирование стекольной шихты.. 19
Работа 1.4. Гранулирование стекольной шихты.. 20
Работа 1.5. Приготовление тонкомолотой шихты.. 22
|
|
1.4. Окислительно-восстановительные характеристики сырьевых материалов и стекольных шихт 22
Работа 1.6. Расчет окислительно-восстановительного
потенциала шихты.. 26
Работа 1.7. Аналитическое определение химической потребности в кислороде. 28
Контрольные вопросы к разделу 1. 29
2. Стекловарение.. 30
2.1. Основные стадии процесса варки стекла. 30
2.1.1.Силикатообразование. 31
Работа 2.1. Определение расхода тепла. 33
на образование силикатов. 33
2.1.2.Стеклообразование. 34
Работа 2.2. Оценка интенсивности процесса
стеклообразования. 37
Работа 2.3. Изучение скорости растворения
кварцевых зерен. 39
2.1.3.Осветление. 42
2.1.4. Гомогенизация и студка стекломассы.. 44
2.2. Интенсификация процесса стекловарения. 50
2.3. Пороки стекломассы.. 54
2.3.1. Газовые включения. 54
2.3.2. Стекловидные включения. 55
2.3.3. Твердые включения. 57
Контрольные вопросы к разделу 2. 60
3. Формование.. 61
3.1. Основы процесса. 61
3.2. Способы формования. 65
3.2.1.Формование листовых стекол. 65
3.2.2. Формование труб. 72
3.2.3. Формование стеклоизделий. 75
|
|
3.2.4. Формование стекловолокна. 78
Работа 3.1. Расчет и оценка выработочных характеристик тарных стекол 80
Работа 3.2. Моллирование стекла. 83
Работа 3.3. Вспенивание стекла. 87
Контрольные вопросы к разделу 3. 92
4. Термическая обработка стекла.. 93
4.1. Отжиг. ……………………………………………………………..93
Работа 4.1. Расчет режима отжига. 99
4.2. Закалка. 101
Работа 4.2. Расчет режима и закалка стекла. 105
4.3. Кристаллизация стекла. 107
Работа 4.3. Кристаллизация стекла. 111
Работа 4.4. Расчет вероятного фазового состава СКМ... 113
Контрольные вопросы к разделу 4. 117
5. Механическая обработка стекла.. 118
Работа 5.1. Шлифовка и полировка стекла. 121
Работа 5.2. Изучение влияния различных факторов
на скорость процесса шлифования. 124
Контрольные вопросы к разделу 5. 129
6. Химическая обработка стекла.. 130
6.1. Обработка плавиковой кислотой. 131
Работа 6.1. Травление поверхности стекла. 132
6.2. Декорирование стекла силикатными красками. 133
Работа 6.2. Декорирование стекла силикатными красками. 135
Контрольные вопросы к разделу 6. 137
7. Содержание и темы курсовой работы... 137
7.1. Содержание курсовой работы по теме «Разработка рациональной технологии, качественное и количественное описание стадий процесса». 138
|
|
7.2. Темы контрольных работ. 138
8. Итоговые тестовые задания.. 140
9. Глоссарий.. 155
Библиографический Список.. 160
ВВЕДЕНИЕ
Основные направления в развитии теплотехнологических процессов
Энергетика имеет большое значение в жизни человечества. Уровень ее развития отражает уровень научно-технического прогресса.
Энергетика теплотехнологии - новая область промышленности энергетики и новая научная дисциплина, являющееся эффективным инструментомэнергосберегающей политики и прогресса промышленного теплотехнологического комплекса.
Теплотехнология - совокупность методов преобразования исходного сырья, материалов, полуфабрикатов в заданный товарный продукт на основе изменения теплового состояния их вещества.
|

Ниже приводятся основные понятия, которые часто применяются в энергетике теплотехнологии и в теплотехнологических процессах.
Теплотехнологический процесс - элемент теплотехнологии, включающий совокупность элементарных процессов, обеспечивающих конкретное тепловое воздействие на сырье, материалы на отдельных этапах производственного цикла.
|
|
|
Различают одностадийные и многостадийные теплотехнологические процессы. Так, нагрев изделий в нагревательных печах - это пример одностадийного процесса.
Так, при варке стекла различают 5 стадий стекловарения:
1) силикатообразование;
|
3) осветление;
4) гомогенизация;
5) охлаждение.
Технологическая схема производства - наглядная иллюстрация последовательной совокупности технологических процессов производства того или иного продукта.
Технологические схемы используются в производствах различных строительных материалов.
Теплотехнологическая схема - тепловая схема, дополнительно иллюстрирующая используемые теплотехнологические принципы организации
теплотехнологического процесса и нетехнологического использования.
Теплотехнологические процессы занимают одно из ведущих мест среди промышленного производства. К их числу относятся разнообразные технологические процессы, реализующие на основе нагрева, плавления, кипения, охлаждения твердых, жидких, газообразных технологических материалов.
Главной целью в организации технологического процесса является повышение производительности труда с одновременным улучшением качества продукции и снижением ее себестоимости.
Основные взаимосвязанные направления развития теплотехнологии следующие:
1. Увеличение масштабов производства, мощностей химико-технологических систем.
2. Интенсификация работы аппаратов.
3. Снижение энергозатрат и максимальное использование теплоты химических реакций.
4. Уменьшение количества стадий производства и переход к циклическим (замкнутым) системам.
5. Замена периодических процессов непрерывными.
6. Механизация трудоемких операций и автоматизация производства.
Основное преимущество укрупнения аппаратов, т.е. увеличение их объемов бет существенного изменения конструкции - это увеличение производительности, которая пропорциональна возрастанию рабочего объема аппарата.
Производительностью П называется количество выработанного продукта G или переработанного сырья за единицу времени :
(кг/ч или т/ч);
(м3/ч).
Увеличение объема аппарата, как правило, приводит к экономии металла или другого конструктивного материала в расчете на единицу реакционного объема и на единицу вырабатываемой продукции.
Однако увеличение объема аппарата без значительного усложнения его конструкции возможно лишь до некоторого предела в связи с затруднением обслуживания крупных аппаратов. Поэтому намного эффективнее повышение производительности аппаратов за счет интенсификации их работы.
