Анализ и расчёт производительности машин в условиях эксплуатации
Оглавление: Автоматизация производственных процессов в машиностроении. 3 Основы автоматизации производства. Производительность станков, автоматов, автоматических линий 3 Основы автоматизации производства. Производительность станков, автоматов, автоматических линий 4 Виды внецикловых потерь. 6 Анализ и расчёт производительности машин в условиях эксплуатации. 7 Особенности технологического процесса автоматизированного производства. 8 Виды многопозиционных автоматов. 8 Автоматы и линии последовательного действия. 11 Автоматы и линии параллельного действия. 12 Автоматы и линии последовательно-параллельного действия. 12 Задачи, решаемые при проектировании сборочных систем.. 13 Способы автоматической сборки деталей. 13 Состав и компоновка в сборочных цехах. 15 Линейная компоновка со спутниковым конвейером.. 17 Линейная компоновка с шаговым конвейером.. 17 Круговая компоновка РТК с поворотным столом.. 19 Компоновки РТК в виде сборочного центра. 19 Промышленные роботы и оборудование, рекомендуемое. 20 для сборки изделий. 20 Требования к сборочным промышленным роботам.. 21 Робот SIGMA.. 21 Робот типа PUMA.. 21 Робот типа SCILAM... 21 Достоинства робота SCILAM... 22 Автоматизация измерений. 22 Структурная схема измерительного устройства. 23 Типы датчиков. 23 Датчики измерения усилия. 25 Пример расчета силового кольца тензодатчика. 26 Список использованной литературы: 29
|
|
Автоматизация производственных процессов в машиностроении
Развитие автоматизации машиностроения принято делить на уровни и ступени:
1 уровень: Автоматизация цикла обработки (станки с ЧПУ). Производительность возрастает в 2-4 раза.
2 уровень: Автоматизация загрузки и выгрузки (многостаночное обслуживание, оборудование РТК (робототехнические комплексы)).
3 уровень: Контрольная автоматизация (контроль инструмента, обрабатываемых деталей, оборудования, технологических процессов).
4 уровень: Автоматическая переналадка оборудования. Необходимо переналаживать загрузочные устройства, приспособления, инструмент, оснастка, контрольные системы.
5 уровень: Гибкие автоматизированные производства. Сокращение обслуживающего персонала в 3-10 раз. Увеличение выпуска продукции, сокращение количества требуемого оборудования, сокращение сроков и стоимости подготовки производства.
Основы автоматизации производства. Производительность станков, автоматов, автоматических линий
Основной задачей автоматизации является рост производительности машин, количества и качества выпускаемых изделий.
Производительность станка определяет его способность обеспечить обработку определённого количества деталей в единицу времени.
|
|
Существует несколько видов производительностей:
§ производительность резания, которая характеризуется объёмом материала, удалённого с обработанного изделия в единицу времени.
§ производительность формообразования, характеризуется площадью поверхности обработанной на станке в единицу времени.
Оба критерия удобны для сравнения разных способов обработки, но не определяют производительность станка, так как не учитывают вспомогательных операций выполняемых на станке.
Для выполнения любой работы требуются затраты времени:
где tp – время рабочих ходов;
tx – время холостых ходов.
Если за период рабочего цикла Т, машина выполняет одно изделие, то её цикловая производительность при условии бесперебойной работы будет определяться как:
при ,
- технологическая производительность;
Þ
где h - коэффициент производительности; он характеризует степень непрерывности протекания технологического процесса.
![]() |

- автоматизация процесса.
Для автоматизации производства требуется усовершенствовать технологию и автоматизировать технологический процесс. Если
и
, то предел повышения производительности отсутствует.
|
|
Помимо цикловых потерь времени при работе машины имеют место и нецикловые потери времени, которые тоже приводят к снижению производительности, и фактическая производительность машины будет ниже цикловой. К нецикловым потерям времени относят простои, в результате которых продукция не выпускается.
Пусть в течение времени Q выпускается z штук продукции, тогда
[шт/мин],
где Q – производительность.
