Промышленные деформируемые алюминиевые сплавы
По уровню прочности сплавы делят на несколько групп (микроструктуры соответствующих сплавов представлены на рис. 4.6):
1. Высокопрочные, термически не упрочняемые АД, АД1, АМц и АМг, хорошо свариваются, коррозионно-стойкие (sвmax=100-250 МПа). Сплавы этой группы Амг5 и Амг6 после отжига имеют sв=320-350 МПа. Используются для изготовления различных полуфабрикатов (листы, профили и т.д.) работающих только при нормальных температурах.
2. Высокопластичные термически упрочняемые сплавы: ковочные АК6, АК8 и типа авиаль АВ, АД13, АД35 (крупногабаритные поковки и профили для вертолетных лопастей) sв=250-350 МПа.
3. Дуралюмины – сплавы средней прочности марки: Д18,В65, Д1, Д16, Д19. Они используются очень широко: от заклепок (Д18, В65) до деталей двигателя и самолета для работы при температурах до 100-1500С. Термическая обработка: закалка с 500±50С, старение естественное или искусственное при 175-1900С. sв=420-520 МПа.
4. Высокопрочные сплавы В95, В96 имеют sв=580-680 МПа, но пониженную пластичность и коррозионную стойкость. Термическая обработка: закалка с 4700С, старение искусственное при t= 120-1400С. Используются для ответственных несущих деталей конструкции самолета, температура эксплуатации – нормальная (<1000С).
5. Жаропрочные сплавы АК4-1, Д20, Д21. Допустимая температура эксплуатации 250-3500С. Термическая обработка: закалка 5300С, старение 190-2200С. Изготавливают детали обшивки самолета, а также поковки и штамповки.
|
|
6. Сплавы пониженной плотности, легированные литием (удельный вес Li 0,5 г/см3). Удельный вес сплавов снижается от 2,85 для В95 до 2,5 г/см3 для сплавов 1420,1440,1460. Сплавы хорошо свариваются.
Состав и свойства некоторых сплавов представлен в таблице 4.2.
Таблица 4.2.
Состав и свойства некоторых алюминиевых сплавов (указан средний состав)
Сплав | Cu | Mg | Mn | Si | Zn | Проч. | sв, МПа | d, % |
АМц | - | - | 1,3 | - | - | - | 170 | 10 |
АМг6 | < 0,1 | 6 | 0,65 | <0,4 | < 0,2 | - | 400 | 10 |
АВ | 0,3 | 0,7 | 0,25 | 0,85 | - | - | 350 | 13 |
Д16 | 4,35 | 1,5 | 0,6 | <0,5 | < 0,3 | - | 480 | 12 |
В96Ц1 | 2,3 | 2,65 | 0,55 | <0,3 | 8,5 | 0,13 Zr | 660 | 8 |
1420 | - | 5,5 | - | 0,2 | - | 2,1 Li, 0,12 Zr | 450 | 10 |
АК4-1 | 2,3 | 1,5 | - | - | - | 1,1Fe | 400 | 8 |
АЛ2 | 0,6 | - | - | 11,5 | - | 170 | 6 | |
АЛ19 | 4?9 | - | 0,8 | - | - | 0,25 Ti | 340 | 4 |
Промышленные литейные сплавы
Литейные алюминиевые сплавы. Сплавы для фасонного литья должны обладать высокой жидкотекучестью, сравнительно небольшой усадкой, малой склонностью к образованию горячих трещин и пористости в сочетании с хорошими механическими свойствами, сопротивлением коррозии и др.
Высокими литейными свойствами обладают сплавы, содержащие в структуре эвтектику. Поэтому содержание легирующих элементов в литейных сплавах выше, чем в деформируемых.
|
|
Наиболее известны сплавы системы Al-Si, получившие название силуминов. Типичным силумином является эвтектический сплав АЛ2, содержащий 10-13 % Si. Сплав имеет хорошие литейные свойства: низкую температуру плавления, высокую жидкотекучесть, малую усадку и др.
Двойные сплавы не обеспечивают высоких механических свойств. После модифицирования сплавов АЛ2 имеет sв=150 МПа, d=4% и твердость НВ 500МПа (литье в землю) рис. 4.7.
Для повышения прочности двойные силумины дополнительно легируют Mg, Cu, Zn. Сплавы АЛ4, АЛ9, АЛ7, ВАЛ1, АЛ19 имеют sв=250-300 МПа.
Коррозионно-стойкий сплав АЛ8 используется для деталей судостроительной отрасли.
Спекаемые сплавы
Спекаемые сплавы типа САП и САС изготавливают методами порошковой металлургии. САП – спеченная алюминиевая пудра является сплавом алюминия с окисью алюминия.
Сплавы САП по своим прочностным свойствам и жаропрочности при 300-500° с значительно превосходят все известные стареющие алюминиевые сплавы и могут при этих температурах работать длительное время (до 10000 ч и выше), сохранять стабильность свойств и структуры.
Так, например, при повышении температуры с 20 до 5000Скратковременная прочность САП понижается в 3-3,5 раза, в то время как для стареющих алюминиевых сплавов прочность снижается в 20-25 раз.
|
|
САП характеризуется высокой коррозионной стойкостью, он удовлетворительно сваривается контактной сваркой и плавлением. Материалы САП можно применять для кратковременной работы при температуре до 1000° С, а для длительной- при 300-500°С.
Спеченные алюминиевые сплавы САС получают путем прессования и последующего спекания легированных алюминиевых порошков или смесей порошков алюминия с легирующими компонентами.
