Основные методы сборки. Сборочные размерные цепи. Техническая классификация методов сборки
Классификация соединений и их технологичность. Классификация соединений, применяемых при сборке. Подвижные и неподвижные соединения, их технологичность
Технологическое оборудование сборочных цехов. Оборудование сборочных цехов, автоматизация и механизация сборочных процессов.
Широко распространены на сборке прессы, действующие от
сжатого воздуха, поступающего из цеховой магистрали; давление
воздуха 4—5 кгс/см2. пресса. Применяют пневмопрессы прямого действия и рычажные.
При необходимости иметь большие силы применяют прессы
со сдвоенными цилиндрами или с усилителями — рычажными
, клиновыми или других типов.
, ! Кроме универсальных пневматических прессов, при сборке
широко применяют также прессы специального назначения.
В группе переносных прессов специального назначения следует
отнести прессы-скобы, имеющие широкое применение во многих
сборочных производствах. Такой пресс имеет литую
или сварную станину, на которой смонтирован пневмоцилиндр.
Пресс-скобу подвешивают над рабочим местом, а при выполнении
операции устанавливают на сборочной единице.
В массовом производстве получают распространение много
|
|
местные запрессовочные автоматы. Например, применяется ав
томат, с помощью которого в блок запрессовываются одновременно
шесть седел клапанов, поступающих из шести магазинов. Седла
запрессовывают после предварительного охлаждения. Сила за
прессовки создается гидроцилиндрами.
В сборочных цехах находят применение также пневмогидра
влические прессы. Силовое устройство такого пресса состоит из
пневмоцилиндра и гидравлического усилителя. Рабочая сила на
штоке пресса создается давлением масла, а ускоренный подъем
штока производится сжатым воздухом.
Сборочные приспособления и инструмент. Оснастка и инструмент сборочных цехов.
С помощью технических средств измерений контролируют за
зоры в сопряжениях и относительное положение деталей. Для этого
применяют концевые и штриховые меры длины, щупы, штанген-
инструменты, микрометрические инструменты, рычажно-меха-
нические, электрические и пневматические приборы, а такжэ
различные специальные контрольные приспособления и уста
новки.
гда следует принимать установочные базы.
К основным видам геометрических проверок, осуществляемых
при сборке сборочных единиц и механизмов с помощью техни
|
|
ческих средств, относятся контроль зазоров , проверка
на радиальное, осевое и торцовое биения , контроль
параллельности и перпендикулярности , соосности, прямо
линейности и плоскостности , положения деталей в неко
торых сборочных единицах .
Для контроля точности сборки служат также разнообразные
специальные средства комплексного контроля, измерения кинема
тической погрешности; применяют анализирующие приборы объ
ективной оценки качества сборочных единиц и изделий.
По типу привода сборочные приспособления подразделяют на
механические, гидравлические, пневматические и пневмогидрав-
лические. Тип привода выбирают на основе технико-экономиче
ского расчета.
Инструмент, используемый в сборочном производстве, в за
висимости от характера операций, при которых он применяется,
условно делится на две группы: для вспомогательных пригоночных
работ, связанных со снятием стружки, и для основных технологи
ческих сборочных работ. В эти группы включаются инструменты
ручные, когда расходуется только энергия сборщика, и механи
зированные. И в той, и другой группе есть инструменты универ
сального и специального назначения.
К ручному относится режущий, вспомогательный и так назы
|
|
ваемый слесарно-сборочный инструмент. Режущий инструмент —
это напильники, шаберы, надфили, притиры; вспомогательный —
кернеры, бородки, пробойники, выколотки, клейма, специальные
молотки; слесарно-сборочные —■ гаечные ключи, отвертки, шпиль-
коверты, плоскогубцы, круглогубцы и острогубцы, шплинто-
и штифтовыдергиватели, оправки.
Конструкция и вид применяемого инструмента в значительной
мере предопределяют уровень производительности труда на
сборке. Общее правило состоит в том, что ручной инструмент
необходимо заменять механизированным. Однако полностью
отказаться от применения ручного инструмента не всегда пред
ставляется возможным. В таких случаях для повышения эф
фективности и улучшения качества сборки целесообразно при
менять ручные инструменты специального назначения. В част
ности, пользоваться в заводских условиях универсальными гаеч
ными ключами (например, разводными) не рекомендуется. Вслед
ствие перекашивания губок они неправильно охватывают гайку
или головку винта, сминают их грани и затрудняют применение
нормальных ключей при дальнейших переборках резьбовых соеди
|
|
нений в условиях эксплуатации машин.
Удобны в работе, например, накладные многогранные гаечные
ключи, имеющие замкнутый контур (рис. 119, 120). Они более
жестки, дают возможность обеспечить большую затяжку гаек
или винтов.
При навинчивании крупных гаек, когда требуются значитель
ные крутящие моменты, применяют подобные ключи с двумя ру
коятками. Весьма удобны ключи-коловороты (рис. 121). Благо
даря непрерывному вращению эти ключи ускоряют завинчивание
гаек и винтов примерно в 4—5 раз. В рациональных конструк
циях ключей-коловоротов предусматривается незначительное тре
ние ручек о стержень и достаточная жесткость при небольшой
массе.
Затягивать винты и гайки крупных размеров, особенно в труд
нодоступных местах, удобно трещоточными ключами, которые,
как и торцовые, не надо снимать с гайки после каждого поворота,
что позволяет экономить до 50—60% времени по сравнению с вы
полнением операций обычными ключами. Для сборки соединений
с диаметрами резьб до 20 мм удобно применять ключи с торцовыми
трещотками (рис. 122). Накладной трещоточный ключ с собачкой
(рис. 123) предназначен для навинчивания гаек или винтов с диа
метрами резьб 24—30 мм.
Для завинчивания вручную винтов небольших размеров целе
сообразно применять отвертки-дрели. При их помощи процесс
завинчивания ускоряется в 1,5—2 раза.
К механизированному инстру
менту для пригоночных работ
относятся сверлильные и шлифо
вальные ручные машины, меха
нические шаберы, машины для на
резания резьбы. Непосредственно
при выполнении сборочных опера
ций применяются завертывающие
и развальцовывающие машины.
В зависимости от назначения приспособления можно разделить на следу
ющие основные группы:
а) приспособления-зажимы, которые служат для закрепления
собираемых изделий, сборочных единиц или деталей в требуемом для сборки
положении, а также для придания устойчивости сборочной единице и облегчения
ее сборки;
б) установочные приспособления, предназначенные для
правильной и точной установки соединяемых деталей или сборочных единиц
относительно друг друга, что гарантирует получение требуемых монтажных
размеров;
в) рабочие приспособления, используемые при выполнении
отдельных операций технологического процесса сборки, например вальцевания,
запрессовки, постановки и снятия пружин и т. д.;
г) контрольные приспособления, изготовленные примени
тельно к конфигурации, формам, размерам и другим особенностям проверяемых
сопряжений сборочных единиц и изделий для контроля конструктивных пара
метров, получающихся в процессе сборки.
