Единая система допусков и посадок (ЕСДП) в машиностроении. Квалитеты, основные отклонения, допуски, поля допусков системы.
ГОСТ 25346-89 “Основные нормы взаимозаменяемости. Единая система допусков и посадок. Общие положения, ряды допусков и основных отклонений.”
КВАЛИТЕТ (степень точности) – совокупность допусков, рассматриваемых как соответствующие одному уровню точности для всех номинальных размеров.
Основные отклонения отверстий обозначают прописными литерами латинского алфавита (А, В, С, D и т.д.), а валов – строчными (а, b, с, d и т.д.).
Основные отклонения-это одно из двух предельных отклонений (верхнее или нижнее) определяемое положением поля допуска относительно нулевой линии (осн. Отклонение-отклонение, ближайшее к нулевой линии)
Допуски (значения допусков, ширина полей допусков) обозначаются числами соответствующих квалитетов, например, Н6, Н7, Н11, Н12 означают поля допусков шестого, седьмого, одиннадцатого и двенадцатого квалитетов.
Основные отклонения, обозначаемые буквами, и допуски, обозначаемые числами, – два независимых составляющих элемента обозначения. У каждого из этих элементов своя роль: буквенное обозначение определяет положение поля допуска, а числовое – ширину поля (они определяют значения допусков указанных квалитетов).
Общее и специальное правило образования основных отклонений отверстий.
Основные отклонения отверстий определяются по двум правилам.
Общее правило. Основное отклонение отверстия должно быть симметрично относительно нулевой линии основному отклонению вала, обозначаемому той же буквой: EI = – es (от A до H); ES = – ei (от J до ZC).
|
|
Правило действительно для всех отклонений, кроме отклонений отверстия N квалитетов 9 – 16 для размеров свыше 3 мм у них ES = 0 и для отклонений, на которые распространяется специальное правило.
Специальное правило. Две соответствующие друг другу посадки в системе отверстия и в системе вала, в которых отверстие данного квалитета соединяется с валом ближайшего более точного квалитета, должны иметь одинаковые зазоры или натяги (например, H7/p6 и P7/h6).
ES = – ei + Δ, где Δ = ITn – ITn-1, т. е. разность между допуском рассматриваемого квалитета, с которым будет сопрягаться данное основное отклонение, и допуском ближайшего более точного квалитета.
Специальное правило действительно для интервалов размеров свыше 3 мм для отверстий: K, M, N – до 8-го квалитета включительно; P – ZC до 7-го квалитета включительно.
13.Основной вал и основное отверстие. Образование посадок в системе основного вала и основного отверстия в ЕСДП
В ЕСДП все рекомендуемые посадки построены либо в системе основного отверстия, либо в системе основного вала.
Основное отверстие – отверстие, у которого нижнее предельное отклонение равно о (EI = 0) и поле допуска задано в (+) плюс (букваH).
|
|
Основной вал – вал, у которого верхнее отклонение es = 0, а поле допуска задано в минус (-)(буква h).
Посадка в системе основного отверстия образуется сопряжением вала, имеющего любое поле допуска, с отверстием, поле допуска которого имеет основное отклонение H (EI=0). Например, H7/e6, H7/k6, H7/s6.
Посадки в системе основного вала получают при сопряжении отверстия (размер с любым полем допуска) и вала с полем допуска, имеющим основное отклонение h (es=0). Например, G7/h6, K7/h6, P7/h6.
Схемы посадок в системе основного отверстия – рис. 1 и основного вала – рис.2
СИСТЕМА ОСНОВНОГО ОТВЕРСТИЯ:
Посадки с зазором в системе основного отверстия образуются с использованием основных отклонений валов а, b, c, cd, d, e, ef, f, fg, g, h.
Посадки с основными отклонениями валов hи отверстий H обеспечивают наименьший зазор, равный 0; их называют посадками с нулевым гарантированным зазором.Они с одинаковыми основаниями относятся к посадкам в системе основного вала и в системе основного отверстия.
