Настройка и Эксплуатация валковой арматуры
8.1 Основные требования
8.1.1 К установке в рабочие клети допускается арматура, изготовленная по чертежам, разработанным калибровочным бюро и утверждённым главным прокатчиком.
8.1.2 Арматура должна соответствовать прокатываемому профилю, в исключительных случаях при прокатке балочных профилей допускается применять близкие проводки, при этом, во избежание аварийной ситуации, проводки должны быть разогнаны по диагонали калибра.
8.1.3 Для производства фасонного проката используется валковая арматура - фланцевые и шейковые проводки, а для сортового – шейковые проводки, направляющие линейки и коробка роликов пропусков (на чистовой клети) для круглого проката.
8.1.4 На рабочей поверхности арматуры, не должно быть раковин, вмятин, трещин и других дефектов, влияющих на качество поверхности готовой продукции.
8.2 Эксплуатация валковой арматуры
8.2.1 В процессе работы охлаждение арматуры осуществляется водой, подаваемой на бочки валков. Ролики пропусков охлаждаются водой, поступающей из коллекторов, установленных в корпусе коробки. В аварийных случаях, когда раскат находится в роликах пропусков и дальнейшая прокатка невозможна, необходимо:
- немедленно прекратить подачу воды на ролики;
- принять срочные меры по извлечению раската из роликов пропусков.
8.2.2 Для исключения случаев перегрева арматуры, при необходимости, устанавливается дополнительное охлаждение.
|
|
8.2.3 Арматура, подвергнутая деформации или механическому повреждению в процессе прокатки, должна быть заменена.
8.2.4 Приёмка валковой арматуры после ремонта и переточек производится сменным мастером УСПК.
8.3 Настройка валковой арматуры
8.3.1 Валковая арматура устанавливается таким образом, чтобы обеспечить безаварийную задачу раската в калибр и прямой безаварийный выход полосыиз валков.
8.3.2 Настройка валковой арматуры клети «1300» описана в 3.2.7.
8.3.3 При настройке проводковой арматуры, устанавливаемой к нижнему валу, необходимо, чтобы носок проводки был ниже верхнего уровня валка на 8-10 мм и плотно соприкасался с валом. «Пятка» проводки должна находиться на одном уровне с носком, либо чуть ниже. Настройка арматуры, устанавливаемой к верхнему валу, производится аналогично. Чтобы обеспечить плотное прилегание носка проводки к валу, необходимо цепное крепление уравновешивающего груза фиксировать по центру проводки. Цепь не должна быть перекручена, а звенья цепи иметь поверхностный износ. ”Коромысло“ необходимо устанавливать в дугообразном пазу анкерного кольца под острым углом.
8.3.4 Для исключения аварийных ситуаций, проводки настраиваются таким образом, чтобы их боковая поверхность находилась в одной плоскости с боковой поверхностью горизонтального валка, либо перекрывала её на 2-4 мм.
|
|
8.3.5 Перемещение проводок в поперечном направлении производится распорными винтами, находящимися на боковой поверхности опор (посадочных мест проводок).
8.3.6 Монтажные зазоры между верхними и нижними проводками регулируются в вертикальном направлении с помощью винтов на опорах. Зазоры устанавливаются таким образом, чтобы рабочая боковая поверхность проводок обеспечивала безаварийное и прямолинейное прохождение полосы.
8.3.7 Направляющие линейки используются при производстве сортового проката, для прямолинейной задачи раската в ящичный, овальный и универсальный калибры, а также для прямолинейного выхода заготовки из валков. Установка направляющих линеек производится по центральной продольной оси калибра и исключает возможность задачи раската на бурты и сваливание заготовки в калибре. Расстояние между линейками, непосредственно у самого калибра, должно быть на 4-10 мм больше ширины прокатываемой заготовки, в зависимости от поперечного сечения профиля.
Если в процессе работы произошло смещение направляющих линеек, прокат должен быть остановлен для установки арматуры.
|
|
8.3.8 При производстве круглого проката для задачи раската овального сечения в чистовую клеть используется коробка роликов пропусков.
