Система станок-приспособление-инструмент-заготовка (СПИЗ).
Основы теории резания.
Основные термины и определения.
При обработке металлов резанием, изделие получается в результате срезания с заготовки слоя припуска, который удаляется в виде стружки. Готовая деталь ограничивается вновь образованными поверхностями. На обрабатываемой заготовке в процессе резания различают обрабатываемую и обработанную поверхности. Кроме того, непосредственно в процессе резания, режущей кромкой инструмента образуется и временно существует поверхность резания (Рис. 1).
Рис. 1 Поверхности, возникающие в процессе обработки.
Для осуществления процесса резания необходимо и достаточно иметь одно взаимное перемещение детали и инструмента. Однако для обработки поверхности одного взаимного перемещения, как правило, недостаточно. В этом случае есть необходимость иметь два и более взаимосвязанных движений обрабатываемой детали и инструмента. Совокупность нескольких движений инструмента и обрабатываемой детали, обеспечивает получение поверхности требуемой формы. При этом, движение с наибольшей скоростью называют главным движением (DГ), а все остальные движения называются движениями подачи (DS). Суммарное движение режущего инструмента относительно заготовки, включающее главное движение и движение подачи, называется результирующим движением резания (De). Геометрическая сумма главного движения резания и скорости движения подачи определяет величину скорости результирующего движения резания (Ve). Плоскость, в которой расположены вектора скоростей главного движения резания и движения подачи, называется рабочей плоскостью (PS). В этой плоскости измеряются угол скорости резания η и угол подачи μ (Рис. 2). Для случаем токарной обработки, угол подачи μ = 90º.
|
|
Рис. 2 Рабочая плоскость при токарной обработке.
Параметры резания.
Интенсивность процесса резания определяется напряженностью режима резания. Режим резания характеризуют три параметра:
1. Глубина резания t (мм);
2. Подача S (мм/об);
3. Скорость резания V (м/мин).
Глубиной резания называется толщина слоя обрабатываемого материала, срезаемого за один проход инструмента.
Подачей называется величина перемещения инструмента или обрабатываемой детали в единицу времени или величина этого перемещения, отнесенная к величине главного движения.
Скоростью резания называется скорость перемещения поверхности резания относительно режущей кромки инструмента. Скорость резания можно представить как путь, пройденный режущим инструментом в единицу времени в направлении главного движения по поверхности резания.
Величины подачи и глубины резания определяют величину площади сечения срезаемого слоя (сечения среза):
|
|
(1)
Процесс пластической деформации срезаемого слоя и напряженность процесса резания наиболее полно оценивается не величиной площади поперечного сечения среза, а величинами ширины a и толщины b поперечного сечения срезаемого слоя (Рис. 3):
Рис. 3 Иллюстрация к формуле (1).
Толщиной срезаемого слоя a называют расстояние между двумя последовательными положениями поверхности резания. Шириной срезаемого слоя b называют расстояние между обрабатываемой и обработанной поверхностями, измеренное по поверхности резания.
Форма поперечного сечения среза зависит от формы режущей кромки инструмента и от расположения ее относительно направления движения подачи. При резании инструментом с прямолинейной режущей кромкой, толщина среза a постоянная на всей ширине среза, а при резании инструментом с криволинейной режущей кромкой толщина среза неодинакова в разных точках по ширине среза. Из Рис. 3 видно, что при постоянных значениях подачи S и глубины резания t, ширина среза b и толщина среза a изменяется в зависимости от положения режущей кромки, а также в зависимости от угла φ между режущей кромкой и направлением подачи.
|
|
Из Рис. 3 видно, что:
В результате того, что режущий инструмент имеет вспомогательный угол φ1 не равный нулю, фактическая площадь среза fфакт меньше номинальной на величину площади среза оставшихся на обработанной поверхности гребешков. Их величина Δf несоизмеримо мала по сравнению с номинальной f и для каких-либо расчетов ею можно пренебречь.
Производительность обработки резанием может характеризоваться объемом металла, срезаемого в единицу времени. Этот объем может быть определен как произведение площади поперечного сечения среза и длины пути, пройденного режущим инструментом в единицу времени:
(2)
Кроме того, производительность механической обработки может оцениваться также величиной площади поверхности, обработанной в единицу времени или по другим показателям.
От выбора режима резания зависит производительность труда, качество и стоимость изготовления деталей.
