Изготовление модели отливки, литниковой системы, стержневых ящиков и выбор опок
Модели служат для образования внешних контуров отливки в форме. В массовом производстве применяют металлические модели. Модель изготавливается с учетом припусков на механическую обработку и линейную усадку металла. Кроме основных моделей, образующих форму отливки, имеются модели литниковых систем, с помощью которых при формовке образуется система каналов, через которые жидкий металл поступает в полость формы.
Стержневые ящики для изготовления стержней должны обеспечивать равномерное уплотнение смеси и быстрое извлечение стержня. Как и модели, стержневые ящики имеют литейные уклоны, при назначении их размеров учитывают величину усадки сплава и, если требуется, также и припуска на механическую обработку. Стержневые ящики делают из тех же материалов, что и модели. По конструкции стержневые ящики могут быть неразъемными и разъемными.
Опоки служат для удержания формовочной смеси и образования литейной песчаной формы. Центрирование верхней опоки с нижней осуществляется фиксирующими штырями, которые вставляются в отверстия в приливах опок, а скрепление опок осуществляется скобами.
Приготовление формовочных и стержневых смесей
Формовочные смеси применяют для изготовления песчаных форм.
Технологический процесс приготовления формовочных смесей заключается в перемешивании составляющих компонентов смеси с последующим ее выстаиванием и разрыхлением. Перемешивание производят в смешивающих бегунах. Время перемешивания составляет для единой смеси 3-5 мин. Затем смеси загружают в бункера, где они выстаиваются в течение нескольких часов для равномерного распределения влаги. Перед загрузкой смесь разрыхляют.
|
|
При заливке формы стержни в большинстве случаев находятся в тяжелых условиях, испытывая значительное термическое и механическое воздействие расплавленного литейного сплава. Поэтому к стержневым смесям предъявляют более высокие требования по прочности и другим свойствам, чем к формовочным смесям.
Изготовление полуформ и стержней, сборка форм
Основным способом изготовления стержней является их машинная формовка в стержневых ящиках. Осуществляем формовку в 2-х опоках по разъемной модели.
Операция сборки форм начинают с установки нижней полуформы на заливочную площадку. Затем полость полуформы продувают сжатым воздухом, устанавливают в нее нижнюю полуформу и осторожно по фиксирующим штырям накрывают верхней. Для предотвращения подъема верхней полуформы статическим давлением металла ее скрепляют с нижней полуформой скобами или ставят грузы.
Приготовление шихты
|
|
- Определение химического состава чугуна.
- Определение состава шихты.
Плавление шихты
Плавление шихты осуществляется в специальных печах вагранках. Процесс плавки чугуна: в вагранку загружают дрова, разжигают их, затем засыпают слой кокса на 700-800 мм выше уровня фурм и включают дутьё. После разогрева нижней части вагранки в неё загружают шихту. За счет тепла от сгорания кокса происходит расплавление металлической части шихты. Процесс плавки происходит непрерывно, а загрузка шихты и выпуск жидкого чугуна производится периодически.
Заливка формы
Температура заливки для серого чугуна колеблется в пределах 1250..1400˚С. Чем более тонкостенные отливки, тем должна быть выше температура заливаемого чугуна.
Формы заливают на плацу, рольгангах и конвейерах. На плацу обычно заливают мелкие и средние формы в небольших литейных цехах. В литейных цехах, производящих большое количество отливок, формы обычно заливают на конвейере. Заливка металла в литейную форму может осуществляться либо ручным способом, либо механическим. Емкость ручных ковшей не превышает обычно 50 кг, а емкость механизированных крановых ковшей составляет 50 – 200 т и более. Для заливки чугуна большое применение получили ковши барабанного типа емкостью до 5 т.
|
|
Выбивка отливок
Время охлаждения отливок в форме зависит от теплофизических свойств формовочной смеси, толщины стенок отливки, от теплосодержания металла и его склонности к образованию трещин. Длительное охлаждение отливок в форме невыгодно, т.к. удлиняет технологический цикл. Поэтому непроизводительное время стараются сократить за счет применения принудительного охлаждения.
Из практики работы литейных цехов известно, что чугунные и стальные отливки можно выбивать из форм при следующих температурах: крупные 300..400˚С, средние 400..500˚С, мелкие 500..600˚С.
Преждевременная выбивка ввиду недостаточной прочности отливок в это время может привести к деформации или разрушению их под действием внешних нагрузок.
После охлаждения отливок до необходимой температуры формы выбивают. Обычно это делается на выбивных решетках – вибровстряхивающих установках. При этом формовочная смесь из опок просыпается сквозь отверстия решетки и передается на переработку.
Обрубка отливок
Обрубка необходима для удаления литниковой системы. Эта операция в зависимости от свойств сплава производится разными способами. Литники от чугунных отливок отбиваются ударом молотка или кувалды, а также в специализированных барабанах.
|
|
Термическая обработка
Термическая обработка предназначена для снятия внутренних напряжений, улучшения структуры и свойств отливок. Применяются следующие виды термической обработки отливок: отжиг, нормализация, закалка и отпуск.
Очистка от окалины
Отливки очищаются от окалины следующими способами: галтовкой, пескоструйной, дробеметной обработкой. Дробеметная очистка является наиболее прогрессивным способом. Она дает возможность получить чистые отливки, и не создает шума при работе.
Контроль
Дефекты отливок выявляются различными методами контроля. Проверяется соответствие размеров отливок размерам чертежа. Отливки периодически разрезают для определения размеров внутренних полостей, разностенности, смещений. Контроль размеров отливок позволяет своевременно предупредить массовый брак из-за износа или коробления модели и стержневых ящиков.
Механические свойства отливок контролируют испытаниями отдельно изготовленных или прилитых образцов, а также (в отдельных случаях) образцов, вырезаемых из тела отливки. Внутренние дефекты отливок выявляются методами радиографической и ультразвуковой дефектоскопии. Для выявления наружных поверхностных дефектов применяется люминесцентный контроль, магнитная и цветная дефектоскопия.
Дата добавления: 2018-05-13; просмотров: 589; Мы поможем в написании вашей работы! |
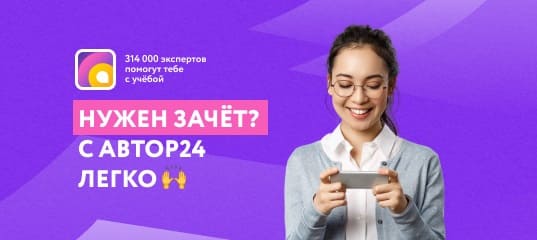
Мы поможем в написании ваших работ!