Термическая обработка титановых сплавов.
Титановые сплавы в зависимости от их состава и назначения можно подвергать всем основным видам термической обработки, а также химико-термической обработке.
Рекристаллизационный отжиг применяют для титана и сплавов с a-структурой для снятия напряжений, созданных предшествующей деформацией. Температура рекристаллизационного отжига должна быть выше температуры рекристаллизации, но ниже температуры аллотропического превращения aÛb, так как в b- области происходит очень быстрый рост зерна. Обычно это температуры 520-8500С в зависимости от химического состава сплава и вида полуфабриката.
Отжиг с фазовой перекристаллизацией применяют для (a+b)- сплавов с целью снижения твердости, повышения пластичности, измельчения зерна, устранения структурной неоднородности. Применяют простои, изотермический и двойной отжиг; температура нагрева 750-9500С (в зависимости от состава сплава).
Простой отжиг предусматривает нагрев (a+b)- сплавов до температуры отжига, выдержку и медленное охлаждение. Образующаяся при нагреве b- фаза (иногда с остаточной a- фазой) при медленном охлаждении распадается и выделяет a-фазу, в результате чего образуется двухфазная структура (a+b), близкая к равновесной.
Изотермический отжиг позволяет получить более термически стабильные свойства титановых сплавов. Изотермический отжиг можно разбить на четыре этапа:
1. Нагрев до температуры выше температуры рекристаллизации (обычно 800-950ОС), для снятия наклепа (I ступень); 2. Охлаждение до 500-650ОС в зависимости от состава сплава; 3. Выдержка при данных температурах для стабилизации b- фазы (II ступень); 4. Охлаждение на воздухе. Изотермическим отжигом достигается высокая прочность и жаропрочность в сочетании с хорошей пластичностью сплава.
|
|
Двойной отжиг отличается от изотермического тем, что после выдержки на высокотемпературной ступени (800-950ОС) сплав охлаждают до комнатной температуры и затем повторно нагревают до температуры II ступени. В процессе охлаждения от I ступени до комнатной температуры в сплаве фиксируется неустойчивая b- фаза, распадающаяся на II ступени отжига. Фактически II ступень при двойном отжиге является старением: образующиеся мелкодисперсные продукты распада упрочняют сплав. Двойной отжиг способствует увеличению сопротивления ползучести.
3акалка применяется только для двухфазных сплавов. В зависимости от химического состава, в первую очередь от суммарного содержания легирующих b- стабилизаторов, в титановых сплавах при закалке может происходить мартенситное превращение или фиксироваться высокотемпературное состояние b- фазы при комнатной температуре, т. е. образовываться нестабильная bнест- фаза. Мартенситное превращение в титановых сплавах происходит сдвиговым, бездиффузионным путем в интервале температур и характеризуется температурой начала (МН) и температурой конца (MК) превращения.
|
|
Схема превращений, происходящих при закалке титановых сплавов в зависимости от содержания b- стабилизатора, показана на Рис.4.28. На этой схеме сплошные линии соответствуют температурам начала и конца полиморфного превращения aÛb, а штриховые - температурному интервалу мартенситного превращения MH-MК.
Рис. 4.10. Схема превращений, происходящих при закалке титановых сплавов в зависимости от содержания b–стабилизатора.
При закалке сплавов, содержащих b-стабилизатора меньше Сaобразуется игольчатая фаза мартенситного типа, называемая a'.
В интервале концентраций b- стабилизатора Сa–С1 процесс закалки протекает так же, как и при концентрациях, меньших С1 с той лишь разницей, что вместо a-фазы образуется a”-фаза.
Фаза a” представляет собой подобно a' фазе твердый раствор легирующих элементов в a-титане, но по сравнению с a'-фазой более насыщена, так как образуется в сплавах с большей концентрацией легирующих элементов; a”-фаза имеет ромбическую решетку.
|
|
При концентрациях b-стабилизатора от С1до CК b-фаза только частично превращается в a”-фазу и образуется структура a”+b. Сохранившаяся b-фаза называется нестабильной (bнест).
Внутри bнест образуется w-фаза, которая когерентна с решеткой b-фазы, имеет искаженную гексагональную кристаллическую решетку, повышает твердость и резко охрупчивает сплавы. При закалке сплавов с концентрацией b-стабилизатора от CК до С3 мартенситное превращение не происходит, и сплавы имеют структуру bнест+w.
При концентрациях b-стабилизатора от С3 до Сb при закалке фиксируется b нестабильная фаза, которая представляет собой твердый раствор легирующих элементов в b-титане.
В процессе нагрева закаленных титановых сплавов происходит старение и образовавшиеся при закалке метастабильные фазы a', a", w и bнест распадаются с образованием более стабильных дисперсных структур.
При температурах старения 500ОС и выше в (a+b): сплавах в зависимости от структуры, полученной после закалки, могут происходить следующие превращения: a¢(a²)®a+b; a"+bнест®a+b; bнест + w®a+b; bнест ®a+b.
В результате распада неравновесных фаз с выделением дисперсных частиц титановые сплавы упрочняются. Наибольший эффект упрочнения получается при распаде bнест- фазы.
|
|
Титановые сплавы подвергают также химико-термической обработке. Для повышения износостойкости трущихся поверхностей применяют азотирование. Получаемый aзoтированный слой имеет глубину 0,1-0, 15 мм и твердость НV 700-1000. Для снижения хрупкости азотированного слоя и повышения его сцепления со сплавом изделия подвергают вакуумному отжигу при 800-900ОС.
Дата добавления: 2018-08-06; просмотров: 489; Мы поможем в написании вашей работы! |
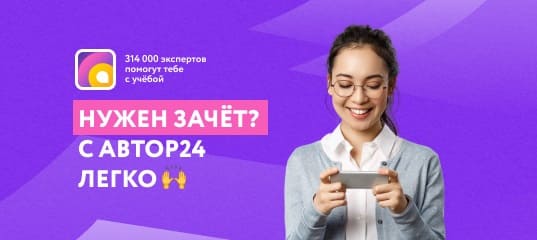
Мы поможем в написании ваших работ!