Разработка технологического маршрута обработки, оформление.
Составление технологического маршрута — это решение сложной многовариантной задачи, в результате которой принимают общий план обработки изделия, намечают содержание технологических операций, определяют состав технологическогооснащения.
При этом надо учитывать, что различные детали машин образуются сочетанием разнообразных поверхностей. Наиболее распространены цилиндрические и плоские поверхности. Многие детали машин имеют винтовые и зубчатые поверхности. Для облегчения их изготовления и эксплуатации они стандартизованы. Редко используют специальные фасонные поверхности (фасонные кулачки, копиры и т. п.).
По ГОСТ 21495—76 все поверхности деталей изделий машиностроения можно разделить на четыре вида:
1) исполнительные поверхности – поверхности, с помощью которых деталь выполняет своё служебное назначение;
2) основные конструкторские базы — поверхности, с помощью которых определяют положение данной детали в изделии;
3) вспомогательные конструкторские базы — поверхности, с помощью которых определяют положение присоединяемых деталей относительно данной;
4) свободные поверхности — поверхности, не соприкасающиеся с поверхностями других деталей.
Поверхности первых трех видов можно объединить в одну основную группу.
Обеспечение заданной точности и качества поверхностей
основной группы с наименьшими затратами труда и издержками
производства является главнейшей задачей технологического
процесса.
|
|
Заданные точность и качество основной группы поверхностей, размеры, масса и форма детали дают возможность определить необходимые методы окончательной обработки этих поверхностей, что предопределяет выбор средств технологического оснащения (СТО).
Каждому методу окончательной обработки предшествуют промежуточные методы и соотвётствующие СТО. При этом исходят из того, что каждый последующий метод должен быть точнее предыдущего.
Одновременно устанавливают методы обработки вспомогательных поверхностей.
Решение задачи по выбору методов обработки всех поверхностей детали сводится к определению содержания технологического процесса, выявлению_необходимости осуществления трех стадий_ обработки: черновой, чистовой и отделочной.
На первой стадии выполняют операции черновой обработки всех поверхностей. На_ этой стадии удаляется основная масса припуска. Обработка сопровождается интенсивным нагревом заготовки и инструмента, большими силами резания, которые требуют соответствующих сил закрепления заготовки и приводят к значительным деформациям технологической системы — источникам образования погрешностей обработки. Удаление большого количества материала позволяет выявить дефекты заготовок (например, раковины в отливках и др.), которые могут быть своевременно устранены или станут основанием для прекращения дальнейшей обработки вследствие непригодности заготовки. После черновой обработки возникают деформации заготовки в результате перераспределения остаточных напряжений_в ее материале, которое наиболее интенсивно происходит при снятии с заготовки наружных_слоев материала.
|
|
Для выполнения черновых операций выбирают наиболее_мощ-
ное и менее точное оборудование, а также _используют рабочих
более низкой квалификации, чем при выполнении чистовых и
отделочных операций.
На второй стадии осуществляются операции чистовой обработки, в результате которых завершается обработка одних поверхностей или происходит подготовка других поверхностей к последующей, более точной обработке.
Третья стадия — отделочная обработка; на этой стадии обрабатывают поверхности с точностью по 6-7 квалитету и получают параметр шероховатости поверхности Ra 0,32 мкм и менее.
|
|
Отделочные методы обработки предусматривают в конце технологического процесса, так как черновые операции выделяют в самостоятельную первую стадию, а также из опасения повреждения окончательно обработанных поверхностей во время многократных установок заготовок на оборудовании и при транспортировании.
Следует отметить, что разделение технологического процесса на указанные три стадии обработки не во всех случаях целесообразно. Например, при обработке заготовки с повышенной точностью и качеством поверхностей технологический процесс начинается с чистовой и даже с окончательной обработки. Если заготовка жесткая, поверхности небольших размеров могут быть окончательно обработаны в начале технологического процесса.
