Описание технологической схемы производства
Технологическая схема разрабатываемого производства представлена на рисунке 1.
Процесс изготовления зарядов СГС также будет состоять из 5 стадий:
Технологический процесс изготовления состава «СГС» на данном производстве включает в себя следующие стадии:
6) Взвешивание компонентов
7) Смешение компонентов
8) Вальцевание состава
9) Прессование зарядов
10) Резка, разбраковка, упаковка зарядов.
Подготовка материалов.
Перхлорат калия транспортируется со склада окислителей, вскрывается тара, разравнивается нитрат калия на противне, после чего отправляется на сушку в сушильный шкаф. Затем нитрат калия измельчают на дисмембраторе. Затем взвешивают на весах.
Термоэластопласт, фторопласт, агидол, краситель, вазелиновое масло транспортируются со склада химреактивов,взвешивание также осуществляется на рабочем столе под зонтом вентиляции.
Этилацетат транспортируют со склада ЛВЖ, приготавливают навеску.
Смешение
Смешение производится в смесителе ЗЛ-63-01-13К. Подготавливается оборудование, затем поочередно загружают в камеру смешения следующие навески:
1) раствор каучука и АБС в этилацетате,
3) "Агидол-2",
4) фторопласт-4 (4Д).
Управление процессом смешения ведут дистанционно, с пульта управления.
Нагревают содержимое смесителя. После выдержки 15 минут загружают половину расчетного количества перхлората калия и перемешивают 15 минут. Загружают оставшееся количество перхлората калия, а также краситель, перемешивают 20-40 минут. Далее следует выгрузка состава из смесителя.
|
|
Вальцевание состава.
Процесс вальцевания осуществляется на горизонтальных вальцах "DEMAG" в присутствии обслуживающего персонала. Подготовка вальцов. Проводится 4-5 прокаток до формирования массы в полотно. Затем проводят еще 10-15 прокаток.После последней прокатки лист, не складывая, помещают на рабочий стол и производят раскрой полотна с помощью острого ножа-шаблона. Полотно должно быть горячим.Далее полотно подвергают рулонированию путем плотного скатывания, готовые рулоны снабжаются ярлыками и передаются на прессование.
Прессование зарядов.
Прессование проводят на прессах Р-50 или УММ-50. Подготовка оборудования к работе. Рулоны укладываются в температурный шкаф для разогрева до температуры прессования.Устанавливают сверху пуанссон,ограничитель, выходят из кабины. Далее процесс прессования проводится дистанционно с наблюдением с пульта управления. Прессование проводится под давлением не более 350кгс/см2. Полученный цилиндр отправляют на следующую стадию.
Резка, разбраковка, упаковка зарядов.
|
|
Осуществляется вручную в кабине. Проверяют на отсуствие дефектов визуально. Используя мерительный инструмент или шаблон, производят скальпелем разрезку бездефектных участков заготовки в изделие. Упаковывают и маркируют.
Технологическая часть.
Необходимо спроектировать промышленную установку по производству ЗЭТ производительностью 73т/г(7300 изделий/год). В основу положена разработанная схема производства СГС на предприятии ФГУП «СКТБ «Технолог», изложенная ранее.
Необходимо: выбрать технологическое оборудование, провести технологические расчеты; разработать чертежи технологической и строительно-монтажной схемы объекта.
Описание технологической схемы производства.
Технологическая схема разрабатываемого производства представлена на рисунке 1.
Процесс изготовления зарядов также будет состоять из 5 стадий:
Рисунок 1. Технологическая схема производства.
Подготовка компонентов.
Подготовка компонентов проводится в помещении 1. Калий азотнокислый, фторопласт-4(4Д), краситель и «Агидол-2» вручную загружаются в бункеры для сыпучих компонентов (Б1-4). Соответственно, из бункеров сыпучие вещества перемещаются вниз самотеком в бункеры-сушилки и дегидратор (БС8-10;ДГ7). Было предложено заменить сушильные шкафы на бункеры-сушилки. При сушке в бункере, в отличие от сушки в сушильном шкафу, уже высушенная часть материала из нижней части бункера может ссыпаться сразу в загрузочное отверстие дисмембратора. Для перхлората калия необходим мягкий режим сушки, с температурой воздуха не больше 40C, для этой цели вместо сушилки был выбран дегидратор.
|
|
Дисмембраторы (ДМ11-14) располагаются на полу помещения 1. В них происходит измельчение сыпучих компонентов. Измельченные компоненты из дисмембраторов направляются в кабину 2 сжатым воздухом, попадая в бункеры-дозаторы (БД15-18), где навески будут находиться до следующей стадии процесса.
