Нормирование операций сборки металлоконструкции
Сумма затрат основного и вспомогательного времени, а также времени на обслуживание рабочего места, на отдых и естественные надобности, называется нормой штучного времени. Норма штучного времени Тш в общем виде определяется по формуле:
Тшт=То+Тв+Топ+Тотд+Тпз, (10)
где То– основное время;
Тв– вспомогательное время; мин
Торг– время на организацию рабочего места; мин
Тпз– подготовительно-заключительное время; мин
Тотд– время на отдых естественной надобности, мин
Произвожу расчет нормирования сборки узла 1
Топ=1,3+0,4+0,27+0,45=2,4 мин
Торг=2,4×10%=0,24 мин
Тотд=2,4×6%=0,14 мин
Тпз–принимается 10 мин.
Тшт=2,4+0,24+0,14+10=12,7 мин
Дальнейшие расчеты проведены аналогичным способом и представлены в таблице 20 и таблице 21.
Таблица 20 –Нормирование сборки узлов металлоконструкции «Поворотный элемент крана» базового технологического процесса
Топ | Торг | Тотд | Тпз | Тшт | |
Узел 1 | 2,4 | 0,24 | 0,14 | 10 | 12,7 |
Узел 2 | 1,8 | 0,18 | 0,11 | 10 | 12 |
Узел 3 | 1,4 | 0,14 | 0,08 | 10 | 11,6 |
Узел 4 | 7 | 0,70 | 0,42 | 10 | 18,12 |
Продолжение таблицы 20
Узел 5 | 6,2 | 0,62 | 0,37 | 10 | 17 |
Узел 6 | 5,9 | 0,59 | 0,35 | 10 | 16,8 |
Таблица 21 –Нормирование сборки узлов металлоконструкции «Поворотный элемент крана» проектного технологического процесса
Топ | Торг | Тотд | Тпз | Тшт | |
Узел 2 | 1,8 | 0,18 | 0,11 | 10 | 12 |
Узел 3 | 6,2 | 0,62 | 0,37 | 10 | 17 |
Узел 4 | 7 | 0,7 | 0,42 | 10 | 18,1 |
Узел 5 | 5,9 | 0,59 | 0,35 | 10 | 17 |
Узел 6 | 1,4 | 0,14 | 0,08 | 0, 10 | 11,6 |
|
|
Полное время сборки узлов равно Тшт.общ.=109,10 мин (базовый процесс)
Полное время сборки узлов равно Тшт.общ.=88,40 мин (проектный процесс)
Нормирование операций сварки металлоконструкции
Расчет нормирования сварки узла 1.
Тшк = (То +Твш) × L × Кобс × Квио × КI, (11)
где Тшк–штучно калькуляционное время сварки, мин
То–основное время сварки, мин
Твш– вспомогательное время, зависящее от длины свариваемого шва мин, определяю по сборнику нормативов
L–длинна шва, м
Кобс– коэффициент к оперативному времени, учитывающий затраты времени на обслуживание рабочего места и личные потребности
Квио– коэффициент к оперативному времени, учитывающий вспомогательное время, зависящее от свариваемого изделия на оборудование
КI–коэффициент, учитывающий подготовительно–заключительное время
, (12)
где То – основное время сварки мин/пог.м
L–длина свариваемого шва, м
F–площадь поперечного сечения шва, мм2
|
|
γ–удельный вес наплавки, гр/см3; 7.85г/см2
Iсв–сила сварочного тока, А
αн–коэффициент наплавки, г/А×ч
То=18,2×2,2×7,85×60/9,9×160=11,9 мин
Тшк=(11,9+1,95) ×1,1×1,1×1,04=17,4 мин
Дальнейшие расчеты проведены аналогичным способом и представлены в таблицах 21 и 22.