8.3.9 Перед сборкой роликов пропусков в кассеты ролики проверяются на соответствие прокатываемому профилю.
8.3.10 После монтажа кассет с роликами пропусков в корпус коробки на участке сборки и перевалки клетей производится её предварительная настройка.
Приёмка предварительной настройки осуществляется вальцовщиком чистовой клети (при необходимости, старшим вальцовщиком и сменным производственным мастером стана).
8.3.11 Пропусковая коробка устанавливается непосредственно напротив рабочего калибра клети.
8.3.12 При помощи кронциркуля и линейки устанавливается соответствующий данному профилю монтажный зазор между роликами пропусков.
8.3.13 Монтажный зазор устанавливается таким образом, чтобы обеспечить прямой безаварийный заход полосы в валки и исключить её застревание в роликах пропусков.
8.3.14 Осевая регулировка передних и задних роликов пропусков производится при помощи распорных болтов, расположенных на боковой поверхности корпуса коробки.
8.3.15 Окончательная настройка коробки роликов пропусков производится вальцовщиком чистовой клети после пробной прокатки. Настройка должна обеспечить получение одинаковой величины разъёмов на готовом профиле. Положение кассет (обойм) с роликами, после окончательной настройки коробки, жестко фиксируется стопорными болтами, находящимися на поверхности корпуса коробки и должно обеспечить равномерную работу всех четырёх роликов.
|
|
8.4 Контроль за соблюдением требований данного раздела осуществляет сменный производственный мастер стана.
ПРОКАТКА
9.1 Основные положения
9.1.1 Металл прокатывается согласно установленной очерёдности выдачи из печей.
О каждом нарушении порядка прокатки (возврат заготовки, снятие недоката) контролёр УТК на печах и старший вальцовщик стана сообщают по потоку по селекторной связи.
9.1.2 Перед прокаткой новой плавки делается кратковременный разрыв с сообщением по потоку контролёром УТК об окончании катаемой плавки. Новая плавка выдаётся из печей после того, как последняя заготовка предыдущей плавки прокатана на клети «1300».
9.1.3 Информация об окончании плавки передаётся по технологическому потоку по селекторной связи операторами постов управления по мере прохождения последней заготовки плавки на каждом технологическом участке.
9.1.4 Перед клеймовочной машиной расположен лазерный измеритель длины вырезанных на участке пил горячей резки (ПГР) штанг. Измеритель фиксирует длину и количество проходящих через лазерный луч штанг для создания оперативного электронного учета проката.
9.1.5 При прохождении последней штанги плавки через лазерный измеритель резчик поста управления участка ПГР сообщает по селекторной связи об окончании плавки на участок холодильника и производит ввод информации об окончании прокатываемой плавки в систему оперативного учёта проката (нажимает кнопку «Конец плавки»).
9.1.6 Оператор поста управления-9 (ПУ-9) (горячей стороны участка центрального холодильника), подтвердив принятие сообщения об окончании плавки, производит поплавочное разделение проката на холодильнике.
9.1.7 В аварийных ситуациях на участке стана металл, прокатанный за несколько пропусков или полностью в клети «1300», может быть возвращен на участок нагревательных печей. Посад в печь заготовок со стороны выдачи для подогрева и дальнейшей прокатки – в соответствии с ТИ 102-П.С-84-2009.
9.1.8 Через возвратный поток универсально-балочного стана (УБС) на участок вырубки и уборки горячего металла (УВ и УГМ) направляются:
- подкат для собственного производства;
- подкат из стали 2 и 3 групп по условиям охлаждения;
- заготовки, выдаваемые из печей из-за аварий на УБС;
- заготовки, прокатанные в клети «1300» с дефектами, указанными в 9.2.5.
Порядок выдачи металла на возвратный поток – в соответствии с ТИ 102-П.С-84-2009.
9.2 Прокатка в обжимной клети
9.2.1 Прокатка в обжимной клети производится согласно утверждённым главным прокатчиком схемам прокатки из заготовки соответствующего сечения и формы.