В помещении 1 также готовится раствор каучука и АБС в этилацетате. Из бункеров (Б5,Б6) и мерника (М20) происходит заполнение смесителя (СМ15), который оснащен перемешивающим устройством. Каучук, АБС и этилацетат смешиваются, а для дальнейшего растворения смесь направляют в лопастной смеситель (СЛ 22) в кабине 2.
Смешение компонентов.
Смешение компонентов происходит в лопастном смесителе типа ЗШ-200 в кабине 2. Предварительно наполненные бункеры-дозаторы (БД15-18) находятся выше по уровню, над смесителем. Смешение производится дистанционно. В камеру смешения подаются компоненты в порядке:
|
|
1) раствор каучука и АБС этил ацетате
2) антиоксидант «Агидол-2»
3) фторопласт-4(4Д).
Смешение ведется при температурном режиме . Дают выдержку 10-20 минут, после чего загружают по половине расчетного количествакалия хлорнокислого и снова перемешивают в течение 10-15 минут. По окончании второй выдержки производят загрузку в смеситель оставшихся перхлората калия, красителя, после чего перемешивают 20-40 минут. Контроль качества смешения производится визуально. Масса должна быть однородной по цветности – черного цвета цвета, без наличия комочков наполнителей (перхлорат калия).
Смешение занимает . После окончания смешения производят выгрузку состава «СГС» с помощью выгружного шнека. Состав выдавливается шнеком непосредственно на ленточный транспортер (ЛТ22), который направляет массу в кабину 3 на стадию вальцевания.
Вальцевание.
Процесс вальцевания осуществляется на горизонтальных смесительно-подогревательных вальцах Demag (Вал24) в кабине 3. Поверхность валков гладкая. Вальцевание проводится в присутствии обсуживающего персонала.
Диаметр валков 400мм, длина 1000мм, вальцы гладкие.
Температура рабочего валка должна быть , холостого
.
Операция особо опасная.
Устанавливают зазор между валками , проводят сначала 4-5 прокаток для формирования массы в полотно, затем 10-15 прокаток. Процесс вальцевания считают законченным при получении равномерно сформированного полотна.
Полученный после последней прокатки лист помещают на рабочий стол с винилопластовым покрытием (СТ26), производят раскрой полотна с помощью острого шаблонного ножа. Разрезается только разогретое полотно. Одновременно с раскроем полотна производят удаление его дефектных участков, а также обрезание неровных краев. После раскроя полотно подвергают рулонированию , для предохранения от раскрутки рулон перевязывают киперной лентой.
Рулоны полуфабриката направляются в кабину 4 для стадии прессования посредством ленточного транспортера (ЛТ24).
Отходы вальцевания (остатки полотна после раскроя) помещают на приемный поддон, разогревают до температуры вальцевания и вводят в зазор между валками при вальцевании очередной порции состава «СГС».
Прессование.
Процесс прессования проводится в кабине
Наибольшая номинальная нагрузка, кН – 500
Рулоны помещают в темперационный шкаф для прогревания, после чего покидают кабину. По окончании времени разогрева входят в кабину и устанавливают разогретый рулон в матрицу пресс-инструмента, далее процесс ведут дистанционно. Давление должно возрастать плавно. Удельное давление прессования не должно превышать 600 кгс/см2, при этом сдвиговое усилие не должно превышать 700кг/см2.
Входят в кабину. Латунным ножом срезают выпрессованный цилиндр подают его на рабочий стол, режут на технологическую длину (0,5+0,05) м в заготовки изделий и раскладывают на ровной поверхности стола для остывания. В матрицу устанавливают следующий разогретый рулон полуфабриката и проводят очередное прессование.
По окончании прессования партии изделий входят в кабину, изделия перекладывают в ящик и переносят в кабину 5 на следующую стадию процесса.
Дата добавления: 2018-04-05; просмотров: 728; Мы поможем в написании вашей работы! |
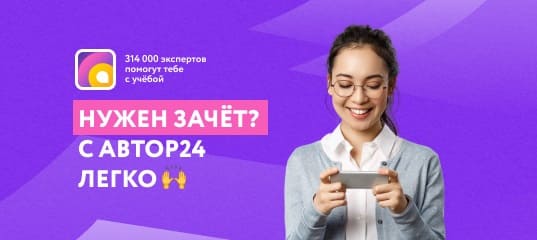
Мы поможем в написании ваших работ!