Интенсивностью работы аппарата I называется его производительность, отнесенная к какой-либо величине, характеризующей размеры данного аппарата. Обычно относительная производительность равна объему аппарата и (м3) или площади его сечения S (м2):
Интенсификация достигается двумя путями: а) улучшением конструкций машин или аппаратов; б) совершенствованием технологических процессов в аппаратах данного вида.
Интенсивность работы аппарата пропорциональна скорости процесса, поэтому стремятся к созданию конструкции и технологическому режиму в аппарате, которые обеспечивали бы максимальную скорость процесса.
При разработке улучшенных или принципиально новых конструкций машин и аппаратов интенсивность технологического процесса повышается главным образом усилением перемешивания реагирующих компонентов и увеличением поверхности соприкосновения между взаимодействующими веществами, находящимися в разных агрегатных состояниях.
Основными технологическими путями интенсификации работы аппаратов различных видов являются в одном случае повышение температуры, давления и концентрации реагирующих веществ, с применением катализаторов и перемешиванием реагирующих масс, в другом - понижение температуры, применение вакуума, окисление концентрирующих веществ. Исходя из этого применяются различные параметры технологического режима: температурный от близкой к абсолютному нулю до нескольких тысяч градусов, давления в производственных аппаратах бывают от почти абсолютного вакуума до сотен МПа. Возможность применения высоких температур и давления часто ограничивается стойкостью конструкционных материалов, из которых изготовлена аппаратура, или разложением реагентов, и наконец, экономической эффективностью интенсифицирующих факторов.
Интенсификация целесообразна лишь при условии, что не вызывает большого роста затрат энергии на проведение процесса.
Снижение затрат энергии на единицу продукции достигается:
а) уменьшением гидравлических сопротивлений всех аппаратов и трубопроводов ХТС;
б) максимально возможным снижением затрат на перемешивание реагирующих масс, не приводящим к снижению интенсивности работы аппарата.
Главная мера экономии в теплотехнологических производствах - максимальное использование теплоты химических реакций для нагревания исходных веществ до оптимальной температуры и для выработки пара, являющегося ценным побочным продуктом ряда производств.
Для повышения степени использования теплоты реакций стремятся увеличивать концентрации реагентов, а также размещать теплообменные элементы и трубы паровых котлов преимущественно в реакционной зоне.
Уменьшение количества стадий производства и переход к циклическим (замкнутым) системам приводит к снижению затрат на капитальное строительство и уменьшение себестоимости.
Периодическим называют процесс, в котором порция сырья загружается в аппарат, проходит в нем ряд стадий обработки и затем выгружаются все образовавшиеся вещества. Таким образом, от загрузки до выгрузки продукта проходит определенный период времени. Аппарат не работает (простаивает) во время загрузки и выгрузки. Эти операции связаны с затратами большого количества труда, аппарат работает с неполной интенсивностью при выводе на режим. Периодические процессы сложны в обслуживании, качество продукции нередко меняется в зависимости от режима обслуживания. Время цикла, т.е. продолжительность периодического производственного процесса, всегда больше, чем непрерывного, энергетические затраты выше. Поэтому в настоящее время стремятся заменить периодические процессы непрерывными.
Непрерывными называют процессы, в которых поступление сырья в аппарат и выпуск продукции происходят непрерывно в течение длительного времени. При этом технологические процессы протекают одновременно со вспомогательными и транспортными операциями. Простоев оборудования нет, производительность аппаратов выше. В каждой точке аппарата соблюдается постоянство температуры, концентрации веществ и давления. Поэтому легко вести наблюдение за работой аппаратов, механизировать загрузку сырья и выгрузку продукта, автоматизировать процесс. При непрерывном процессе улучшается качество продукции, облегчается использование теплоты реакции и отходов производства, например газов, так как они выделяются равномерно.
Большинство производств уже работают непрерывно, оставшиеся периодические процессы заменяются непрерывными. Однако, в настоящее время еще нельзя сразу все производства перевести на непрерывные, в одном случае это приводит к ухудшению качества продукции (например, при коксовании), в других - еще не изобретены средства рациональной механизации и автоматизации процесса, в особенности на маломощных и малогабаритных установках.
Сырьевые материалы
Сырьевыми называются материалы, используемые в качестве исходных при получении промышленной продукции.
В подавляющем большинстве случаев технологический процесс получения какого-либо силикатного материала или изделия можно описать следующей общей схемой : добыча сырья и его транспортировка на предприятие ; первичная обработка – обогащение, сушка, измельчение (дробление и помол) , рассев по фракциям ; приготовление технологических смесей – смешивание компонентов, гранулирование или брикетирование смесей, приготовление шихты, шламов или шликеров ; тепловая обработка материалов или отформованных изделий, результатом которой является получение конечного продукта. В процессе производства силикатных материалов или изделий отдельные операции выполняются в различной последовательности, например, первичная обработка сырья может осуществляться прямо в карьере, тогда на завод транспортируется уже подготовленное сырьё. Некоторые операции могут отсутствовать, например, операции гранулирования или брикетирования.
В технологическую линию подготовки сырья в теплотехнологических процессах входят основные стадии:
1. Добыча сырья
Минеральное силикатное сырьё добывают из месторождений, разрабатываемых, как правило, открытым способом. Горное предприятие или отдельное заводское хозяйство, осуществляющее добычу полезного ископаемого открытым способом, называется карьером . Работы в карьере выполняются в несколько этапов. На подготовительном этапе производится подготовка поверхности месторождения к разработке (вырубка леса, корчевание пней, переноска дорог, линий электропередач и т.п.) , а также осушение месторождения и ограждение его от вод поверхностного стока. На втором этапе, называемом строительным периодом, ведется подготовка вскрышных (удаление покрывного слоя, под которым находится полезное ископаемое) и добычных (извлечение полезного ископаемого) работ, строительство транспортных коммуникаций, обеспечивающих доступ к рабочим горизонтам. После добычи (выемки) наступает последний, завершающий этап – рекультивация (восстановление) территории, нарушенной горными работами.
Характер добычных работ зависит от физико-механических свойств полезного ископаемого и определяется ведущими процессами: подготовкой пород к выемке, выемкой и погрузкой.