Отработка обжатий выполняется в автоматическом режиме работы нажимных механизмов. Эксплуатация микропроцессорной системы управления нажимными механизмами приведена в приложении Ж.
Для выполнения заданного профиля и исключения подрезов, закатов и других дефектов, получаемых вследствие несоответствия размеров заготовки, увеличения ширины калибров при переточке или выработке валков, допускается отступление от схемы обжатий с соответствующим увеличением количества пропусков.
Превышение максимальных обжатий, установленных схемой прокатки, допускается не более, чем на 10 % при условии соблюдения температурного режима прокатки.
9.2.2 Во избежание пробуксовок захват заготовок и прокатка в первых пропусках производится при скорости вращения валков не более 20 об/мин, выброс раската из валков – при скорости не более 30 об/мин. Выброс раската в последнем пропуске производится при максимальной скорости вращения валков.
9.2.3 Темп прокатки в обжимной клети устанавливается в зависимости от темпа прокатки на универсальных группах клетей.
В случае задержки прокатки на универсальных группах клетей прокатка следующих заготовок в обжимной клети приостанавливается.
9.2.4 Температура конца прокатки в обжимной клети должна быть не менее 1100 °С.
Температура конца прокатки в обжимной клети «1300» фиксируется спектропиром, установленным перед ПГР № 7.
9.2.5 После прокатки на обжимной клети заготовки подаются на раскатной рольганг черновой группы клетей.
Запрещается подача заготовок с закатом, усом, скрученных и с температурой, ниже регламентированной. Такие заготовки направляются на возвратный поток.
9.2.6 Дефекты, имеющиеся на концах раската, должны быть удалены на ПГР № 7, находящейся после клети «1300».
9.2.7 При порезке на ПГР № 7 необходимо:
- собрать схему на работу пилы;
- включить вращение диска пилы;
- предупредить оператора поста управления черновой группой клетей (ПУ-5) о порезке;
- дождаться показания на счётчике пропусков ГУК-1 первого пропуска;
- подогнать раскат под пилу и остановить его;
- нажать кнопку подачи пилы на рез;
- при возвращении пилы в исходное положение нажать кнопку сталкивателя обрези, предварительно поставив ключ управления сталкивателем в нужное положение;
- отдать раскат на рольганг черновой группы клетей или докатать его в обжимной клети;
- разобрать схему на работу пилы.
9.2.8 Основные дефекты профиля заготовки, прокатанной в обжимной клети «1300», и меры по их предупреждению и устранению - в соответствии с приложением И.
9.3 Прокатка в универсальных группах клетей
9.3.1 Прокатка в универсальных группах клетей производится согласно утверждённым главным прокатчиком схемам в автоматическом режиме работы оборудования.
В случае отказа системы автоматического управления прокаткой производится переход на полуавтоматический или ручной режим работы до устранения причин неполадок и сбоев в работе оборудования.
При аварийной ситуации на одной из групп клетей допускается прокатка на другой группе с использованием аварийной схемы прокатки для данного профиля.
9.3.2 Захват и выброс раскатов производится на пониженных оборотах, величина которых, также как и скорость самой прокатки, зависит от прокатываемого профиля и отрабатывается системой автоматического управления главными приводами.
9.3.3 Пробная прокатка после перевалки клетей ведётся в ручном режиме работы на пониженных скоростях захвата прокатки и выброса полосы. Переход в автоматический режим производится после получения удовлетворительного профиля и полной настройки вспомогательного оборудования по указанию вальцовщика соответствующей группы клетей.
9.3.4 Прокатка в черновой и промежуточной группах клетей ведется с обеспечением одинаковых линейных скоростей вращения валков ГУК и ВК соответствующих групп, которые регулируются и контролируются автоматически.
В случае отказа системы автоматики допускается ручная регулировка синхронности вращения валков.
9.3.5 Темп прокатки поддерживается в зависимости от пропускной способности участка пил горячей резки и участка центрального холодильника, а также от графика выдачи заготовок из печей.
9.3.6 Температура конца прокатки в чистовой клети должна обеспечивать качественную порезку раската на ПГР и соответствовать таблице 1.