Сборка крупных сборочных единиц — конструкций, а в ряде
случаев и общая сборка изделий осуществляется в приспособле
ниях, называемых стапелями. При сборке детали закрепляют
в массивных каркасах-стапелях, на которых и производят все
необходимые пригоночные и сборочные операции. Благодаря со
хранению постоянства конструкторских баз в самих стапелях
обеспечивается совпадение и единство баз сборочных единиц и в ре
зультате точная стыковка их между собой при общей сборке.
Различают разделочные и собственно сборочные стапели. Пер
вые предназначены для выполнения механической доработки
стыковых поверхностей и других элементов агрегатов, вторые —
для выполнения всех подготовительных операций и сборки сбо
рочных единиц (с применением клепки, крепления на болтах и пр.).
Основные требования, предъявляемые к любому сборочному
приспособлению, состоят в том, чтобы его конструкция обеспечи
вала точность установки деталей или сборочной единицы, удоб
ство расположения собираемого объекта и простоту его закрепле
ния, возможность легкого снятия сборочкой единицы (изделия)
после сборки, безопасность в работе.
Большое значение для точности сборки имеет известный прин
цип определенности базирования деталей в приспособлении. Оп
ределенность характеризуется таким относительным положением
деталей в сборке, при котором процесс соединения осуществляется
в полном соответствии с технологией и достигается высокое каче
ство сборки, обусловленное техническими требованиями. При
соединении, например, валика и втулки сопряжение возможно
лишь в случае определенности базирования обеих деталей, при
котором смещение е осей не превышает наименьшей
величины зазора плюс удвоенная величина фаски валика.
К приспособлениям-зажимам предъявляют следующие основ
ные требования: крепление детали сборочной единицы в приспо
соблении должно быть достаточно надежным и прочным; зажатие
должно осуществляться немногими и простейшими приемами и
возможно быстрее; закрепление не должно деформировать детали
или вызывать повреждение их поверхностей; при необходимости
точной установки деталей зажимы не должны смещать их во время
закрепления.
Универсальные приспособления для закрепления. На сбороч
ных участках многих производств распространенным видом зажим
ных приспособлений являются слесарные тиски. Преимущество
их заключается в том, что они в ряде случае делают излишним из
готовление специальных зажимных приспособлений, особенно
если используются сменные губки, которым придается любая
форма в зависимости от формы зажимаемой детали. Губки изготов
ляют из мягкой стали, латуни, меди, алюминия. Иногда их отли
вают из свинца. Однако обычные слесарные тиски относятся к группе медленно
действующих приспособлений, и при большой расчлененности
процесса сборки вспомогательное время на зажатие и отжатие
может составлять значительную долю основного времени, затра
чиваемого на операцию. Поэтому следует применять быстродей
ствующие тиски.
Существует много разнообразных конструкций таких тисков —
рычажные, эксцентриковые и др. Однако наиболее целесообраз
ными являются конструкции с пневматическим приводом. Время,
требуемое для зажатия, благодаря применению пневматического
зажима значительно сокращается. При использовании, например,
винтового зажима с гаечным ключом для закрепления требуется
4,9 с, эксцентрикового зажима — 1,6 с, а пневматического —
только 0,35 с. Преимущества пневматического зажима: обеспече
ние стабильности закрепления, легкость регулирования, силы за
жатия, освобождение рабочего от утомительных движений, что
способствует повышению производительности труда на сборке.
превышает 0,8—0,85 кгс/см2.
Специальные приспособления для закрепления. Такие при
способления предназначены для закрепления одной детали, сбо
рочной единицы или же группы деталей, сборочных единиц опре
деленной формы. совом производствах.
Эти приспособления бывают стационарные и передвижные.
В зависимости от размеров сборочных единиц их устанавливают
на верстаке или на полу и закрепляют винтовыми, эксцентрико
выми или пневматическими зажимами. Для базирования сбороч
ных единиц применяют призмы, конусные центры, плоские вы
ступы или кольцевые опоры, часто облицованные вкладышами
из мягких сплавов, фибры или кожи.
При конвейерной сборке приспособления для закрепления со
бираемых сборочных единиц устанавливают на тележках или пла
стинах конвейера. Однако при сборке мелких узлов на ленточном
или пластинчатом конвейере нередко используют приспособления-
спутники, которые вместе с узлом снимает сборщик для выполне
ния операции на верстаке, а затем опять возвращает на конвейер.
Зажимные элементы в таких приспособлениях механические бы
стродействующие (рычаги, эксцентрики, клинья).
Пригоночные работы при сборке механизируют главным обра
зом с помощью универсальных и специализированных инструмен
тов с электрическим, пневматическим, реже гидравлическим при
водами. Такие инструменты дают возможность существенно повы
сить производительность труда и качество работ. Механизирован
ные инструменты имеют КПД: 8—11 % с пневматическим приводом,
55—65% с электрическим и около 70% с гидравлическим.
Для местной зачистки закаленных и точно обработанных де
талей используют квадратные, плоские, трехгранные, круглые
или полукруглые абразивные бруски. Работают такими брусками
с применением минерального масла, керосина или скипидара.
После опиливания напильниками поверхности обычно зачи
щают шлифовальными шкурками. При зачистке деталей из стали,
твердой бронзы, ковкого чугуна и других твердых сплавов приме
няют мелкозернистые шкурки номеров 4—6 с электрокорундовым
зерном, для хрупких и мягких металлов — чугуна, бронзы, алю
миниевых сплавов — шкурки номеров 5—10 с карбидокремние
вым зерном. Для очень тонкой зачистки применяют шкурки зер
нистостью Ml 0—М28.
Притирку при сборке применяют в тех случаях, когда необхо
димо получить точный размер деталей за счет снятия очень малого
припуска, или для достижения плотного прилегания поверхностей,
обеспечивающего гидравлическую непроницаемость соединения.
Точность размеров, достигаемая при притирке, до 0,1 мкм.
Притирка , как известно, представляет собой процесс
резания абразивными зернами, находящимися между поверхно
стями притира и детали. Относительное движение поверхностей
притира вызывает вращение зерен абразива, которые внедряются
в притир и в деталь, срезая с их поверхностей микронеровности;
при этом одновременно происходит окисление поверхностей, а
также возникает явление их наклепа.