2. Транспортировка
Добываемое сырье от забоев до пунктов разгрузки ( сырьевой склад завода или железнодорожные вагоны) подвозится карьерным транспортом. Трудоемкость процесса транспортировки весьма высока и составляет от 45 до 70% общих затрат на добычу. Основными видами карьерного транспорта являются железнодорожный, автомобильный, конвейерный и гидравлический. Железнодорожный транспорт целесообразно применять при больших размерах и незначительной глубине карьера, большом годовом грузообороте (более 15 млн. т) и при необходимости транспортировки сырья на расстояния более 4 км. Автомобильный транспорт применяют на карьерах с годовым грузооборотом до 15 млн. т и при транспортировке сырья на большие расстояния. Основным недостатком этого вида транспорта является его зависимость от климатических условий. Конвейерный транспорт применяют для перемещения сырья в рыхлом и измельченном состоянии ( размер кусков до 400 мм). Широкий диапазон изменения производительности конвейерных установок позволяет применять их в карьерах с различным грузооборотом. Преимуществами этого вида транспорта являются возможность преодоления подъемов с уклоном до 18% и поточность перемещения груза, что создает возможность автоматизации процесса и эффективного использования оборудования. Гидравлический транспорт может применяться для перевозки всех видов влажного сырья, особенно если в процессе переработки оно используется в виде шлама. При использовании этого вида транспорта водная суспензия материала перекачивается по трубам насосами. Гидравлический транспорт наиболее приемлем для доставки пластичного сырья ( мела, глины, суглинков, мергеля и др.) и особенно эффективен, если сырьевой материал перерабатывается непосредственно в карьере. Пневматический транспорт служит для перемещения сыпучих или штучных грузов созданием перепадов давления воздуха или газа. Преимущества пневматического транспорта: герметичность, возможность использования установок для нагревания, сушки или охлаждения материалов; простота обслуживания и компактность установок, возможность эксплуатации при любом уклоне пневмотрассы; основные недостатки – сравнительно высокий расход энергии и большая металлоемкость.
3. Обогащение
Использование в технологическом процессе сырья стабильного химического состава в некоторых случаях вызывает необходимость в дополнительной его обработке – обогащении. Обогащением – называется совокупность операций по первичной обработке сырья с целью удаления вредных примесей, пустой породы или разделения минералов. Методы обогащения основаны на разделении компонентов по их плотностям (гравитационное обогащение) . магнитной восприимчивости (магнитное обогащение), физико – химический свойствам поверхностей (флотация) и т.д. стоимость обогащения значительно ниже, если его проводят на крупных обогатительных фабриках, располагаемых на месте добычи сырья.
В технологии силикатов обогащению подвергают кварцевые пески, глинистые и некоторые другие материалы.
3.1. Обогащение кварцевых песков
Кварцевые пески обогащают в тех случаях, когда содержание в них железа и других нежелательных примесей больше допустимого для данного вида изделий. Для обогащения песка применяют различные методы: промывку , флотооттирку, электромагнитную сепарацию, химическую обработку и др.
Промывку применяют в тех случаях, когда песок загрязнен глинистыми примесями. Она осуществляется в классифицирующих конусах, гидромеханических классификаторах и гидроциклонах. Комбинированный метод – флотооттирку – применяют, когда в песке имеются железосодержащие примеси в виде обволакивающей зерна песка пленки. А также в виде легких и тяжелых минералов. Метод флотооттирки включает три процесса: флотацию, оттирку пленки и промывку. Флотация основана на различной смачиваемости поверхности минералов водой. Частицы несмачиваемого (гидрофобного) материала не преодолевают силы поверхностного натяжения воды и остаются на ее поверхности, а частицы смачиваемого (гидрофильного) материала опускаются на дно. Чтобы отделить примеси от песка, используют поверхностно-активные вещества (ПАВ), снижающие смачиваемость минералов примесей водой. Одновременно ПАВ ( например, сульфатное мыло)служат пенообразователями (пена увлекает примеси на поверхность пульпы). При перемешивании пульпы в результате трения зерен удаляется поверхностная пленка оксидов железа. Для лучшей оттирки в пульпу добавляют соду. Флотационная пеня, содержащая загрязняющие примеси, направляется в отвал. В классификаторе от пульпы отделяют крупную фракцию и частично ее обезвоживают. Окончательно песок обезвоживают в центрифугах, а затем подают на сушку.
При содержании в песке примесей, способных улавливаться магнитом. Используется электромагнитная сепарация, которая может применяться в сочетании с другими методами обогащения.
Когда требуется особо тщательное удаление железосодержащих примесей, применяют химические методы обогащения. Сущность их состоит в превращении железосодержащих примесей (пленок оксидов железа, зерен гематита) в растворимые соединения. С этой целью песок обрабатывают различными реагентами: гидроксалатом натрия, серной кислотой, хлороводородом и др.
3.2 Обогащение глинистых материалов
Глинистые материалы подвергают обогащению с целью удаления отощающих (песок) , окрашивающих (железо – и титансодержащие соединения) и других примесей, отрицательно влияющих на технологию производства или свойства изделий.
Каолины обогащают преимущественно микрогравитационным (электролитным) , воздушно-гравитационным (сухим) и гидроциклонным ( безэлектролитным) методами. При обогащении микрогравитационным методом измельченный каолин распускают в воде, содержащей электролиты – разжижители, в бассейнах осаждается песок. После этого суспензия поступает в чаны, куда добавляют коагуляторы (известковое молоко, полиакриламид и т.д.). Затем суспензию обезвоживают в фильтрпрессах, сушат, измельчают, расфасовывают в мешки. В последние годы находит применение гидроциклонный метод обогащения каолинов. Гидроциклоны устанавливают каскадами из отдельных батарей. Отдельный гидроциклон представляет собой сосуд из двух частей: верхней – цилиндрической и нижней – конусообразной. Подается суспензия в гидроциклон под давлением 0,25 – 0,30 МПа по патрубку, установленному тангенциально к боковой поверхности цилиндрической части. Вследствие тангенциальной подачи суспензии в гидроциклоне создаются вихревые потоки и возникают центробежные силы, позволяющие разделять материал по массе и крупности зерен. Более тяжелые частицы примесей отбрасываются к стенкам гидроциклона и выводятся через нижнее отверстие, а частицы каолинита уносятся водой через верхний цилиндр. Преимущество гидроциклонов состоит в простоте их конструкции и высокой производительности.