Таблица 1 – Температура конца прокатки
Вид профиля | Температура, °С, не менее |
Сортовой | |
Фасонный |
Температура измеряется перед ГУК-3 пирометром – спектропиром.
9.3.7 Недокаты, полученные в процессе прокатки в универсальных группах клетей, снимаются с рабочей линии стана на специальный стеллаж. Данные о количестве недокатов старший вальцовщик передаёт контролёру УТК ПУ-3.
9.3.8 Управление технологическим процессом осуществляется операторами постов управления черновой (ПУ-5), промежуточной (ПУ-6) групп клетей и чистовой клети (ПУ-7), а также вальцовщиками и старшим вальцовщиком стана. Контроль за соблюдением и правильным применением настоящей инструкции на участке возлагается на старшего вальцовщика и сменного мастера стана.
9.3.9 В процессе работы оператор ПУ стана горячей прокатки производит настройку системы автоматического управления прокаткой и непрерывно контролирует её работу. В случае отказа работы систем автоматики переходит на полуавтоматический или дистанционный (ручной) режим управления обслуживаемых механизмов. Оператор непрерывно контролирует показания «нагрузок» двигателей главных приводов, сообщая о них старшему вальцовщику стана, не допускает нарушение температурных режимов и режимов обжатий; cледит за разделением плавок по потоку (передаёт информацию о начале и конце плавки на своём технологическом участке); в случаях аварий или появления брака останавливает прокат.
9.3.10 В процессе работы вальцовщик стана производит настройку валков клетей в осевой регулировке, настройку валковой арматуры, установку направляющих бортов и подъёмных столов. Контролирует геометрические размеры профиля раската, подающегося в соответствующую группу клетей. Непрерывно следит за задачей и выходом раската из валков, прохождением полосы между клетями, а также за охлаждением валков и валковой арматуры.
9.3.11 Выходящие из клетей раскаты не должны иметь загнутых концов.
Причинами изгиба передних концов раскатов могут быть:
- неточная установка подъёмных столов;
- неправильная установка проводковой арматуры;
- недостаточная длина проводок;
- неравномерный нагрев металла;
- смещение оси прокатки.
Вальцовщик стана не допускает в прокат холодные, скрученные заготовки и раскаты с дефектами по концам, способные привести к аварии; выполняет указания старшего вальцовщика по настройке стана; в случаях аварий или появления брака останавливает прокат.
9.3.12 В процессе работы старший вальцовщик производит настройку стана и руководит работой технологического персонала участка, постоянно следит за правильностью получения профиля, расходом и раскроем металла на участке ПГР, а также темпом прокатки на стане. Старший вальцовщик контролирует: качество профиля периодическим отбором проб на соответствие размеров, массу 1 м длины профиля, состояние поверхности; следит за показаниями «нагрузок» на главных приводах двигателей через вальцовщиков стана; контролирует размеры раската с клети «1300», черновой и промежуточной групп клетей. В случаях аварий и получения брака останавливает прокат.
9.3.13 Основные дефекты профиля, меры их предупреждения и устранения при прокатке в универсальных группах клетей - в соответствии с приложением К.
9.3.14 При производстве двутавров, в зависимости от размеров профиля, раскат прокатывается за 3-7 пропусков в черновой, за 1-3 пропуска в промежуточной группах клетей и за один пропуск в чистовой клети.
Прокатка раскатов, длина которых превышает расстояние между осями промежуточной группы и чистовой клетью, производится в клетях ГУК-2, ВК-2 и ГУК-3 одновременно, по инструкции для операторов ПУ-6 и ПУ-7 «Прокат длинномерного раската».
Аварийные схемы прокатки предусматривают прокатку за 5-9 пропусков в одной из групп клетей и за один пропуск в чистовой клети.
9.3.15 Прокатка шпунта ведётся за один пропуск во всех группах клетей.