Наиболее распространен сплав САС1 (25-30% Si, 5-7% Ni, остальное А1). Он имеет наиболее низкий из всех алюминиевых сплавов коэффициент линейного расширения (при 20°С a= 14,5-15,5.10-6), характеризуется повышенными упругими свойствами (Е = 80000 МПа) и высокой жаропрочностью (при 200°С sв= 180 МПа, slOO = 110 МПа, при 300° с sв= 145 МПа, slOO = 60 МПа).
Для приготовления сплава САС1 обычно используют легированный алюминиевый порошок с размерами частиц не более 100 мкм,полученный распылением жидкого сплава, отвечающего его составу. Из этого сплава освоено производство прутков, получаемых горячим прессованием спечных заготовок при 5500С.
Сплав САС1 удовлетворительно обрабатывается резанием, обладает хорошей герметичностью и удовлетворительно сваривается стыковой сваркой (прочность сварного соединения составляет 90% от прочности основного металла).
|
|
Материалы типа САС в основном применяются для деталей, работающих при температурах до 2000С.
Титановые сплавы
Титан – металл серебристо-белого цвета IV переходной группы периодической таблицы Д.И.Менделеева. Тпл.=1665±5°С; g=4,5г/см3. Титан немагнитен, является парамагнитным металлом. Титан обладает полиморфизмом (TiaÛTib (882°C)). Низкотемпературная модификация Tia имеет гексагональную плотноупакованную кристаллическую (ГП) решетку с параметром а=0,296 нм; с=0,472 нм. Высокотемпературная модификация имеет ОЦК решетку с а =0,332 нм. По коррозионной стойкости в пресной и морской воде титан превосходит нержавеющие стали. Высокая коррозионная стойкость титана обусловлена образованием на поверхности изделий плотной защитной оксидной пленки – рутила TiO2.
Титан активно взаимодействует с водородом. Максимальная растворимость водорода в Tia составляет при 335°С 0,18%Н, при 20°С – 0,002%Н, в результате чего образуются тонкие, хрупкие вторичные кристаллы g¢(TiH2), располагающиеся в первую очередь по границам зерен, а при большом их количестве и по телу зерен, резко повышая хрупкость титана и его сплавов вплоть до возникновения макро и микротрещин. Водородная хрупкость особенно опасна в сварных конструкциях из титана и его сплавов из-за возникающих при сварке напряжений.
Титан при достаточно высоких температурах активно взаимодействует с другими газами, такими, как O, N, C, образуя твердые растворы внедрения, твердые и хрупкие химические соединения – оксиды, нитриды, карбиды, которые резко снижают коррозионную стойкость, ударную вязкость и способность к пластической деформации и сварке. Титановые сплавы обладают повышенной вязкостью и низкой теплопроводностью, что ухудшает их обрабатываемость резанием.
С целью улучшения комплекса физико-механических и химических свойств титан легируется различными химическими элементами.
По влиянию на температуру полиморфного превращения Ti все легирующие элементы можно разделить на 4 группы:
1) a - стабилизаторы, повышающие температуру полиморфного превращения и расширяющие область существования a-фазы (Al; O; N; Ga; C).
2) Нейтральные упрочнители, не влияющие на температуру полиморфного превращения (Sn, Zr, Ge, Hf, Th). Практическое значение имеют олово, который увеличивает sв и жаропрочность без значительного снижения пластичности, и цирконий, увеличивающий предел ползучести сплавов.
3) b - стабилизаторы, понижающие температуру полиморфного превращения, которые в свою очередь классифицируются на b - эвтектоидные стабилизаторы (H; Cr; Mn; Fe; Ni; Cu; Si) и
4) b - изоморфные стабилизаторы (V; Nb; Mo).
а)
б)
в)
г)
Рис. 4.9. Схема влияния легирующих элементов и примесей на температуру полиморфного превращения титана а) a-стабилизаторы, б) эвтектоидообразующие b-стабилизаторы, в) изоморфные b-стабилизаторы, г) нейтральные упрочнители
В зависимости от содержания тех или иных легирующих элементов титановые сплавы имеют различную структуру при комнатной температуре. По структуре титановые сплавы классифицируют на группы:
1) a–сплавы;
2) a+b– сплавы;
3) b– сплавы;
4) сплавы на основе интерметаллидов, в том числе сплавы с «эффектом памяти формы».
a - фаза более жаропрочна, чем b фаза, a стабилизатор алюминий значительно повышает прочностные характеристики Tia и уменьшает пластичность, особенно при введении алюминия более 7%, когда в структуре титановых сплавов появляется фаза a2 (сверхструктура) – ГП решетка с упорядоченным расположением атомов, что резко понижает пластичность сплавов.
Сплавы с b структурой отличаются от a - сплавов предельно насыщенной концентрацией, более высокой прочностью. Поэтому прочность двухфазных (a+b) сплавов аддитивно возрастает при переходе от a к (a+b) сплавам и максимальные значения прочности отличаются в сплавах (50% a+50%b).
Меняя количественное соотношение a и b фаз, получают конструкционные материалы с большим диапазоном прочностных и пластических характеристик.
Дата добавления: 2018-08-06; просмотров: 684; Мы поможем в написании вашей работы! |
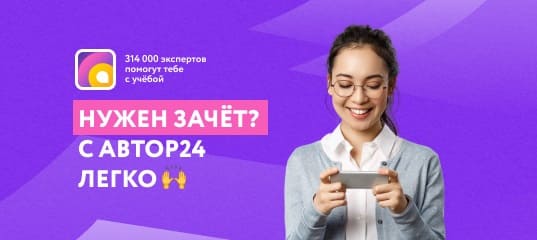
Мы поможем в написании ваших работ!