4. Сушка
Сушкой называется удаление влаги из любых (газообразных, жидких и твердых) материалов. В технологии силикатов приходится иметь дело в основном с сушкой твердых материалов или их суспензий. Сушка материала – это процесс, сопровождающийся тепло- и массообменном между сушительным агентом (воздух, дымовые газы или газовоздушные смеси, перегретый пар и т.д.) и влагой высушиваемого материала. При сушке удаляется, как правило, свободная, капиллярно- и адсорбционно-связанная влага. Испарение влаги из материала или изделия происходит за счет подвода теплоты конвекцией сушильного агента, лучеиспусканием от нагретых поверхностей, созданием в теле электрического поля высокой частоты и другими методами. Испарение влаги из материала может происходить при условии, что окружающая среда не насыщена ею. Следовательно, для успешного протекания процесса сушки необходимо, чтобы концентрация (парциальное давление) водяного пара у поверхности влажного материала была большей, чем его концентрация в окружающей среде
Сырьевые материалы сушат либо в самостоятельном цикле с применением различных типов сушилок, либо в совмещенном сушильно-размольном процессе. Выбор параметров сушки определяется свойствами подвергаемого сушке материала. Например, кварцевый песок можно сушить при любых температурах и скоростях удаления влаги. Глину, доломит, магнезит можно сушить при любых скоростях удаления влаги, но температура нагревания не должна превышать 400 С, так как при более высокой температуре происходят физико-химические процессы, изменяющие свойства этих материалов.
Сушка производится в тепловых агрегатах, называемых сушилами (сушилками), отличающимися по виду обрабатываемого материала, конструкции сушильного пространства, схеме движения материала и сушильного агента и т.д.
5. Измельчение
Является одним из основных процессов в производстве большинства строительных материалов. Предприятия силикатной промышленности используют разнообразное сырье, сильно различающееся по структуре, химическому составу и свойствам (плотности, твердости, механической прочности, вязкости, влажности и др.). Поэтому для измельчения сырьевых компонентов до требуемой степени применяют разнообразные измельчители – дробильные и помольные машины периодического или непрерывного действия.
Одним из важнейших показателей измельчителей является степень измельчения i, представляющая собой отношение среднего (или наибольшего) размера кусков исходного (начального) dH и измельченного (конечного) dk материала:
Процессы, протекающие при измельчении
Целью тонкого помола является увеличение химической активности поверхности материала. Для облегчения протекания реакций, увеличения их скорости необходимо уменьшить размеры частиц до минимальной величины.
Класс измельчения | Размер кусков, мм |
| |
dH | dk | ||
Дробление крупное среднее мелкое Помол грубый средний тонкий коллоидный | 1000 250 20 1-5 0,1-0,04 0,1-0,04 0,1-0,04 | 250 20 1-5 0,1-0,04 0,005-0,015 0,001-0,005 0,001 |
Почти все сырьевые материалы при низких температурах являются твердыми, хрупкими телами с высокой степенью неоднородности. Их зерна имеют макро- и микротрещины различных размеров, а кристаллической решетке свойственны нерегулярность координации, пустоты, дислокации. Поэтому прочность реальных кристаллов в 100 – 1000 раз меньше вычисленной теоретически. В процессе измельчения твердых материалов различают три этапа. На первом этапе (грубый помол) происходит раскрытие крупных и мелких пор, дефекты структуры. Величина работы измельчения пропорциональна величине вновь образующейся поверхности. Второй этап (средний помол), сопровождающийся резким возрастанием сопротивляемости материала измельчению, заключается в разрушении кристаллов. Линейная зависимость величины энергии измельчения от величины удельной поверхности сохраняется. На третьем этапе (тонкий помол) процессу измельчения отдельных кристаллов сопутствуют явления налипания и агрегирования. Линейная зависимость величины энергии разрушения от величины удельной поверхности нарушается. Явления агломерации и налипания при сверхтонком (коллоидном) помоле могут привести к прекращению роста удельной поверхности и даже к ее уменьшению. Энергия, затрачиваемая на измельчение, расходуется на образование агрегатов и на их повторное диспергирование.
При достаточно высокой степени измельчения (разрушение кристаллов) происходят процессы, подобные химической реакции: раскрывающиеся поверхности в момент разрыва связей приобретают электрические заряды различной плотности. При измельчении, например, кальцита соотношение противоположно заряженных частиц Ca2+ : CO32- = 1:1, при помоле флюорита - Ca2+ : F - = 1 : 4. Присутствие кварца ускоряет механохимическое разрушение кальцита за счет возможных обменных реакций. При совместном помоле кварца и известковых пород образуется некоторое количество силиката CaO*SiO2 и выделяется CO2. Разрушение кварца сопровождается разрывом кремний-кислородных связей. Образующаяся поверхность приобретает положительные и отрицательные заряды. Если поверхность излома совпадает с кристаллографическими плоскостями, имеющими одинаковое количество анионов и катионов, то она заряжена отрицательно, так как более крупные ионы O2- выступают над ионами Si4+ . Тонкий помол кварца сопровождается аморфизацией поверхностных слоев в результате пластической деформации кристаллической решетки. Кварц при этом становится более активным. Аморфизация поверхностных слоев наблюдается и при помоле других материалов. При помоле кальцита наряду с аморфизацией выделяется СO2 и образуются CaO и Ca(OH)2 . Тонкий помол магнезита и доломита также сопровождается выделением CO2 . При помоле водных силикатов алюминия разрываются ковалентные связи Si-O-Al с образованием групп [Si]+ и [Al –O-]- , являющихся особенно адсорбционно активным.
Таким образом, взаимодействие отдельных компонентов при совместном их помоле сопровождается образованием новых фаз и разложением сложных веществ.
Дробление
Перед тонким помолом материалы необходимо предварительно дробить до размеров кусков не более 5-8 мм, так как более крупные частицы в мельницах окатываются, резко снижая производительность помола.
