Лекция №39: «Технология сборки МПП на примере компании
ФОРМОЗА-АЛЬТАИР»
Лекция сопровождается презентацией.
Рассмотрим последовательность технологических операций монтажа многослойных печатных плат на промышленном оборудовании. В основном материал лекции носит иллюстративный характер и даёт общее представление о процессах автоматизированного монтажа планарных чипов и дискретных компонентов на многослойные печатные платы, контроле и устранении брака в условиях предприятия «Формоза-Альтаир».
Так как при транспортировке с завода изготовителя МПП могут подвергаться воздействию влаги и изменению температур, необходимо перед монтажом электронных компонентов их просушить. Сушка проводится в специальном термостате (рис. 39.1). Если сушку не провести, то в процессе пайки компонентов с планарными выводами (SMD) печатная плата может деформироваться, а это может привести к её полной негодности.
Рис. 39.1. Сушильный шкаф
Рис. 39.2 Просушенные печатные платы (PCB) на специальной подставке.
На печатные платы устанавливают два типа компонентов – SMD и DIP.
Первый тип (SMD) – это компоненты поверхностного монтажа (резисторы, конденсаторы, небольшие индуктивности, микросхемы).
Второй тип (DIP) – элементы, у которых выводы проходят в отверстия в печатной плате (оксидные конденсаторы, разъемы, слоты).
Весь технологический процесс разбивается на два этапа: расстановка и пайка SMD компонентов и расстановка и пайка DIP компонентов.
|
|
Перед тем как начать размещение SMD компонентов, на требуемые контактные площадки печатной платы необходимо нанести паяльную пасту. Она представляет собой измельченные в мелкодисперсный порошок смесь флюса (канифоли) и припоя, которые замешаны в несущем веществе (например, скипидаре или другом высокомолекулярном растворителе). Паста
Рис. 39.3. Трафарет наносится через специальный трафарет.
Трафарет представляет собой металлическую пластину с отверстиями, где располагаются контактные площадки (см. рис. 39.3.).
Нанесение пасты производится с помощью специальной установки (см. рис. 39.4.). Под трафарет подается и точно позиционируется печатная плата. Трафарет прижимается к ней, а ракели (резиновые ножи) (см. рис. 39.4) на подвижной подвеске с манометрами для контроля давления пасты проходят по трафарету, размазывая паяльную пасту.
Рис.39.4. Установка для нанесения паяльной пасты продавливанием с помощью ракеля.
Нанесение пасты производится с помощью специальной установки (см. рис. 39.4.). Под трафарет подается и точно позиционируется печатная плата. Трафарет прижимается к ней, а ракели (резиновые ножи) (рис. 39.4) на подвижной подвеске с манометрами для контроля давления пасты проходят по трафарету, размазывая паяльную пасту.
|
|
Паяльная паста, попав в отверстия в трафарете, остается на контактных площадках печатной платы. Теперь МПП готова для подачи на конвейер. Вначале она попадает в приемник печатных плат (рис. 39.5.), из него печатные платы поступают в робот-маунтер (mounter) от Yamaha (см. рис. 39.6., 39.7. и 39.8.).
Рис. 10.4.5. Печатные платы в приемном устройстве роботизированного станка.
Робот представляет собой станок с манипулятором, который принимает из кассет компоненты (резисторы, чипсеты, контроллеры) и, в соответствии с координатами, получаемыми от компьютера, помещает каждую деталь в нужное место. Для контроля позиционирования компонентов установка имеет «электронный глаз», который определяет правильность их ориентации.
Рис.39.6.Общий вид SMT При этом, если деталь захвачена криво, то
(surface mounting technology) цеха. манипулятор ее выравнивает в пространстве.
Станок работает по программе, заложенной в его компьютер. Упрощенно структуру этого станка можно представить как состоящую из компьютера, подвижной пневмоголовки (1) (см. рис. 39.7.), конвейера, по которому движутся печатные платы (2), и специальных податчиков компонентов (3). Подача компонентов ведется с двух сторон станка.
|
|
Рис.39.7. Роботизированный станок для расстановки SMD компонентов.
Для удобства подачи SMD компоненты упакованы в ленту и намотаны на бобину (рис.39.8.). Эта бобина закрепляется на специальный податчик (рис.39.9.)
