А) Расчет суммарного сечения питателей
,
где – суммарное сечение питателей, см2;
Q – масса жидкого металла, протекающая через литниковую систему, кг;
Q=G+Q1 ,
где Q1 – расход металла на литниковую систему, зависит от массы отливки [2, с.52];
G=4*Mотл;
G=4*9,3=37,2 кг
Тогда по диаграмме зависимости расхода металла от
массы отливки.
=18% (рис.32; [2, с.52]);
Следовательно: Q=G+Q1=37,2+6,7=43,9 кг
Сечение питателя
b |
a |

h=12 мм, a=12 мм, b=9 мм
Б) Определяем площадь шлакоуловителя и стояка
Для среднего и мелкого литья
; [2, с.53]
Следовательно:
(см2)
a |
b |

Размеры сечения определяем таблице 24[2, с.53]
h a
h=27 мм, a=26 мм, b=20 мм
Диаметр стояка в нижней части по формуле
[2, с.53]:
(см2)
см= 27,9 мм
Dв>Dн на 10…15%
Dв=30,7 мм
|
|
В) Определение размеров литниковой чаши или литниковой воронки
В зависимости от диаметра стояка выбираем по таблице 25, 27 будет в нашем случае литниковая чаша или воронка
[2, с.57]. По таблице 27 выбираю литниковую чашу по диаметру стояка D=32 мм.
Рис.7 Литниковая чаша
Размеры литниковой чаши представлены в таблице 7.
Таблица 7
L,мм | M,мм | h,мм | R1,мм | R2,мм | R3,мм | R4,мм | R,мм | r1,мм | диаметр стояка, мм |
120 | 40 | 70 | 25 | 20 | 35 | 30 | 10 | 5 | 25 |
Проверка высоты стояка
Высота стояка, определенная раннее выбранной высотой верхней опоки (литниковая система располагается по разъему формы), проверяется по формуле:
Hmin= Hст–C=L*tgα
Hст= C+L*tgα
где – минимальный избыточный напор металла, обеспечивающий заполнение формы;
– высота стояка; α – угол падения напора, α = 8…9°;
С – высота отливки над питателем, L – расстояние от центра стояка до наиболее удаленной и высокой точки формы, [2, с.55].
|
|
L1 = 32+230,9/2+9,3/2=152,1 мм;
L2 =16+230,9=246,9 мм;
мм;
Hст=289,9*tg9°=289,9*0,1584=45,9 мм;
Высота стояка обеспечивает минимальный избыточный напор металла для заполнения литейной формы.
Определение состава металлической шихты для выплавки чугуна в вагранке и расчет расхода топлива (кокса) на тонну чугуна.
Определение химического состава чугуна
Определяем химический состав СЧ-40 по таблице 30 [2, с.60]:
Углерод – 2,6%; кремний – 2,7%; марганец – 0,3%; фосфор – 0,02%;
сера – 0,02%, хром – 0,25%.
Определение состава шихты
1) Чушковый легированный чугун – 15%;
2) Чушковый нелегированный чугун – 14%;
3) Стальной лом – 31%;
4) Собственные отходы – 20%;
5) Чугунный лом – 20%.
Расчет массовой доли элементов в шихте для плавки приведем в таблице 8.