Степень измельчения определяется природой измельчаемого материала, конструкцией измельчителя, а также крупностью кусков исходного материала. Для получения высокой стпени измельчения осуществляют постадийное дробление – крупное, среднее и мелкое. Это позволяет повысить эффективность дробления при одновременном снижении расхода электроэнергии. Дву – и трехстадийные схемы дробления применяют на заводах средней и большей мощности, одностадийную схему – на предприятиях небольшой мощности. При наличии в исходном материале пыли и мелких фракций их необходимо предварительно отсеять на грохотах. Это предотвращает возможное переизмельчение материала, снижает расход электроэнергии и износ дорогостоящих деталей измельчителя, выполненных из легированных сталей.
Дробление материалов осуществляют на разнообразных по конструкции и способу измельчения дробильных машинах. Дробильные агрегаты могут работать по открытому и замкнутому циклу. Открытый цикл характеризуется однократным прохождением исходного материала через измельчитель. Готовый продукт при это содержит частицы различной крупности. При использовании замкнутого цикла дробления крупные частицы материала, не прошедшие через грохот, после сортировки возвращаются в измельчитель на повторное дробление. Производительность дробильных агрегатов, работающих по замкнутому циклу, повышается, гранулометрический состав готового продукта получается более равномерным, расход электроэнергии и износ рабочих деталей агрегатов снижается.
Существуют различные способы измельчения твердых тел. Твердые хрупкие материалы лучше всего измельчаются ударом или раздавливанием, пластичные материалы – сочетанием раздавливания и истирания. В зависимости от способа разрушения различают измельчители ударного, ударно – истирающего, раздавливающего, истирающе-раздавливающего, раскалывающего и разламывающего действия, а также каллоидные измельчители. По принципу раскалывающего и разламывающего действия работают щековые, конусные и зубчатые валковые дробилки. Наибольшее распространение среди них при производстве силикатных материалов получили щековые дробилки, применяемые главным образом при крупном и среднем дроблении горных пород высокой прочности, а также различных ферросплавов.
Помол
Тонкое измельчение (помол) широко применяют при производстве вяжущих (цемент, известь, гипс), тонкой керамики, стекла, огнеупоров, сварочных материалов (электроды,флюсы, порошковая проволока) и других изделий. Для тонкого измельчения применяются разнообразные помольные агрегаты, использующие различные способы разрушения материала. Большинство существующих мельниц (вращающиеся, вибрационные, струйные и др.) работает по принципу удара и истирания, при этом материал разрушается под действием ударов мелющих тел или кусков того же материала. Реже применяют мельницы, в которых материал разрушается под действием окружающей (жидкой или газовой) среды (электрогидравлические, кавитационные, ультразвуковые). Каждый из существующих измельчителей позволяет получать материал с определенным диапазоном дисперсности, в котором он является наиболее пригодным и эффективным.
Наиболее широкое распространение при измельчении сырьевых компонентов в керамической, огнеупорной, цементной промышленности, в производстве сварочных материалов, а также при измельчении цементного клинкера получили барабанные шаровые и стержневые мельницы.
Материал в барабанных мельницах измельчается под действием удара и частично истирания свободно падающими или скатывающимися мелющими телами внутри вращающегося барабана. Существует большое количество конструкций барабанных мельниц, отличающихся габаритами, принципом загрузки и выгрузки материала, производительностью ( от нескольких килограмм до десятков тонн в час.) По принципу работы барабанные шаровые мельницы классифицируют на мельницы периодического и непрерывного действия, по способу помола – на мельницы сухого и мокрого помола, по характеру работы – на работающие по открытому и замкнутому циклу, по способу разгрузки – на мельницы с механической и пневматической разгрузкой. Барабанные шаровые мельницы периодического действия имеют низкие технологические и технико-экономические показатели, однако применяются в тонкой и технической керамике для получения высокодисперсных порошков, при мокром помоле керамических масс и глазурей, а также на некоторых предприятиях сварочных материалов при помоле ферросплавов (ферромарганца, ферротитана, ферросилиция). При помоле сырья для тонкой керамики во избежание попадания в продукт железа применяют мельницы с керамическими мелющими телами и керамической футеровкой. Барабанные мельницы непрерывного действия по форме рабочего барабана подразделяют на цилиндрические, конические и трубные цилиндрические, по конструкции загрузочного и разгрузочного устройств – на мельницы с центральной загрузкой и разгрузкой через пустотелые цапфы, с разгрузкой через торцевую решетку и с периферийной разгрузкой через решетку ( мельницы с непрерывным просевом). По способу помола барабанные мельницы классифицируют на мельницы сухого и мокрого помола.
В последние годы при мокром помоле сырьевых материалов широко применяются высокоэффективные барабанные стержневые мельницы, где в качестве мелющих тел используются стальные стержни. Их применение позволяет повысить производительность измельчения на 70-75% и одновременно понизить удельный расход электроэнергии на 25% . При выборе условий помола необходимо учитывать, что при мокром помоле процесс протекает значительно эффективнее, однако мелющие тела изнашиваются интенсивнее. При мокром и сухом помоле небольших количеств материала различной твердости применяют однокамерные мельницы с центральной разгрузкой, а при крупнотоннажном производстве – трубные многокамерные мельницы. Мощные дву- и трехкамерные трубные мельницы применяют на современных цементных заводах, двукамерные трубные мельницы- в производстве извести, керамики и огнеупоров.
Для тонкого и сверхтонкого помола материалов в производстве керамики, стекла,железобетона и других изделий применяют вибрационные мельницы. Измельчение материала происходит в результате многогранного воздействия мелющих тел, подвергающихся вибрации вместе с корпусом. Применение вибромельниц эффективно при помоле материала до размеров частиц 10-20 мкм, и особенно – при помоле до размеров частиц менее 1-3 км.
Вибропомол пока не применяют в производстве фарфора, фаянса и некоторых других видов керамики во избежание загрязнения измельчаемого материала металлом. Однако вибромельницы находят широкое применение при получении ферромагнитной, конденсаторной и высокоогнеупорной оксидной керамики. Успешно применяют вибропомол и в производстве сварочных материалов.
При помоле материалов низкой и средней прочности применяют эффективно работающие среднеходные мельницы – роликовые маятниковые кольцевые шаровые и др.