Рис. 39.8. Бобина с намотанной на нее лентой с SMD компонентами.
![]() |
Податчик осуществляет съем удерживающей полиэтиленовой ленты и подачу открытых SMD компонентов к приемной площадке, где автоматическая пневмоголовка (1) см. рис. 39.7
Рис.39.9. Податчик компонентов. захватит SMD компонент и перенесет его
на нужную позицию
Манипулятор робота (1) (см. рис. 39.7.) захватывает компоненты, присасывая их воздухом. Причем размер присоски может изменяться на ходу. Одновременно на одном станке может комплектоваться только один вид платы. Зато можно использовать два и более станков одновременно, при этом каждый устанавливает определенную группу компонентов, что ускоряет работу.
![]() |
Однако не все SMD элементы удобно упаковывать в ленту и наматывать на бобину. Некоторые микросхемы поставляются не на бобине, а на панелях. Для расстановки таких компонентов применяется немного другие автоматические станки (рис. 39.10.).
|
|
Рис. 39.10. Автоматический расстановщик компонентов с панелей.
Кроме панелей применяются пластиковые рейки (4) (рис. 39.7.), внутри которых помещаются микросхемы. Подача таких компонентов осуществляется путем наклона рейки, по которой микросхемы съезжают вниз, откуда они захватываются и перемещаются к месту установки на плате пневмоголовкой.
После того, как все необходимые компоненты будут установлены, печатная плата по конвейеру переместится в печь (в печи пять камер, в каждой - своя температура), где по специальному температурному графику МПП будет нагрета, а затем охлаждена (рис. 39.11.). В процессе нагрева паяльная паста расплавляется, и припой соединяет расставленные SMD компоненты с контактными площадками платы.
При установке компонентов возможны погрешности позиционирования, в результате чего SMD компонент может оказаться немного смещенным относительно контактных площадок. Это смещение допустимо, если оно не превышает размеров контактной площадки. При переходе паяльной пасты в расплавленное состояние, за счёт сил поверхностного натяжения SMD компонент сместится по контактным площадкам и автоматически центрируется.
Рис. 39.11. Печь для пайки SMD элементов.
![]() |
Выезжая из печи, платы упаковываются в специальные стойки (см. рис. 39.12.). После этого начинается первая стадия контроля.
Рис. 39.12. Приемник печатных плат.
На первой стадии испытаний используется аппарат JetBoard (рис. 39.13.). Этот стенд управляется компьютером. Плата с распаянными поверхностными компонентами (SMD) устанавливается в специальное гнездо, а сверху опускается пластина с расположенными на ней иголками.
Рис. 39.13. Аппарат JetBoard для обнаружения «непропаек».
Иголки замыкают необходимые цепи, а компьютер прогоняет тест и ищет короткие замыкания и отсутствия контакта, а также позволяет определить отклонения в параметрах установленных компонентов. Расположение и количество контактных игл можно менять, используя специальную программу, так что проверять можно любую плату. Кроме того, постоянно производится визуальный контроль качества пайки.
Далее, после того как в приемнике накопится достаточное количество печатных плат, их перевозят в другое помещение, где устанавливаются и напаиваются DIP компоненты.
Установка DIP компонентов производится вручную (рис. 39.14.). Печатные платы непрерывно подаются по конвейеру, и по ходу на них устанавливаются компоненты. Каждый оператор за конвейером устанавливает ограниченный набор компонентов, при этом каждый следующий работник проверяет правильность и комплектность работы предыдущего. Самая ответственная работа у последнего оператора первой части конвейера.
Рис.39.14. Установка DIP компонетов
![]() |
На этом рабочем месте проверяется комплектность и правильность установки всех компонентов.
Рис. 39.5. Рабочее место оператора по установке DIP компонентов.
Затем, платы попадают в блок пайки волной (рис.39.16.). В этом блоке расположена емкость с расплавленными 400 кг припоя, над которым проезжают платы. Предварительно плата проходит через жидкий флюс (рис. 39.17), а затем касается гребня волны припоя, с помощью которого осуществляется пайка выводов DIP компонентов и перемычек.
Рис. 10.4.16. Установка для пайки волной.