Таблица 8
| Массовая доля Ме % | Массовая доля элемента, % | |||||||||
кремний | марганец | хром | сера | фосфор | |||||||
в Ме | в шихте | в Ме | в шихте | в Ме | в шихте | в Ме | в шихте | в Ме | в шихте | ||
Нелегированный Чушковый чугун ЛК2 | 15 | 3,0 | 0,45 | 0,8 | 0,12 | - | - | 0,02 | 0,0025 | 0,05 | 0,0075 |
Легирован ный Чушковый чугун ХЧ-3 | 14 | 2,2 | 0,308 | 0,7 | 0,098 | 2,5 | 0,35 | 0,04 | 0,0046 | 0,10 | 0,014 |
Стальной лом | 31 | 0,2 | 0,062 | 0,5 | 0,155 | - | - | 0,05 | 0,0125 | 0,05 | 0,0155 |
Собственные отходы | 20 | 2,7 | 0,54 | 0,3 | 0,06 | 0,25 | 0,05 | 0,02 | 0,0025 | 0,02 | 0,004 |
Чугунный лом | 20 | 2,0 | 0,4 | 0,8 | 0,16 | - | - | 0,10 | 0,02 | 0,20 | 0,04 |
ИТОГО | 100 | - | 1,76 | - | 0,593 | - | 0,40 | - | 0,0431 | - | 0,081 |
|
|
Проверяем состав шихты: считая угар кремния 10%, марганца 50%, хрома 30% пригар серы 100% (по табл. 34 [2,с. 64]) находим по заданному составу чугуна массовую долю элементов в шихте по формуле:
, где а – необходимое количество элемента. Входящего состав металла после плавки в вагранке, %
х – пригар (+) и угар (-) элемента при плавке, %
Кремний (2,7/(100-10))*100% = 3,0%
Марганец (0,3/(100-50))*100% = 0,6%
Сера (0,02/(100+100))*100% = 0,04%
Хром (0,25/(100-30))*100% = 0,4%
Фосфор 0,02% . Согласно табл. 34 [2, с.64] изменение массовой доли элементов при плавке в вагранке не происходит у фосфора.
Сопоставляя полученный состав шихты с необходимым, видим недостаток кремния 3,0 – 1,76 = 1,24%
Для увеличения массовой доли кремния заменяем чугун ЛК2 чугуном ЛК1 (добавляем ферросилиций СИ10 с 15% кремния) , его необходимо добавить:
|
|
(1,24/15)*100% = 8,3%
Добавка ЗЧ2 дается сверх 100% и металлическая калоша массой 600 кг определяется окончательно:
Таблица 9
Шихта | Массовая доля металла в шихте,% | Масса металла в шихте, кг |
Нелегированный чушковый чугун ЛК2 | 15 | 90 |
Легированный чушковый чугун ХЧ3 | 14 | 84 |
Стальной лом | 31 | 186 |
Собственные отходы | 20 | 120 |
Чугунный лом | 20 | 120 |
Ферросилиций СВ10 | 8,3 | 49,8 |
ВСЕГО | 108,3 | 649,8 |
Плавление шихты
Плавление шихты осуществляется в специальных печах вагранках. Процесс плавки чугуна: в вагранку загружают дрова, разжигают их, затем засыпают слой кокса на 700-800 мм выше уровня фурм и включают дутьё. После разогрева нижней части вагранки в неё загружают шихту. За счет тепла от сгорания кокса происходит расплавление металлической части шихты. Процесс плавки происходит непрерывно, а загрузка шихты и выпуск жидкого чугуна производится периодически.
Расчет кокса для получения 1000 кг отливок
Qж.м. – масса жидкого металла
Qж.м. = Qотл+Qлит.с.
Qотл=1000 кг – масса отливок
Qлит.с. – масса литниковой системы из п. 5.3.1.
Xк – расход топлива (кокса) в процентах, определяем по таблице 35 [2, с. 65].
Xк = 18%
Qж.м. = 1000+180 = 1180 кг
Список использованных источников:
1. МУ-57-02. Методические указания для выполнения контрольных и лабораторных работ по курсам «Технологические процессы в машиностроение» и «Проектирование производства заготовок» для студентов заочного факультета Сост.: А.К. Денисюк, В.А. Иванова, О.М Епархин; ЯГТУ. – Ярославль, 2002 – 40 с. [№2455]
2. Потанин С.Л. Технология изготовления чугунных отливок в песчаные формы: Учеб. пособие к РГР / Яросл. политех. ин-т. – Ярославль, 1992, - 80 с. [№1561]
3. Дальский А.М. Технология конструкционных материалов. Учебник для вузов. М., «Машиностроение», 1977- 664с.
Дата добавления: 2018-05-13; просмотров: 556; Мы поможем в написании вашей работы! |
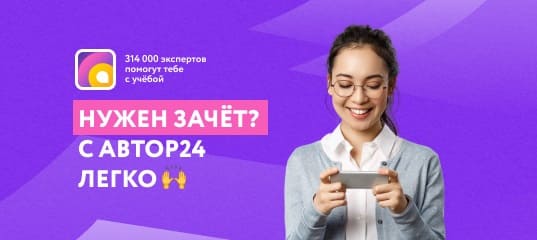
Мы поможем в написании ваших работ!