Переходные посадки в системе основного отверстия образуются с использованием основных отклонений валов js, j, k, m, n.
|
|
Посадки с натягом в системе основного отверстия образуются с использованием основных отклонений валов p, r, s, t, u, v, x, y, z, zb, zc.
СИСТЕМА ОСНОВНОГО ВАЛА:
Посадки с зазором в системе основного вала образуются с использованием основных отклонений отверстий А, B, C, CD, D, E, EF, F, FG, G, H.
Переходные посадки- основные отклонения отверстия Js, J, K, M, N.
Посадки с натягом- основные отклоненияотверстияP, R, S, T, U, V, X, Y, X, Z, ZB, ZC
Особенностью систем основного отверстия и основного вала является безусловная определенность характера посадок с зазором и переходных, в отличие от «посадок с натягом», которые зависят от значений допусков основных поверхностей (основных отверстий и валов). Например, посадка H9/p6 -переходная, хотя по приведенным выше правилам – посадка с натягом.
Систему вала следует применять в тех случаях, когда это оправдано конструктивными и экономическими условиями. Чаще всего точность отверстия задается грубее, рекомендуется не более чем на 2 квалитета. (обусловлено тем, что обработка отверстий всегда в худших условиях)
14.Рекомендуемые и предпочтительные поля допусков и посадки ЕСДП. Посадки с зазором.
В отличие отГОСТ 25346-89, который содержит всю возможную номенклатуру полей допуска и образованных с их помощью посадок, ГОСТ 25347-89 выделяет ограниченный перечень полей допуска и посадок, которые наиболее часто применяются на практике. Эти поля допуска и посадки названы рекомендованными. Кроме этого, в среде рекомендуемых полей допусков и посадок в этом стандарте выделяют предпочтительные.
|
|
Таким образом существует 3 уровня предпочтительности полей допуска:
1-Поля допуска и посадок общей номенклатуры ГОСТ 25346-89
2-Рекомендуемые поля допуска и посадок ГОСТ 25347-89
3-Предпочтительные поля допуска и посадок тоже из ГОСТ 25347-89
Зазор - разность между размерами вала и отверстия до сборки, если размер отверстия больше размера вала.
Посадки с зазором-посадка, реализация которой всегда приводит к образованию зазора в соединении, т.е. наименьший предельный размер отверстия больше наибольшего предельного размера вала или равен ему.
Такие посадки предназначены для образования подвижных и неподвижных разъемных соединений детали.
Наиболее распространенными соединениями с зазором являются подшипники скольжения.
В подвижных соединениях зазор служит для обеспечения свободы относительного перемещения деталей, размещения слоя смазки, погрешности сборки и т.д.
В неподвижных соединениях посадки с зазором применяются для обеспечения точной сборки деталей, их неподвижность обеспечивается дополнительными креплениями.
Выбор посадки для неподвижных соединений производится так, чтобы наименьший зазор компенсировал отклонение формы поверхностей. Наибольший зазор определяется исходя из допустимых погрешностей в сопряжении деталей.
Посадки с нулевым гарантированным зазором (H/h) применяются в случаях продольного перемещения деталей или поворота с небольшой скоростью.
Применение посадок с зазором:
H7/g6, G7/h6 -для обеспечения точного вращения детали с необходимым числом оборотов применяют посадки с наименьшим гарантированным зазором.
H7/h6, F8/h6 – для опоры скольжения с высокими требованиями центрирования применяют посадки с большим гарантированным зазором.
H7/e8, H8/e8, H9/d9 – для опор с трением скольжения при невысоких требованиях точности
При расчете необходимо точно учитывать требования к данному сопряжению в конкретном изделии. Например, в неподвижных сопряжениях следует учитывать последствия смещения с зазором, в направляющих скольжения следует учитывать влияние зазоров на перемещение.
15. Рекомендуемые и предпочтительные поля допусков и посадки ЕСДП. Посадки с натягом
Натяг – разность между размерами вала и отверстия до сборки, если размер вала больше размера отверстия.
Посадка с натягом – посадка, при которой всегда образуется натяг в соединении, т.е. наибольший предельный размер отверстия меньше наименьшего предельного размера вала.