При пробной прокатке, после перевалки клетей, первый подкат с клети «1300» задаётся в клеть ВК-1 и реверсом выдается из валков. На ПГР-7 вырезается профильная проба очага деформации, заготовка убирается на возвратный поток, как недокат. После замера элементов профиля, при необходимости, производится выравнивание валков и изменение межвалковых зазоров клетей «1300» и ВК-1. На следующем раскате после прокатки в черновой группе клетей производят замер стенки профиля. Полосу задают в клеть ГУК-2 и реверсом выбрасывают из валков, для очередного замера стенки профиля. Затем прокатывают в промежуточной группе клетей и после замера стенки докатывают в чистовой клети. После осмотра и замера элементов готового профиля, при необходимости, производится выравнивание валков и изменение межвалковых зазоров клетей ГУК-1, ГУК-2, ГУК-3 и ВК-2.
9.3.16 При производстве круглого проката заготовка прокатывается за три пропуска в черновой группе клетей, затем кантуется при помощи кантователя на 90° вокруг своей оси, прокатывается за один пропуск в промежуточной группе клетей и, скантованная на 90° в кантующей шайбе, за один пропуск прокатывается в чистовой клети.
Для задачи и прохождения полосы через чистовую клеть в качестве проводковой арматуры применяется пропусковая коробка.
Осевая регулировка передних и задних роликов пропусков производится при помощи распорных болтов, закреплённых с обеих сторон корпуса коробки.
Примечание - При прокате круга 210, 220 (круглый прокат диаметром 210, 220 мм) вместо клетей ВК-1, ГУК-1 и ВК-2 устанавливаются съёмные секции рольгангов. Подкат с клети «1300» прокатывается за один пропуск в овальном калибре клети ГУК-2, а затем кантуется на 90° в кантующей шайбе и прокатывается за один пропуск в чистовой клети.
9.3.17 Прокат квадратной заготовки ведется в ящичных и универсальных калибрах.
Количество клетей, пропусков в них, наличие кантовок раската вокруг своей оси на 90° зависит от сечения готового профиля и отражено в схемах прокатки.
9.3.18 При производстве листового проката заготовка прокатывается в черновой группе клетей за 5-9 пропусков в зависимости от толщины листа. Клети ГУК-2, ВК-2 и ГУК-3 убираются, вместо них устанавливаются съёмные секции рольгангов. Скорость захвата и выброса полосы 20-25 об/мин, скорость прокатки 60-90 об/мин в зависимости от длины раската. В целях исключения аварийных ситуаций, при прокате тонкого листа, скорость вращения роликов транспортного рольганга должна быть не меньше скорости прокатки. При производстве листа толщиной более 50 мм прокатка производится за один пропуск, зазор между валками устанавливается с учетом размера листа и коэффициента теплового расширения металла.
9.3.19 Подкат для сортовых станов после проката на обжимной клети «1300» транспортируется через участок УБС с использованием съемных беспроводных секций рольгангов, устанавливаемых вместо ГУК-1, ГУК-2, ГУК-3 и ВК-2, ВК-3.
9.4 Контроль процесса прокатки
9.4.1 Качество профиля контролируется периодическим отбором проб. Для проверки соответствия размеров элементов профиля и массы 1 м профиля требованиям НД пробы отбираются от каждой прокатываемой плавки, но не реже, чем через 50 полос при установившейся работе стана. Размеры элементов профиля, масса 1 м длины и состояние поверхности должны соответствовать требованиям НД. Результаты контроля заносятся в журнал регистрации отбора проб.
Примечание - При пробной прокатке после перевалки клетей пробы отбираются от каждой полосы до получения удовлетворительного профиля по размерам и допустимой массы 1 м длины профиля.
9.4.2 Размеры готового профиля контролируются с помощью шаблонов, микрометра, штангенциркуля.
9.4.3 Масса 1 м длины профиля контролируется путём взвешивания проб на весах с точностью до 10 г и измерения длины пробы и определяется делением массы пробы на её среднюю длину с регистрацией результата в журнале регистрации отбора проб.
9.4.4 Контроль состояния поверхности проката осуществляется старшим вальцовщиком и мастером стана на пробах длиной не менее 150 мм, отбираемых от каждой плавки, после удаления концевой обрези, от любой части раската или на холодильнике - путём осмотра проката по всей длине.
