Автоматическая сварка под слоем флюса
Сварка под флюсом в большинстве случаев используется как автоматический процесс. Полуавтоматическая сварка под флюсом применяется в значительно меньшем объеме, чем автоматическая. Процесс ведется преимущественно в нижнем положении. Объем работ, выполняемых при помощи сварки под
флюсом, из года в год увеличивается. Интенсивное развитие автоматической сварки под флюсом обусловлено высокой производительностью этого способа, стабильным качеством сварки, малым расходом электродного металла и электроэнергии и хорошими условиями труда.
Резкое повышение абсолютной величины тока и плотности тока в электроде без увеличения потерь на угар и разбрызгивание и без ухудшения формирования шва возможно благодаря наличию плотного слоя флюса вокруг зоны сварки; это предотвращает выдувание жидкого металла шва из сварочной ванны и сводит потери на угар и разбрызгивание до 1–3%. Увеличение силы тока позволяет сваривать металл значительной толщины без разделки кромок с одной или, двух сторон (производительность сварки для этого случая определяется в основном глубиной проплавления основного металла) и увеличивать количество наплавляемого в единицу времени металла. Повышение силы тока, увеличеие глубины провара и коэффициента наплавки позволяют повысить производительность и при сварке многослойных швов. Отсутствие брызг – также серьезное преимущество сварки под флюсом, так как отпадает надобность в трудоемкой операции очистки от них поверхности свариваемых деталей.
|
|
При сварке под флюсом обеспечивается высокое и стабильное
качество сварки. Это достигается за счет надежной защиты металла шва от воздействия кислорода и азота воздуха, однородности металла шва по химическому составу, улучшения формы шва и сохранения постоянства его размеров. В результате обеспечивается меньшая вероятность образования непроваров, подрезов и других дефектов формирования шва и отсутствие перерывов
в процессе сварки, вызванных необходимостью смены электродов.
За счет уменьшения доли электродного металла в металле
шва в среднем с 70% при сварке покрытыми электродами до 35%
при сварке под флюсом и уменьшения потерь на угар, разбрызгивание и огарки снижается расход электродного металла и электроэнергии. Отпадает необходимость в защите глаз и лица рабочего и несколько уменьшается количество выделяемых в процессе сварки вредных газов, что улучшает условия труда. Для приобретения квалификации автосварщика необходимо затратить значительно меньше времени и средств, чем для овладения специальностью сварщика, работающего вручную.
Рисунок 1.7 – Схема автоматической сварки под слоем флюса
|
|
1 – подающие ролики; 2 – электродная проволока; 3 – токоподвод;
4 – флюс; 5 – расплавленный флюс; 6 – шлаковая корка; 7 – сварной шов;
8 – сварочная ванна; 9 – газовый пузырь; 10 – дуга.
Электрошлаковая сварка
Метод электрошлаковой сварки, разработанной в СССР сотрудниками Института электросварки им. Е.О. Патона, нашел широкое применение в нашей промышленности и за рубежом. Электрошлаковая сварка является наиболее экономичным способом сварки углеродистых, низколегированных и высоколегированных сталей толщиной свыше 40 мм. В условиях монтажа применение электрошлаковой сварки часто оказывается эффективным и при меньших толщинах свариваемых элементов. Использование этого способа позволяет отказаться от изготовления многих изделий в цельнолитом и цельнокованом исполнении и перейти к более экономичным составным конструкциям с применением сварки. [Куркин СА]
Основной областью применения электрошлаковой сварки является тяжелое машиностроение. Электрошлаковая сварка успешно применяется при изготовлении барабанов паровых котлов высокого давления, станин крупных механических прессов, элементов мощных гидропрессов, валов крупных гидротурбин, цилиндров гидропрессов, станин прокатных станов и другого оборудования. Указанный перечень объектов является далеко не полным и непрерывно расширяется.
|
|
Электрошлаковая сварка в большинстве случаев применяется для сварки вертикальных швов в сочетании с методом принудительного формирования. Поэтому свариваемые детали специально устанавливаются так, чтобы швы занимали вертикальное положение. Свариваемые детали, не имеющие скоса кромок, собираются с обязательным зазором, величина которого находится в пределах 20—30 мм.