При работе с мягкими сырьевыми материалами(мелом, мягким мергелем, глиной) для предварительного измельчения и взмучивания сырья применяют глиноболтушки с гидроциклонами. Применение гидроциклона позволяет отделить от глиняного шлама до 70% материала, не требующего дополнительного помола.
В настоящее время для мокрого помола мягкого сырья вместо глиноболтушек и барабанных мельниц применяют мельницы самоизмельчения типа «Гидрофол», в которых процесс помола происходит очень эффективно.
В производстве сварочных материалов при помоле рудо-минерального сырья распространение получили также мельницы с непрерывным просевом. Они компактны, не требуют специальной сортировки материала, однако имеют низкую производительность и не могут быть использованы при помоле влажных, слипающихся и размазывающихся материалов.
Сортировка
Гранулометрический состав материалов
Важнейшей характеристикой измельченного материала является его дисперсность (гранулометрический или зерновой состав). Гранулометрическим составом называется содержание в порошкообразном материале частиц различных размеров, выраженное процентным отношением массы (количества) частиц определенного размера к общей массе (количеству) частиц исследуемого образа. Гранулометрический состав можно описывать содержание отдельных фракций (фракционный состав), т.е. содержанием в порошке частиц в некотором интервале размеров. Более наглядно дисперсность порошков описывается непрерывной кривой, называемой кривой распределения. При построении этой кривой на оси абсцисс откладывают размеры частиц, а на оси ординат – процентное содержание отдельных фракций, получая дифференциальную кривую распределения, либо суммарное содержание всех частиц от начала отсчета до данной точки, получая интегральную кривую распределения. В зависимости от размеров частиц (d,мм), сыпучие материалы делятся на кусковые –d >10; крупнозернистые -2<d<10; мелкозернистые -0.5<d<2.0; порошкообразные -0.05<d<0.50; пылевидные-d<0.05/
Для определения гранулометрического состава сыпучих материалов используют различные методы: непосредственное измерение размеров частиц; ситовый, седиментационный, кондуктометрический и фильтрационный анализы; разделение в поле центробежных сил. Наиболее распространенным является ситовый анализ, заключающийся в разделении порошкообразной смеси на фракции просеиванием через набор сит с ячейками различного диаметра; после просеивания фракции взвешивают. Широко применяется и седиментационный анализ, основанный на различии скоростей осаждения твердых частиц разного размера в жидкости.
При необходимости использования частиц определенных размеров или определенных фракций материала, его подвергают сортировке. В зависимости от свойств перерабатываемых материалов и от требований к гранулометрическому составу применяют различные методы сортировки и очистки от посторонних включений-механический (грохочение), воздушный(сепарация), электромагнитный)сепарация), гидравлический( классификация).
Сухие смеси
Смешивание компонентов
Смешивание – механический процесс, в результате которого отдельные компоненты равномерно распределяются в смешиваемом объеме и образуют однородную смесь. Например, если смешивается пять веществ, массы которых относятся как p:q:m:n:k, то после идеального смешивания в любом малом объеме произвольной точки смеси массы компонентов также должны относиться как p:q:m:n:k.
Степень смешивания (однородность смеси) зависит от соотношения компонентов и их свойств, метода смешивания, конструктивных особенностей смесителей и др. Для оценки качества смешивания наиболее часто используется метод ключевого компонента: из смешиваемой системы выделяют любой один компонент, который называют ключевым, а все остальные объединяют во второй условный компонент. По степени распределения ключевого компонента в массе всего смешиваемого материала (принимаемого за второй условный компонент) судят о качестве смешивания.
Полученные смеси характеризуются рядом свойств, определяющих условия их использования или дальнейшей переработки. Кроме дисперсности порошкообразные материалы характеризуются также текучестью (сыпучестью), сопротивлением сдвиговым усилиям, трением порошкообразного материала о поверхность, скольжением его по наклонной плоскости. Эти характеристики зависят от угла естественного откоса, величины сил внутреннего трения, трения о поверхность, трения скольжения. Угол естественного откоса а образуется линией естественного откоса сыпучего материала и горизонтальной плоскостью. Внутреннее трение порошков обусловлено силами трения скольжения и прилипания в местах контакта отдельных частиц и механическим зацеплением частиц друг за друга. Сила трения порошковых смесей о поверхность определяется шероховатостью (совокупностью микронеровностей) поверхности. Если шероховатость поверхности, по которой движется порошковая смесь, больше шероховатости порошка, то сдвиг происходит не по этой поверхности, а по поверхности порошковой смеси. При Движении плотных порошков возникает трение скольжения в результате зацепления острых краев частиц о поверхность, по которой движется порошковая смесь.
Текучесть (сыпучесть) порошковых материалов характеризуется величиной, определяемой отношением времени высыпания 1кг порошка из конусообразной воронки диаметром выпускного отверстия 15мм и углом конусности 600 ко времени высыпания 1 кг сухого песка. Эта относительная величина показывает, во сколько рас сыпучесть порошкового материала меньше сыпучести сухого песка, которая принята равной 1. Текучими являются только те порошковые смеси, у которых силы сцепления между частицами незначительны. Комкующиеся материалы текучестью не обладают. Текучесть зернистых и порошковых материалов является одним из важных показателей, от величины которого зависит производительность различного транспортного оборудования, скорость истечения продуктов из силосов и бункеров. Повысить текучесть порошкового материала можно введением добавок (0, 5 – 1,0 %) высокомолекулярных спиртов и других органических веществ, бентонитов, кремнийорганических жидкостей.
Способность порошков течь обусловливает их поведение при деформациях в результате внешних воздействий и под действием собственной массы. Порошковые материалы способны как и упруго-пластическим деформациям, обусловленным деформациями самого материала частиц, так и к деформациям структурным, обусловленным перемещением отдельных групп частиц относительно друг друга. При перемещении порошкообразных смесей под действием приложенной нагрузки возникают и упруго-пластические и структурные деформации. Соотношение этих деформаций зависит от свойств порошка и от величины нагрузки. Структурные деформации связаны с изменением объема смеси, а упруго-пластические могут протекать при неизменном объеме. Структурные деформации приводят к уменьшению пористости порошковых смесей, они необратимы и носят разрывной характер.