В начале прокатки, после перевалки и аварийных остановок старший вальцовщик останавливает раскат после чистовой клети и осматривает поверхность проката для выявления отпечатков, рисок, закатов, усов и т.п.
9.4.5 В профилактику, после перевалки клетей, а также при аварийных остановках стана вальцовщик чистовой клети и старший вальцовщик (при необходимости, мастер стана и мастер УТК) осматривают поверхность проката на штанге, вырезанной на участке ПГР, на специальной смотровой площадке за чистовой клетью. При выявлении отпечатков, рисок и других дефектов производится обточка валков или, при необходимости, делается перевалка клетей. Обточка валков осуществляется вальцовщиком стана абразивным кругом, установленным в специальное приспособление.
9.4.6 После перевалки клетей, профилактики, при переходе с литера на литер, с углеродистых марок стали на легированные и наоборот, а также в течение смены вальцовщики ГУК-1, ГУК-2, ГУК-3 контролируют размеры элементов профиля, поступающего в соответствующую группу клетей.
Схема контроля технологического процесса – в соответствии с приложением Л.
ПОРЕЗКА
10.1 Порезка раскатов производится пилами горячей резки в соответствии с фабрикацией (заказом) на мерные, кратные мерные и немерные длины.
10.2 Порезка подкатов для сортовых станов крупносортного (КСЦ) и рельсобалочного (РБЦ) цехов не производится.
10.3 Штанги мерной и кратной мерной длины вырезаются с учётом припуска на температурную усадку и допуска на порезку: в соответствии с заказами и требованиями НД.
Коэффициент температурного линейного расширения принимается:
для фасонного проката………………………………….………….….1,013;
для сортового проката………………………………………………...1,015.
10.4 Для обеспечения стойкости дисков пил порезка раскатов производится при температуре металла после чистовой клети, оС, не менее:
для квадратной заготовки и круглого сортового проката……..…….800;
для фасонного проката……………………………………..……………700.
10.5 В исключительных случаях (аварийная ситуация) допускается порезка раскатов при температуре не менее 600 °С.
10.6 Размеры обрези переднего и заднего концов должны гарантировать полное удаление концевых дефектов и невыполненных элементов профиля.
Минимальная величина концевой обрези приведена в таблице 2.
Таблица 2 – Минимальная величина концевой обрези
Наименование профиля | Обозначение профиля, размеры профиля, мм | Длина обрези, мм |
Двутавры | 20Б-25Б | |
20ДА-25ДА | ||
30Б-41БA | ||
31УA-36УA | ||
41УА | ||
45Б-61БA | ||
61УА | ||
20Ш-30Ш | ||
35Ш-50Ш | ||
12КC-15КC | ||
20К | ||
25К-30К | ||
35К-40К | ||
24М, 30М | ||
36М, 45М | ||
Квадратная заготовка | 100-125 | |
130-160 | ||
Круглый прокат | 120, 130 | |
140, 150 | ||
210, 220 | ||
Шпунт | Л5-УМ | |
Лист | - |
10.7 При порезке раскатов следует руководствоваться следующими положениями:
10.7.1 Первой по потоку стационарной пилой отрезается передний конец и вырезаются пробы.
10.7.2 По переднему обрезанному концу раскат устанавливается в заданном положении для порезки пилами № 2, 3, 4, 5, 5а, 6. В зависимости от длины раската и заданного раскроя применяются схемы расстановки пил, приведённые в таблице 3.
Таблица 3 – Схема расстановки пил
Длина вырезаемой штанги, м | Длина раската, м | Количество штанг, шт. | Номера пил, участвующих в порезке |
от 6 до 9 | от 48 до 96 | 5-10 | 2-3-5-5а-6 |
св. 9 до 12 | от 48 до 96 | 5-10 | 2-4-6 |
св. 12 до 16 | от 48 до 96 | 4-8 | 2-3-5-6 |
св. 16 до 18 | от 48 до 96 | 3-6 | 2-3-5 |
св. 18 до 24 | от 54 до 96 | 3-5 | 2-4-6 |
свыше 24 | от 48 до 96 | 2-4 | 2-5 |
10.7.3 При порезке второй половины раската производится обрезка заднего конца стационарной пилой № 2, одновременно следующий раскат подаётся к пиле № 1 для обрезки переднего конца.
