Анализ точности обработки с использованием законов распределения размеров.
Законы распределения размеров в ТМС применяются для:
1. для установления надежности проектируемого тех. процесса и обеспечения обработки деталей без брака.
2. определения количества деталей, требующих доп. обработки;
3. расчета экономической целесообразности использования высокопроизводительных станков пониженной точности
4. при расчете точности настройки станков
5. сопоставление точности обработки деталей в различных условиях.
Установление надежности обработки сводится к сопоставлению поля фактического рассеяния размеров детали (ω) с допуском (Т), при этом надежность обеспечения точности обработки характеризуется запасом точности. Ψ=Т/ω; Ψ<1- брак вероятен, Ψ≥1,2- процесс обработки надежен, Ψ>1 – обработка может быть осуществлена без брака при правильной настройке.
Главное условие надежности и качества: ω < T
При наличий систематической погрешности, вызывающей смещение поля рассеяния: ω + ∆сист < T
Методика статистического анализа операций тех. процесса методом выборок:
1. из партии деталей, обработанных на данной операций берется текущая выборка, состоящая из деталей, изготовленных подряд при одних и тех же условиях обработки, при условий, что объем выборки не менее 50 штук.
2. производится измерение по интересующему нас параметру и цена деления измерительного прибора должна быть в пределах (1/5; 1/10) Т.
3. действительные размеры деталей выборки разбиваются на ряд интервалов, число которых не менее 6 и цена интервала не должна превышать цену деления шкалы измерит. прибора не менее чем в 2 раза.
|
|
4. определяются частоты и частности.
5. рассчитываются среднеарифметические и среднеквадратическое отклонения.
6. в особо ответственных случаях производится проверка выборки на случайность с помощью метода последовательных разностей.
а1 = L2 - L1; a2 = L3 - L2; аn-1 = Ln - Ln-1
После чего определяется несмещенная оценка:
7. рассчитывается критерий: τ = с2/σ2
Если τ < τq – выборка случайна:
8. производится проверка соответствия эмпирического распределения действительных размеров закону Гаусса.
9. определяется зона практического рассеяния и необходимое и достаточное условие работы без брака: ω + ∆сист < T
10. определяется запас точности.
11. опр-ся коэфф. точности настройки, показывающий величину смещения вершины кривой рассеяния относительно середины поля допуска.
Расчет количества вероятного брака деталей:.
- производится из предположения что площадь ограниченная кривой нормального рассеяния и осью абсцисс охватывает 100% деталей партии.
Для определения количества годных деталей находим площадь, ограниченную полем допуска и кривой рассеяния. При симметричном расположении кривой относительно поля допуска, необходимо найти удвоенное значение интеграла:
|
|
; где t = (Li-Lcp)/σ = x0/σ
С увеличением значения t уменьшается количество брака.
Т. к. решение ф-ий Лапласа зависит не от х0 и σ, а от их соотношения то расчет количества годных деталей сводится к определения t и определению ф-ий Лапласа.
Определение количества деталей, требующих дополнительной обработки.
При выполнений задания на высокопроизводительном, но неточном станке или отсутствии на предприятии станка требуемой точности, т. е. когда не выполняется условие обработки без брака, а допустить появление окончательного брака нельзя, настройка производится с заведомым смещением вершины кривой рассеяния, так чтобы весь брак можно было исправить путем доп. обработки.
При обработке валов необходимо сместить вершину кривой рассеяния, на некоторую величину m вправо от середины п. д. вершину кривой рассеяния чтобы все валы выходящие за пределы поля допуска имели размер больше допустимого и после доп. обработки могли стать годными. Аналогично, отверстия должны иметь размер меньше заданного для чего кривая смещается влево на величину m по отношению к середине поля допуска.
|
|
При этом кол-во дет. требующих доп. обработки значительно возрастает.
хВ = хА = Т - 3σ - Δн
Обеспечение точности мех. обработки.
Эта задача обеспечивается по следующим направлениям, т. е. точностные расчеты и осуществление первоначальной настройки станков обеспечивающие min систематическую погрешность, связанные с настройкой, а также реализация наибольшего периода работы станков без поднастройки.
Расчеты режимов резания с учетом фактической жесткости технолог. системы.
Точное управление процессом обработки и своевременная точная поднастройка станков.
Дата добавления: 2015-12-21; просмотров: 21; Мы поможем в написании вашей работы! |
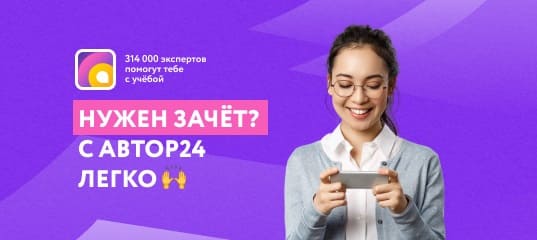
Мы поможем в написании ваших работ!