При притирке обязательно применяют машинное масло, олеиновую кислоту,
керосин, бензин, скипидар, техническое сало и другие смазывающие жидкости,
а также их смеси (например, 70% олеиновой кислоты и 30% керосина).
ПОЛИРОВАНИЕ
Этот вид обработки в процессе сборки обычно производят для
достижения меньшей шероховатости поверхностей, подвергав
шихся опиливанию или зачистке. Припуск под полирование остав
ляется очень небольшой (0,005—0,007 мм). Заглаживание рисок
при полировании поверхностей благотворно сказывается на из
носостойкости деталей. Кроме того, при уменьшении шерохова
тости сокращается поверхность соприкосновения деталей с воз
духом и коррозионными средами, что повышает стойкость полиро
ванной поверхности против коррозии. Полирование позволяет
также обнаружить дефекты поверхностного слоя — трещины, во
лосовины, флокены, которые на грубо обработанной поверхности
часто незаметны.
Процесс полирования осуществляют при помощи вращающихся
со скоростью 30—50 м/с эластичных кругов, на рабочую поверх
ность которых наносится абразивная смесь с жидким наполните-
лем или мастика, состоящая из вяжущего вещества и полироваль
ного порошка. Круги применяют из войлока (сделанного из овечьей
шерсти или в смеси с козьей), хлопчатобумажной ткани, а также
из сульфитцеллюлозной оберточной бумаги. Для получения по
верхности с меньшей шероховатостью применяют круги с графи
товым наполнителем, а также алмазные эластичные полировальные
ленты. Полируют с применением тонких порошков или специаль
ных полировальных паст.
В качестве вяжущего вещества употребляют смесь парафина,
олеина, стеарина, воска, говяжьего сала, вазелина. Для грубого
полирования употребляют окись алюминия, окись железа (кро
кус) и окись хрома, а для самого тонкого полирования — венскую
известь. При грубом полировании применяют составы со смазоч
ной связкой; тонкое полирование производят абразивами без
смазочных наполнителей.
компонентов.
Полирование при обработке деталей осуществляется на спе
циальных полировочных станках. В условиях же сборки, где
объем таких работ небольшой, применяют механизированные
шлифовальные или быстроходные сверлильные машинки, исполь
зуя их или в качестве переносного инструмента или
в качестве верстачной установки . При большем объеме
полировальных работ применяют ручные полировальные машины
с эластичным кругом, работающим торцовой поверхностью .
ШАБРЕНИЕ
Этот метод отделочной обработки состоит в соскабливании
шаберами тонких (около 0,005 мм) слоев металла для получения
ровной поверхности после предварительной обработки ее резцом,
напильником или другим режу
щим инструментом. При шабре
нии металл постепенно сре
зается с участков, соприкаса
ющихся (при пробе на краску1)
с поверхностью, к которой при
гоняется данная деталь. При
последующих пробах эти уча
стки становятся все мельче и
мельче («разбиваются»), пока
не получится «сетка», т. е. до
статочное число пятен сопри
косновения.
Шабрением можно получить
высокую точность: плоскост
ность и прямолинейность до
0,002 мм на длине 1000 мм и до
30 пятен на площади 25x25 мм.
В процессе сборки машин шабрят либо плоские поверхности
деталей (плоскости разъема, направляющие) для обеспечения
особо точных сопряжений, либо цилиндрические поверхности
(вкладыши подшипников, втулки). Часто шабрят также детали,
конструктивные формы которых не позволяют обеспечить требуе
мую точность при обработке на станках.
Шабрить поверхности целесообразно под углом к рискам и
следам, оставшимся от предыдущей обработки. Двигаясь к риске
под углом 30—45°, шабер не делает скачка, и риска быстро исче
зает. В связи с этим в практике получил широкое распростра
нение так называемый шахматный способ шабрения, при котором
шабер движется под углом к образующей поверхности. При вто
ричном проходе шабер направляют под тем же углом к образую
щей, но в другую сторону.
Результаты шабрения определяют обычно или по краске, или
всухую — «на блеск». Последний способ заключается в том, что
при затяжке, например, вкладышей и провертывании вала на два-
три оборота участки касания сопрягающихся поверхностей начи
нают блестеть и становятся заметными. Этот способ дает обычно
лучшие результаты, так как краска может местами залить и не-
соприкасающиеся участки обрабатываемых поверхностей.
После этого опять повторяют операцию притирки.
Плоскости после шабрения проверяют на краску при помощи
точных чугунных поверочных плит. Если детали громоздкие, про
верку ' производят через тела качения — роликовые дорожки.
Качество шабрения детали зависит от назначения соединения и
контролируется числом пятен касания в квадрате со стороной
25 мм и равномерностью их распределения.
Шабрение считается тонким, если число пятен более 22 (Ra =
= 0,08 мкм; по ГОСТ 2789—73); точным, если число пятен 10—■
14 (Ra = 0,63 мкм); чистовым — 6—10 (Ra = 1,25 мкм); и гру
бым — 5—6 на площади 25 X 25 мм.
Шаберы применяют ручные — плоские, канавочные, трехгран
ные, полукруглые, насадочные и др., а также механические.
СВЕРЛЕНИЕ
В процессе сборки отверстия сверлят, когда требуемая точность
достигается проще всего путем обработки двух или большего числа
деталей в сборе ; когда место сверления труднодоступно для обработки на станке, а отверстие небольшого
диаметра и может быть просверлено с помощью механизированного
инструмента; когда отверстие не было предусмотрено при механи
ческой обработке (например, для постановки пробок при обнаруже
нии пористости в литых деталях — в станине, картере, блоке,
в различных корпусах), если это допускается техническими требо
ваниями.
Сборочные цехи для таких операций обычно имеют несколько
сверлильных станков, установленных вблизи линии сборки. Для
отверстий диаметром до 10—12 мм применяют переносные приспо
собления или небольшие станки на колонках, а для более круп
ных — станки на фундаменте.
ГИБОЧНЫЕ РАБОТЫ
Соединения, осуществляемые с помощью гибки, имеют в кон
струкциях машин небольшое распространение. Гибка в этом случае обычно
выполняется ручным инструментом или с помощью легкого пресса.
Гибка труб вручную — малопроизводительная и тяжелая работа. Поэтому
там, где это возможно, целесообразно применять механические или пневматиче
ские приспособления и трубогибочные станки. В этих случаях гибка труб осуще
ствляется по принципу штампования или обкатывания роликами. Трубу
укладывают в разъемный штамп-шаблон 1, установленный на пневма
тическом прессе, а при опускании штока 2 выгибают в соответствии с формой
ручья штампа-шаблона. При больших радиусах изгиба и значительных диаметрах
труб штамп-шаблон делают с раздвижной матрицей, состоящей из двух гибочных
вкладышей .
