Классификация сварных соединений и швов
Министерство образования и науки Российской Федерации
Государственное образовательное учреждение
высшего профессионального образования
«Омский государственный технический университет»
Еремин Е.Н.
ТЕХНОЛОГИЧЕСКИЕ ОСНОВЫ СВАРКИ ПЛАВЛЕНИЕМ
Конспект лекций
Омск
Издательство ОмГТУ
2013
ОГЛАВЛЕНИЕ
ПРЕДИСЛОВИЕ.. 3
ВВЕДЕНИЕ.. 4
1 ТИПЫ СВАРНЫХ СОЕДИНЕНИЙ И ШВОВ. КОНСТРУКЦИОННЫЕ ЭЛЕМЕНТЫ СВАРНЫХ СОЕДИНЕНИЙ. 6
1.1 Классификация сварных соединений и швов. 6
1.2 Конструктивные элементы сварных соединении. 11
2 СВАРОЧНЫЕ МАТЕРИАЛЫ. 15
2.1. Назначение сварочных материалов. 15
2.2. Покрытые электроды для дуговой сварки и наплавки. 17
2.3. Сварочная сплошная и порошковая проволока, прутки, порошки, неплавящиеся электроды.. 25
2.4. Флюсы сварочные. 29
2.5. Защитные газы. 34
2.6. Газы для газопламенной обработки. 35
3 СУЩНОСТЬ И ТЕХНИКА РАЗЛИЧНЫХ СПОСОБОВ СВАРКИ ПЛАВЛЕНИЕМ И ТЕРМИЧЕСКОЙ РЕЗКИ. 38
3.1. Ручная дуговая сварка металлическими электродами с покрытием. 38
3.2. Дуговая сварка под флюсом. 40
3.3. Дуговая сварка в защитных газах. 43
3.4. Электрошлаковая сварка. 50
4 ТЕХНОЛОГИЯ СВАРКИ УГЛЕРОДИСТЫХ И НИЗКОУГЛЕРОДИСТЫХ НИЗКОЛЕГИРОВАННЫХ КОНСТРУКЦИОННЫХ СТАЛЕЙ.. 54
4.1.Состав и свойства сталей. 54
4.2. Особенности технологии и техники сварки. 56
5 ТЕХНОЛОГИЯ СВАРКИ НИЗКО- И СРЕДНЕЛЕГИРОВАННЫХ ЗАКАЛИВАЮЩИХСЯ СТАЛЕЙ.. 52
5.1 Сварка низколегированных бейнитно – мартенситных сталей. 62
|
|
5.2. Сварка среднелегированных мартенситно-бейнитных сталей. 65
5.3. Сварка жаропрочных перлитных сталей. 70
6 ТЕХНОЛОГИЯ СВАРКИ ВЫСОКОХРОМИСТЫХ МАРТЕНСИТНЫХ, МАРТЕНСИТНО - ФЕРРИТНЫХ И ФЕРРИТНЫХ СТАЛЕЙ.. 74
6.1. Сварка мартенситных хромистых сталей. 74
6.2. Сварка мартенситно-ферритных сталей. 76
6.3. Сварка ферритных хромистых сталй. 77
7 ТЕХНОЛОГИЯ СВАРКИ ВЫСОКОЛЕГИРОВАННЫХ АУСТЕНИТНЫХ СТАЛЕЙ И СПЛАВОВ.. 79
7.1. Состав и свойства сталей. 79
7.2. Особенности технологии и техники сварки. 82
8 ТЕХНОЛОГИЯ СВАРКИ РАЗНОРОДНЫХ СТАЛЕЙ.. 90
8.1. Свариваемость разнородных сочетаний сталей. 91
8.2. Особенности технологии сварки комбинированных конструкций из сталей различных структурных классов. 93
8.3. Особенности технологии сварки комбинированных конструкций из разнородных сталей одного структурного класса. 96
9 ТЕХНОЛОГИЯ СВАРКИ ЧУГУНА.. 98
9.1. Состав и свойства. 98
9.2. Основные сведения о свариваемости. Технологические рекомендации по дуговой сварке. 99
10 ТЕХНОЛОГИЯ СВАРКИ ЦВЕТНЫХ МЕТАЛЛОВ И СПЛАВОВ НА ИХ ОСНОВЕ.. 108
10.1 Состав и свойства. 108
10.2. Особенности технологии и техники сварки. 109
11 БЕЗОПАСНОСТЬ ТРУДА И ЗАЩИТА СРЕДЫ ОБИТАНИЯ.. 140
СПИСОК ЛИТЕРАТУРЫ... 145
|
|
ВВЕДЕНИЕ
При сварке плавлением под действием источника тепла кромки металла свариваемых элементов (основной металл) и если необходимо, дополнительный металл (сварочная проволока и др.) расплавляются в месте соединения совместно образуя сварочную ванну. В ней происходят различные физико-химические взаимодействия. При охлаждении, по мере удаления источника тепла металл сварочной ванны кристаллизуется, образуя сварной шов, соединяющий свариваемые элементы. В отличие от основного металла, структура которого характерна измельченным после пластической деформации зерном (прокатка и т.д. за исключением сварно-литых конструкций) металл шва всегда имеет структуру литого металла с укрупненным зерном. Его химический состав и свойства могут значительно отличаться от состава и свойств основного металла.
