Термическая обработка алюминиевых сплавов.
Цветные сплавы
К группе широко применяемых цветных металлов относятся алюминий, титан, магний, медь, свиней, олово. Цветные металлы обладают целым рядом весьма ценных свойств, например, высокой теплопроводностью (алюминий и медь), очень малой плотностью (алюминий и магний), высокой коррозионной стойкостью (алюминий и титан).
Магниевые сплавы
Как конструкционный материал магний долго не находил практического применения из-за трудности извлечения его из руд и довольно сложной технологии производства из него полуфабрикатов. Лишь в начале 30-х годов нашего столетия были разрешены основные металлургические проблемы производства магния и началось промышленное его освоение. Судьбу магния как конструкционного материала решила авиационная техника. Магний в 1,6 раза легче алюминия, в 4,5 раза легче железа, что обеспечивает высокую удельную прочность магниевых сплавов, плотность магния 1,74 г/см3. Магниевые сплавы хорошо поглощают механические вибрации, что также имеет важное значение при их применении в авиации, ракетной технике и транспорте. Из-за гексагональной структуры магний и его сплавы значительно уступают алюминию по пластичности, технологичности, особенно при температурах, близких к комнатной и ниже ее. Температура плавления магния 6500С. Диффузионные процессы в магнии протекают медленно и поэтому магниевые сплавы надо длительно нагревать под закалку, что осложняет их термическую обработку. Коррозионная стойкость магния и его сплавов также ниже по сравнению с алюминием и сплавами на его основе, так как магний – химически активный элемент. При нагреве на воздухе до температур порядка 600 0С магний воспламеняется и горит.
|
|
Магний по своим характеристикам занимает промежуточное положение между щелочными металлами и типичными переходными. Магний образует непрерывный твердый раствор только с кадмием. При выборе легирующих элементов прежде всего необходимо учитывать их влияние на механические свойства магния. К числу сравнительно сильных упрочнителей магния относятся: иттрий, кремний, алюминий, цинк и марганец. Однако марганец слабо влияет на временное сопротивление разрыву литых сплавов магния. В области малых концентраций довольно сильное упрочнение оказывает скандий. По влиянию на пластичность магния легирующие элементы можно разбить на две группы: а) элементы, уменьшающие пластичность (марганец, кремний); б) элементы, повышающие пластичность магния при их введении до определенной концентрации (Li, Al, Zn, Sc, Се).
Zr и Ce оказывают модифицирующее действие, уменьшая размер зерна в 80-100 раз. Алюминий и цинк - наиболее распространенные легирующие элементы в магниевых сплавах общего назначения, поскольку они значительно более доступны и менее дороги, чем остальные. К сожалению, упрочняющее действие алюминия и цинка сохраняется лишь до температур 150-200°С. Максимальная прочность магниевых сплавов при комнатной температуре достигается при концентрациях легирующих элементов, близких к пределу насыщения твердых растворов при температурах их максимальной растворимости, прочность сплавов порядка 200-400 МПа.
|
|
Термическая обработка магниевых и алюминиевых сплавов имеет много общего, что объясняется отсутствием в них полиморфных превращений.
Магниевые сплавы, как и алюминиевые, подвергают гомогенизации для повышения технологичности при горячей обработке давлением. Гомогенизацию деформируемых магниевых сплавов часто совмещают с их нагревом под обработку давлением. Нагрев металла при такой совмещенной операции бывает достаточно длительным, но меньшим, чем при гомогенизации, и большим, чем при нагреве под обработку давлением.
