Технологическая схема существующего производства
Содержание
Введение. 3
1. Аналитический обзор. 4
1.1.Характеристика основных компонентов. 7
1.2.Технологическая схема существующего производства. 8
1.2.1.Подготовка материалов. 9
1.2.2.Смешение компонентов. 10
1.2.3.Вальцевание состава. 10
1.2.4.Прессование зарядов. 11
1.2.5.Резка, разбраковка, упаковка зарядов. 11
2.Технологическая часть. 12
2.1.Описание технологической схемы производства. 12
2.1.1.Подготовка компонентов. 13
2.1.2.Смешение компонентов. 14
2.1.3.Вальцевание. 15
2.1.4.Прессование. 16
2.1.5.Резка, разбраковка, упаковка, маркировка зарядов . 18
2.2.Иженерные расчеты.. 19
2.2.1.Материальные расчеты. 19
2.3.Технологические расчеты.. 27
2.3.1.Расчет оборудования. 27
Расчет смесителя ЗШ-200. 27
2.3.1.1.Тепловой расчет смесителя. 30
3.Строительная часть. 34
Выводы.. 36
Список литературы.. 37
Введение
В данном курсовом проекте рассматривается технология изготовления зарядов «СГС».
Конкурентом СГС являются баллиститные пороха, но при температуре более 80° С они начинают плавится. Кроме того при запуске они могут сдетонировать, а не гореть. Поэтому баллиститные пороха можно использовать только в неглубоких, не горячих скважинах. Состав СГС, в отличие от баллиститных порохов, лишён всех этих недостатков, что объясняет причину популярности состава СГС.
Целью курсового проекта является объединение специальных знаний для проектирования производства взрывчатых веществ, в свою очередь, ставятся определенные задачи: усовершенствовать технологическую схему процесса; заменить оборудование так, чтобы уменьшить ручной труд на стадиях процесса; привести нужные расчеты оборудования, чтобы подтвердить правильность его выбора; спроектировать монтажную схему цеха.
|
|
Аналитический обзор
СГС (Состав газогенерирующий скважинный) — предназаначен для создания избыточного давления в скважинах, пробуренных на нефть и газ, с целью разрыва пласта и повышения производительности скважин. А также изготовления зарядов для скважинных генераторов.
Технологический процесс производства зарядов “СГС” состоит из следующих основных стадий:
1) изготовление эластичного взрывчатого состава СГС.
2) вальцевание СГС;
3) прессование зарядов СГС;
4) резка и разбраковка зарядов СГС;
5) маркировка и упаковка готовой продукции.
ЭЭВ представляет собой однородную массу черного цвета, не содержащую посторонних включений.
Компонентный состав "СГС":
Массовая доля наполнителей (суммарно), %
Фторопласт-4(4Д) 1,38
Антиоксидант «Агидол 2» 0.47
Калий хлорнокислый (перхлорат калия) 71,43
|
|
Массовая доля связующих (суммарно), %
Углерод технический(сажа) 0.13
Каучук бутадиеннитрильный 9,15
Сополимеры акрилонитрилбутадиенстирольные 9,16
Этилацетат 8,31
Чувствительность к механическим воздействиям и взрывчатые характеристики ЭВВ "СГС":
Чувствительность к удару по ГОСТ 4545-88:
частость взрывов в приборе 1 - 48%
Чувствительность к трению по ГОСТ Р 50835-95 на приборе К-44-3 (при ударном сдвиге):
нижний предел: 217 МПа
Температура вспышки по ОСТ В 84-1582-78 (60 секунд) 280оС Тротиловый эквивалент 1,15
Токсичность состава в процессе приготовления определяется перхлоратом калия. Готового состава-этилацетатом.
Готовая продукция - эластичный трубчатый заряд - представляет собой цилиндр черного цвета со сквозными внутренними каналами.
Удельный объём газообразных продуктов горения составляет 700 л/кг для обеспечения в скважине избыточного давления. Закон скорости горения в интервале от 0 до 1000 атм.:
|
|
U = 5, 87 * p0,415
Плотность состава ~ 1,7 — 1,8 г/см3
Состав СГС может использоваться в большом количестве изделий, таких как: пороховые генераторы давления(ПГД), заряды скважинные твердотопливные (ЗПГК), заряды теплогазогенераторные (ЗТГГ).
Характеристика основных компонентов.
Таблица 1 – перечень основных материалов.