Рядом со швом в основном металле под действием тепла, распространяющегося из зоны сварки, происходят структурные изменения (зона термического влияния). Таким образом сварное соединение, т.е. металл шва и зоны термического влияния характеризуется разнообразием структур и значит и свойств. Последующая термическая обработка позволяет уменьшить это различие.
|
|
При сварке плавлением в качестве источника тепла используют различные источники: высокотемпературное газовое пламя (газовая сварка), электрическую дугу (электродуговая сварка), теплоту выделяемую в шлаковой ванне проходящим через нее электрическим током (электрошлаковая сварка), теплоту струи ионизированных газов плазмы (плазменная сварка), теплоту, выделяемую в металле в результате преобразования в нее кинетической энергии электронов (электронно-лучевая сварка), теплоту когерентного светового луча лазера (лазерная сварка) и некоторые другие.
Из способов сварки плавлением наиболее широко используется электродуговая сварка. Она имеет много разновидностей в зависимости от способа защиты зоны сварки от воздуха и металлургических взаимодействий в ней и в металле сварочной ванны. Это сварка покрытыми электродами, под флюсом, в защитных газах, порошковой проволокой. По степени механизации она может быть ручной, полуавтоматической и автоматической.
Сварка плавлением используется для соединения практически всех используемых в технике металлов толщиной от долей миллиметра до сотен сантиметров, а также некоторых неметаллов (стекла, керамики, графита и др.). Широкие возможности сварки плавлением облегчают решение задач, стоящих перед инженерами-технологами. Однако разработанный технологический процесс должен не только обеспечить требуемые свойства сварных соединений, но быть экономичным и экологически приемлемым. При разработке технологического процесса изготовления целесообразна разработка нескольких его вариантов с использованием ЭВМ для выбора оптимального.
|
|
Россия внесла значительный вклад в создание и развитие сварки плавлением. В 1882 г. Н.Н. Бенардос предложил способ электродуговой сварки угольным электродом. Дальнейшее развитие электродуговая сварка получила в работах Н.Г. Славянова (1888 г.), применившего в качестве электрода металлический стержень, который одновременно являлся и присадочным (дополнительным) металлом. Славянов Н.Г. разработал металлургические основы электродуговой сварки, предложив использовать в качестве флюса дробленое стекло для защиты расплавленного металла сварочной ванны от взаимодействия с воздухом. Однако качество сварных соединений было низким. Значительно повысилось их качество, когда в 1907 г. шведский инженер О. Кьельберг разработал электроды, в которых на металлический стержень наносилось специальное покрытие. Оно содержало легирующие, раскисляющие, газозащитные и шлакообразующие компоненты.
В России интенсивное применение сварки с одновременным проведением широкого круга исследований по технологии, металлургии, прочности сварных конструкций, разработке сварочного оборудования началось с середины 20-х годов в различных регионах страны. Во Владивостоке (В.П. Вологдин, Н.Н. Рыкалин, Г.К. Татур, С.А. Данилов), в Москве (Г.А. Николаев, К.К. Хренов, К.В. Любавский) в Ленинграде (В.П. Никитин, А.А. Алексеев, Н.О. Окерблом) и т.д. Особую роль в развитии и становлении сварки сыграл академик Е.О. Патон, создавший в 1929 г. лабораторию, а впоследствии и Институт электросварки АН УССР, в котором в конце 30-х годов был разработан новый способ - автоматическая сварка под флюсом. Там же в 1949 г. был создан принципиально новый вид сварки плавлением - электрошлаковая сварка. Широкое применение в промышленности находит разработанный в 50-х годах в ЦНИИТМАШе К.В. Любавским и Н.М. Новожиловым способ сварки плавящимся металлическим электродом в среде углекислого газа. Его существенными преимуществами является универсальность (автоматический и полуавтоматический), высокая производительность и качество, экономичность. Электронно-лучевая сварка была разработана французскими учеными в конце 50-х годов. Использование для сварки оптических квантовых генераторов-лазеров началось в 60-х годах. Сварка занимает достойное место в ряду других технологических процессов. Это обусловлено универсальностью, возможностью значительной экономии металла, возможностью создания уникальных конструкций, которые при других технологических процессах создать невозможно.