Жидкий шлак и расплавленный металл, образующиеся в процессе сварки, удерживаются от вытекания из зазора медными планками-ползунами, охлаждаемыми водой. В пространство между двумя медными планками подается электродная проволока, которая в процессе сварки расплавляется и заполняет зазор между кромками деталей. В первый момент сварки между начальной планкой, установленной в нижней части свариваемого стыка, и электродной проволокой возбуждается электрическая дуга, которая расплавляет флюс, засыпаемый в пространство, ограниченное кромками деталей и охлаждаемыми планками. После того как под воздействием тепла дуги сварочный флюс расплавился и образовалась шлаковая ванна (расплавленный флюс, взаимодействуя с жидким металлом, образует шлак), электродуговой процесс прекращается. Электрический ток начинает протекать через шлаковую ванну, нагревая ее до высокой температуры.
|
|
Подача электродной проволоки в зону сварки и передвижение медных охлаждаемых планок осуществляется специальным сварочным аппаратом. По мере заполнения зазора расплавленным электродным металлом сварочный аппарат передвигается вверх. Поэтому уровень шлаковой и металлической ванны относительно медных планок, перемещающихся вместе с аппаратом, остается постоянным. Однако это обстоятельство действительно только в тех случаях, когда при постоянной скорости передвижения аппарата и постоянной скорости подачи проволоки зазор между кромками сохраняется по высоте строго постоянным. При колебаниях зазора уровень сварочной ванны относительно медных планок будет также изменяться. Значительные колебания уровня ванны могут привести к нарушению процесса сварки. Для предупреждения этого аппараты для электрошлаковой сварки снабжаются схемой автоматического регулирования уровня ванны.
Расплавленный металл сварочной ванны, вследствие теплоотвода в сва-риваемые детали и медные планки, которые обычно называют медными ползунами, постепенно охлаждается и затвердевает, образуя сварной шов.
При электрошлаковой сварке электродом может служить не только тон-кая проволока.
В зависимости от того, какие электроды применяются, различают следующие способы электрошлаковой сварки: а) электрошлаковая сварка электродными проволоками (рисунок 1.8); б) электрошлаковая сварка электродами большого сечения - пластинами (рисунок 1.9).
Рисунок 1.8 – Схема процесса электрошлаковой сварки проволочным электродом:
1 – электродная проволока, 2 – механизм подачи, 3 – формирующее устройство, 4 – шлаковая ванна, 5 – ванна расплавленного металла,
6 – свариваемый металл
Наиболее распространенным в настоящее время является способ элек-трошлаковой сварки с помощью электродных проволок. При этом способе сварка может выполняться одним или несколькими (обычно не более трех) электродами, имеющими возвратно-поступательное перемещение в направлении, перпендикулярном продольной оси свариваемого шва. Количество электродов набирается в зависимости от толщины свариваемых листов.
Электрошлаковая сварка электродами большого сечения принципиально не отличается от электрошлаковой сварки электродными проволоками. В качестве электродов могут применяться пластины и стержни круглого, квадратного и других сечений.
Сварку деталей большей толщины обычно выполняют тремя пластинчатыми электродами. Перед сваркой пластинчатые электроды устанавливаются по середине зазора так, чтобы кромки первого и третьего электрода соответствовали наружным кромкам свариваемых деталей.
Размеры электродов и их количество выбираются в зависимости от размеров свариваемых деталей, формы и размеров завариваемых полостей и отверстий.
Рисунок 1.9 — Схема процесса электрошлаковой сварки пластинчатыми электродами:
1 — электродная пластина, 2 — механизм подачи, 3 — формирующее устрой-ство, 4 — шлаковая ванна, 5 — ванна расплавленного металла,
6 — свариваемый металл.
