Режимы резания и основные процессы резания.
Под термином режимы резания понимается совокупность числовых значений глубины резания, подачи, скорости резания, геометрических параметров и стойкости режущей части инструментов, а также силы резания, мощности и других параметров рабочего процесса резания, от которых зависят его технико-экономические показатели. Режимы резания будут рациональны, если они позволяют получить высокие технико-экономические показатели процесса. Названные показатели обеспечиваются, если:
а) режущая часть инструмента имеет оптимальные геометрические параметры и качественную заточку лезвий;
б) обработка заготовок ведется с технически и экономически обоснованными подачами S и скоростями резания υ;
в) кинематические и динамические возможности механизмов коробки подач и коробки скоростей станка позволяют реализовать обоснованные значения подачи и скорости резания.
Режимные параметры взаимосвязаны и поэтому нельзя произвольно заменять значение хотя бы одного из них, не изменяя соответствующим образом всех прочих. При выборе и назначении режимов резания необходимо производить соответствующее согласование значений всех параметров с учетом возможности их реализации на используемом оборудовании. Необходимость оценки и учета большого количества взаимовлияющих факторов ведет к тому, что для решения задачи расчета и назначения режимов резания требуется использовать метод постепенного приближения. Т. е., задаваясь предварительными (стартовыми) значениями некоторых параметров, производить последующую корректировку, расчет и уточнение с учетом других параметров до получения окончательных значений, которые могут быть использованы для реализации данного технологического процесса. Может оказаться, что несколько вариантов сочетаний режимных параметров удовлетворяют поставленным требованиям, т. е. решение поставленной задачи иногда может быть многовариантным.
|
|
Назначение и методика расчета режимов резания.
Обычно выбор основных режимных параметров начинают с определения глубины резания. Она связана с припуском металла, оставляемым на выполнение данной технологической операции. На операциях чистовой обработки припуск составляет не более 0,5мм. На промежуточных операциях резания припуск на обработку изменяется в пределах 0,5...5мм. На операциях черновой обработки заготовок в зависимости от размеров и способа их изготовления припуск может быть более 5мм. За один проход резца может быть срезан припуск до 7мм. При превышении некоторых критических значений глубины резания могут возникнуть вибрации всей технологической системы, состоящей из станка, приспособления, инструмента и обрабатываемой заготовки. Поэтому при припуске более 7мм его срезают за два или более проходов резца, причем глубина резания на каждом проходе может быть одинакова, или ее последовательно уменьшают.
|
|
Значение подачи S, как и глубины резания, определяется видом технологической операции. Чистовую обработку ведут с подачами S < 0,1 мм/об. На промежуточных операциях формообразования подачу назначают, в пределах S=0,1...0,4 мм/об. Черновые операции с целью сокращения времени на обработку стремятся вести с подачами S = 0,4...0,7 мм/об.
На тяжелых станках обработку можно вести с глубинами резания до 30мм и с подачами до 1,5 мм/об.
При предварительном выборе подачи S в общем случае можно пользоваться следующими рекомендациями.
Если при выполнении операции следует основное внимание обращать на качество обработанной поверхности, то значения подач выбираются в пределах
S=(0,1 ... 0,125)t.
При черновой обработке, когда более важным параметром является производительность обработки, предварительные значения подач составят
S = (0,18 ... 0,2) t.
Таким образом, выбрав предварительно значение глубины резания t, можно тем самым установить интервал предварительных значений подач, учитывая выше приведенные рекомендации в зависимости от технологического назначения операции.
|
|
Следующим этапом является выбор конкретных рабочих значений основных режимных параметров.
Рабочая глубина резания, как правило, равна полуразности диаметров обрабатываемой и обработанной поверхностей.
t = (D – d)/2
Рабочую подачу выбирают из числа имеющихся в коробке подач станка, причем это значение должно находиться в пределах интервала предварительно выбранных значений подач. Рекомендуемые значения подачи Sвыбирают также по принятой методике расчета режимов резания (Косил).