В процессе технологических переработок порошковых смесей к ним прикладывают сдвиговые усилия, перемещающие смесь на угол, превышающий угол естественного откоса. В результате этого возникают силы сопротивления сыпучего материала, обусловленные тремя группами факторов: механическими – зацепление и заклинивание неровностей поверхности; физическими- сцепление, адгезия, трение скольжения; химическими – взаимидействие оксидных и адсорбированных пленок. Сопротивление порошков сдвигу в основном обусловливается внутренним горением и сцеплением частиц. Большое сцепление имеют влажные порошки с мелкими частицами неправильной формы.
Гранулирование
Гранулирование (грануляция) – технологический процесс, в результате которого высокодисперсные частицы под влиянием различных сил соединяются в более крупные образования – гранулы. Гранулирование необходимо для сообщения веществу улучшенных технологических свойств: предотвращения слипания, увеличения сыпучести, облегчения погрузки и транспортировки, снижение пыления, обеспечения возможности использования материала малыми порциями. Гранулирование может использоваться при подготовке стекольной шихты, производстве портландцемента сухим способом и т.д. Гранулирование происходит под влиянием как сил межмолекулярного взаимодействия, присущих гранулируемым частицам, так и адсорбционных, поверхностно-активных, капиллярных сил, обусловленных введением жидкости, за счет создания между частицами мостиков из твердого тела. Мостики из твердого тела образуются при различных физико-химических процессах. При гранулировании спеканием, плавлением в результате диффузии молекул или атомов в местах микроконтактов частиц возникают мостики из сплавленного материала, твердеющие при остывании. К образованию мостиков между частицами приводят и химические реакции (например, реакция окисления FeO à Fe2O3 ). Мостики между гранулами образуются и при отверждении вязких связующих, которые вводятся в процессе гранулирования либо в расплавленном состоянии, либо в виде суспензии. Возможен также способ связывания частиц твердыми мостиками при кристаллизации растворенных веществ.
Гранулирование пастообразных систем основано на создании определенной структуры в дисперсных системах с высокой концентрацией дисперсной фазы.
В промышленности гранулирование осуществляется сухим и мокрым способами.
Сухое гранулирование осуществляется под воздействием межмолекулярных и электростатических сил, а также в результате непосредственного вдавливания частиц друг в друга при формовании. При сухом гранулировании достаточно прочные гранулы получаются при размерах исходных частиц 0,1-1,0 мкм, так как для более крупных частиц влияние межмолекулярных сил недостаточно для соединения их в гранулы. Электростатические силы, возникающие вследствие трения частиц друг о друга и о рабочие органы аппаратов гранулирования, существенно влияют на процесс сближения частиц и их агломерирование. Соединение частиц, обусловленное силами электростатического притяжения, очень мало и не обеспечивает достаточной прочности гранул. Влажное гранулирование осуществляется соединением сухих частиц жидкой фазой, при этом решающее влияние на процесс оказывают гидродинамические свойства жидкости. При влажном гранулировании наиболее существенным является взаимодействие жидкости и сухих частиц. Различные варианты соединения частиц в гранулы зависят от количественного соотношения твердой и жидкой фаз. Если жидкости для гранулирования недостаточно, то она распределена линзами или мостиками в точках соприкосновения частиц. При увеличении количества жидкости она втягивается порами гранулируемого вещества, и мостики сливаются между собой. Если жидкость полностью обволакивает сухие частицы и ее участки сливаются на поверхности гранул, то сила связывания частиц определяется поверхностным натяжением жидкости на границе с воздухом. Такое состояние является предельным и временным, так как жидкость гранулирования вновь будет смачивать другие частицы, открывая ранее скрытые ею частицы и поры, и в конечном счете прочность влажных гранул будет зависеть от поверхностного натяжения жидкости в порах. При влажном гранулировании одновременно действуют два механизма связывания частиц в гранулы: посредством жидкостных мостиков и под действием сил капиллярного разрежения.
Одним из важнейших показателей качества гранулируемого продукта является гранулометрический состав конечного продукта, выражаемый процентным отношением содержания данной фракции к общей массе материала. Поскольку монодисперсный гранулят технически получить очень трудно, для каждого вида гранулируемого продукта ограничивают верхний и нижний пределы размеров частиц.
Форма гранул зависит как от вида гранулируемого вещества, так и от способа его получения. При гранулировании окатыванием получат гранулы правильной формы – шарообразной, дискообразной, овальной. При прессовом гранулировании получают гранулы в виде цилиндров, в кипящем слое – многогранные.
Структура гранулята также является важной характеристикой его качества и зависит от формы и плотности укладки частиц. Для гранул неправильной формы – пластин, чешуек – характерна хаотическая укладка частиц. Форма, размеры частиц, их шероховатость определяют пористость гранулята. Для сферических гранул вид укладки частиц оказывает решающее влияние на пористость гранулята и на количество точек соприкосновения частиц (координационное число). Последнее влияет на динамические характеристики гранулята – текучесть, угол естественного откоса, внутреннее трение.
Прочность гранул определяет их свойство сопротивляться разрушающим механическим усилиям и напряжениям, под воздействием которых гранулят разделяется на мелкие частицы. Прочность может служить и общей характеристикой гранулята, характеризовать его структуру и силу связывания исходных частиц. Прочность гранул, образованных из полидисперсных частиц, меньше, чем из монодисперсных.
Гранулирование окатыванием осуществляется при непрерывном перемещении гранулируемого материала по поверхности гранулирующего аппарата, что приводит как к образованию и росту гранул, так и к деструкции наименее прочных из них. При окатывании происходят процессы как сухого, так и мокрого гранулирования с образованием твердых мостиков. Из многих возможностей сцепления частиц при окатывании осуществляются только те, которые обеспечивают относительно большую прочность гранул.
Наиболее распространенным способом гранулирования окатыванием является гранулирование во вращающихся аппаратах (барабанных, тарельчатых, конических), устанавливаемых горизонтально или с наклоном. В гранулятор поступает порошок, орошаемый на входе связующей жидкостью. Смоченные частицы агломерируются и, окатываясь, приобретают необходимые размеры и плотность.