Примечание – Для установки раската под раскрой на заданные длины используются три передвижные телекамеры.
10.7.4 При порезке штанг немерной длины остановка раската производится по заднему концу в зоне удаления минимально допустимой обрези.
10.7.5 Расстановка пил производится в соответствии с заказом дистанционно или автоматически по заданной программе. Оперативный контроль точности расстановки пил производится путём измерения длины вырезанных штанг, проходящих через лазерный измеритель. Окончательная корректировка расстановки пил производится с учётом промера штанг рулеткой на участке центрального холодильника.
10.7.6 При расстановке пил старший резчик визуально контролирует расстояния (зазоры) между пилами, неприводными и приводными роликовыми секциями рольгангов, которые должны обеспечить качественное и безаварийное транспортирование штанг, исключающее получение механических дефектов на годном прокате.
10.8 Обрезь от пил № 1 и № 2 подаётся сталкивателями на промежуточные тележки, установленные на наклонных рельсовых путях, а затем – в скиповый подъёмник, который транспортирует обрезь в вагоны. Передвижение вагонов производится маневровым устройством.
10.9 Технологические пробы после вырезки сталкиваются с рольганга и затем транспортируются пробовозом на участок чистовой клети.
Пробы для испытаний снимаются на участок вырезки проб.
10.10 В процессе порезки диски пил непрерывно охлаждаются водой. В местах реза не допускается потемнение раската.
10.11 Ответственность за порезку раскатов на длины в соответствии с заказом, максимальный выход мерных длин и качество реза возлагается на старшего резчика.
ЗАМЕНА ДИСКОВ ПИЛ
11.1 Замене подлежат диски деформированные, с трещинами, с выкрошенными (срезанными) зубьями. При появлении грубых заусенцев и стружки на поверхности реза также производится замена дисков.
11.2 К установке на пилу допускаются диски, предварительно заточенные, отрихтованные и отбалансированные, с одинаковым шагом зубьев, без трещин и других видимых дефектов.
11.3 При замене диска пилы необходимо:
- остановить двигатель вращения диска пилы и разобрать электрическую схему вращения диска;
- с помощью стопорного механизма зафиксировать тягу кожуха диска на раме пилы;
- маятник пилы вывести в крайнее переднее положение, при этом кожух диска поворачивается и открывается гайка, крепящая диск;
- разобрать электрическую схему подачи диска пилы;
- отвернуть гайку крепления диска, оставив 2-3 нитки резьбы;
- произвести строповку диска в комплекте со ступицей, отвернуть гайку до конца;
- вывести диск из зацепления с вала и перевести на стенд использованных дисков;
- установить новый диск на вал, закрепить диск гайкой и отсоединить строп;
- после надёжного закрепления диск повернуть вручную и убедиться в плотном прилегании к планшайбе;
- собрать электрическую схему подачи диска пилы;
- включением механизма подачи диска привести маятник в исходное положение, расфиксировать стопорным механизмом тягу кожуха диска;
- собрать электрическую схему вращения пилы, опробовать работу пилы вхолостую и убедиться в нормальной работе оборудования.
11.4 Контроль за соблюдением требований данного раздела осуществляет сменный мастер стана.
Дата добавления: 2015-12-20; просмотров: 42; Мы поможем в написании вашей работы! |
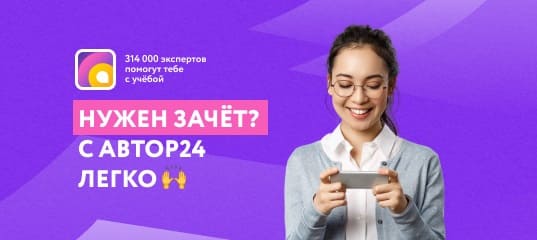
Мы поможем в написании ваших работ!