Классификация металлорежущих инструментов.
Одним из основных классификационных критериев является особенность конструкции режущего инструмента. По нему выделяют такие виды как:
1. Резцы: инструмент однолезвийного типа, позволяющий выполнять металлообработку с возможностью разнонаправленного движения подачи;
2. Фрезы: инструмент, при использовании которого, обработка выполняется вращательным движением с траекторией, имеющей неизменный радиус и движением подачи, которое по направлению не совпадает с осью вращения;
3. Сверла: режущий инструмент осевого типа, который используется для создания отверстий в материале или увеличения диаметра уже имеющихся отверстий. Обработка сверлами осуществляется движением подачи, направление которого совпадает с осью вращения;
4. Зенкеры: инструмент осевого типа, с помощью которого корректируются размеры и форма имеющихся отверстий, а также увеличивается их диаметр;
5. Развертки: осевой инструмент, который применяется для чистовой обработки стенок отверстий (уменьшения их шероховатости);
6. Цековки: осевой инструмент, использующийся для обработки торцовых и цилиндрических участков отверстий;
7. Плашки: используются для нарезания наружной резьбы на заготовках;
8. Метчики: используются для нарезания резьбы в отверстиях;
9. Ножовочные полотна: инструмент многолезвийного типа, имеющий форму металлической полосы с множеством зубьев. Ножовочные полотна используются для отрезки части заготовок или создания в ней пазов, при этом главное движение резания является поступательным;
|
|
10. Долбяки: применяются для зуботочения или зубодолбления шлицев валов, зубчатых колес и других деталей;
11. Шеверы: инструмент, предназначенный для чистовой обработки зубчатых колес методом «скобления»;
12. Абразивный инструмент: бруски, круги, кристаллы, крупные зерна или порошок абразивного материала. Инструмент, входящий в данную группу, применяется для чистовой обработки различных деталей.
Следующим классификационным критерием является вид поверхности, обработка которой осуществляется с помощью металлорежущего инструмента. По нему выделяют следующие инструменты:
1. Инструменты, применяемые для обработки тел вращения, наружных фасонных, а также плоских поверхностей; в данную группу включаются описанные выше резцы, фрезы, абразивные круги и прочие инструменты;
2. Инструменты, применяемые для обработки отверстий: зенкеры, сверла, расточные резцы, протяжки и другие;
3. Инструменты, применяемые для нарезания резьбы: плашки, метчики, накатные ролики и прочие инструменты;
4. Инструменты, применяемые для обработки поверхностей звездочек, шлицевых валов, зубьев колес. Эти операции выполняются с помощью пальцевых, дисковых фрез, обратных резцов, долбяков, шлифовальных кругов, шеверов, протяжек, зубострогальных резцов, конических фрез червячного типа, зубострогальных головок.
|
|
Еще одним критерием классификации металлорежущего инструмента является принцип взаимодействия с обрабатываемым материалом. По нему выделяют такие инструменты как:
1. Обычные;
2. Ротационные, круговое лезвие которых непрерывно обновляется;
Кроме того, существует такой классификационный критерий как тип изготовления инструмента, согласно которому выделяют:
1. Цельный режущий инструмент;
2. Составной инструмент, конструкция которого представляет собой неразъемное соединение нескольких элементов;
3. Сборный инструмент, отличающийся разъемным характером соединения элементов, которые его образуют.
Также классифицируют инструменты по способы соединения со станком:
1. Насадной инструмент;
2. Хвостовой инструмент;
3. Призматический инструмент.
Также существует классификация по способу применения:
1. Ручной инструмент;
2. Машинный инструмент;
3. Машинно-ручной инструмент.
Понятие о металлорежущих станках.
Металлорежущие станки являются основным видом промышленного оборудования для размерной обработки заготовок. Вследствие быстрого развития вычислительной техники, за последние 30 лет конструкции станков существенно изменились.
|
|
Металлорежущий станок – технологическая машина, которая предназначена для обработки металлических заготовок посредствам снятия материала механическим способом (резанием), в результате чего обеспечивается заданная форма и размеры заготовки.
Процесс обработки на станках осуществляется с помощью движений формообразования, в которых участвуют инструмент и заготовка. Движения в процессе резания образуют на заготовке поверхности.
В основном, процесс обработки производится с помощью режущего инструмента (лезвийного или абразивного). Однако существуют особые методы обработки, такие как: электрохимические, электрофизические, поверхностно пластическое деформирование, оптические лазерно-лучевые, а также операции по измерению или контролю обрабатываемых деталей, а также сборки.
Заготовка – предмет труда, из которого, путем изменения размеров, формы и свойств поверхности, изготавливают деталь.
Деталь – продукт труда (изделие), который предназначен для использования на предприятии в основном или вспомогательном производстве.
|
|
Основные узлы станков.
Все станки состоят из трех основных механизмов – двигательного (электродвигатель), передаточного и исполнительного.
Передаточный механизм – совокупность устройств, служащих для передачи движения от двигателя к исполнительному органу – столу, суппорту с режущим инструментом, у шпинделю и так далее.
Станочное оборудование имеет ряд узлов и деталей, которые предназначены для выполнения аналогичных для всех классов оборудования, хотя они и отличаются по конструктивному исполнению.
К таким деталям и узлам станка можно отнести:
· станину – корпусная часть станка, на которой закрепляются остальные детали и узлы станка; станина изготавливается литьем из чугуна или сваркой из стальных профилей или листов;
· стол – часть станка, служащая для установки заготовок;
· суппорт – узел для закрепления заготовки или инструмента и передачи им движения;
· шпиндель – вал, на котором закрепляется в патроне инструмент или заготовка.
Классификация станков.
Основная классификация, которая предложена Экспериментальным научно-исследовательским институтом металлорежущих станков (ЭНИМС), является цифровой и предлагает разделение станков на девять групп по технологическому признаку (по виду обработки и применяемому металлорежущему инструменту). Каждую группу подразделяют на типы (подгруппы), а каждый тип – на типоразмеры.
Группы станков определяют по технологическому назначению станка (токарные, фрезерные, шлифовальные и так далее), типы станков – по числу основных рабочих органов (многошпиндельные, одношпиндельные), по степени автоматизации (автоматы, полуавтоматы и так далее).
Классификация:
Группа 1: Токарные
Типы станков:
0 – специализированные автоматы и полуавтоматы;
1 – одношпиндельные автоматы и полуавтоматы;
2 – многошпиндельные автоматы и полуавтоматы;
3 – токарно-револьверные;
4 – сверлильно-отрезные;
5 – карусельные;
6 – токарно-винторезные; лобовые;
7 – многорезцовые; копировальные;
8 – специализированные;
9 – разные.
Дата добавления: 2018-04-15; просмотров: 3031; Мы поможем в написании вашей работы! |
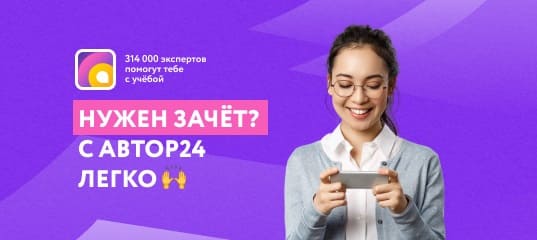
Мы поможем в написании ваших работ!