Магниевые сплавы подвергают также рекристаллизационному отжигу. Температура начала рекристаллизации чистого магния равна примерно 150 °С, а магниевых сплавов 250...280 °С. Поэтому отжиг магниевых сплавов обычно проводят при температурах примерно 350 °С. При более высоких температурах происходит рост зерна, ухудшающий механические свойства магниевых сплавов. Скорость охлаждения после рекристаллизационного отжига не оказывает существенного влияния на механические свойства магниевых сплавов. Рекристаллизационный отжиг понижает прочностные свойства магниевых сплавов, повышает их пластичность и существенно уменьшает различие в свойствах полуфабрикатов вдоль и поперек волокна.
|
|
Деформируемые полуфабрикаты из магниевых сплавов отжигают также для снятия напряжений. Эту обработку проводят при более низких температурах, чем рекристаллизационный отжиг, сразу же после технологической обработки, создающей остаточные напряжения. При длительном действии остаточных напряжений может произойти нежелательное коробление изделий.
Магниевые сплавы подвергают также закалке с температур порядка 4200С и старению до 2000С (в течение 16-24 ч). Магниевые сплавы также подвергаются термомеханической обработке ВТМО и НТМО. Пересыщенные растворы на основе магния, за исключением сплавов магния с РЗМ, фиксируются при сравнительно небольших скоростях охлаждения. Поэтому магниевые сплавы обычно закаливают на воздухе и иногда в кипящей воде. Естественное старение в магниевых сплавах не происходит, т.е. выдержка закаленных сплавов при комнатной температуре не вызывает никаких изменений структуры и свойств. Исключение составляют сплавы на основе системы Мg-Li. После закалки сплавы подвергают искусственному старению. Продолжительность старения магниевых сплавов значительно больше, чем алюминиевых. При старении сплавов системы Мg-А1 (рис. 4.1) не наблюдается тех сложных промежуточных стадий, которые имеют место при старении сплавов А1-Си. При распаде пересыщенного твердого раствора в магниево-алюминиевых сплавах сразу выделяется равновесная g-фаза. Выделяющиеся мелкодисперсные частицы g-фазы на начальных этапах старения кристаллографически ориентированы относительно матрицы. Они имеют форму пластин. При повышении температуры и длительности старения вторая фаза начинает укрупняться и эффект упрочнения снижается.
|
|
Рис. 4.1. Диаграмма состояния Mg– Al
Деформируемые сплавы магния:
1. Сплавы системы Mg-Al сплав МА5 (8,0 Al и 1,0 Zn).
2. Сплавы системы Mg- Zn являются высокопрочными МА14, МА15, они дополнительно легированы цирконием, кадмием, редкоземельными металлами.
3. Сплавы системы Mg- Zn дополнительно легированы литием (МА21,МА18) относятся к сверхлегким (плотность 1,350 г/см3).
Литейные магниевые сплавы
По химическому составу литейные сплавы близки к деформируемым. Их преимущество в том, что при производстве деталей имеется значительная экономия металла, а качество поверхности отливок почти исключает их обработку резанием. Но литейные магниевые сплавы имеют более низкие механические свойства, из за грубозернистой структуры. Ее улучшают перегревом расплава (увеличивается количество интерметаллидов железа, являющихся центрами кристаллизации), модифицированием (цирконием, магнезитом, мелом), гомогенизацией отливок (4200С, 12-24 ч.). Чаще применяют сплавы системы Mg-Al-Zn (МЛ5, МЛ6), а также используют сплавы легированные цирконием, кадмием, редкоземельными металлами.
Таблица 4.1.
Химический состав и свойства некоторых магниевых сплавов
Сплав | Al | Mn | Zn | Zr | Проч. | sв, МПа | d,% | Т 0С |
МЛ5 | 7,5-9,0 | 0,15-0,5 | 0,2- 0,8 | - | - | 230 | 5 | 150 |
МЛ6 | 9,0-10,2 | 0,1-0,5 | 0,6- 1,2 | - | - | 220 | 4 | 150 |
МЛ10 | - | - | 0,1-0,7 | 0,4-1,0 | 2,2- 2,8 Nd | 250 | 5 | 250 |
МА5 | 7,8-9,2 | 0,15-0,5 | 0,2- 0,8 | - | - | 310 | 8 | 150 |
МА15 | - | - | 2,5-3,5 | 0,45-0,9 | 0,7 La, 1,2 Cd | 320 | 6 | 150 |
МА21 | 4,0-6,0 | 0,1-0,4 | 0,8-2,0 | 3,0 Cd, 7,0 Li | 280 | 25 | 100* |
Примечание: Т – рабочая температура сплава
* - сплав предназначен для криогенных температур
Алюминиевые сплавы
Алюминий легкий (плотность 2,7 г/см3) и легкоплавкий (температура плавления 660ОС) металл, он не имеет полиморфных превращений, кристаллизуется в гранецентрированной кубической решетке с параметром а = 0,404 нм и поэтому обладает высокой пластичностью. Алюминий имеет высокую теплопроводность, а электропроводность его составляет 65% от электропроводности меди.
