Систематические погрешности обработки.
Систематическая погрешность – это погрешность, которая для всех деталей рассматриваемой партий остается постоянной или закономерно изменяется при переходе от одной обрабатываемой детали к другой.
Причины возникновения постоянных систематических и переменных систематических погрешностей:
1. Неточность, износ, деформация станков, приспособлений и инструментов.
2. Деформация обрабатываемой детали.
3. Тепловое явление, происходящее в технической системе.
Погрешности вследствие неточности, износа и деформации станков.
Износ станков обуславливает увеличение систематических погрешностей обрабатываемых заготовок, что связано с тем, что износ рабочих поверхностей станка происходит неравномерно, т.е. происходит изменение взаиморасположения отдельных узлов станка, которое вызывает дополнительные погрешности.
Неравномерный износ направляющих приводит к перекосу суппорта и к увеличению диаметра обрабатываемой детали. А неравномерность износа направляющих по длине приводит к появлению систематических погрешностей формы обрабатываемой детали.
Деформация станков при их неправильном монтаже, а также под действием массы при оседании фундамента вызывают искривление направляющих и станин, вызывает дополнительные систематические погрешности обработки детали.
Погрешности, связанные с неточностью и износом режущего инструмента.
Неточность режущего инструмента непосредственно переносится на обрабатываемые детали, вызывая появление систематических погрешностей формы и размеров обрабатываемых поверхностей, но значительно большее влияние на точность обработки оказывают погрешности режущего инструмента, связанные с его износом, которая приводит к появлению систематической переменной погрешности обработки.
|
|
Размерный износ инструмента подчиняется линейному закону. Первый период: непродолжительный начальный износ характеризуется повышенным размерным износом. В этот период происходит приработка инструмента, иногда возможно выкрашивание отдельных неровностей. Начальный износ, его продолжительность зависят от материалов инструментов и обрабатываемой детали, качества заточки и режимов резания. Второй период износа характеризуется нормальным износом, прямопропорциональным пути резания. Интенсивность этого периода оценивается относительным износом, который определяется по формуле: Uотн = U/L. Третий период износа соответствует наиболее интенсивному катастрофическому износу,который сопровождается значительным выкрашиванием и поломками инструмента. Т.к. износ инструмента обратно пропорционален подачи, то увеличение подачи повышает общую размерную стойкость и точность обработки. Заметное влияние на относительный износ оказывает задний угол. С его увеличением растет износ. Точность обработки может быть повышена рациональной конструкцией, материалом режущего инструмента и подбором режимов резания.
|
|
Погрешности обработки, вызванные закрепление детали.
Усилия закрепления в приспособлениях и усилия резания, вызывают деформацию детали, порождающую погрешности формы обрабатываемых деталей.
При закреплении втулки в патроне происходит её упругая деформация в местах прилегания кулачков и погрешность формы обрабатываемой детали, связанная с упругой деформацией, зависит от числа кулачков, при увеличении числа зажимных кулачков погрешность геометрической формы втулки заметно уменьшается, от конструкций кулачков и площади контакта и соответствий формы детали и формы кулачков. При наиболее полном прилегании поверхностей кулачков к поверхности заготовки погрешность геометрической формы втулки также снижается.
В определённых условиях существенными причинами возникновения погрешностей обработки могут быть силы тяжести, центробежные силы и остаточные напряжения в заготовке. При одностороннем снятии припуска или снятии неравномерного припуска в обрабатываемой заготовке происходит перераспределение внутренних напряжений, образовавшихся в исходных заготовках при их литье, штамповке и т.д. Упругие деформации заготовок, вызываемые действием перечисленных сил, служат источником возникновения систематических погрешностей геометрической формы деталей.
|
|
Погрешности обусловленные температурными деформациями технологической системы.
Она вызывается следующими причинами:
1. нагрев теплом, выделяющимся в зоне резания;
2. нагрев теплом, выделяющимся при трений движущихся частей технологической системы;
3. непостоянство температуры помещения.
Температурная деформация станков:
Основными причинами нагревания станков и их отдельных частей являются потери на трение в подвижных механизмах станков, встроенных приводов и электроустановок, а также теплопередачи охлаждающей жидкости и нагрева от внешних источников. Особое влияние на точность обработки оказывает нагревание шпиндельных бабок. Наибольшая температура нагрева наблюдается в местах расположения подшипников шпинделя и быстроходных валов.
|
|
Продолжительность нагрева передней бабки, сопровождается смещением шпинделя и стабилизируется после 3-5 часов непрерывной работы. При остановке станка происходит его медленное охлаждение и обратное перемещение шпинделя.
Тепловые деформации инструмента.
Некоторая часть теплоты, выделяющейся в зоне резания, переходит в режущий инструмент, вызывая его нагревание и изменение размеров. При повышении скорости резания, глубины резания и подачи нагревание увеличивается, а следовательно, увеличивается удлинение резца. Удлинение резца приблизительно обратно пропорционально площади поперечного сечения его стержня. С увеличением толщины пластинки твердого сплава удлинение резца уменьшается и оно прямопропорционально твердости обрабатываемого материала. Первый период работы до наступления теплового равновесия удлинения резца сопровождается непрерывным изменением размеров или формы поверхности обрабатываемой детали. При обработке детали с перерывами машинного времени в момент прекращения резания начинается охлаждение резца и его укорочения, которое продолжается до начала следующего периода резания. При прерывистой механической обработке нагрев инструмента оказывает меньшее влияние на точность обработки.
Температурные деформации деталей.
Некоторая часть теплоты, выделяющаяся в зоне резания, переходит в обрабатываемую деталь. Нагрев обрабатываемых деталей зависит от режимов резания: с увеличением скорости и подачи температура детали понижается; увеличение глубины резания повышает температуру обрабатываемой детали.
Расчет погрешности обработки усложняется тем, что температура обрабатываемой детали неравномерна по длине и непрерывно изменяется.
Дата добавления: 2015-12-21; просмотров: 14; Мы поможем в написании вашей работы! |
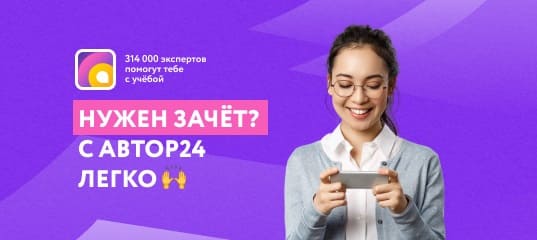
Мы поможем в написании ваших работ!