Общее время складывается из работы и простоя:
Количество выпускаемой продукции:
,
где hисп - коэффициент использования.
,
Суммарные простои отнесем к единице выпускаемой продукции и преобразуем коэффициент использования:
,
- внецикловые потери, приходящиеся на единицу продукции;
,
Внецикловые потери подобно холостым ходам оказывают существенное влияние на производительность, однако, природа их возникновения иная, т.е. холостые ходы строго ориентированы и повторяются каждый цикл, а внецикловые потери являются случайными.
![]() |
Виды внецикловых потерь
Если за произвольный период времени Q выпускается z изделий и суммарные нецикловые простои составляют ∑θп , то внецикловые потери отнесенные к единице продукции:
|
|
С точки зрения теории производительности любой момент времени в течении которого не происходит процесс обработки, контроля, сборки и других операций считается потерянным, т.к. приводит к снижению фактической производительности .
Все потери условно подразделяются на виды:
1) По холостым ходам: подача материала, транспортировка, фиксация, зажим и разжим заготовки, подвод и отвод рабочих органов, т.е. несовмещенные холостые ходы автоматического цикла работы;
2) По инструменту;
3) По оборудованию: поломка, регулирование, ожидание запчастей;
4) По организационным причинам: заправка материала, уборка отходов, сдача готовых деталей, сдача смены, отсутствие рабочего);
5) По браку: брак изделий при наладке, брак после первых операций;
6) По переналадке:
§ потери, вызванные причинами прямого или косвенно связанными с конструкцией и режимом работы машины;
§ потери, вызванные внешними организационно-техническими причинами.
где θп – собственные потери( по оборудованию);
θот – организационно-технологические потери;
ηтех – коэффициент технического использования: его значение показывает, какую долю времени работает машина, при условии обеспечения всем необходим.
ηз – коэффициент загрузки: он характеризует, прежде всего, долговечность механизмов и инструментов.
Анализ и расчёт производительности машин в условиях эксплуатации
Исследования производительности машин в условиях эксплуатации ставят 2 цели:
1) Определить резервы повышения производительности в данных конкретных условиях производства;
2) Дать исходные параметры для проектирования новых машин данного типа.
Если анализировать резервы повышения производительности, то необходимо учитывать все виды потерь: собственные и организационно-технические.
Если анализируются и сравниваются конструктивные, структурные и другие варианты машин, которые отличаются длительностью рабочих и холостых ходов, интенсивностью режимов обработки, надёжностью; то следует учитывать только цикловые и собственные внешние потери.
Так как основные причины потери производительности являются случайными, то достоверность значений можно достигнуть путём длительных наблюдений и замеров с соответствующей их математической обработкой. Во время наблюдения фиксируют все затраты фонда времени: производительные (работа) и непроизводительные (простои) технического и организационного характера, продолжительность неполадок, количество изделий выпущенных в каждую смену, продолжительность циклов и т.д. Наблюдения производятся непрерывно в течение 12-18 смен.
После этого все простои группируют по функциональным признакам, и рассчитывают характеристики работоспособности (коэффициент использования, загрузки, сумма потерь, ,
,
,
,
, С,
Потери производительности:
Суммарную величину потери распределяют между простоями 6 видов, пропорционально их удельному весу, а складывая все эти значения в одном масштабе получаем баланс производительности линии. Часть производительности уходит на потери.
![]() |
Потери I вида – по холостым ходам.
Дата добавления: 2018-05-12; просмотров: 439; Мы поможем в написании вашей работы! |
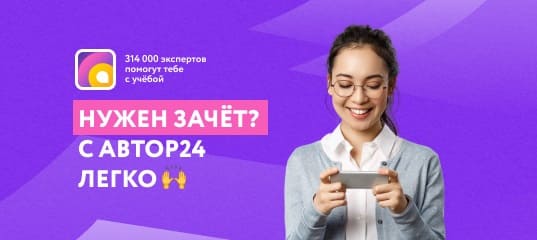
Мы поможем в написании ваших работ!