Алюминий – коррозионностойкий металл. Образующаяся на его поверхности плотная пленка оксида Al2O3 обладает очень хорошим сцеплением с металлом, малопроницаема для всех газов и предохраняет алюминий от дальнейшего окисления и коррозии в атмосферных условиях, воде и других средах. Алюминий стоек в концентрированной азотной кислоте и никоторых органических кислотах (лимонной, уксусной и др.). Минеральные кислоты (соляная, плавиковая) и щелочи разрушают оксидную пленку.
Из-за низкой прочности технический алюминий применять как конструкционный материал нецелесообразно. Его широко используют для изготовления ненагруженных деталей и элементов конструкций, когда основную роль играют его малая плотность, высокая пластичность, коррозионная стойкость, хорошая свариваемость. Высокая электропроводность алюминия, сочетающаяся с малой плотностью, позволили широко использовать его в электротехнике в качестве проводникового материала.
Благодаря высокой теплопроводности из технического алюминия изготавливают теплообменники в холодильных установках. Высокая отражательная способность позволяет делать из него рефлекторы, зеркала, экраны телевизоров. Коррозионная стойкость позволяет широко применять алюминий в химическом машиностроении, пищевой промышленности и строительстве.
Наибольшее количество алюминия расходуется для производства сплавов на алюминиевой основе, которые благодаря их малой плотности позволяют значительно снижать массу конструкций.
Рис. 4.3. Диаграмма состояния сплавов на алюминиевой основе (схема): А - деформируемые сплавы; В- литейные сплавы. I, II – сплавы, не упрочняемые и упрочняемые термической обработкой, соответственно.
По технологии изготовления полуфабрикатов и изделий все применяемые в промышленности алюминиевые сплавы делят на три группы: деформируемые, литейные и спеченные.
Деформируемые сплавы должны иметь высокую технологическую пластичность, так как используются для изготовления деталей различными способами пластической деформации (прокаткой, ковкой, прессованием и т.д.). Поэтому деформируемые сплавы должны иметь однородную структуру твердого раствора на основе алюминия.
Литейные сплавы, предназначенные для изготовления деталей методами фасонного литья (в земляные или металлические формы, под давлением и пр.) должны иметь хорошие литейные свойства - высокую жидкотекучесть, малую склонность к образованию горячих трещин, которые зависят от интервала кристаллизации. Чем меньше интервал температур начала и конца затвердевания сплава, тем выше его жидкотекучесть и, следовательно, способность расплава к заполнению литейной формы сложной конфигурации. Поэтому наилучшими литейными свойствами обладают эвтектические сплавы, так как они кристаллизуются практически при постоянной температуре.
В схематичном виде диаграмма состояния сплавов на алюминиевой основе представлена на рис. 4.3. Сплавы, в которых суммарное количество добавляемых элементов меньше количества, соответствующего точке S, в твердом состоянии будут однофазными, т.е. представляют собой твердый раствор. Такие сплавы должны иметь высокую пластичность, хорошо обрабатываться давлением в горячем и холодном состояниях. Поскольку в них не происходит фазовых превращений, упрочнить такие сплавы термической обработкой невозможно.
