Параметры, определяющие качество поверхностного слоя. Зависимость шероховатости, микротвердости, остаточных напряжений при резании от условий обработки
Качество детали после обработки резанием прежде всего определяется: – точностью размеров; – геометрическими параметрами качества – шероховатостью, граностью, бочкообразностью, корсетностью и т.д.; – физическими параметрами – глубиной и степенью наклепа, микроструктурой, остаточными поверхностными напряжениями, дислокационной структурой и т.д.
Влияние скорости резания на шероховатость
Влияние подачи на шероховатость обработанной поверхности. При чистовой обработке повышение подачи чаще ограничивается требуемой низкой шероховатостью обработанной поверхности.
Влияние глубины резания на шероховатость. При работе с резцами ε < 90° повышается высота неровностей.
Влияние свойств обрабатываемого и инструментального материалов на шероховатость.
Влияние геометрии инструмента на наклеп. На условия стружкообразования в основном влияет передний угол γ. При изменении γ от +15 до –15° глубина наклепа hн увеличивается. Увеличение радиуса округления режущего лезвия ρ повышает наклеп поверхностного слоя. Значительное влияние на характеристики наклепа оказывает и инструментальный материал через коэффициент трения на задней поверхности.
Элементы режима резания при круглом наружном шлифовании. Формула машинного времени
Существуют три способа наружного круглого шлифования: шлифование продольной подачей; шлифование за один проход – глубинное; шлифование методом врезания. Шлифование с продольной подачей (рис. 134, а) применяют при обработке относительно длинных (нежестких) деталей. Глубина резания, равная поперечной подаче, измеряется за время двойного продольного хода детали. При черновом шлифовании стали S = = 0,01…0,07 мм/дв. ход; при чистовом S = 0,005…0,02 мм/дв. ход. Величина продольной подачи выбирается в зависимости от ширины круга. Для чернового шлифования S = (0,3…0,85), для чистового S = (02…0,3)В, мм/об. Шлифование глубинное применяется при обработке жестких относительно коротких деталей. Припуск в данном случае снимается за один проход. Подача S = 1...6 мм/об. Чем больше диаметр обработки, тем больше подача. Шлифование методом врезания применяется при обработке деталей относительно малой длины, особенно при шлифовании фасонных поверхностей. Поперечную подачу S принимают 0,02…0,07 мм/об
|
|
to = QM/Q = FП/VДst, где QM - объем металла, подлежащего снятию, мм3, F - поверхность обработки, мм2, П - припуск на сторону, мм, Q - объем металла, снимаемый в единицу времени, мм3/мин, VД, s, t- подачи при шлифовании
Физическая сущность процесса шлифования. Изнашивание и стойкость шлифовальных кругов. Понятие о самозатачивании, засаливании шлифовальных кругов
|
|
При шлифовании толщина среза измеряется сотыми и тысячными долями миллиметра. Процесс стружкообразования при снятии тонких стружек в значительной мере определяется отношением K = а/ρ, где а – толщина среза; ρ – радиус округления лезвия. Чем больше K, тем в более благоприятных условиях протекает процесс стружкообразования и становится сходным с процессом стружкообразования при снятии толстых стружек.
В зависимости от условий шлифования круг может работать как в режиме затупления, так и в режиме самозатачивания. Под самозатачиванием понимается способность круга обновлять свою рабочую поверхность под влиянием сил резания. Самозатачивание наступает тогда, когда нагрузка и другие условия работы становятся такими, что зерна раскалываются, образуя новые острые выступы. В различных условиях обработки абразивный инструмент подвергается следующим видам износа: хрупкому, адгезионному, диффузионному и абразивному. При работе изношенным кругом возрастают
усилие и темпера- тура резания, появляются вибрации, что ухудшает качество обработанной поверхности. Для исправления геометрической формы круга и восстановления его режущей способности применяют правку, чаще всего алмазным инструментом (карандаши, ролики и т.д.). При правках удаляется более 60…70 % рабочего объема круга.
Дата добавления: 2018-05-02; просмотров: 605; Мы поможем в написании вашей работы! |
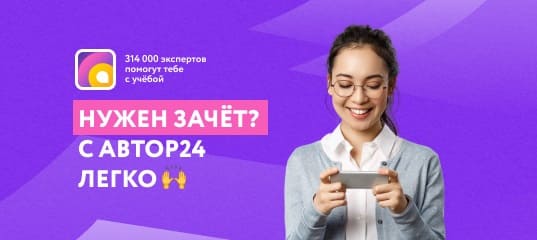
Мы поможем в написании ваших работ!