Таблица 21 –Нормирование сварки узлов металлоконструкции «Поворотный элемент крана» базового технологического процесса
То | Тнш | L | Кобс | Квио | КI | |
Узел 1 | 9 | 10,8 | 2,20 | 1,1 | 1,04 | 1,04 |
Узел 2 | 12 | 14,2 | 0,78 | 1,1 | 1,04 | 1,04 |
Узел 3 | 7,5 | 9,3 | 0,4 | 1,1 | 1,14 | 1,04 |
Узел 4 | 8,3 | 10,2 | 3,20 | 1,1 | 1,1 | 1,04 |
Узел 5 | 12 | 14,3 | 0,95 | 1,1 | 1,1 | 1,04 |
Узел 6 | 8,3 | 3 | 0,13 | 1,1 | 1,1 | 1,04 |
Таблица 22 –Нормирование сварки узлов металлоконструкции «Поворотный элемент крана» проектного технологического процесса
То | Тнш | L | Кобс | Квио | КI | |
Узел 2 | 5 | 10,1 | 0,78 | 1,1 | 1,04 | 1,04 |
Узел 3 | 1,8 | 5 | 0,4 | 1,1 | 1,04 | 1,04 |
Узел 4 | 17,6 | 25,5 | 3,20 | 1,1 | 1,14 | 1,04 |
Узел 5 | 5,2 | 9,4 | 0,95 | 1,1 | 1,1 | 1,04 |
Узел 6 | 0,5 | 3,3 | 0,13 | 1,1 | 1,1 | 1,04 |
Полное время сварки узлов будет равно Тшт.общ.=90,40 мин (базовый процесс)
|
|
Полное время сварки узлов будет равно Тшт.общ.=70,70 мин (проектный процесс)
Общее время на операции по изготовлению проектируемой металлоконструкции «Поворотный элемент крана» представлены в таблицах 23 и 24.
Таблица 23 – Штучное-калькуляционное базового технологического процесса
Наименование этапа изготовления | Штучное время сборочной операции, мин. | Штучное время сварочной операции, мин. | Штучное-калькуляционное время, мин. |
Узел 1 | 12,7 | 10,8 | 23,5 |
Узел 2 | 12 | 14,2 | 24,2 |
Узел 3 | 11,6 | 9,3 | 20,9 |
Узел 4 | 18,12 | 10,2 | 28,22 |
Узел 5 | 17 | 14,3 | 21,3 |
Узел 6 | 16,8 | 3 | 19,8 |
Таблица 24 – Штучное-калькуляционное проектного технологического процесса
Наименование этапа изготовления | Штучное время сборочной операции, мин. | Штучное время сварочной операции, мин. | Штучное-калькуляционное время, мин. |
Узел 1 | 12,7 | 17,4 | 30,1 |
Узел 2 | 12 | 10,1 | 22,1 |
Узел 3 | 17 | 5 | 22 |
Продолжение таблицы 24
Узел 4 | 18,1 | 25,5 | 46,6 |
Узел 5 | 17 | 9,4 | 26,4 |
Узел 6 | 11,6 | 3,3 | 14,9 |
Глава2. Конструкторский раздел
Проектирование приспособлений для сборки и сварки
Металлоконструкции
Оснастка это–совокупность устройств, механизмов, приспособлений и специального инструмента, необходимых для осуществления запроектированного технологического процесса сборки и сварки узлов. По конструктивному оформлению и характеру использования различают универсальную и специальную сборочно-сварочную оснастку. Универсальная оснастка является переналаживаемой, что позволяет изготовлять однотипные конструкции, отличающиеся друг от друга габаритными размерами и формой. Ее преимущественно применяют в мелкосерийном и среднесерийном производстве и используют для изготовления целой группы однотипных конструкций. К универсальной оснастке относят, например, электромагнитные сварочные стенды с передвижными флюсовыми балками, сектора, сборочные постели с выдвижными стойками, переносные леса.
|
|
Для объемных сварочных работ существует значительное многообразие вспомогательной оснастки. При этом тип сварочной оснастки зависит от конструкции свариваемого узла, характера производства и способа самого термического процесса. Грамотный выбор и разумное конструктивное исполнение сварочной оснастки не только существенно повышает механизацию работ, но и позволяет снизить операционные издержки.