В сплавах с содержанием легирующих элементов больше концентрации в точке S при охлаждении выделяются избыточные фазы - вторичные кристаллы. Характер их зависит от состава сплава в соответствии с диаграммами состояния. Избыточные фазы всегда упрочняют сплав, делают его более твердым, более прочным, но менее пластичным. Насколько эффективно влияют вторичные кристаллы, зависит от их свойств, количества, формы и распределения. Чем ближе сплав по составу к точке Е, тем больше эффект от выделения вторичных кристаллов.
В структуре сплавов, лежащих правее точки Е, имеется равновесная эвтектика, не устраняемая никакой термической обработкой. Способность этой группы сплавов к пластической деформации из-за наличия эвтектики резко снижается, а литейные свойства возрастают.
Деформируемые алюминиевые сплавы могут быть классифицированы также по склонности к термическому упрочнению. Способность упрочняться в результате термической обработки зависит от изменения концентрации a-твердого раствора при изменении температуры и от природы упрочняющих фаз, которыми могут быть только интерметаллиды, растворяющиеся в основном a-твердом растворе при нагревании сплава. Следовательно, деформируемые алюминиевые сплавы можно разделить на две подгруцпы: деформируемые, неупрочняемые термической обработкой (левее точки S на схеме диаграммы рис. 4.3), и деформируемые, упрочняемые термической обработкой (находящиеся по составу между точками S и Е). Наконец, все алюминиевые сплавы, как литейные, так и деформируемые, классифицируют по свойствам: сплавы повышенной пластичности, конструкционные, высокопрочные, жаропрочные и др.
Термическая обработка алюминиевых сплавов.
Структура алюминиевых промышленных сплавов в равновесном состоянии, соответствующем диаграмме, должна представлять собой алюминиевый a-твердый раствор c включениями интерметаллидных фаз q(CuAl2), на примере диаграммы Al-Cu (рис. 4.4), S(Al2CuMg), Mg2Si и др. Однако в реальных условиях затвердевания промышленных слитков, а также под действием внешних сил (нагрузки и тепла) происходит изменение равновесного состояния, структуры и свойств сплавов. Получить требуемый комплекс механических и технологических свойств алюминиевых сплавов можно путем термической обработки: отжига, закалки, старения.
Рис. 4.4. Диаграмма состояния Al-Cu
Отжиг
Применяется для устранения неравновесного структурного состояния. Образование неравновесных структур может быть вызвано различными причинами.
Гомогенизирующий отжиг устраняет неравновесные структурные составляющие, возникающие в сплаве вследствие неполноты протекания диффузионных процессов при кристаллизации слитков. Так как в промышленных условиях скорость кристаллизации слитка всегда выше равновесной, в литом металле наблюдается ликвация химических элементов и появляется дендритная ликвация. Неоднородность литой структуры значительно понижает технологическую пластичность сплавов.
В результате гомогенизирующего отжига структура слитка становится более однородной (гомогенной), выравнивается химический состав по сечению зерна. Пластичность слитков в результате гомогенизации значительно возрастает, что положительно сказывается на последующей обработке давлением (прокатке, ковке и др.). Гомогенизирующий отжиг промышленных слитков алюминиевых сплавов проводят при температурах от 450 до 540ОС, выдержка от 4 до 40 ч (в зависимости от состава сплава), охлаждение с печью или на воздухе.
Рекристаллизационный отжиг устраняет неравновесность структуры, возникающую при холодной или горячей деформации. Его применяют как промежуточную операцию при обработке давлением. В результате отжига в деформированном металле снимается наклеп, протекает процесс рекристаллизации, прочность и твердость снижаются, а пластичность возрастает. При выборе температур рекристаллизационного отжига необходимо учитывать, что образующаяся рекристаллизованная структура должна быть мелкозернистой. Отжиг этого вида осуществляют при температурах 350-500ОС в течение 0,5-2 ч.