Электроды большого сечения применяются главным образом при значительной толщине свариваемых деталей и сравнительно небольшой высоте швов (до 1 м). Во многих случаях там, где высота швов небольшая, более целесообразно применение электрошлаковой сварки электродами большого, сечения, чем способа, основанного на применении электродных проволок.
С увеличением толщины свариваемого металла провар по толщине листов становится более равномерным. Более равномерный разогрев шлаковой ванны по всей длине приводит к тому, что глубина металлической ванны при сварке пластинчатым электродом при одинаковых режимах сварки будет меньшей, чем при сварке тонкой электродной проволокой. Непрерывный и равномерный подогрев поверхности металлической ванны благоприятствует более полному удалению газов из жидкого металла и получению швов высокого качества.
Преимуществом электрошлаковой сварки электродами большого сечения по сравнению с электрошлаковой сваркой электродными проволоками является упрощение техники сварки и сварочной аппаратуры.
Электрошлаковая сварка имеет серьезные преимущества не только по сравнению с ручной сваркой открытой дугой, но также и по сравнению с многослойной автоматической сваркой под флюсом. Наиболее важным преимуществом электрошлаковой сварки, как уже было сказано выше, является возможность однопроходной сварки изделий большой толщины. Эта особенность электрошлаковой сварки позволила решить одну из сложнейших проблем современного тяжелого машиностроения — проблему изготовления крупногабаритных стальных изделий без привлечения уникального ковочного и литейного оборудования, при значительном удешевлении и упрощении производства.
При электрошлаковой сварке кромки деталей не требуют специальной подготовки. Поэтому отпадают такие трудоемкие операций как строжка кромок, вследствие чего объем подготовительных работ значительно уменьшается.
Электрошлаковая сварка производится в один проход. Это значит, что не требуется зачистка шлака после наложения каждого слоя, как при многослойной
сварке в нижнем положении. Вследствие этого уменьшается трудоемкость сва-рочных работ, а также улучшается качество швов, так как при недостаточно тщательной зачистке шлака в многослойных швах часто встречаются дефекты в виде шлаковых включений.
При электрошлаковой сварке расход флюса примерно в 15—20 раз меньше, чем при обычной электродуговой сварке под флюсом. Подача флюса в шлаковую ванну в процессе сварки необходима только для того, чтобы компенсировать его расход на образование шлаковой корочки, покрывающей поверхность сварного шва. Толщина такой корочки равна примерно 1,0—1,5 мм.
В отличие от многослойной сварки под флюсом, при электрошлаковой сварке не требуется частая кантовка изделий, так как процесс сварки производится в вертикальном положении.
Электрошлаковая сварка обеспечивает равномерный провар кромок сва-риваемых деталей. При этом форма провара получается симметричной относительно плоскости, проходящей через середину толщины листов, и листы после электрошлаковой сварки не имеют угловых деформаций.
Производительность электрошлаковой сварки значительно (в 10—15 раз) выше производительности многослойной сварки под флюсом, а при сварке некоторых изделий производительность возрастет еще выше.
Значительные преимущества электрошлаковой сварки, слагающиеся из большой производительности процесса, высокого качества швов и значительного уменьшения трудоемкости и стоимости работ, способствуют успешному внедрению этого нового способа сварки на многих заводах различных отраслей промышленности.
Выбор материала изделия
Как известно, любые углеродистые стали можно считать самыми распространенными и массовыми конструкционными материалами, применяемыми в химическом и нефтехимическом машиностроении, строительстве, различных отраслях промышленности. Такие материалы принято классифицировать по нескольким признакам. Так, по своему химическому составу они бывают конструкционными и инструментальными, а по качеству – высококачественными, качественными и обыкновенного качества.
Сталь 15 марки следует относить к конструкционным углеродистым качественным сталям, которые имеют относительно низкое процентное содержание углерода: от 0,12 до 0,19%, т.е. в среднем – 0,15%, что и соответствует 15 марке сплава. Если же данный материал получает дополнительное количество какого-либо легирующего элемента, он повышает свои прочностные и антикоррозионные свойства: например, хромированная сталь 15Х включает в себя не менее 1% хрома (Cr), влияющего и на прочность и на протекание диффузных процессов.