![]() |
Рис. 39.17. Емкость с расплавленным припоем для пайки волной.
Затем печатные платы подаются в моечносушильный аппарат (рис.39.18.), где платы проходят через разные типы растворителей и воды при разной температуре. Смываются излишки флюса, и грязь. Потом происходит сушка. На этом этапе сборка печатной платы завершена.
Рис. 10.4.18. Моечносушильный аппарат.
Затем платы вновь попадают на конвейер, где происходит окончательная комплектация. Устанавливаются микросхемы BIOS, клеятся наклейки и, вновь происходит визуальный контроль качества. Рабочее место оператора показано на рис. 39.19. На этом этапе отсеиваются печатные платы, в которых отсутствуют необходимые DIP компоненты (разъемы, слоты).
Рис. 39.19. Контроль качества после моечносушильного аппарата.
Когда плата готова, начинается процесс её тестирования. В каждую МПП устанавливаются необходимые компоненты - процессор, память, видеокарта, подключаются жесткие диски, дисковод и запускаются тестовые программы. Плюс ко всему, есть специальный эксперт, который производит более сложную выборочную проверку. Каждая плата имеет уникальный номер и наклейку, на которой отражена информация о том, кто ее проверял.
Отсюда, платы поступают в цех упаковки, где они комплектуются шлейфами, заглушками, руководствами и компакт дисками с драйверами. А затем поступают в магазины или на сборку компьютеров.
Если изготовленная плата не прошла тестирование, ее отправляют на доработку. Если при первом включении устройство не заработало – вполне возможно чипсет или разъем процессора не пропаялся. В таком случае чипсет и/или разъем процессора отпаиваются.
Причины брака на SMT конвейере:
· Человеческий фактор:
o путают податчики SMD компонентов с бобин;
o неправильно задают температурный профайл, из-за чего происходит или непропайка, или могут быть испорчены пластмассовые корпуса (например, socket – разъем центрального процессора).
· Брак от других факторов:
o паяльная паста плохого качества, из-за чего возможна непропайка компонентов, образование оловянных шариков по всей поверхности печатной платы;
o компонент, установленный роботом-маунтером Yamaha может не прилипнуть к паяльной пасте и слететь;
o при перемещении, устанавливаемого компонента с помощью пневмоприсоски, между ней и компонентом может попасть пыль, вследствие чего пневмоприсоска может «уронить» компонент;
o возможны погрешности установки компонентов на печатную плату. Если сдвиг компонента относительно контактной площадки не больше размеров самой контактной площадки, то при пайке в печи под действием сил поверхностного натяжения компонент «встанет» на свое место. В противном случае – нет. Повысить точность установки можно, снизив скорость работы робота, но при этом снизится производительность установки.
Возможные браки на DIP конвейере:
· Человеческий фактор
o неправильная установка DIP компонентов;
o неустановка (пропуск) необходимых компонентов;
· Брак от других факторов:
o при пайке волной DIP компонент может вылететь (или сместиться) из отверстий,
o куда он был установлен;
o SMD компоненты, припаянные к обратной стороне печатной платы, могут отпаяться
o при проходе через «волну», если они плохо закрыты специальной пастой.
Для снижения брака могут быть приняты следующие меры:
· после пайки SMD компонентов печатные платы проходят тест на стенде JetBoard;
· вводится проверка наличия необходимых SMD компонентов вручную по шаблону;
· осуществляются проверки на этапе ручной установки DIP компонентов;
· ведется проверка после припайки DIP компонентов;
· проводится проверка собранных устройств с помощью тестов и испытаний на вибростенде.
Дата добавления: 2018-05-30; просмотров: 613; Мы поможем в написании вашей работы! |
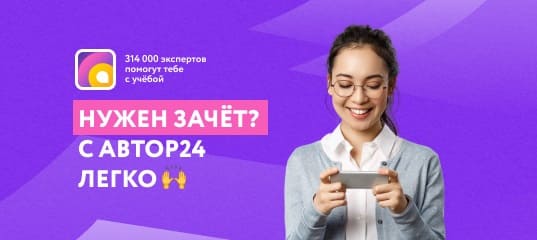
Мы поможем в написании ваших работ!