Неполный отжиг (дорекристаллизационный) дают как окончательную операцию в тех случаях, когда свойства детали должны сочетать прочность и пластичность. Отжиг проводят при температуре ниже температуры рекристаллизации (при 200-350ОС), в результате сплав приобретает полигонизованную структуру, поэтому упрочнение от холодной деформации снимается не полностью.
Закалка
Целью закалки является получение при комнатной температуре структурного состояния, свойственного повышенной температуре, а именно пересыщенного твердого раствора. Закалка алюминиевых сплавов основана на переменной растворимости легирующих элементов в твердом растворе. К таким элементам относятся медь, магний, кремний, цинк, присутствующие в сплавах в определенном сочетании. Легирующие элементы образуют интерметаллидные фазы.
Рассмотрим, как происходят фазовые превращения при закалке на примере сплава Аl + 4,5 % Cuпо диаграмме Al-Cu (рис. 4.4).
В структуре этого сплава перед закалкой имеются кристаллы a-фазы и вторичные кристаллы фазы q (СuAl2). При нагревании до температуры 5000С происходит растворение кристаллов интерметаллида СuAl2вследствие чего в кристаллической решетке a-фазы увеличивается содержание атомов меди от 0,1 % (при комнатной температуре) до 4,5 % (в момент достижения температуры закалки). При последующем охлаждении со скоростью больше критической, при которой затормаживаются диффузионные процессы, атомы меди не могут выделиться из решетки алюминия, поэтому в сплаве фиксируется тот твердый раствор, который получился при нагревании (т. е. с содержанием 4,5 % Си). Таким образом, получается a-твердый раствор, пересыщенный атомами легирующего элемента.
Критическая скорость закалки большинства алюминиевых сплавов достигается путем охлаждения в воде. Целью закалки является получение при комнатной температуре пересыщенного твердого раствора, поэтому важнейшими технологическими параметрами закалки можно назвать температуру нагрева и скорость охлаждения до комнатной температуры.
Температура нагрева под закалку определяет долю растворяющихся в твердом растворе вторичных кристаллов и, следовательно, насыщение его легирующими элементами. Если содержание легирующих элементов в сплаве меньше предельной растворимости их в твердом растворе при эвтектической температуре, то при нагреве можно растворить в твердом растворе все вторичные кристаллы и получить однофазную структуру сплава, содержащую только кристаллы алюминиевого раствора.
В этом случае температура нагрева под закалку может быть выше температуры полной растворимости вторичных кристаллов, т.е. выше температуры растворимости компонентов в алюминиевом твердом растворе. Верхним пределом нагрева под закалку данного сплава может быть температура солидус.
Однако в большинстве промышленных сплавов содержание легирующих элементов больше предельной растворимости их при эвтектической температуре, поэтому в сплаве присутствует некоторое количество эвтектической составляющей. И кроме того в промышленных слитках, затвердевание которых происходит при высоких скоростях охлаждения, диффузионные процессы не успевают происходить полностью, что вызывает дендритную ликвацию и появление неравновесной эвтектики в сплаве. Следовательно, нагревать сплав под закалку без опасения оплавить эвтектику можно до температуры ниже эвтектической. В этом случае растворится большая часть вторичных кристаллов и кристаллов неравновесной эвтектитки, а твердый раствор будет максимально насыщен. Нагрев такого сплава до температуры выше эвтектической неизбежно приведет к неисправимому браку – пережогу: произойдет оплавление эвтектики по границам зерен алюминиевого твердого раствора с одновременным окислением жидких прослоек и последующим образованием усадочной пористости при затвердевании жидкой фазы. При малом объеме оправления будут снижаться в первую очередь характеристики пластичности и вязкости, при большом объеме оплавления снижаются прочность и твердость.
Время выдержки при температуре нагрева должно обеспечить сквозной прогрев изделия и растворение вторичных кристаллов. Увеличение времени выдержки нежелательно, особенно для листов, из-за возможного роста зерна твердого раствора или нарушения плакировки вследствие диффузии легирующих элементов сплава в плакирующий слой.