1 ТИПЫ СВАРНЫХ СОЕДИНЕНИЙ И ШВОВ.
КОНСТРУКЦИОННЫЕ ЭЛЕМЕНТЫ СВАРНЫХ СОЕДИНЕНИЙ.
Классификация сварных соединений и швов
Термины и определения основных понятий в области сварки устанавливает ГОСТ 2601-84 (в ред. 1992 г.). Термины, установленные стандартом, обязательны для применения в документации всех видов, научно-технической, учебной и справочной литературе.
Сварное соединение - неразъемное соединение, выполненное сваркой.
Термины и определения основных понятий в области сварки устанавливает ГОСТ 2601-84 (в ред. 1992 г.). Термины, установленные стандартом, обязательны для применения в документации всех видов, научно-технической, учебной и справочной литературе.
Сварное соединение - неразъемное соединение, выполненное сваркой. Сварное соединение (рис. 1.1) включает три образующиеся в результате сварки характерные зоны металла в изделии: зону сварного шва 1, зону сплавления 2, зону термического влияния 3, а также часть основного металла 4, прилегающую к зоне термического влияния.
Рис. 1.1. Сварное соединение
Сварной шов - участок сварного соединения, образовавшийся в результате кристаллизации расплавленного металла.
Металл шва - сплав, образованный расплавленным основным и наплавленным металлами или только переплавленным основным металлом. Основной металл - металл подвергающихся сварке соединяемых частей.
Зона сплавления - зона, где находятся частично оплавленные зерна металла на границе основного металла и металла шва. Эта зона нагрева ниже температуры плавления. Нерасплавленные зерна в этой зоне разъединяются жидкими прослойками, связанными с жидким металлом сварочной ванны и в эти прослойки имеют возможность проникать элементы, введенные в ванну с дополнительным металлом или сварочными материалами. Поэтому химический состав этой зоны отличен от химического состава основного металла.
Зона термического влияния - участок основного металла, не подвергшийся расплавлению, структура и свойства которого изменились в результате нагрева при сварке, наплавке или резке.
Тип сварного соединения определяет взаимное расположение свариваемых элементов. Различают: стыковые, угловые, тавровые, нахлесточные и торцовые сварные соединения.
Стыковое соединение - сварное соединение двух элементов, примыкающих друг к другу торцовыми поверхностями и расположенных в одной плоскости или на одной поверхности (рис. 1.2). Поверхности элементов могут быть несколько смещены при соединении листов разной толщины (см. рис. 1.2, б).
Угловое соединение - сварное соединение двух элементов, расположенных под углом и сваренных в месте примыкания их краев (рис. 1.3).
Тавровое соединение - сварное соединение, в котором торец одного элемента примыкает под углом и приварен к боковой поверхности другого элемента (рис. 1.4).
а) б) в)
Рис. 1.2. Стыковые соединения
а) б) в)
Рис. 1.3. Угловые соединения
а) б)
Рис. 1.4. Тавровые соединения
Нахлесточное соединение - сварное соединение, в котором сваренные элементы расположены параллельно и частично перекрывают друг друга (рис. 1.5, а, б). Отсутствие опасности прожогов при сварке облегчает применение высокопроизводительных режимов сварки. Применение нахлесточных соединений облегчает сборку и сварку швов, выполняемых при монтаже конструкций (монтажных швов).
Торцовое соединение - сварное соединение, в котором боковые поверхности сваренных элементов примыкают друг к другу (рис. 1.5,в).
Сварные швы подразделяют по разным признакам: по типу шва, по протяженности, по способу выполнения, по пространственному положению и по форме разделки кромок.
По типу сварные швы делят на стыковые, угловые и прорезные.
Стыковой шов - сварной шов стыкового соединения. Угловой шов - сварной шов углового, нахлесточного или таврового соединений. Прорезной шов (рис. 1.6) получается в результате полного проплавления верхнего, а иногда и последующих листов, и частичного проплавления нижнего листа (детали). Частным случаем прорезного шва является точечный или пробочный шов (электрозаклепка - при дуговой сварке) (рис. 1.6, г). Прорезные швы при приварке толстого листа (рис. 1.6, д) могут выполняться по заранее выполненным отверстиям в верхнем листе (при точечном шве) или прорези (при непрерывном шве).
Различают следующие характеристики сварного шва: ширину, выпуклость, вогнутость и корень шва.
