Принципы построения операций ТП механической обработки.
Ввиду многообразия факторов, обусловливающих построение технологических процессов, создать общие правила для его построения невозможно. Однако существуют некоторые соображения, установленные на основе опыта промышленности, которые следует учитывать при разработке технологического процесса.
Важнейшие из них следующие:
1. Технологический процесс должен обеспечивать выполнение технических требований, предъявляемых к изделию (детали) при условии наименьших затрат на изготовление при наибольшей производительности.
2. При механической обработке следует выполнять в первую очередь операции, при которых удаляются значительные припуски, так как:
\ а) в этом случае в наибольшей степени перераспределяются внутренние напряжения, возникшие при изготовлении заготовки, и происходит ее деформация в начале технологического процесса. При выполнении последующей обработки заготовки ей может быть придана правильная форма и размеры;
б) при снятии значительных слоев металла в начале технологического процесса можно выявить пороки металла для заготовок, а обнаруженный брак, возникший по этой причине, можно не пускать в дальнейшую обработку;
в) при снятии значительных припусков возникают большие силы резания, требующие соответствующих больших сил зажима заготовок; эти силы могут деформировать детали; при последующей обработке деталям могут быть приданы правильные формы и размеры.
|
|
3. Операции, при выполнении которых в большей степени уменьшается жесткость деталей, следует производить после тех, в которых эта жесткость уменьшается в меньшей степени. В этом случае при большой жесткости детали допустимые силы резания могут быть больше, следовательно, можно производить обработку с большими сечениями стружки.
4. При выполнении черновой и чистовой обработки в одной операции может быть затруднено достижение заданной точности из-за перераспределения внутренних напряжений после черновой обработки или повышенного износа станка из-за действия больших сил резания. В таких случаях рекомендуется выполнять черновую и чистовую обработку в разных операциях, на различных станках.
Классификация методов обработки цилиндрических поверхностей.
Обработка поверхностей на токарных станках.
Точение благодаря простоте кинематической схемы ишироким технологическим возможностям является одним из самых распространенных методов резания металлов. Токарная обработка (точение) – применяется для обработки резанием на токарных станках тел вращения (детали типа осей, валов, колец, втулок, дисков, фланцев и др.). Деталь крепится в шпинделе станка и вращается (главное движение, обеспечивающее образование стружки), а резец, закрепленный, в резцедержателе суппорта, совершает продольное или поперечное поступательное движение подачи, обеспечивающее снятие стружки о поверхности детали. Различают также вспомогательные движения, которые обеспечивают транспортирование и закрепление заготовки на станке, его включение и изменение частоты вращения заготовки, отвод резца и др.
|
|
Обработка заготовки должна производиться с рациональными режимами резания, т.е. скорости резания, подачи и глубины резания.
Скорость резания - это путь режущей кромки инструмента относительно обрабатываемой заготовки в направлении главного движения за единицу времени.
V = D n / 1000, м/мин,
где D - диаметр обрабатываемой поверхности, мм;
n- частота вращения шпинделя, об/мин;
V - скорость резания.
Подачей (S, мм/об) называют путь, пройденный режущей кромкой инструмента относительно вращающейся заготовки в направлении движения подачи за один оборот заготовки. Подача может быть продольной (при перемещении инструмента параллельно оси вращающейся заготовки) и поперечной, если инструмент перемещается перпендикулярно оси заготовки.
|
|
Глубина резания (t,мм) определяется толщиной срезаемого слоя материала, измеренного перпендикулярно к поверхности детали, за один рабочий ход инструмента относительно обрабатываемой поверхности:
t = (D-d)/2 , мм,
где D- диаметр обрабатываемой, поверхности, мм;
d - диаметр обработанной поверхности.
Обрабатываемая поверхность - поверхность, с которой снимают стружку; обработанной называют поверхность, с которой стружка удалена. Переходная поверхность между обрабатываемой и обработанной поверхностями, которая находится в контакте с кромкой режущего инструмента, называется поверхностью резания. Обработка наружных поверхностей
вращения называется обтачиванием, обработка внутренних повер
хностей вращения — растачиванием, обработка канавок — проре
занием, обработка торцов — подрезанием, а обработка резьб —
нарезанием.
Все известные внастоящее время конструкционные материалы могут быть обработаны точением. При применении в качестве инструментальных материалов быстрорежущих сталей и металлокерамических твердых сплавов точением обрабатывают стали и сплавы твердостью до HRCЭ 45.
|
|
При использовании сверхтвердых материалов, таких как алмаз и кубический нитрид бора, возможна обработка заготовок любой твердости.
Различают следующие виды точения:
черновое точение или обдирка - удаление поверхностных дефектных слоев заготовок, при котором срезается "корка" и основная (70%) часть припуска на обработку;
полулучистое точение - удаление 20...25% припуска, которое позволяет получать шероховатость Rz 40...20 и точность 11...10 квалитета. Заготовка получает форму, близкую к форме детали;
чистовое точение обеспечивает шероховатость Rz 20...12,5 и точность 9...7 квалитета, деталь получает окончательную форму и размеры;
тонкое точение позволяет при срезании очень тонкого слоя получать на поверхности детали шероховатость Rz 0,65...0,32 и точность 7...5 квалитета.
В зависимости от типа обрабатываемой поверхности
используют различные типы универсальных или специальных рез
цов.
Станки токарной группы являются наиболее распространенным видом металлорежущего оборудования, применяемого во всех отраслях машиностроения. К основным типам станков этой группы относят токарно-винторезные, токарно-револьверные, токарные автоматы и полуавтоматы, токарно-лобовые, карусельные и др.
Токарно-винторезные станки предназначены для наружной и внутренней обточки цилиндрических деталей, так называемых "тел вращения", включая обработку конусных и сложных поверхностей, нарезание резьбы и т.д. Применяются широко в единичном и мелкосерийном производстве, ремонтных мастерских и других производствах при обработке единичных и малых групп деталей.
На токарно-револьверных станках обрабатываются малые и большие группы деталей сложной формы из прутка или штучных заготовок в серийном производство.
Токарные автоматы применяют в крупносерийном и массовом производствах для обработки деталей из прутка, а токарные полуавтоматы для обработки из прутка и штучных заготовок.
Токарно-лобовые станки предназначены для обработки коротких деталей большого диаметра.
Дата добавления: 2018-05-12; просмотров: 353; Мы поможем в написании вашей работы! |
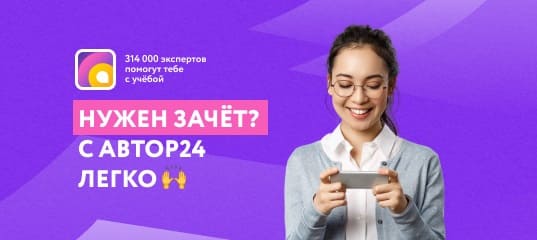
Мы поможем в написании ваших работ!