Сталь 15 очень популярна в промышленности, поскольку идет на производство винтов, болтов и прочих деталей, отличающихся высокой пластичностью и прочностью. Диапазон рабочих температур для данного сплава весьма широк: от минус 40 С0 до 450 С0. Прошедшая соответствующую термическую обработку, сталь 15 наделяется высокой поверхностной твердостью, что позволяет получать из нее износостойкие гайки, рычаги, кулачки и другие элементы узлов и механизмов. [http://metallicheckiy-portal.ru/]
Таблица 1.1 – Физические свойства Стали 15
T | E 10- 5 | a 10-6 | l | р | C | R 109 |
С0 | МПа | 1/ С0 | Вт/(м·С0) | кг/м3 | Дж/(кг·С0) | Ом·м |
20 | 2.01 | – | 53 | 7850 | – | – |
100 | 1.92 | 12.4 | 53 | 7827 | 465 | 233 |
200 | 1.85 | 13.2 | 53 | 7794 | 486 | 296 |
300 | 1.76 | 13.9 | 49 | 7759 | 515 | 387 |
400 | 1.56 | 14.4 | 46 | 7724 | 532 | 487 |
500 | – | 14.8 | 43 | 7687 | 565 | 607 |
600 | – | 15.1 | 39 | 7648 | 586 | 753 |
700 | – | 15.3 | 36 | 7611 | 620 | 904 |
800 | – | 14.1 | 32 | 7599 | 691 | 1092 |
900 | – | 13.2 | 30 | 7584 | 708 | 1140 |
Обозначения физических свойств:
Т – Температура, при которой получены данные свойства , С0;
E – Модуль упругости первого рода , Мпа;
a – Коэффициент температурного (линейного) расширения (диапазон 20o – T ) , 1/ С0;
l – Коэффициент теплопроводности (теплоемкость материала) , Вт/(м· С0);
р –Плотность материала , кг/м3;
C – Удельная теплоемкость материала (диапазон 20o – T ), Дж/(кг· С0);
R – Удельное электросопротивление, Ом·м;
Таблица 1.2 – Химический состав в процентах стали 15
C | 0,12 - 0,19 |
|
Si | 0,17 - 0,37 | |
Mn | 0,35 – 0,65 | |
Ni | до 0,25 | |
S | до 0,04 | |
P | до 0,035 | |
Cr | до 0,25 | |
Cu | до 0,25 | |
As | до 0,08 | |
Fe | ~98 |
Термообработка: состояние поставки.
Температура ковки: начала ковки 1300 °С:, конца ковки 700 °С:. Охлаждение на воздухе.
Твердость материала: HB 10 -1 = 149 Мпа.
Температура критических точек: Ac1 = 735 °С, Ac3(Acm) = 860 °С, Ar3(Arcm) = 840 °С, Ar1 = 685°С.
Свариваемость материала: без ограничений, кроме деталей после химико термической обработки.
Флокеночувствительность: не чувствительна.
Склонность к отпускной хрупкости: не склонна.
Обрабатываемость резанием: в горячекатанном состоянии при HB 143
К υ тв. спл=1,8.
Сталь 15 относится к хорошо свариваемым сталям и может быть сварена без подогрева и без обязательной последующей термообработки, которая применяется только в том случае, если необходимо снять внутренние напряжения металла после сварки.
Технологический раздел
Дата добавления: 2018-08-06; просмотров: 573; Мы поможем в написании вашей работы! |
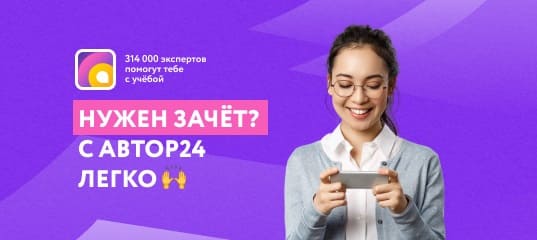
Мы поможем в написании ваших работ!