Трубы диаметром более 20 мм гнут после наполнения их
песком или расплавленной канифолью. Песок должен быть мел
ким и сухим, и чем плотнее он будет утрамбован, тем менее вероят
но появление на трубе морщин и вмятин при изгибе.
Стальные трубы диаметром до 10 мм гнут без нагрева и без на
полнителя; трубы больших размеров гнут в горячем состоянии.
Нагревать трубу необходимо только в месте изгиба на длине,
приблизительно равной α/15d, где α —внешний угол изгиба, a d —
наружный диаметр трубы. Стальные трубы нагревают до ярко-
красного цвета, алюминиевые или дюралюминиевые — до тех пор,
пока от прикосновения к трубе не начинает обугливаться бумага.
Медные трубы нагревать необязательно, но эти трубы перед гиб
кой должны быть отожжены, т. е. нагреты и замочены в холодной
воде.
Мойка. Сборочная единица, требующая промывки,
укрепляется на кассете и вводится в шкаф. Затем включается
насос, и моющий раствор поступает в каналы и отверстия.
Снабжение таких шкафов моющим раствором централизовано;
подача производится по трубам, проложенным под полом в спе
циальных крытых траншеях.
В серийном и массовом производствах используют специаль
ные моечные машины (однокамерные, двухкамерные и трехкамер
ные), в которых процесс мойки деталей и сборочных единиц
осуществляется в закрытом пространстве без участия рабочего.
В некоторых машинах детали после мойки охлаждаются.
В массовом производстве для мойки однотипных сборочных
единиц, используемых в больших количествах, применяют меха
низированные установки специального назначения.
Сборка передач основных агрегатов. Методы соединений, сварные и паяные соединения. Сборка зубчатых и червячных передач. Сборка подшипниковых узлов. Сборка цепных передач. Сборка ременных передач. Сборка передач с использованием шпоночных и шлицевых соединений. Балансировка деталей перед сборкой.
СБОРКА РЕЗЬБОВЫХ СОЕДИНЕНИЙ
Резьбовые соединения в конструкциях машин составляют 15—
25% от общего количества соединений. Такая распрсстраненнссть
объясняется их простотой и надежностью, удобством регулиро
вания затяжки, а также возможностью разборки и повторной
сборки соединения без замены детали.
Широко применяются следующие разновидности резьбовых соединений:
для обеспечения неподвижности и прочности сопрягаемых деталей; для обеспече
ния прочности и герметичности; для правильности установки сопрягаемых дета
лей; для регулирования взаимного положения деталей.
Процесс сборки резьбсвсго соединения в общем случае скла
дывается из следующих элементов; подачи деталей, установки
их и предварительного ввертывания (наживления), подвода и
установки инструмента, завинчивания, затяжки, отвода инстру
мента, дотяжхи, шплинтовки или выполнения иного процесса,
необходимого для предохранения от самоотвинчивания. Из техно
логических работ в процессе завинчивания 12—17% идет на пред
варительное ввертывание, 18—20% на затяжку и 5—8% на до-
тяжку (от всего времени сборки соединения). В случае автомати
ческой сборки все эти три элемента процесса выполняются последо
вательно одним инструментом. Однако при механизированном
выполнении работ предварительное ввертывание часто производят
вручную.
СБОРКА БОЛТОВЫХ И ВИНТОВЫХ СОЕДИНЕНИЙ
В конструкциях машин применяются болтовые и винтовые
соединения, собираемые без затяжки и с предварительной затяж
кой. Область использования соединений первого типа крайне
ограничена, соединения же второго типа распространены чрез
вычайно широко.
Предварительная затяжка соединений при сборке играет
существенную роль в повышении долговечности работы сборочных
единиц или машины и должна быть такой, чтобы упругие деформа
ции деталей соединения при установившемся режиме работы
машины или механизма находились' в определенных пределах,
обусловленных конструктивными особенностями. Степень пред
варительной затяжки болта или винта зависит от сил, нагру
жающих соединение.
ПОСТАНОВКА РЕЗЬБОВЫХ ВТУЛОК И ЗАГЛУШЕК
В часто разбираемых резьбовых соединениях для уменьшения
износа резьбы корпуса в него ввертывают втулки (латунные)
с наружной и внутренней резьбами . Чтобы втулки
не вывинчивались из гнезда, их ставят с натягом и расчеканивают
или раскернивают. Для облегчения постановки таких втулок
необходимо, чтобы отверстие в корпусе имело небольшую фаску.
К соединению втулки с корпусом нередко предъявляется еще
требование герметичности, так как жидкости (горячее масло, вода,
бензин) и газы протекают под давлением и легко просачиваются
через неплотности.
Герметичности достигают торцовым уплотнением. Поэтому
очень важно, чтобы поверхности торцов сопрягаемых корпуса и
втулки были перпендикулярны оси резьбы. Для уплотнения со
единений под торец детали ставят прокладку 1 из
легкодеформируемого материала — отожженную медную, медно
асбестовую, из паронита и др. Если обе торцовые поверхности
сопрягаемых деталей перпендикулярны оси резьбы и достаточно
чисты (нет глубоких царапин, рисок), то прокладки выдержи
вают даже высокие давления. Однако при каждой переборке
в ответственных соединениях прокладки следует менять.
Заглушки — стальные, бронзовые латунные, алюминиевые
обычно должны препятствовать просачиванию жидко
стей при наличии разности давления. Если заглушки не вывин
чиваются при разборке, сопряжения часто уплотняют в резьбе белилами или суриком. Однако засохшие белила и сурик сильно
затрудняют отвертывание заглушек, так что иногда во избежание
порчи резьбы основной детали их приходится даже высверливать.
Такие уплотнения испытывают на герметичность под давлением
жидкости, несколько превосходящим рабочее давление, причем
если потребуется заменить заглушку, это необходимо сделать до
того, как засохнут белила.
СБОРКА СОЕДИНЕНИЙ СО ШПОНКАМИ
Точность сборки соединения с одной или несколькими шпон
ками обеспечивается изготовлением его элементов по размерам
с допусками.
Размеры шпонок выполняют по системе вала, так как посадки
в пазах вала и ступицы, как правило, различны. При неподвиж
ных соединениях шпонку устанавливают в паз вала плотно или
даже с натягом, а в пазу ступицы посадка создается более сво
бодная.
Посадку Р/h
шпонки в пазу втулки применяют обычно тогда,
когда втулка, передавая крутящий момент, должна свободно
перемещаться вдоль оси вала. При монтаже на вал охватывающей
детали необходимо следить, чтобы она не «сидела» на шпонке,
т. е. центрировалась бы исключительно на цилиндрической или
конической поверхности вала. При этом между верхней плоскостью
шпонки и впадиной паза втулки должен быть достаточный зазор.
