Группа 2: Сверлильные и расточные
Типы станков:
0 – не существует;
1 – вертикально-сверлильные;
2 – одношпиндельные полуавтоматы;
3 – многошпиндельные полуавтоматы;
4 – координатно-расточные;
5 – радиально-сверлильные;
6 – горизонтально-расточные;
7 – алмазно-расточные;
8 – горизонтально-сверлильные; центровые;
9 – разные.
Группа 3: Шлифовальные, полировальные, доводочные, заточные
Типы станков:
0 – не существует;
1 – круглошлифовальные;
2 – внутришлифовальные;
3 – обдирочно-шлифовальные;
4 – специализированные шлифовальные;
5 – продольно-шлифовальные;
6 – заточные;
7 – плоскошлифовальные;
8 – притирочные; полировальные; хонинговальные; доводочные;
9 – разные.
Группа 4: Комбинированные
Типы станков:
0 – не существует;
1 – не существует;
2 – светолучевые электрохимические;
3 – шлифовальные электрохимические; хонинговальные электрохимические; суперфинишные электрохимические;
4 – копировально-прошивочные электрохимические; электрохимические станки для удаления заусенцев; маркировочные электрохимические; контурнодоводочные электрохимические;
5 – вырезные электроэрозионные;
6 – электроэрозионные прошивочные станки для извлечения остатков сломанного инструмента;
7 – копировально-прошивочные электроэрозионные; ультразвуковые электроэрозионные; электрохимические прошивочные комбинированные электроэрозионные;
8 – анодно-механические отрезные;
|
|
9 – не существует;
Группа 5: Зубо- и резьбообрабатывающие
Типы станков:
0 – резьбонарезные;
1 – зубострогальные для цилиндрических зубчатых колес;
2 – зуборезные для конических зубчатых колес;
3 – зубофрезерные для цилиндрических зубчатых колес и шлицевых валов;
4 – зубофрезерные для нарезания червячных колес;
5 – станки для обработки торцев зубьев колес;
6 – резьбофрезерные;
7 – зубоотделочные; проверочные; обкатные;
8 – зубошлифовальные; резьбошлифовальные;
9 – разные;
Группа 6: Фрезерные
Типы станков:
0 – барабанно-фрезерные;
1 – вертикально-фрезерные консольные;
2 – фрезерные непрерывного действия;
3 – продольно-фрезерные одностоечные;
4 – копировально фрезерные; гравировальные;
5 – вертикально-фрезерные бесконсольные;
6 – продольно-фрезерные двухстоечные;
7 – консольно-фрезерные широкоуниверсальные;
8 – горизонтально-фрезерные консольные;
9 – разные;
Группа 7: Строгальные, долбежные, протяжные
Типы станков:
0 – не существует;
1 – строгальные одностоечные продольные;
2 – строгальные двухстоечные продольные;
3 – поперечнострогальные;
4 – долбежные;
5 – протяжные горизонтальные;
6 – не существует;
7 – протяжные вертикальные;
|
|
8 – не существует;
9 – разные;
Группа 8: Отрезные (разрезные)
Типы станков:
0 – не существует;
1 – отрезные, работающие резцом;
2 – отрезные, работающие абразивным кругом;
3 – отрезные, работающие гладким или насечным диском;
4 – правильно-отрезные;
5 – ленточные пилы;
6 – дисковые пилы;
7 – ножовочные пилы;
8 – не существует;
9 – не существует;
Группа 9: Разные
Типы станков:
0 – не существует;
1 – муфтообрабатывающие; трубообрабатывающие;
2 – пилонасекательные;
3 – правильнообдирочные; бесцентровообдирочные;
4 – не существует;
5 – станки для испытания инструмента;
6 – делительные машины;
7 – балансировочные;
8 – не существует;
9 – не существует;
Нумерация металлорежущих станков.
Исходя из выше представленной классификации, моделям станков присваивают условное обозначение (индекс или шифр), состоящее из сочетания цифр и букв:
1. Первая цифра – номер группы, к которой относится станок;
2. Вторая цифра – номер типа станка в пределах данной группы;
3. Буква после первой или второй цифры определяет модернизирован ли станок, либо указывает на определенную техническую характеристику станков одного размера;
4. Третья или третья-четвертая цифры определяют типоразмеры – один из важнейших цифровых параметров станка и обрабатываемой детали;
|
|
5. Буква после всех цифр в конце номера означает конструктивную модификацию базовой модели или технологические особенности станка.
Другие типы классификации.
По классу точности:
1. Нормальной точности (Н);
2. Повышенной точности (П);
3. Высокой точности (В);
4. Особовысокой точности (А);
5. Сверхвысокой точности (С).
По степени универсальности:
1. Универсальные (общего назначения) – используются для изготовления небольших партий деталей широкого спектра наименований и размеров;
2. Специализированные – используются для изготовления больших партий однотипных деталей схожих конфигураций, но разного размера;
3. Специальные – используются для изготовления очень крупных партий деталей одного вида или типоразмера.
По уровню автоматизации:
1. Ручные;
2. Станки-полуавтоматы;
3. Станки-автоматы;
4. Станки с числовым программным управлением;
5. Гибкие производственные модули.
По массе:
1. Легкие (до 1 тонны);
2. Средние (от 1 тонны до 10 тонн);
3. Тяжелые (более 10 тонн);
4. Уникальные (более 100 тонн).