Предварительное (стартовое) значение скорости резания вычисляется по уравнению (5 или 6),
υ=C /Tm tx Sy (HB/200)z,
υ = Cv kv /Tm tx Sy ,
где известны глубина резания t и выбранный интервал подач S.
Твердость заготовки НВ устанавливают по технической документации, сопровождающей поступающую на обработку партию деталей. Стойкость Тназначают согласно рекомендациям справочных материалов в зависимости от характера выполняемой операции и инструментального материала. При этом берут некоторый интервал значений стойкости. Например, для твердосплавных резцов при выполнении промежуточных операций формообразования на предварительном этапе можно назначить стойкость в пределах Т =30 ... 45 мин.
|
|
Значения коэффициентов и показателей степени выбирают из соответствующих таблиц методики расчета режимов резания.
По уравнению вычисляют два значения скорости резания: большее — для меньших значений подачи S и стойкости Т и меньшее — для больших их значений. По найденным значениям скорости резания для заданного диаметра Dмм обрабатываемой заготовки по уравнению
n = 1000υ/(πD) об/мин
рассчитывают два значения частоты вращения шпинделя — наибольшее и наименьшее. Таким образом, определяется интервал значений частоты вращения шпинделя, в пределах которого можно выбрать определенное значение, обеспечиваемое кинематикой станка.
Рабочая частота вращения шпинделя берется из числа значений, обеспечиваемых коробкой скоростей станка, причем выбранная частота вращения должна находиться в интервале частот для меньшей и большей скоростей, установленных на предварительном этапе. Так как для установленных на предварительном этапе интервалов подач и частот вращении шпинделя по кинематическим возможностям станков можно установить как одно, так и несколько, конкретных значений этих параметров, то их выбор на этом этапе требует в ряде случаев волевого решения. Выбор должен подчиняться логическим соображениям, учитывающим требования по производительности обработки и качеству обрабатываемых деталей. По установленным рабочим значениям основных режимных параметров — глубине резания t, подачеS и частоте вращения шпинделя n — проводят дальнейший расчет остальных рабочих режимов и соответствующих технико-экономических показателей.
. Рабочую скорость резания υ, м/мин, когда известна выбранная частота вращения шпинделя n, об/мин, определяют по уравнению
υ = 10-3πDn (8)
Рабочую стойкость резца рассчитывают с помощью уравнения (6), разрешенного относительно стойкости, т. е.
T = (Cv kv / υ tx Sy )1/m
причем это значение должно укладываться в выбранный интервал 30... 45 мин.
Если все режимы резания, кроме скорости, будут постоянными, то
C0v = Cv kv / tx Sy =const,
а выражение стойкости можно показать в виде
T = (C0v/ υ)1/m (9)
Сила резания, возникающая в процессе обработки с глубиной резания t, подачей S и скоростью υ рассчитывается по уравнению [Кос]
Р = 10Ср tx Sy υn Кp , [Н] (10)
Эффективная мощность, затраченная на обработку заготовки, подсчитывается по уравнению
Ne= Pυ/1020*60, [кВт] (11)
где Р – усилие резания в Ньютонах,
υ м/мин - скорость резания.
Необходимая мощность электродвигателя главного привода станка определяется по уравнению
Nэд= N℮/η, (12)
где η ≈ 0,8, - коэффициент полезного действия механизма главного привода станка.
26. Трудоемкость станочных операций.
Дата добавления: 2018-05-12; просмотров: 531; Мы поможем в написании вашей работы! |
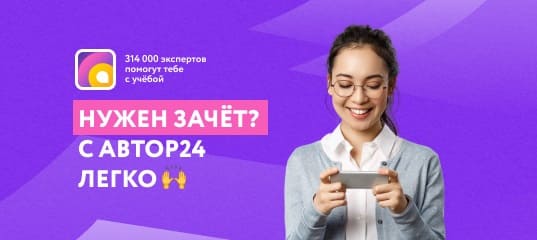
Мы поможем в написании ваших работ!