Рекомендации по выбору режимов резания:
1. Глубина резания: припуск на обработку можно в один или несколько проходов; выгоднее работать с возможно меньшим количеством проходов. Следует весь припуск снимать за один проход, если мощность и прочность станка, а также прочность инструмента и жесткость обрабатываемой детали допускают это. Если же припуск на обработку велик, а обработанная поверхность должна быть точной и чистой, следует припуск разделить на два прохода, оставляя на чистовую обработку минимальную его часть;
|
|
2. Подача: для получения наибольшей производительности следует работать с возможно большими подачами. Величина подачи при черновой обработке ограничивается жесткость детали, прочностью инструмента и слабых звеньев механизма подачи станка. Величина подачи при получистовой и чистовой обработке определяется требованиями чистоты поверхности и точности детали;
3. Скорость резания: скорость резания зависит главным образом от обрабатываемого материала, материала и стойкости инструмента, глубины резания, подачи и способа охлаждения.
Основные случаи резания.
Процесс пластической деформации срезаемого слоя и образования стружки, кроме указанных ранее параметров, может характеризовать степень усложненности условий, в которых совершается образование стружки. По этому признаку различают два случая резания: свободное и несвободное (усложненное).
1. Свободное резание (Рис. 4).
Происходит в случае, когда в резании участвует одна прямолинейная режущая кромка. Деформированное состояние срезаемого слоя при этом является плоским.
Рис. 4 Случай свободного резания.
В этом случае деформация совершается в плоскостях, параллельных друг другу и все элементарные объемы срезаемого слоя могут свободно перемещаться в параллельных направлениях.
Свободное резание может осуществляться также при строгании прямых гребешков на плоской поверхности призматической заготовки или при точении с поперечной подачей буртика на цилиндрической заготовке. Длина прямолинейной режущей кромки инструмента в обоих случаях должна быть больше ширины гребешков или буртика на ширину перекрытия режущего лезвия. Свободное резание обычно производится при выполнении каких-либо экспериментов в различных исследованиях. Это делается для того, чтобы исключить влияние усложненного деформирования срезаемого слоя на исследуемое явление.
2. Несвободное (усложненное) резание (Рис. 5).
Рис. 5 Случай несвободного резания.
Данный случай резания характеризуется тем, что отдельные объемы срезаемого слоя на разных участках режущей кромки перемещаются в разных направлениях, что создает условия сложного деформированного состояния и затруднят образование стружки.
При несвободном резании отдельные элементарные объемы срезаемого слоя перемещаются в разных направлениях и, поэтому в разных точках зоны резания одни и те же явления протекают по-разному, с разной степенью интенсивности. Картина состояния материала в зоне резания в одной секущей плоскости не является типичной для всех других секущих плоскостей и не повторяет картины состояния материала в других секущих плоскостях.
По расположению режущей кромки лезвия относительно направления главного движения (вектора скорости резания), резание может быть прямоугольным или косоугольным. При расположении режущей кромки под прямым углом к направлению главного движения, процесс резания называется прямоугольным. Если же режущая кромка расположена к направлению резания не под прямым углом – процесс резания называют косоугольным. При прямоугольном резании, стружка завивается в плоскую логарифмическую спираль, а при косоугольном – в винтовую, направление и шаг которой зависят от расположения режущей кромки.
Резание может осуществляться режущими инструментами с одним лезвием или с несколькими лезвиями. Согласно этому, резание может называться однолезвийным или многолезвийным. Также резание может быть непрерывным (при точении), или прерывистым (при фрезеровании) и происходить с постоянным или переменным сечением среза.
Система станок-приспособление-инструмент-заготовка (СПИЗ).
Станок |
Приспособление |
Инструмент |
Заготовка |
Рис. 6 Система СПИЗ.
В процессе резания могут возникать смещения, зазоры в подшипниках, люфты в механизмах зажима заготовки, что приводит к искривлению обрабатываемых поверхностей.
Жесткостью j технологической системы называется способность системы оказывать сопротивление действию деформирующих ее сил. При нахождении жесткости системы по значениям жесткости отдельных ее звеньев, удобно пользоваться понятием податливости.
Податливостью ω технологической системы называется способность этой системы упруго деформироваться под действием внешних сил.
(3)
(4)
(5), где
Y – суммарное смещение системы СПИЗ;
PY – радиальная составляющая силы резания;
yС - смещение узлов станка;
yП - смещение узлов приспособления;
yИ – смещение узлов инструмента;
yЗ - смещение заготовки.
Дата добавления: 2018-04-15; просмотров: 1207; Мы поможем в написании вашей работы! |
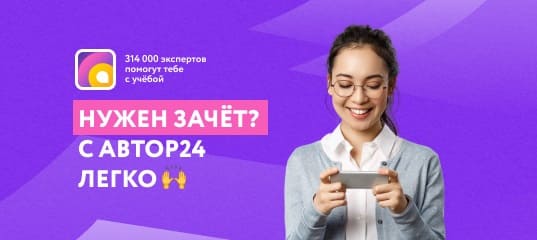
Мы поможем в написании ваших работ!