Общие требования к сборочно–сварочной оснастке:
Точное пространственное размещение свариваемых деталей, в том числе для многокомпонентных узлов, исключение ручной подгонки;
Легкий доступ ко всем местам для прихваток, зачисток и основных сварочных швов;
Сборка в соответствии с допусками, заложенными в конструкторской документации (чертежах, технических заданиях).
Соблюдение требуемых межкромочных размеров соединяемых изделий.
Оптимальный порядок сборки, высокая производительность и обеспечение достойного качества накладываемых швов.
Обязательная безопасность использования, в том числе при возникновении внештатных ситуаций–разборка узла, выход из строя фиксирующих приспособлений.
Исходными данными для выбора или разработки сборочно-сварочных приспособлениях являются:
Чертежи деталей и сварной конструкции в целом;
Технологический процесс изготовления металлоконструкции;
Производственная программа назначение и условия эксплуатации приспособлений.
Сначала разрабатывают принципиальную схему приспособления на основе общих принципов базирования и зажима деталей в приспособлении с расчетом прочности или жесткости его элементов, а затем разрабатывают общий вид приспособления с учетом силового привода и точности исполнительных размеров.
Проектирование приспособлений обычно выполняют в следующей последовательности:
По сборочному чертежу изделия определяют базовую деталь и устанавливают базовые поверхности для фиксирования или крепления в приспособлении.
Определяют усилия, действующие на приспособление в процессе его эксплуатации.
Разрабатывают принципиальную схему приспособлений.
Разрабатывают конструкторскую схему или эскизную компоновку приспособления и последующим расчетом или конструктивно определяют размеры его основных деталей.
Окончательно оформляют конструкцию приспособлений в виде сборочных чертежей.
Определяют экономическую эффективность применения эффективности разрабатывают рабочие чертежи приспособления.
При конструировании приспособления необходимо учитывать простоту загрузки деталей и заготовки, жесткость их закрепления, безопасность работы. Основные элементы приспособления следует выбирать из числа типовых элементов, применяемых предприятиях. После разработки приспособления необходимо определить его эффективность и окупаемость производстве.
Размещение собираемых деталей в приспособлении по правилам базирования. Положение любого твердого тела в пространстве определяется шестью степенями свободы-перемещение вдоль трех взаимно перпендикулярных осей (OX, OY, OZ) и вращением вокруг них. Чтобы твердое тело закрепить неподвижно, необходимо лишить его всех этих степеней свободы. В общем случае это достигается прижатием тела к шести опорным точкам, расположенным в трех взаимно перпендикулярных плоскостях XOY, YOX, XOZ.
Рисунок 10. Схема базирования для узла 1
При разработке сборочно – сварочных приспособлений рекомендуется устанавливать точность не менее 60% от точности размеров металлоконструкции, так как на металлоконструкции предельные отклонения составят Н14, h14, IT14\2, то точность базовых элементов приспособления для сборки составит Н12, h12, IT12\2
Для сварки узла 4применяю сборочно–сварочное приспособление «Сектор», которое является шаблоном и значительно облегает сварку этого узла.
Контрольное приспособление состоит из установочных, зажимных, измерительных и вспомогательных элементов, смонтированных на корпусе приспособления.
На установочные элементы (опоры) ставят проверяемую деталь своими измерительными базами для проведения контроля. Для установки применяют постоянные опоры со сферическими и плоскими головками, опорные пластины, а также специальные детали (секторы, кольца) в зависимости от конфигурации детали.
Рисунок 11. Сборочно–сварочное приспособление «Сектор»
Дата добавления: 2018-06-27; просмотров: 1706; Мы поможем в написании вашей работы! |
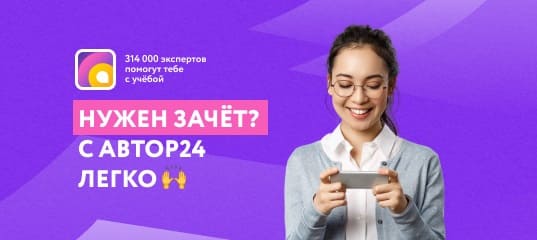
Мы поможем в написании ваших работ!