Правильная сборка соединений со шпонками в значительной
мере обеспечивает работоспособность и надежность работы сбороч
ной единицы. Большое значение при этом прежде всего имеет
строгое соблюдение посадок в сопряжениях шпонки с валом
и охватывающей деталью. Увеличенные зазоры —•
одна из основных причин нарушения распределения нагрузок,
смятия и разрушения шпонки.
Смещение осей шпоночных пазов в валу и втулке
также приводит к неправильному положению
шпонки и несовпадению боковых поверхностей
шпонки и паза .
триваемые для этой цели отверстия. -
В условиях крупносерийного и массового производства приз
матические и сегментные шпонки обычно не пригоняют (в процессе
самой сборки). В единичном и мелкосерийном производствах
такие работы допускаются, особенно когда к шпоночным соеди
нениям предъявляют особые требования в отношении точности.
Шпоночные соединения имеют недостатки, заключающиеся
в том, что при передаче больших и особенно знакопеременных
крутящих моментов шпоночный паз на валу приходится делать
глубоким, при этом снижается прочность вала. При боковых
зазорах между шпонкой и пазом охватывающей детали паз посте
пенно разрабатывается, что может вызвать срез шпонки или ее
деформацию. Учитывая это, особые требования предъявляют
к точности центрирования шпоночного соединения и плотности
посадки на валу охватывающей детали. В конструкциях машин
начинают применяться разнообразные виды бесшпоночных соеди
нений. Один из таких видов — соединение упругопластичными
втулками .
СБОРКА ШЛИЦЕВЫХ СОЕДИНЕНИЙ
Соединение деталей по шлицам позволяет обеспечить более
точное центрирование, чем при соединении деталей со шпонкой,
а также повышенную прочность. Распространены прямобочные,
эвольвентные и треугольные шлицевые цилиндрические соедине
ния. В прямобочном шлицевом соединении охватывающая деталь
может быть центрирована по наружной поверхности шлицев, по
поверхности впадин или по боковым сторонам шлицев. В соеди
нениях с эвольвентными шлицами центрирование осуществляется
профилями зубьев или по наружной поверхности шлицев. При
треугольных шлицах детали центрируются по боковым профилям
шлицев. В зависимости от применяемой посадки центрирующих поверх
ностей шлицевые соединения можно отнести к одной из следу
ющих групп: тугоразъемные, легкоразъемные и подвижные.
При сборке шлицевых соединений полная взаимозаменяемость
даже в условиях массового производства обычно не достигается
из-за весьма малых зазоров, выдерживаемых в центрирующих
сопряжениях.
сопряжениях.
Сборку шлицевых соединений начинают с осмотра состояния шлицев обеих
деталей. Даже незначительные забоины, задиры или заусенцы в шлицевом соеди
нении не допускаются. Особое внимание уделяют осмотру внешних фасок и за
круглений внутренних углов шлицев, так как при неправильном выполнении
этих элементов возможно заедание на шлицах при сборке соединения. В туго
разъемных соединениях охватывающую деталь обычно напрессовы
вают на вал при помощи специального приспособления или на прессе.
Собирать такие соединения, применяя молоток, не рекомендуется. Нерав
номерные удары могут вызвать перекос охватывающей детали на шлицах и даже
задир их. При очень тугих шлицевых соединениях целесообразно охватывающую
деталь перед запрессовкой нагреть до 80—120° С.
УСТАНОВКА ПОДШИПНИКОВ СКОЛЬЖЕНИЯ
В КОРПУСЕ
Последовательность установки подшипников скольжения
в корпусе зависит от конструкции подшипников, а также всей со
бираемой сборочной единицы. Подшипники скольжения могут
быть цельными и разъемными. В первом случае подшипник пред
ставляет собой втулку, изготовленную из антифрикционного
материала, запрессовываемую в корпус. Во втором случае под
шипник состоит из двух частей — вкладышей с диаметральным
разъемом.
Процесс установки втулки в корпусе включает ее запрессовку,
закрепление от провертывания и подгонку отверстия.
Запрессовку в зависимости от размеров втулки и натяга в сопря
жении производят при обычной температуре, с нагревом или же
с охлаждением самой втулки.
Простейший способ запрессовки втулки в корпус ■— при по
мощи обычной универсальной выколотки и молотка. Этот способ,
широко распространенный в индивидуальном и мелкосерийном
производстве, дает удовлетворительные результаты лишь при ма
лых натягах в сопряжении, относительно большой толщине сте
нок втулки и при тщательном выполнении операции. Направле
ние движения при запрессовке создается здесь только отверстием
в корпусе, поэтому большое значение имеет правильная первона
чальная установка втулки, предотвращающая ее перекос, дефор
мацию и задир поверхности корпуса.
Операция запрессовки значительно упрощается применением
несложных приспособлений (рис. 258), которые обеспечивают
втулке направление и предотвращают ее перекашивание. Однако
диаметр втулки при этом способе запрессовки уменьшается, воз
можно также искажение ее формы. Поэтому при относительно
больших натягах, во избежание перекосов и сдавливания втулок
(особенно при монтаже тонкостенных втулок), их при запрессовке
необходимо более точно центрировать относительно отверстия
в корпусе.
Перед запрессовкой втул
ка и отверстие корпуса
должны быть тщательно ос
мотрены, острые углы на
торцах зачищены, а поверх
ности сопряжения протерты.
Часто при больших натягах во избежание задира сопрягаемые
поверхности деталей смазывают чистым машинным маслом или
другими смазками.
При установке втулок с нагревом охватывающей детали послед
нюю помещают в электрическую печь или ванну с горячим маслом.
Время выдержки зависит от формы, массы и материала детали.
Запрессовку втулки в нагретый корпус следует производить по
возможности быстро, так как втулка будет нагреваться и расши
ряться, что усложнит операцию. Если втулка идет неправильно
или деформируется, запрессовку надо прекратить, а втулку при
помощи выколотки аккуратно выпрессовать, установить причину
погрешности и устранить ее.
Необходимо иметь в виду, что диаметр отверстия втулки после
ее запрессовки уменьшается. Особенно это ощутимо при посадках со значительными натягами .
Как уже отмечалось, тол
стостенные вкладыши можно
пригонять в процессе сборки по
месту или они могут быть вза
имозаменяемыми. В первом слу
чае поверхности трения оконча
тельно обрабатывают после ус
тановки вкладышей в постели.
Требуемые размеры отверстия
получают обычно путем одно
временного развертывания под
шипников при одной установке
приспособления. При этом воз
можные деформации вкладышей
до их пригонки не оказывают
влияния на состояние рабочей
поверхности.