Ширина шва е - расстояние между видимыми линиями сплавления сварного шва (см. рис. 1.2, а). Выпуклость шва g определяется расстоянием между плоскостью, проходящей через видимые линии границы сварного шва с основным металлом и поверхностью сварного шва, измеренным в месте наибольшей выпуклости (см. рис. 1.2, а; 1.4, а). Вогнутость шва т определяется расстоянием между плоскостью, проходящей через видимые линии границы шва с основным металлом и поверхностью шва, измеренным в месте наибольшей вогнутости (см. рис. 1.2, в; 1.3, в). Вогнутость корня стыкового шва является дефектом обратной стороны одностороннего шва. Корень шва - часть сварного шва, наиболее удаленная от его лицевой поверхности (см. рис. 1.2, б; 1.4, а). По существу это обратная сторона шва, в которой различают ширину е1 и высоту g1 обратного валика (см. рис. 1.2, а).
Угловой шов имеет следующие размерные характеристики: катет, толщину, расчетную высоту. Катет углового шва к определяется кратчайшим расстоянием от поверхности одной из свариваемых частей до границы углового шва на поверхности второй свариваемой части (см. рис. 1.3, в; 1.4, а). Катет задается в качестве параметра режима, который нужно выдерживать при сварке. Толщина углового шва а - наибольшее расстояние от поверхности углового шва до точки максимального проплавления основного металла (см. рис. 1.4, а). Для оценки прочности сварного соединения используют расчетную высоту углового шва - р (см. рис. 1.4, а). Для угловых швов более благоприятна вогнутая форма поверхности шва с плавным переходом к основному металлу (см. рис. 1.3, в).
По протяженности сварные швы подразделяют на непрерывные и прерывистые. Стыковые сварные швы, как правило, выполняют непрерывными. Угловые швы могут быть непрерывными (рис. 1.7, а) и прерывистыми (рис. 1.7, б), с шахматным (рис. 1.7, в) и цепным (рис. 1.7, г) расположением отрезков шва. Угловые швы могут быть выполнены и точечными швами (рис. 1.7, б, д).
По способу выполнения различают сварку: одностороннюю и двустороннюю, однослойную и многослойную. Одностороннюю сварку стыкового сварного соединения выполняют со сквозным проплавлением кромок на подкладке или без подкладки (на весу). Двустороннюю сварку выполняют с зачисткой (удалением) корня шва (механической обработкой) перед сваркой обратной стороны сварного соединения или без зачистки корня шва. При двусторонней сварке зачастую приходится кантовать изделие или вести сварку в трудном потолочном положении.
Многослойный шов применяют при сварке металла большой толщины, а также для уменьшения зоны термического влияния. Под слоем сварного шва (I—IV на рис. 1.8) понимают часть металла сварного шва, которая состоит из одного или нескольких валиков (/-5 на рис. 1.8), располагающихся на одном уровне поперечного сечения шва. Валик - металл сварного шва, наплавленный за один проход. Под проходом при сварке подразумевается однократное перемещение в одном направлении источника тепла при сварке или наплавке.
По пространственному положению с учетом требований международных стандартов различают следующие сварные швы: горизонтальные (на вертикальной плоскости), вертикальные, потолочные и швы, сваренные в нижнем положении (рис. 1.9, 1.10). На рисунках даны русские и в скобках международные обозначения. Схемы сварки стыков труб с горизонтальной, вертикальной или наклоненной осью показаны на рис. 1.10.
Рис. 1.10. Положение шва при сварке стыковых (а) и угловых (б) соединений труб: Н1 - нижнее при горизонтальном расположении осей труб (трубы), свариваемых (привариваемой) с поворотом; Н2 - нижнее при вертикальном расположении оси трубы, привариваемой без поворота или с поворотом; В1 - переменное при горизонтальном расположении осей труб (трубы), свариваемых (привариваемой) без поворота "на подъем"; В2 - переменное при горизонтальном расположении осей труб (трубы), свариваемых (привариваемой) без поворота "на спуск"; Г - горизонтальное при вертикальном расположении осей труб, свариваемых без поворота или с поворотом; Н45 - переменное при наклонном расположении осей труб (трубы), свариваемых (привариваемой) без поворота; П2 - потолочное при вертикальном расположении оси трубы, привариваемой без поворота или с поворотом.
Дата добавления: 2018-04-15; просмотров: 525; Мы поможем в написании вашей работы! |
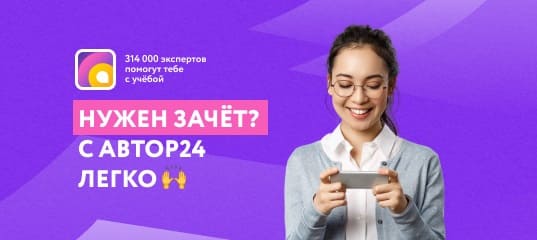
Мы поможем в написании ваших работ!