Ремонт корпуса шпиндельного узла
При ремонте корпуса (рис. 6.4) необходимо восстановить прямолинейность направляющих 2, 3, 4 и 5 и параллельность их оси отверстия для гильзы 7 шпинделя. Поверхности 2 и 3, 4 и 5 не должны быть извернуты. Поверхности 1 и 6 должны быть параллельны направляющим 2, 3 и 4, 5, а отверстие под гильзу шпинделя не должно иметь овальности и конусности.
Ремонт корпуса нужно начинать с восстановления точности отверстия. Для этого необходимо предварительно произвести замер отверстия и определить его геометрическую точность. Замер осуществить индикаторным нутромером. Необходимо определить зазор в посадке, для этого замерить диаметр гильзы шпинделя с помощью микрометра. При овальности и конусности более 0,005 мм отверстие восстановить притирами.
Доводку следует производить комплектом притиров из шести штук. Диаметр первого притира должен быть на 0,006-0,008 мм меньше диаметра отверстия корпуса, а диаметр каждого из последующих притиров должен быть на 0,005-0,007 мм полнее предыдущего. При доводке пользоваться пастой ГОИ, которую наносить на притир тонким слоем. После нескольких проходов отработанную пасту снять чистым керосином и затем повторить процесс.
Отверстие корпуса для гильзы шпинделя считается восстановленным, когда достигнута чистота поверхности V10, а конусность и овальность не превышают 0,003 мм.
Если в отверстии корпуса остались невыведенными 1-2 задира глубиной до 0,1-0,2 мм и шириной до 1 мм, то это не должно служить основанием для забраковки.
|
|
Направляющие корпуса удобно шабрить, после того, как в отверстие корпуса установлена отремонтированная гильза, по которой ориентируют положение поверхностей 2, 3, 4 и 5. Шабрение вести по поверочной линейке и шаблону, добиваясь непрямолинейности, извернутости и не параллельности их оси шпинделя не более 0,003 мм на всей длине поверхностей.
Количество отпечатков краски должно быть 20-25 на площади 25x25 мм.
Непрямолинейность и извернутость направляющих определять мостиком с уровнем методом построения графика. Непараллельность определять индикатором в горизонтальной и вертикальной плоскостях.
Поверхности 1 и 6 шабрить по поверочной линейке, добиваясь их параллельности к поверхностям 4 и 5, 2 и 3 с точностью 0,003 мм. Проверку параллельности осуществить индикатором, закрепленным на мостике. Последний располагают на направляющих корпуса, а измерительный штифт подводят к проверяемым поверхностям. Отклонения определяют, перемещая мостик по направляющим.
Направляющие 1, 2, 3 и 4рационально ремонтировать шабрением по сопрягаемым отремонтированным поверхностям 2, 3, 4 и 5 (рис. 6.4) корпуса шпинделя. При этом добиваются параллельности к поверхности 5 с точностью 0,01 мм на длине 300 мм и количество отпечатков при проверке на краску должно быть не менее 20-25 на площади 25x25 мм.
|
|
Проверку параллельности направляющих удобно производить при расположении блока на поверочной плите и установке на них корпуса шпинделя. При этом замеры выполняют индикатором методом засечек от поверхности плиты поверхней или нижней образующим оправки или гильзы шпинделя, установленной в отверстии корпуса. Засечки производить у торца корпуса и на расстоянии 200-300 мм.
Рисунок 6.4 Корпус шпиндельного узла
а — общий вид; б — схема проверки
Рисунок 6.5 Блок направляющих.
Дата добавления: 2018-04-15; просмотров: 515; Мы поможем в написании вашей работы! |
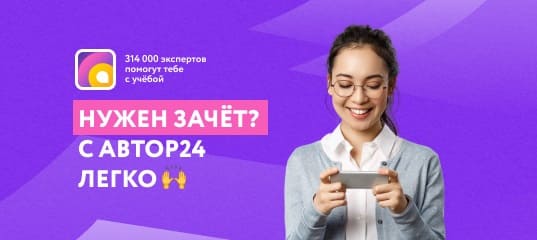
Мы поможем в написании ваших работ!