ности подшипника.
Надлежащую плотность соприкосновения невзаимозаменяемых
вкладышей с постелью и крышкой обеспечивают иногда увеличен
ными натягами, чего при взаимозаменяемых вкладышах по ука
занным выше причинам допустить нельзя. Следовательно, требо
вания к качеству подбора и установки взаимозаменяемых толсто
стенных вкладышей должны быть более жесткими. Одновременно
необходимо учитывать, что крышка подшипника при затяжке гаек
тоже деформируется.
Эти деформации крышки могут нарушить нормальное положение
вкладыша и вызвать искажение формы отверстия подшипника.
Ограничить влияние этих погрешностей можно тщательным под
бором деталей в пределах допустимых натягов, соблюдением после
довательности и требуемой степени затяжки гаек, крепящих
крышки, а также строгим контролем подшипниковых сборочных
единиц после сборки.
ческая поверхность пальца.
СБОРКА СБОРОЧНЫХ ЕДИНИЦ С ПОДШИПНИКАМИ
КАЧЕНИЯ
Подшипники качения монтируют в сборочной единице по
двум неподвижным посадкам — внутреннего кольца с валом и
наружного кольца с корпусом — обычно без специальных креп
лений, препятствующих проворачиванию.
Напрессовка подшипника качения на вал или установка его
с натягом в отверстие корпуса вызывают деформацию колец:
диаметр внутреннего кольца увеличивается, а наружного умень
шается.
Таким образом, если оба кольца подшипника смонтировать
с натягом, то вследствие расширения внутреннего и сжатия на
ружного колец шарики или ролики могут быть защемлены, так
как радиальный зазор между ними и кольцами до установки под
шипника чрезвычайно мал (для подшипника среднего размера
и точности зазор в пределах 5—25 мкм).
Поэтому характер обеих посадок, как правило, различный.
Кроме того, внутреннее и наружное кольца подшипника, находя
щиеся под действием постоянной радиальной нагрузки, работают
в разных условиях. Так как одно из колец подвижно, то износ
его желобка происходит равномерно. Неподвижное же кольцо
воспринимает действие нагрузки все время одним и тем же неболь
шим участком желобка, который интенсивно изнашивается. Для
уменьшения этого износа желательно, чтобы при сборке в сочле
нении неподвижного кольца с корпусом или валом была достигнута
посадка, позволяющая этому кольцу незначительно поворачива
ться. Иными словами, при постоянно действующей нагрузке вра
щающееся кольцо подшипника должно быть сочленено с деталью
сборочной единицы, безусловно, неподвижно, кольцо же невра-
щающееся должно получить более слабую посадку, дающую
возможность проворачивать его от руки в ненагруженном со
стоянии.
межуточной детали.
Для осуществления надежного сопряжения подшипника с ва
лом и корпусом посадочные места должны быть обработаны
(быть чистыми, гладкими, без рисок, задиров и коррозионных
пятен). Шероховатость посадочных поверхностей для высоко
точных подшипников должна соответствовать Ra = 1,25-4-0,32 мкм,
для менее точных Rz = 20 мкм, Ra = 1,25 мкм, а торцов заплечи
ков валов и корпусов Rz = 20 мкм, Ra = 1,25 мкм.
Допустимые отклонения от правильной геометрической формы
мест посадки шарико- и роликоподшипников на валах и в корпу
сах следующие: овальность и конусность — не более 0,5 допуска
на диаметр, а для точных подшипников классов А и С — не более
0,25 допуска; биение заплечика для подшипников нормальной и
повышенной точности 0,02—0,03 мм на валу и 0,04—0,07 мм
в отверстии корпуса.
Контроль производится индикатором или миниметром.
Сборку сборочной единицы вал — подшипник качения осуще
ствляют следующим образом. Подшипник тщательно промывают
в 6%-ном растворе масла, в бензине или в горячих (75—85°С)
антикоррозионных водных растворах.
В хорошо промытом подшипнике наружное кольцо легко и
равномерно вращается. Проверку ведут, удерживая подшипник
за внутреннее кольцо в горизонтальном положении.
Далее, промытый подшипник нагревают в масляной ванне в те
чение 15—20 мин и после этого напрессовывают на вал.
Обычно температура нагрева подшипников при сборке назна
чается в пределах 60—100° С. Подшипники целесообразно нагре
вать в электрованне с точным контролем температуры масла.
Нагретый подшипник устанавливают на вал и доводят до места
небольшим осевым усилием. При этом сторона подшипника, на
которой нанесено заводское клеймо, должна быть снаружи.
Операцию напрессовки необходимо обязательно осуществлять
с применением оправок. Наносить удары непосредственно по
подшипнику нельзя, так как при этом могут быть повреждены
кольца, поломаны шарики и т. д.
Во избежание перекоса подшипника при его запрессовке
целесообразно применять подставки, обеспечивающие хорошее
базирование деталей сборочной единицы .
зазоров.
Установку подшипника в корпусе, если его наружное кольцо
запрессовывают в отверстие, производят так же, как и монтаж
подшипника на валу, только нагревают при этом корпус или охлаждают подшипник. Для охлаждения обычно используют
сухой лед. Сборку производят с помощью специальных оправок
и приспособлений для запрессовки, обеспечивающих удобную
установку и закрепление собираемой сборочной единицы
(рис. 320). Поэтому в значительной мере устраняется возможность
появления брака из-за перекосов при запрессовке и ускоряется
процесс сборки.
Для запрессовки подшипника качения в корпус требуются
сравнительно небольшие силы. Подшипники с внешним диаметром
наружного кольца 80—130 мм запрессовывают силой 400—450 кгс.
Однако при плохом центрировании и даже незначительных пере
косах подшипника сила, необходимая для запрессовки, возрастает
в несколько раз. В связи с этим к конструкции приспособления
предъявляются жесткие требования в части обеспечения базиро
вания подшипника при его установке .
Крупногабаритные подшипники качения, устанавливаемые
в разъемные корпуса, часто проверяют на прилегание наружного
кольца к посадочной поверхности по краске. Прилегание счита
ется хорошим, если отпечатки краски составляют не менее 75%
площади поверхности. При плохом
прилегании возможно пришабри-
вание посадочных мест. В местах
разъема отверстие в корпусе рас-
шабривают (рис. 321) для предот
вращения сжатия кольца подшип
ника. Для подшипников диамет
ром 120—260 мм а = 0,15 мм;
b — 15 мм.
СБОРКА ЗУБЧАТЫХ И ЧЕРВЯЧНЫХ ПЕРЕДАЧ
В конструкциях машин и механизмов наиболее широко рас
пространены 1 зубчатые передачи со следующими видами колес:
цилиндрическими — прямозубыми, косозубыми, шевронными, вин товыми и коническими — с прямыми, криволинейными и косыми
зубьями. Червячные передачи применяют с цилиндрическим (ар
химедовым) и глобоидными червяками.