Характерные структуры сплавов после различных режимов термической обработки представлены на рис 4.5. на примере сплава деформируемого сплава Д16.
Старение
Это заключительная операция термической обработки. Старение, основано на распаде закаленного пересыщенного твердого раствора.
Старение сплавов при комнатной температуре называют естественным; при повышенной - искусственным.
В процессе распада пересыщенного твердого раствора различают три стадии: зонную, фазовую и коагуляционную. На зонной стадии старения создается химическая неоднородность в объеме кристалла пересыщенного твердого раствора, т. е. возникают субмикроскопические зоны с повышенным содержанием легирующего компонента. Эти зоны называют зонами Гинье-Престона по имени исследователей, впервые их открывших в дуралюминах. В зависимости от соотношения размеров атомов алюминия и легирующих компонентов зоны могут иметь форму дисков (в сплавах Al-Cu) или сферическую форму (в сплавах Al-Zn). По мере развития зонной стадии различают зоны Г.П.1 и Г.П.2. Зоны Г.П.l имеют меньший размер, атомы легирующего компонента в них расположены хаотично. Зоны Г.П.2 имеют больший, чем зоны Г.П.l, размер, концентрация атомов легирующего компонента в них возрастает, приближаясь к составу интерметаллидной фазы. Для зон Г.П.2 характерно упорядоченное взаимное расположение атомов алюминия и легирующего компонента.
Фазовая стадия старения развивается по мере повышения температуры. Диффузионные превращения на этой стадии протекают более интенсивно, что приводит к образованию в местах, где образовались зоны Г.П.2, дисперсных частиц промежуточной фазы, которая по своему составу не отличается от стабильной интерметаллиднoй фазы, но имеет отличную от нее кристаллическую решетку. Промежуточная фаза когерентна с твердым раствором. Размер зон Г.П.1, Г.П.2 и кристаллов промежуточной фазы зависит от температуры старения. При повышении температуры увеличивается размер устойчивых при данной температуре зон и промежуточных фаз, а зоны и промежуточные фазы, ранее образовавшиеся при низкой температуре, будут нестабильны и растворятся.
Дальнейшее повышение температуры старения приводит к развитию коагуляционной стадии. На этой стадии образуется некогерентная стабильная интерметаллидная фаза, которая укрупняется (коагулирует) по мере развития процесса.
Изменение свойств алюминиевых сплавов в процессе старения также соответствует рассмотренным стадиям распада пересыщенного твердого раствора.
На зонной стадии многочисленные зоны Г.П. препятствуют перемещению дислокаций, что увеличивает сопротивление сплава пластической деформации. При этом повышаются прочностные свойства без существенного изменения пластических характеристик.
При естественном старении наблюдается только зонная стадия.
На коагуляционной стадии укрупнение выделившихся кристаллов равновесной фазы приводит к разупрочнению сплава.
Эффект упрочнения при старении зависит от природы упрочняющих фаз. Упрочняющими фазами называются интерметаллические соединения, которые растворяются в алюминии при нагреве под закалку и выделяются из пересыщенного твердого раствора при старении. Процессы старения развиваются диффузионным путем, поэтому зависят и от температуры и от времени. При естественном старении упрочнение достигается в течение нескользких суток. Искусственное старение происходит в течение нескольких часов в зависимости от температуры.
Дата добавления: 2018-08-06; просмотров: 1209; Мы поможем в написании вашей работы! |
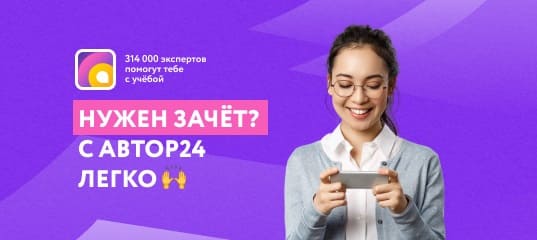
Мы поможем в написании ваших работ!