Посадки с натягом применяются для получения неподвижных неразъемных соединений без дополнительных средств крепления (шпонок, штифтов и др.).
Условием годности посадки с натягом является обеспечение минимальным натягом передачи внешней нагрузки без разрушения соединения, а максимальный натяг должен обеспечивать прочность соединения при сборке (отсутствие разрушения соединения).
H7/p6, P7/h6 -посадки с минимальным натягом применяются как центрирующие посадки, если сопряжение в условиях динамических нагрузок
H7/r6, H7/s6 – для передачи крутящего момента или осевой силы
Надежность посадок с натягом зависит от многих факторов: механические свойства материалов, размеры сопрягаемых поверхностей, шероховатость и т.д.
Выбранную посадку следует проверить на опытной партии сопряжений.
16.Рекомендуемые и предпочтительные поля допусков и посадки ЕСДП. Переходные посадки.
В отличие отГОСТ 25346-89, который содержит всю возможную номенклатуру полей допуска и образованных с их помощью посадок, ГОСТ 25347-89 выделяет ограниченный перечень полей допуска и посадок, которые наиболее часто применяются на практике. Эти поля допуска и посадки названы рекомендованными. Кроме этого, в среде рекомендуемых полей допусков и посадок в этом стандарте выделяют предпочтительные.
Таким образом существует 3 уровня предпочтительности полей допуска:
1-Поля допуска и посадок общей номенклатуры ГОСТ 25346-89
2-Рекомендуемые поля допуска и посадок ГОСТ 25347-89
3-Предпочтительные поля допуска и посадок тоже из ГОСТ 25347-89
Переходная посадка- посадка, при которой возможно получение как зазора, так и натяга в соединении в зависимости от действительных размеров отверстия и вала. При графическом изображении поля допусков отверстия и вала перекрываются полностью или частично.
Переходная посадка представляет собой характеристику партии сопряжений с большей или меньшей вероятностью зазоров и натягов. В конкретном сопряжении двух деталей может быть либо зазор, либо натяг.
Предназначены для неподвижных соединений деталей, подвергающихся при ремонтах или по условиям эксплуатации сборке и разборке. Взаимная неподвижность деталей обеспечивается шпонками, штифтами, нажимными винтами и т.п. Менее тугие посадки назначают при необходимости в частых разборках соединения, при неудобствах требуется высокая точность центрирования, при ударных нагрузках и вибрациях.
- При высоких требованиях точности и больших нагрузках и работе в условиях вибрации назначаются ПП с наибольшей вероятностью натягаH/n, H/k
- При умеренных и спокойных нагрузках применяются ПП: M/m, M/h
- При частой разборке и сборке выбирают ПП типа: H/k, K/h, H/js, JS/h.
17.Поля допусков и посадки деталей из пластмасс.
Система полей допусков и посадок деталей из пластмасс согласно ГОСТ 25349-89. Стандарт распространен на гладкосопряженные и несопряженные элементы деталей из пластмасс с номинальным размером от 1 до 500 нм.
Данная система отличается от системы полей и допусков металлических изделий следующими свойствами:
- Нормальные условия измерения: номинальная температура20 ,как это установлено для металлов, дополнительно включают относительную влажность 65%
- В системе используются поля допусков с 8 по 18 и предусматриваются поля допусков с основными отклонениями аy, аz, аe– для валов и АY, АZ, АE – для отверстий, которых нет в системе допусков для металлических деталей.
- В стандарте есть рекомендуемые посадки, но не выделены предпочтительные поля допусков и посадки.
- В системе используются дополнительные основные отклонения аy, аz, аe (АY, АZ, АE), а также отклонения типа zа и ZА, которые расположены дальше от нулевой линии, чем крайниеотклоненияа, А и z, Z и предназначены для образования посадок в системах основных вала и отверстия с очень большими зазорами (отклонения аy, аz, аe, АY, АZ, АE) или натягами (zа, zb, zc,ZА, ZB, ZC)
Эти основные отклонения позволяют учитывать некоторые свойства пластмасс такие, как увеличенные температурные коэффициенты, склонность к старению и деформациям, пониженные упругие свойства.