Для зубчатых цилиндрических и конических передач, а также
червячных передач государственными стандартами устанавливает
ся двенадцать ^степеней точности, обозначаемых в порядке убыва
ния точности степенями 1—12.
Для каждой степени точности зубчатых передач государствен
ным стандартом установлены нормы: кинематической точности ко
леса, плавности^работы_колеса_и контакта зубьев. Нормы кинема
тической точности определяют полную погрешность угла поворота
зубчатых колес за оборот.
Нормы плавности работы колеса определяют величину состав
ляющих полной погрешности угла_поворота зубчатого колеса.
Нормы контакта зубьев определяют точность соблюдения отно
сительных размеров пятна контакта сопряженных зубьев колес
в передаче. Независимо от степени точности колес и передач
устанавливают нормы бокового зазора.
Основными являются величины минимального гарантирован
ного бокового зазора (при сопряжении В), обеспечивающего ком
пенсацию уменьшения бокового зазора от нагрева передачи при
разности температур зубчатой передачи и корпуса 25° и равенстве
коэффициентов линейного расширения. Нормы гарантированного
бокового зазора можно изменять. ГГри_изменении этих норм пред
почтительно применять одно из следующих сопряжений: Я — с ну
левым гарантированным зазором, Е, Д — с уменьшенным гаран
тированным зазором, А — с увеличенным гарантированным за
зором.
Важным фактором, определяющим эксплуатационное качество
зубчатой передачи, является боковой зазор между зубьями колес.
Боковой зазор измеряется для цилиндрических колес в сечении,
перпендикулярном к направлению зубьев, в плоскости, касатель
ной к основным цилиндрам, для конических — по нормали к по
верхностям зубьев у большего основания делительного конуса.
Зазор в зацеплении является необходимым для компенсации
возможных ошибок в размерах зубьев, неточности расстояния ме
жду осями зубчатых колес, изменения размеров и формы зубьев
при нагреве в процессе работы передачи. Но вместе с этим зазор
является причиной возникновения ударов и дополнительного из
носа зубьев при работе зубчатых колес, а также причиной появле
ния в передаче так называемого мертвого хода, когда отклонение
на некоторый угол ведущего зубчатого колеса не вызывает пово
рота ведомого. Таким образом, зазор в зацеплении должен быть
таким, чтобы при работе передачи не произошло заклинивания
зубьев, не нарушилась плавность вращения и в то же время мерт
вый ход был возможно меньше.
Установку колес производят посредством пресса или же вруч
ную при помощи специальной мягкой оправки и молотка. Послед
ний способ применяют в мелкосерийном производстве лишь для
зубчатых колес малого размера, термически не обработанных,
монтируемых с небольшими натягами. Зубчатые колеса большого
размера, термически обработанные, а также устанавливаемые со
значительными натягами, следует непрессовывать только посред
ством пресса, с применением специальных приспособлений. При
мером таких приспособлений могут быть пневматические или гид равлические скобы. Основным требованием, предъявляемым к при
способлениям, является обеспечение точного направления напрес
совываемого зубчатого колеса и, таким образом, устранение пере
коса его на посадочной шейке.
При больших диаметрах зубчатых колес целесообразно при
, напрессовке применять приспособления с направляющими план
ками или стержнями. В таком приспособлении (рис. 391) зубчатое
колесо устанавливают или укрепляют на упорной доске 1, кото
рая движется по направляющим стержням 2. В результате этого
осуществляют точное центрирование колеса при запрессовке,
особенно в начале ее.
В ряде случаев воспользоваться универсальными прессами
не представляется возможным, например при установке зубчатых
колес на длинных валах. Тогда целесообразно для напрессовки
применить специальные несложные установки, имеющие привод
от пневматической сети, насосных станций или пневмогидравли-
ческих устройств.
Необходимо предотвращать перекосы зубчатых колес не только в
процессе монтажа, ной при их снятии с валов. Эти операции часто
приходится осуществлять в процессе сборки, когда возникает не
обходимость повернуть колесо относительно вала или устранить
какую-либо другую погрешность. Снимают зубчатые колеса с вала
также с помощью пресса или съемниками. При использовании
пресса колесо обычно опирают на его торцовую плоскость, а цен
трирование обеспечивается по наружной цилиндрической поверх
ности зубьев или тремя бобышками, входящими во впадины между
ними. При установке на шлицевой вал несимметричных прямозубых
колес возможен их перекос вследствие зазоров в шлицевом соеди
нении. Тогда под действием крутящего момента при работе пере
дачи возникают дополнительные осевые силы, сдвигающие колесо.
Вследствие этого в сопряжении ступицы колеса со шлицами вала
следует выдерживать минимальные зазоры.
Перед напрессовкой зубчатого колеса на вал необходимо обра
тить внимание на состояние поверхностей отверстия и посадочной
шейки вала. Если зубчатое колесо напрессовывается до упора, то
фаска на зубчатом колесе должна быть достаточной величины во
избежание упора торца его в переднюю поверхность вала.
Положение ведущего и ведомого валов в корпусе при сборке
зубчатой передачи имеет существенное значение. Для правильного
зацепления цилиндрических зубчатых колес оси их валов должны
лежать в одной плоскости и быть параллельны, а расстояние между
ними должно быть равно полусумме диаметров начальных окруж
ностей зацепляющихся зубчатых колес. Допуски на межосевое
расстояние устанавливают в соответствии с ГОСТ 1643—72 в за
висимости от вида сопряжения .
СБОРКА ЦЕПНЫХ ПЕРЕДАЧ
Передача вращательного движения с одного вала на другой,
параллельный ему вал, при больших межосевых расстояниях
часто осуществляется в машинах и механизмах при помощи цеп
ных передач.
В зависимости от назна
чения в машиностроении при
меняются^ цепи: пластинчато
зубчатые,% втулочные, вту
лочно-роликовые, пластинча
тые блочные со сплошными
звеньями и фасоннозвен
ные.
Пластинчато-зубчатые це
пи, называемые иногда бес
шумными, применяют для
передачи сравнительно боль
ших мощностей при скоро
стях от 3 до 25 м/с. При ра
боте цепь сопрягается со звездочкой, имеющей трапецеидальные зубья с углами впадин
от 32 до ЪТ (при числах зубьев от 13 до 120). Пластинчатые втулочно-роликовые цепи (однорядные и много
рядные) применяют для передачи движения при скоростях от 1
до 15 м/с. Фасоннозвенные цепи широко распространены в тихо
ходных передачах при скоростях до 3—4 м/с.
