Станкоёмкость и трудоёмкость механической обработки
Станкоёмкость операции представляет собой затраты штучного или штучно-калькуляционного времени на её выполнение. Станкоёмкость детали (в станко-часах) включает всё нормированное время по всем операциям механической обработки.
Под трудоёмкостью понимают величину затрат живого труда на изготовление единицы продукции в человеко-часах. Связь между трудоёмкостью и станкоёмкостью можно выразить следующим образом:
(3.8)
где: Тчел.ч. — трудоемкость обработки в чел. ч; Тст.ч. - станкоёмкость обработки в ст.ч; Км — коэффициент многостаночности — число станков, обслуживаемых одним рабочим.
Станкоёмкость может быть определена различными способами, выбор которых определяется типом производства. При Проектировании цехов крупносерийного и массового производств, как правило, разрабатываются подробные технологические процессы изготовления деталей с нормированием операций.
В этом случае трудоёмкость обработки детали Т будет равна:
- для массового производства,
- для крупносерийного (серийного) производства,
где и
— штучное и штучно-калькуляционное время обработки детали на i-й операции, мин.
Для цехов мелко- и среднесерийного производств, когда разрабатывается приведённая программа с выделением в группе технологически и конструктивно подобной детали-представителя, нормирование операций обработки производят только для представителя. Станкоёмкость изготовления других деталей группы осуществляют, используя коэффициенты приведения: Тi= Тпр∙ Кoi, где Тi и Тпр — станкоёмкость любого изделия из группы деталей и представителя соответственно, Кoi — общий коэффициент приведения рассматриваемой детали. Методика расчёта коэффициентов приведения рассмотрена ранее в 3.2
|
|
При разработке цеха единичного или мелкосерийного производства, его технического перевооружения и реконструкции станкоемкость находят не по отдельным деталям, а по цеху в целом, используя заводские данные или данные аналогичных производств. В основу расчёта принимают фактическую (достигнутую) станкоемкость — Тф, определяемую по формуле:
(3.9)
где — действующая в цехе станкоемкость годового выпуска в станко-часах; КП — средний по цеху коэффициент выполнения норм, Км — коэффициент многостаночного обслуживания.
Достигнутая (фактическая) станкоемкость для целей проектирования должна быть дополнительно ужесточена с учетом дальнейшего снижения норм за счёт внедрения прогрессивной технологии и оборудования, предусматриваемых в проекте. Тогда Тпр= Tф∙Kу где Тпр — станкоемкость, принимаемая для проекта, ст.ч; Ку — коэффициент ужесточения норм.
|
|
Коэффициент ужесточения корм определяют, разрабатывая технологические процессы на отдельные детали и нормируя операции обработки. Полученные данные сопоставляют с заводскими (базовыми) нормами на аналогичные детали, т.е.
, (3.10)
где числитель — норма времени на обработку детали по проекту; знаменатель — по базе.
С учётом возможных изменений объёмов производства по проекту и базе проектная станкоемкость определяется из выражения Тпр = Тф ∙КY ∙КD, где КD — коэффициент изменения объёмов выпуска: КD =Nпр /Nб — отношение проектного и базового объёмов выпуска деталей, шт/год.
На этапе технико-экономического обоснования проекта (ТЭО) или технико-экономических расчетов годовая станкоемкость цеха может быть найдена по показателям удельной станкоемкости механической обработки единицы массы изделии или комплекса деталей изделия.
В первом случае Тпр=Туд.g ∙ G ∙N , где Туд.g — удельные затраты времени на изготовление 1 т изделия; G — масса изделия в тоннах; N — годовой выпуск изделий, шт.
Во втором случае Тпр=Туд.∙N, где Туд — время обработки одного комплекта деталей изделия. Данные по удельным показателям установлены отраслевыми проектными организациями на основе анализа опыта работы предприятий.
|
|
В таблице 3.8 приведены значения удельной трудоемкости обработки 1т массы изделий и 1т массы комплекта обрабатываемых деталей, а также выпуск на 1 единицу произведенного оборудования по данным технико-экономических показателей механических цехов тяжелого машиностроения и станкостроения [ ]. (Егоров)
Таблица 3.8.- Примерное число человеко-часов и станко-часов, затрачиваемых на механическую обработку 1 тобщего веса (машин), на 1 т обрабатываемых деталей и на единицу производственного оборудования.
Машины | На 1 тоннуобщего веса | На 1 тонну обрабатываемых деталей | Выпуск на единицу производственного оборудования, ч | ||
чел.-ч | станко-ч. | чел.-ч | станко-ч | ||
Тяжелое машиностроение Редукторы для прокатных: станов цилиндрические, цилиндрическо-конические, червячные, глобоидные (при выпуске 4500 т весом до 30т | 37 | 41 | 87 | ||
Краны мостовые электрические грузоподъемностью: | |||||
5т……………… | 28 | 31 | 98 | ||
15 – 20т………… | 22 | 24 | 135 | ||
30 – 50т………………… | 20 | 22 | 149 | ||
Двигателя внутреннего сгорания: тихоходные дизели мощностью 600 л.с. ………… | 46 | 50.4 | 78 | ||
быстроходные » » 450 л.с. ………… | 214 | 235 | 17 | ||
Специальные крепежные детали (винты, болты, гайки, шпильки, штифты) и нормализованные детали (втулки, кольца, стаканы, фланцы и т.п.)…… | 273 | 300 | 11 | ||
Станкостроение Токарно -винторез вые, взльце-токарные, специальные и агрегатные станки (средний вес станка 8,7 т) ………… | 131 | 73.5 | - | - | 43.6 |
Резьбошлифовальные, червячно-шлифоваль ные, зубошлифовальные станки высокой точности (средний, вес станка 5,1 т)…………… | 264 | 208 | - | - | 18 |
Горизонтально- и координатно-расточные станки, включая станки высокой точности (средний вес станка 32т)………… | 177 | 74 | - | - | 48 |
Токарно-револьверные станки (средний вес станка 4,3 т) ………………………………... | 25.5 | 65 | - | - | 51 |
|
|
Дата добавления: 2018-06-01; просмотров: 669; Мы поможем в написании вашей работы! |
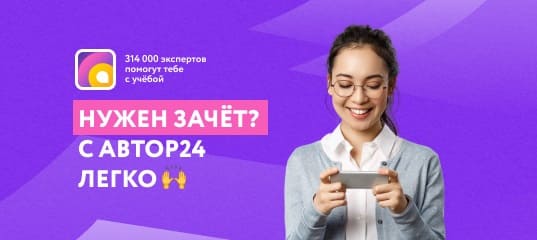
Мы поможем в написании ваших работ!