При вращении гранулятора часть гранулируемого порошка захватывается стенками и затем падает или сползает вниз. При подъеме гранулы движутся вместе с аппаратом, перемещаясь относительно друг друга до определенной точки, где начинается скатывание, в процессе которого формуются гранулы. По мере продвижения гранулируемого материала от места загрузки в аппарат к разгрузочному концу рост гранул прекращается. Конечные размеры гранул зависят от свойств гранулируемого материала, количества и свойств связующей жидкости.
Окатывание можно осуществлять сухим и мокрым способами. Сухое гранулирование применяется очень редко, так как гранулы из-за незначительных межмолекулярных сил очень непрочны и процесс сопровождается большим пылением. При мокром гранулировании смоченные связующей жидкостью частицы порошка соединяются под действие адсорбционных или капиллярных сил и сил поверхностного натяжения. Хорошо гранулируются гидрофильные материалы. Связующая жидкость вводится форсунками или другими диспергирующими устройствами внутрь гранулятора. Режим подачи жидкости-связки и ее количество влияют на качество гранулята и производительность агрегатов.
Прессовое гранулирование осуществляется в процессе изменения структуры исходной смеси действием механических сил сжатия и сдвига и последующим формованием ее в гранулы нужной формы и размеров. Гранулируемую смесь подвергают объемному сжатию иди сдвигу, переводят в пастообразное состояние с определенной структурой и формуют гранулы, которые имеют высокую дисперсность и прочность, не слеживаются и не пылят.
Прессовое гранулирование обычно ведется мокрым способом в нескольких стадий: подготовительная стадия с операциями классификации, вследствие которой масс структурируется в червячных прессах, валковых машинах или под действием вибрации (для облегчения пластификации вводят небольшое количество ПАВ) ; гранулирование-продавливание структурированной массы через каналы матрицы с отверстиями определенной формы и размеров.
В промышленности прессовое гранулирование ведут в специальных установках, совмещающих все стадии.
Гранулирование в дисперсных потоках осуществляется распылением дисперсной системы в сплошной фазе(воздухе, газе). Принцип гранулирования порошков в дисперсных потоках состоит в интенсивной турбулизации системы. При этом частицы порошков сталкиваются, что приводит к их агломерированию. К гранулированию в дисперсных потоках относится и гранулирование порошков в виброкипящем слое, осуществляемое в струйных грануляторах. Основным недостатком такого гранулирования является образование большого количества пыли.
Брикетирование
В технологии силикатных материалов брикетирование (прессование) сыпучих сырьевых материалов применяют при подготовке глинистого сырья к обжигу на шамот, шихты для варки стекла, утилизации мелких фракций извести, подготовке мела для обжига в шахтных печах. В последние годы в цементной промышленности применяют брикетирование портландцементных сырьевых смесей и пыли цементных вращающихся печей. В производстве сварочных материалов брикетируют электродные обмазки и шихты керамических флюсов.
Брикетирование порошкообразных сыпучих материалов обычно ведет с небольшим количеством технологической связки. При сжатии порошков происходит ряд физических процессов. В начальной стадии уплотнения идет перемещение частиц материала в направлении действия давления прессования с заполнением крупных пор и разрушением мостиков и арок, имеющихся между частицами сыпучего материала. Частицы при этом не деформируются. При дальнейшем увеличении давления прессования частицы порошка не могут свободно перемещаться и заполнять уменьшившиеся поры – начинается деформация частиц порошка. С увеличением давления прессования степень деформации частиц возрастает и увеличивается контактная поверхность частиц формуемой смеси.
На процесс уплотнения порошков существенно влияет и технологическая связка. Увеличение содержания связки ведет к более интенсивному уплотнению при меньших давлениях прессования. На плотность укладки брикетируемых порошков влияет соотношение размеров частиц. Для монофракционных систем, состоящих из изометрических частиц неправильной формы, плотность укладки почти не отличается от плотности укладки шарообразных частиц. В системах, состоящих из различных фракций порошков, плотность может существенно повышаться в результате распределения мелких частиц в промежутках между крупными. Для брикетирования сыпучих порошкообразных материалов оптимальным считается трехфракционный состав смеси с содержанием 60-65% крупной фракции, 25-30% средней и около 10% мелкой при большом разрыве между размерами частиц фракций. Основными технологическими характеристиками брикетированной массы являются структура порового пространства, плотность и прочность брикетов.
Для брикетирования в силикатной промышленности применяют коленно-рычажные прессы, позволяющие осуществлять двуступенчатое сжатие смеси со снятием нагрузки в середине цикла для удаления воздуха; прессование сыпучего материала в виде плоской ленты можно вести на кольцевых и дисковых прессах. Наиболее широко в силикатной промышленности для брикетирования применяются вальцевые прессы. Поверхность валков может быть гладкой и профилированной, позволяющей получать брикет определенных размеров и формы. На вальцевых прессах в зависимости от формы ячеек можно получать брикеты в виде лепешек, линз, шаров 70 – 800г.
Сырьевые материалы для производства стекла условно делятся на две группы: главные и вспомогательные.
Главные материалы содержат оксиды, образующие основу стекла и определяющие его свойства.
Вспомогательные материалы содержат соединения, которые вводятся в стекло для варьирования свойств стекла и ускорения его варки. Это — красители, глушители, осветлители, обесцвечиватели, окислители, восстановители и ускорители.
Сырьевые материалы могут быть разделены также на природные и синтетические. В стеклоделии обычно применяются природные материалы: кварц, карбонаты кальция и магния (известняк, мел, доломит), глиноземсодержащие материалы (полевые шпаты, пегматиты и т. д.). Все другие материалы, как правило, синтетические (сода, поташ, красители и др.). Качество сырьевых материалов (химический состав, примеси, дисперсность и др.) регламентируется соответствующими ГОСТами и ТУ, которые периодически пересматриваются и уточняются.
Дата добавления: 2018-08-06; просмотров: 614; Мы поможем в написании вашей работы! |
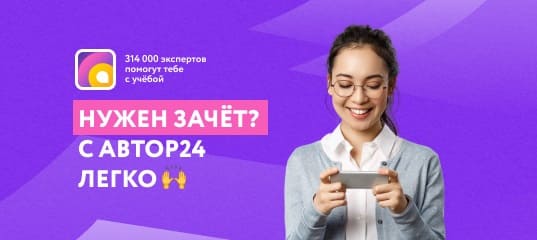
Мы поможем в написании ваших работ!