Наименование материала | Обозначение нормативного документа |
1. Калий хлорнокислый(перхлорат калия) | ТУ 6-09-3801-76 ТУ 2147-471-05121441-2008 |
2. Сополимеры акрилонитрилбутадиенстирольные | ТУ 2214-019-00203521-96 |
3. Каучук бутадиеннитрильный ЮНКС-18АМН 1/”Цитропласт-18М” | ТУ 38.30313-2006/ ТУ 38.40350 |
4. Антиоксидант «Агидол-2» любой марки | ТУ 38.101617-80 |
5. Фторопласт марки 4(4Д) | ГОСТ 10007-80 |
6. Углерод технический для производства резины | ГОСТ 7885-76 |
7. Этиловый эфир уксусной кислоты (далее по тексту – этилацетат) технический любого сорта. | ГОСТ 8981-78 |
· Калий хлорнокислый ТУ 6-09-3801-76, ТУ 2147-471-05121441-2008
Калий хлорнокислый представляет собой твердое кристаллическое вещество белого цвета. Плотность 2524 кг/м3. Температура плавления 610 оС. Термическое разложение начинается при температуре 400 оС, температур интенсивного разложения 525 оС. Мало растворим в воде (1,80 г в 100 г при 20 оС), не растворим в этаноле. При взаимодействии ультрафиолетовых лучей разлагается на хлористый калий и кислород.
|
|
Является окислителем, способствует самовозгоранию горючих веществ. Сам по себе калий хлорнокислый не взрывоопасен, но в смеси с горючими веществами способен давать взрывоопасные высокочувствительные смеси.
· Сополимеры акрилонитрилбутадиенстирольные ТУ 2214-019-00203521-96.
Сополимеры акрилонитриллбутадиенстирольные АБС представляют собой продукт сополимеризации акрилонитрила бутадиена и стирола(альфаметилстирола) в виде гранул от 2 до 5 мм. Плотность
1020-1060 кг/м3. Водопоглощения за 24 часа (по ГОСТ4650-80) – 0-0,20 %
В виде гранул АБС не взрывоопасны, загораются при контакте с огнем. Температура самовоспламенения 395-450 оС, температура воспламенения 285-370оС. По ГОСТ 12.1.044-89 – горючее вещество.
· Каучук бутадиеннитрильный ТУ38.30313-2006.
Каучук бутадиеннитрильный представляет собой представляет собой бутадиена и акрилонитрила, резиноподобное вещество (поступает в виде блока). Плотность 950 кг/м3. Растворим в кетонах и этилацетате.
Токсичные свойства каучука определяются токсичностью остаточного количества бутадиена и акрилонитрила.
· Каучук бутадиеннитрильный ТУ38.30313-2006.
Каучук бутадиеннитрильный представляет собой представляет собой бутадиена и акрилонитрила, резиноподобное вещество (поступает в виде блока). Плотность 950 кг/м3. Растворим в кетонах и этилацетате.
Токсичные свойства каучука определяются токсичностью остаточного количества бутадиена и акрилонитрила.
· Антиоксидант "Агидол-2".
Антиоксидант "Агидол-2" является продуктом конденсации ортотретбутилпара-крезола с формальдегидом и применяется для стабилизации резин и каучуков. Антиоксидант "Агидол-2" представляет собой мелкий порошок белого цвета с температурой плавления 126-128 оС. Пожароопасен. Нижний концентрационный предел распространения пламени 10 г/м3. Для тушения "Агидола-2" применяют огнетушитель, песок.
· Фторопласт-4 ГОСТ 10007-80, фторопласт-4Д ГОСТ 14906-77
Фторопласт представляет собой мелкий однородный порошок белого цвета, без посторонних включений. При температуре до плюс 250 оС невзрывоопасен, не горюч.
· Этилацетат ГОСТ 8981-78
Этилацетат представляет собой легковоспламеняющуюся бесцветную жидкость с резким запахом. Плотность 1082 кг/м3; температура кипения 139,6 оС. Температура вспышки 40 оС; температура самовоспламенения 360 оС. Концентрационные пределы воспламенения паров в воздухе, % (об.): нижний 1,21, верхний 9,9.
Технологическая схема существующего производства.
За основу взято существующее производство ФГУП «СКТБ «Технолог».
Технологический процесс изготовления состава «СГС» на данном производстве включает в себя следующие стадии:
1) Взвешивание компонентов
2) Смешение компонентов
3) Вальцевание состава
4) Прессование зарядов
5) Разбраковка и упаковка зарядов.
Дата добавления: 2018-04-05; просмотров: 366; Мы поможем в написании вашей работы! |
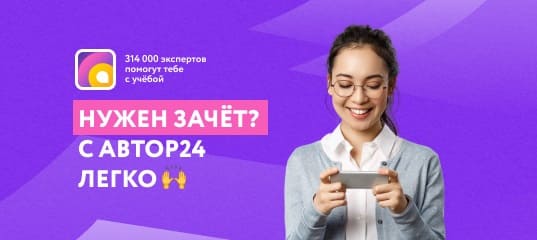
Мы поможем в написании ваших работ!