18.Система общих допусков линейных и угловых размеров деталей
Для тех случаев, когда требования к точности элемента детали не указаны индивидуально, непосредственно у этого элемента, то можно использовать в технических требованиях общие допуски размеров, формы и расположения поверхностей.
Общий допуск размера – допуск линейного или углового размера, указываемый на чертеже или в других технических документах общей записью и применяемый в тех случаях, когда предельные отклонения не указаны индивидуально у соответствующих номинальных размеров.
Общие допуски применяются:
- для линейных размеров (наружных, внутренних, межосевых расстояний, размеров фасок, скруглений);
- угловых размеров, включая прямые углы 90º;
- линейных и угловых размеров, получаемых при обработке деталей в сборке.
Общие допуски применяются для металлических деталей, изготовленных резанием, также могут применятся для неметаллических деталей и деталей, обрабатываемых способами, не относящимися к резанию.
Например, нет стандартов допусков размеров заготовок, вырезаемых из листа технологическим лазером, значит, на эти параметры можно назначить общие допуски.
Общие допуски размеров установлены по четырем классам точности:
- точный f; - средний m; - грубый c; - очень грубый v;
Ссылка на общие допуски должна содержать номер настоящего стандарта и буквенное обозначение класса точности по данному стандарту - ГОСТ 30893.1–т.
Преимущества применения общих допусков:
- легче читаются чертежи;
- сокращается время работы конструктора;
- облегчается управление качеством, так как размеры с общими допусками контролируются только выборочно;
19. Методы выбора полей допусков и посадок.
Существует три основных метода выбора полей допуска и посадок:
1. Метод прецедентов (аналогов)
Суть метода состоит в том, что конструктор должен отмечать изделия, ранее сконструированные и находящиеся в эксплуатации, для которых накоплен положительный опыт использования, и на основе этого назначать аналогичные поля допусков и посадки для проектируемого изделия.
2. Метод подобия
Метод подобия при назначении посадок используется при наличии большого справочного материала по применению посадок в конструкциях. При совпадении конструктивных и эксплуатационных показателей проектируемого и аналогичного изделия (рекомендуемого по справочнику) производится выбор посадки. Таковыми будут считаться конструкции, совпадающие с проектируемыми по характеру соединения (типу посадки: с зазором, натягом или переходная); по системе посадки (отверстия или вала); по точности изделия (машины, механизма), а также по экономическойточности обработки деталей сопряжения (в нормальных производственных условиях).
Порядок назначения посадки методом подобия:
- выбирается система посадки, определяется ее тип (с зазором, натягом или переходные) и вид сопряжения;
- выбирается квалитет, учитывая условия эксплуатации данного соединения;
- назначается посадка по рекомендациям;
- определяются предельные отклонения сопрягаемых деталей;
- строится схема расположения полей допусков, рассчитываются предельные и среднее значения зазоров или натягов и допуск посадки;
- посадки указываются на сборочном чертеже, а поля допусков на чертежах деталей, входящих в изделие.
Недостатки для 1 и 2 методов: Сложность определения признаков однотипности и подобия.
3. Расчетный метод.
Выбирая этим методом квалитеты поля допуска и посадки при проектировании детали стремятся максимальным способом удовлетворить эксплуатационные требования (требования к точности, прочности и т.д.). Этот метод предполагает проведение сложных вычислений с использованием большого объема исходных данных, что совершить сложно, поэтому применяется он редко, в основном при проектировании.
Дата добавления: 2018-05-02; просмотров: 5209; Мы поможем в написании вашей работы! |
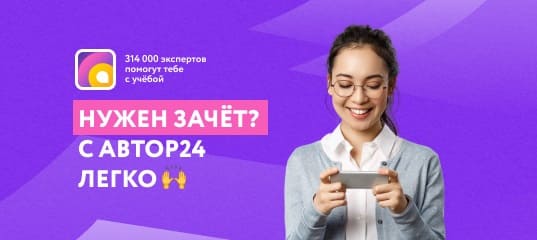
Мы поможем в написании ваших работ!