Figure 5.3Systemdrawingsideview
Figure 5.4System drawing bottom view
Figure 5.5System drawing top view
Assembly and programming
First of all, it was necessary to choose a fan whose rotation speed could be controlled. It was planned to use a cooler for a computer, but it has a big step in changing the speed of rotation. When choosing the motor, the following characteristics were taken into account:
1. Motor, with a smooth change in the speed of rotation;
2. Engine power;
3. The presence of the body, for ease of connection with the pipe.
The most optimal option was the brushless motor, in a special case called the impeller, it is shown in the figure below (used parts and their characteristics) and is used in aircraft modeling.
The essence of brushless motor control is quite simple: it consists of several copper coils, which are supplied with current at certain moments, which makes it possible to regulate the speed of rotation. This motor at maximum power can lift a weight of about 500 grams.
Further for a specific motor it was necessary to choose a speed regulator that would be compatible with the motor. Based on the characteristics of the engine, the speed controller shown in the figure below (used parts and their characteristics) was selected.
For power from the network, it was necessary to supply power (used parts and their characteristics)
Then it was necessary to determine the type of sensor that could fix the position of the ball in the pipe and transmit the information to the control platform. The following types of sensors were considered:
1. Ultrasonic sensors;
2. Laser sensors;
3. Photosensitive sensors.
The first type of sensor, although it transmits a digital signal, it did not fit due to limitations. Since the impeller rotation creates very strong sound interference and the sensor does not transmit information. Another complication associated with this type of sensor was static: between the body, which it must "track" and the sensor should not be any interference.
The second type of sensor, although it is optimal in this situation, but its cost is quite high.
At the heart of the third type of sensor are photoresistors, whose resistance varies depending on the illumination. LM 393 is an analog comparator that compares the analog signal received from the photoresistor with a predetermined threshold voltage and from here the digital signal 0 or 1 is obtained.
First of all, the sensors had to be calibrated, that is, to set such a sensitivity threshold so that external light sources do not interfere and the sensors do not work for any external influences. For this, a trimmer resistor is used on the sensor board.
|
|
It was necessary to pair sensors to accurately determine the position of the ball in the pipe, and also to specify the range of oscillations, since the oscillations of the ball are insignificant, but will.
The principle of the sensors consisted in the following: light-sensitive elements of the sensors were fed with signals in the form of laser beams and when the ball crossed their digital signal was transmitted to arduino and the increase in the speed of revolutions ceased.
Two laser pointers were used as sources of "light". At the same time, the frequency of reading the signals is 5 milliseconds, that is, after a given time, the sensor reads the signal and, depending on the results, the rotation speed changes.
Figure 6. Sensor operation (1)
Figure7.Sensor operation (2)
The sensors are connected and installed on a rigid C-shaped structure for immovability and ease of movement. The structure was assembled from plates, which are used for the production of plate-foamed fiberglass. As a rule, it is a textolite plate, which is covered with a layer of copper foil. This material is widely used for the manufacture of boards.
This material can be easily processed and at the same time has rigidity. As a fastener, fast-curing epoxy adhesive was used.
Figure 8. Assembly of mounting for sensors (1)
Figure 9. Assembly of mounting for sensors (2)
Figure 10. Assembly of mounting for sensors (3)
The pipe was selected based on the diameter of the impeller, for greater tightness. The cheapest option was a pipe for packing New Year's balls.
Based on the parameters of the pipe and the characteristics of the motor, a ball was selected. The main criteria for selecting a ball:
1. The mass of the ball;
2. The diameter;
3. Surface smoothness.
The mass of the ball should be taken into account in conjunction with the diameter of the ball, because the closer the diameter of the ball to the diameter of the tube, the less power is needed to push and hold at a certain height. A consideration of the flatness of the surface is necessary in order to predict the oscillations of the ball from side to side because of the turbulence of air streams during flow around the ball.
|
|
As a regulator, the Arduino Uno was used.
Description of the assembly process:
• Connect the impeller to the regulator;
• connect the regulator to 12 volts. from the power supply unit;
• nourish Arduino from the 5th century. from the regulator and connect the control output of the regulator to the arduino;
• fix sensors and lasers on a rigid structure, calibrate, supply them from the output of 3.3 V. with arduino;
• learn how to control the brushless motor controller;
• write an algorithm that determines the position of the ball according to the sensor data;
• Select the values of the width of the pulse applied to the regulator for climbing, hovering and lowering the altitude.
The peculiarity of the system is that it is impossible to connect the power from the computer and the battery at the same time, this leads to the fact that the protective element in the regulator of the brushless motor burns out.
The program code is presented in Appendix 2
Figure 11. Programmed controller
Дата добавления: 2018-02-28; просмотров: 187; Мы поможем в написании вашей работы! |
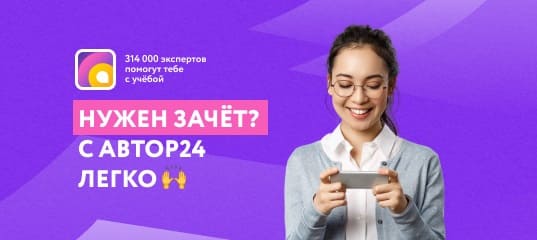
Мы поможем в написании ваших работ!