Расчёт количества сварных постов при автоматической сварке под флюсом
Количество постов для автоматической сварки под флюсом определяем по формуле
(22)
где – эффективный фонд времени сборочного поста:
, (23)
где ПС – продолжительность одной смены, час;(8,2)
ЧС – число рабочих смен в сутках;(2)
ЧД – число рабочих дней в году, дн.;(250)
КП – коэффициент потерь времени работы оборудования (выбирается в зависимости от ЧС, КП = 0,95).
.
Принимаем количество сборочных постов .
Коэффициент загрузки поста для автоматической сварки под флюсом рассчитывается по формуле:
Таким образом, мы принимаем один пост для автоматической сварки под флюсом. Число рабочих смен в сутках – две.
Расчёт количества сварных постов при электрошлаковой сварке
Количество постов для электрошлаковой сварки определяем по формуле
(22)
где – эффективный фонд времени сборочного поста:
, (23)
где ПС – продолжительность одной смены, час;(8,2)
ЧС – число рабочих смен в сутках;(2)
ЧД – число рабочих дней в году, дн.;(250)
КП – коэффициент потерь времени работы оборудования (выбирается в зависимости от ЧС, КП = 0,95).
|
|
.
Принимаем количество сборочных постов .
Коэффициент загрузки поста для электрошлаковой сварки рассчитывается по формуле:
Таким образом, мы принимаем один пост для электрошлаковой сварки. Число рабочих смен в сутках – две.
Конструкторский раздел
Проектирование технологической оснастки
Расчет двухстоечного вращателя с электромеханическим приводом
Рисунок 3.1 – Расчетная схема двухстоечного вращателя с шарнирными крепежными устройствами.
h1 = 69,2 см;
h2 = 72,05 см;
G = 789 кг;
e = 5,67 см;
l1 = 45,95 см;
l2 = 115,86 см;
a1 = 85,71 см;
a2 = 41,1 см;
k = 22,97 см;
R = 30 см.
На рисунке 4. представлена расчетная схема двухстоечного вращателя с шарнирными крепежными приспособлениями. Наибольший крутящий момент воспринимаемый приводом кантователя, равен сумме двух моментов: грузового
и
сил трения в подшипниках обоих шпинделей:
(32)
Рассчитаем массу изделия представленного на рисунке 3.2.
Рисунок 3.2 – Изделие «Коленчатый вал»
Расчет массы изделия представлен на рисунке 3.3.
|
|
Рисунок 3.3 – Расчет массы изделия «Коленчатый вал»
Расчет первой составляющей изделия представлен на рисунке 3.4
Рисунок 3.4 – Расчет первой составляющей изделия
Расчет второй и восьмой составляющих изделия представлен на рисунке 3.5.
Рисунок 3.5 – Расчет второй и восьмой составляющих изделия
Расчет третей, пятой и седьмой составляющих изделия представлен на рисунке 3.6.
Рисунок 3.6 – Расчет третей, пятой и седьмой составляющих изделия
Расчет второй и шестой составляющих изделия представлен на рисунке 3.7.
Рисунок 3.7 – Расчет четвертой и шестой составляющих изделия
Расчет девятой составляющей изделия представлен на рисунке 3.8.
Рисунок 3.8 – Расчет девятой составляющей изделия
Рассчитаем мощность двигателя.
Диаметры шпинделей
dA = dB = 30 см;
dС = dD = 30 см.
Определяем усилия, действующие на хвостовики:
(33)
где G – масса, кг;
h2, h1 – расстояния, см (см. рисунок 3.1).
|
|
(34)
Определяем вертикальные радиальные усилия в подшипниках передней бабки:
(35)
(36)
где l1, a1 – расстояния, см (см. рисунок 3.1).
Определяем вертикальные радикальные усилия в подшипниках задней бабки:
(37)
(38)
где a2, l2 - расстояния, см (см. рисунок 3.1).
В подшипниках передней бабки, кроме того, возникают радиальные усилия под действием окружной силы Q на зубчатом колесе:
(39)
(40)
|
|
где Q = Мгр/R= 4473,63/30 = 149,21,
R – радиус зубчатого колеса, см.
Так как при данном расположении ведущей шестерни или червяка (при червячной передаче) усилия А3 и В3 будут направлены горизонтально, т. е. перпендикулярно вертикальным нагрузкам АВ и ВВ, то суммарные радиальные усилия в подшипниках передней бабки будут равны геометрической сумме двух взаимно перпендикулярных составляющих:
(41)
(42)
Грузовой момент определяем по формуле
где е – эксцентриситет, см.
63 кг см.
Момент сил трения определяется по формуле:
(43)
где – коэффициенты трения (для упорных и радиально-упорных подшипников качения f = 0,02).
Определяем наибольший крутящий момент, воспринимаемый приводом кантователя:
(44)
Определяем общий КПД привода:
(45)
где – КПД червячной передачи и КПД ременной передачи.
Скорость вращения примем равное 850 об/мин.
Определяем мощность приводного двигателя
(46)
Планировка сборочно-сварочного участка
Участок, где осуществляется техпроцесс изготовления изделия, состоит из следующих мест:
1. Склад заготовок.
2. Сборочный пост.
3. Сварочный пост.
4. Место зачистки.
5. Контроля.
6. Склад готовых изделий.
Минимальная ширина прохода между местами составляет 1,5 м. На участке размещены источники питания, щит пожарной опасности, ящик с песком.
К участку подведены магистрали подачи сжатого воздуха, воды, углекислого газа, а также осуществлен подвод электрической энергии, есть противопожарный трубопровод.
Площадь участка составляет 52 .
Ширина проезда 4 м.
План и грузопоток сборки и сварки стойки изображены на чертеже ВКР -15.03.01 - 17. 18 - 0882.
Дата добавления: 2018-08-06; просмотров: 406; Мы поможем в написании вашей работы! |
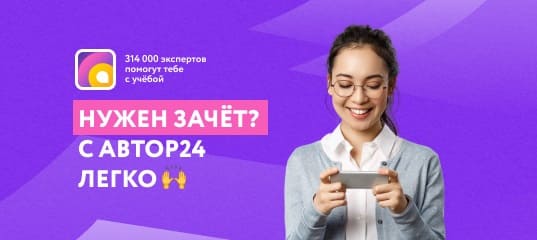
Мы поможем в написании ваших работ!