При обработке заготовок из пруткового материала на револьверных станках и автоматах не отделяют черновую обработку от чистовой. При разработке технологического маршрута необходимо учитыватъ требования к взаимному расположению поверхностей.Если, например, предъявляются высокие требования к соосности поверхностей вращения, следует стремиться к их обработке в одной операции с одной установки.
|
|
В связи с невысокими требованиями к точности и качеству свободных поверхностей их обработка выполняется на стадии чистовых или даже черновых операций и по возможности включается в качестве перехода в операции, где обрабатываются поверхности основной группы.
На ранее обработанных поверхностях производится нарезание зубьев, шлицев, резьбы, фрезеруются лыски, канавки, сверлятся отверстия и др. Обработку этих видов выделяют в самостоятельные операции.
( Методы обработки различных поверхностей рассмотрены 1в разд. 3.)
В начале технологического маршрута, используя черновые (первоначальные) базы, обрабатывают поверхности, которые_будут использованы в качестве технологических баз для дальнейшей обработки.
При формировании содержания операций учитывают возможность объединения тех переходов, которые могут быть выполнены
на одном станке.
В тяжелом машиностроении обрабатывают крупногабаритные и тяжелые заготовки, что вызывает необходимость сокращения числа их перестановок со станка на станок. Это характерно также для мелкосерийного производства.
При разработке технологического маршрута важно определить, когда будет выполняться термическая обработка. Технологический процесс будет проще и экономичнее, если механическая обработка не прерывается термическими операциями. Это возможно предусмотреть, если заготовка подвергается только предварительной термической обработке, которая заключается в отжиге, нормализации или улучшении материала заготовки.
После выполнения черновых операций, в случае необходимости,
в технологическом процессе предусматривается промежуточная
термическая обработка:
для улучшения обрабатываемости малоуглеродистых, в том числе легированных малоуглеродистых, стальных заготовок предусматривается нормализация;
старение предусматривается для крупных отливок ответственных деталей с целью снятия остаточных напряжений в материале заготовки.
После термической обработки (закалка и отпуск) заготовки Г до получения НRСЭ > 40 необходимо использовать для дальнейшей механической обработки абразивные инструменты. Это необходимо учитывать при составлении технологического маршрута.
При наличии в технических условиях требования повысить твердость отдельных поверхностей (чаще до НRСЭ = 55...60) посредством их цементации и последующей закалки необходимо науглероживать эти поверхности. Все другие поверхности должны быть защищены от цементации различными способами: омеднением, повышенным (на глубину цементации) припуском, который удаляют после цементации, но до закалки, а также комбинацией отмеченных способов.
Поверхности, подлежащие цементации, предохраняют от омеднения, покрывая их диэлектриком, чаще лаком.
В маршрутной технологии механической обработки предусматривается технический контроль соответствия параметров требованиям, заданным чертежом и техническими условиями.
В процессе разработки технологического маршрута обработки решается задача обеспечения всех требований к качеству детали (точность формы и размеров, взаимного расположения поверхностей, физико-механических свойств поверхностного слоя и шероховатости и т.п.)- При этом целесообразно придерживаться определенной последовательности:
1) для каждой поверхности детали установить последовательность (этапы) обработки, обратив внимание прежде всего на наиболее точные;
2) выбрать последовательность обработки поверхностей детали;
выявить возможность их одновременной обработки и наметить технологические базы;
3) выбрать способы обработки и обосновать количество переходов,
подобрать оборудование и технологическую оснастку;
4) определить возможность совмещения переходов обработки поверхностей детали и сформировать из них операции;
5) рассчитать режимы резания, выявить возможность их обеспече
ния на выбранном оборудовании, произвести нормирование операций
технологического процесса;
6)оформить документацию на маршрутно-операционнъш технологический процесс.
Дата добавления: 2018-05-12; просмотров: 351; Мы поможем в написании вашей работы! |
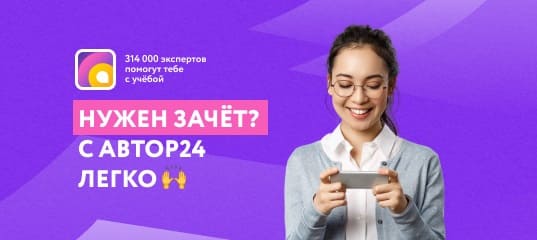
Мы поможем в написании ваших работ!