Понятие о приводе станков.
Приводом станка называется совокупность механизмов, обеспечивающих получение одного элементарного (вращательного или поступательного) движения. В привод входят двигатель, механизм изменения передаточного отношения, механизм включения/выключения /реверсирования движений. В станках применяют приводы вращательного и поступательного движений. Существуют приводы периодического движения рабочих органов на точно фиксированную величину.
|
|
Приводы металлорежущих станков предназначены для осуществления рабочих, вспомогательных и установочных перемещений инструментов и заготовок.
К каждому виду привода, с учетом служебного назначения станка, предъявляют свои специфические требования по передаче мощности от привода, обеспечению постоянства скорости, ее изменению и настройке, точности перемещения, погрешности позиционирования угла, быстродействию, надежности, стойкости, габаритам.
В связи с применением числового программного управления, в станках каждое движение чаще всего осуществляется от своего отдельного источника – электрического или гидравлического двигателя, обладающего своими особенностями. Источник определяет область рационального применения привода.
По своим функциям и конструктивному исполнению, приводы разделяют:
1. Привод главного движения;
2. Привод подач и вспомогательных перемещений;
3. Привод вращательного и поступательного движений;
4. Привод ступенчатого и бесступенчатого регулирования;
5. Механические, гидравлические, электрические приводы.
Передача движения от двигателя на ведущий вал механизма осуществляется ременной или зубчатыми передачами, а также непосредственным соединением валов электродвигателя и механической передачи (встроенные электродвигатели). В механизмах изменения скоростей движения/включения/выключения/реверсирования передача движения происходит через ременные, зубчатые, цепные, винтовые и червячные передачи. В механизмах подачи – через шариковые винтовые пары или пары винт-гайка и безлюфтовые редукторы, электрические и гидромеханические связи.
Основной задачей при выборе параметров и характеристик привода является обеспечение технологических режимов обработки детали с допустимыми геометрическими погрешностями и шероховатостью поверхности при максимальной производительности и минимальной себестоимости обработки. Особенностью работы современных электроприводов главного движения в станках с числовым программным управлением является совмещение операций в технологических циклах обработки деталей, характерных как для механизмов главного движения, так и для механизмов подачи.
Кинематической цепью называется совокупность кинематических пар, связывающих источник движения с исполнительными органами или два исполнительных органа станка между собой. Кинематические пары располагаются в определенной последовательности.
Кинематической схемой называется условное изображение совокупности кинематических цепей станка в одной плоскости.
Стандартизованные условные обозначения элементов кинематических цепей представлены в Табл. 1:
Табл. 1 Стандартизованные условные обозначения элементов кинематических цепей
Обозначение | Наименование |
![]() | Вал |
Соединение двух валов | |
![]() | Глухое |
![]() | Глухое с предохранением от нагрузок |
![]() | Эластичное |
![]() | Шарнирное |
![]() | Телескопическое |
![]() | Плавающая муфта |
![]() | Зубчатая муфта |
Соединение деталей с валом | |
![]() | Свободное для вращения |
![]() | Подвижное без вращения |
![]() | При помощи вытяжной шпонки |
![]() | Глухое |
Подшипники скольжения | |
![]() | Радиальный |
![]() | Радиально-упорный односторонний |
![]() | Радиально-упорный двухсторонний |
![]() | Радиальный |
![]() ![]() | Радиально-упорный односторонний |
Муфты | |
![]() | Кулачковая односторонняя |
![]() | Кулачковая двухсторонняя |
![]() | Конусная |
![]() | Дисковая односторонняя |
![]() | Дисковая двухсторонняя |
![]() | Обгонная односторонняя |
![]() | Обгонная двухсторонняя |
Электродвигатели | |
![]() | На лапах |
![]() | Фланцевые |
![]() | Встроенные |
Ременная передача | |
![]() | С плоским ремнем |
![]() | С плоским ремнем перекрестная |
![]() | С клиновым ремнем |
![]() | Передача цепью |
Передачи зубчатые | |
![]() | Цилиндрическими колесами |
![]() | Коническими колесами |
![]() | Винтовые |
![]() | Червячная |
![]() | Зубчатая реечная |
Передача ходовым винтом и гайкой | |
![]() | Неразъемной |
![]() | Разъемной |
Концы шпинделей станков | |
![]() | Центровых |
![]() | Патронных |
![]() | Сверлильных |
![]() | Прутковых |
![]() | Расточных с планшайбой |
![]() | Фрезерных |
![]() | Шлифовальных |
Тормоза | |
![]() | Конусный |
![]() | Ленточный |
![]() | Колодочный |
![]() | Дисковый |
Дата добавления: 2018-04-15; просмотров: 578; Мы поможем в написании вашей работы! |
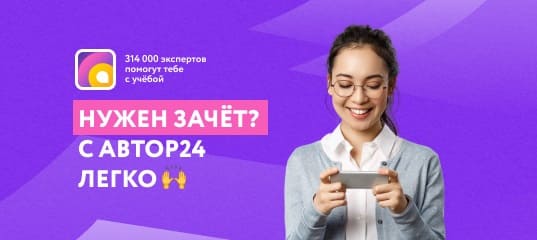
Мы поможем в написании ваших работ!