Втулочно-роликовые и фасоннозвенные цепи работают в сопря
жении со звездочками, профили зубьев которых очерчиваются
дугами окружностей.
Сборка цепной передачи состоит в установке и закреплении
звездочек на вал ах, надевании цепи и регулировании. Установку
звездочек на валах при обычном креплении с помощью шпонок
осуществляют так ж?, как и установку зубчатых колес. После
закрепления звездочки на валу ее следует проверить на радиаль
ное и торцовое биение. Для правильной работьГ цепной передачи оси звездочек должны
быть параллельны. Положение звездочек проверяют по уровню,
измерением межосевых расстояний и другими методами контроля
на параллельность осей валов.
лельности осей'валов (звездочек) вызывает появление в передаче
дополнительной силы, сдвигающей звездочки. При этом наиболее
неблагоприятным является случай, когда оси обоих валов пере
кошены «внутрь» передачи. Для устранения смещения конструкцией часто предусматри
вается возможность регулирования положения одной из звездочек
с последующим закреплением ее винтом. Для втулочно-роликовой цепи соединительное звено предста
вляет собой два валика, скрепленных пластинками (рис. 432, а).
Таким звеном можно соединить только цепь, имеющую четное
число звеньев. Для соединения концов цепи одну пластинку сни
мают, валики вставляют в отверстия втулок конечных звеньев,
затем устанавливают снятую ранее пластинку и валики зашплин-
товывают. Если нужно собрать цепь с нечетным числом щагов, то вво
дится переходное звено (рис. 432, б). По такой же схеме при
помощи соединительных и переходных звеньев собирают пластин
чатые зубчатые цепи.
Концы втулочно-роликовой цепи соединяют либо на верстаке,
либо непосредственно на сборочной единице. На верстаке соби
рают цепи в том случае, когда звездочки расположены на концах
валов и цепь может быть на них надета после соединения ее кон
цов. Если же звездочки закрыты, то соединение концов цепи
производят на собираемом узле. При этом нередко по конструктив
ным условиям цепь предварительно должна быть установлена на
звездочки. В таких случаях концы цепи необходимо стягивать
при помощи специальных стяжек .
Пластинчатые зубчатые цепи также вначале надевают на звез
дочки, а затем стягивают стяжкой .
Надевать цепи на звездочки необходимо таким образом, чтобы
крючки звеньев были направлены в сторону движения цепи,
а не наоборот (рис. 434). Тогда звенья цепи при сбегании ее со
звездочки вращаются в шарнире крючка, а последний не трется
о поверхность зуба звездочки. Это уменьшает износ звена и звез
дочки.
Натяжение ветвей в правильно собранной цепной передаче
должно быть строго определенным. Недостаточное натяжение
ветви ухудшает ее набегание на ведомую звездочку, а излишнее
натяжение, кроме этого дефекта, вызывает еще усиленный износ
зубьев звездочек, подшипников опор и самой цепи.
БАЛАНСИРОВКА СБОРОЧНЫХ ЕДИНИЦ
И МАШИН В СБОРЕ
Неуравновешенность вращающейся детали или сборочной еди
ницы является причиной появления в машине при ее работе дина
мических сил, которые дополнительно нагружают опоры, повы
шают интенсивность износа подшипников, а также вызывают
вибрационные явления и связанные с этим усталостные напряже
ния в деталях. Часто неуравновешенность может сказаться на
основных показателях качества машины.
Балансировку деталей обычно осуще
ствляют в механических цехах при их
изготовлении. Однако после сборки сбо
рочных единиц, в которые входят отба
лансированные детали, возникает необхо
димость повторной их проверки, так как
смещение одной из деталей, даже в преде
лах зазоров, предусмотренных чертежом,
нередко может вызвать значительную
неуравновешенность всей сборочной еди
ницы. В связи с этим в технологических
процессах сборки многих изделий балан
сировка является обязательной опера
цией.
цией.
Балансировка окончательно собранных сборочных единиц
на специальных установках или балансировочных станках пред
ставляет собой контрольно-пригоночную операцию, которая не
редко не включается в поток сборки, а выполняется на отдельном
участке. Тем не менее балансировочные работы составляют важ
нейшую часть процесса сборки.
Точность уравновешивания, допустимые дисбалансы устанавли
ваются техническими требованиями, исходя из особенностей
конструкции и назначения сборочных единиц и деталей, скорости
их вращения, допустимых вибраций машины, необходимой на
дежности и долговечности, возможных физиологических ощуще
ний оператора, работающего на машине в условиях эксплуатации,
и пр.
Например, статическую несбалансированность дисков ротора
турбин назнэчают из условия, чтобы неуравновешенная сила
не превышала 5% веса диска. Точность динамической баланси
ровки собранного ротора часто устанавливают такой, чтобы
возмущающая сила на каждом подшипнике не превышала 1—2%
массы ротора.
В процессе сборки обычно производят статическую и динами
ческую балансировки сборочных единиц — роторов. Статическую
балансировку производят на горизонтальных параллелях
, на дисковых роликах , на сферической
пяте , на весах и на специальных станках.
Статическая балансировка сборочных единиц и деталей состоит
в определении величины дисбаланса и его устранении путем пере
становки отдельных элементов конструкции, удаления в нужных
местах сверлением, шлифованием, растачиванием части металла
или, наоборот, добавлением соответствующей его массы сваркой,
приклепыванием и пр., а также комбинированием этих способов.
ролика; а — угол между роликами (см. рис. 437, б).
Методы статической балансировки применяют в мелкосерийном
и единичном производствах. В условиях крупносерийного и мас
сового производств используют более точный и производитель
ный метод статической балансировки в динамическом режиме.
В этом случае балансируемая сборочная единица — ротор вра
щается с повышенной скоростью. Используемые балансировочные
станки имеют высокую производительность, обеспечивают оста
точный дисбаланс не более 0,5—1 гс- см на 1 кг массы баланси
руемой сборочной единицы, при этом устранение дисбаланса
производится без съема детали со станка, часто автоматически.
Эти станки просты в эксплуатации, не требуют специальных
фундаментов.
Для уравновешивания вращающихся сборочных единиц, име
ющих большую сравнительно с диаметром длину (например,
шпиндели, роторы турбин, коленчатые валы), одной статической
балансировки недостаточно. Такие сборочные единицы подвер
гают динамической балансировке.
При динамической балансировке в сборе искусственно создается система
сил, в которой равнодействующие, а также моменты равны нулю или постоянны
по величине и направлению.
В массовом производстве получают распространение автомати
зированные балансировочные машины, в которых процессы соеди
нения балансируемой детали (сборочной единицы) с приводом,
определения неуравновешенности, передача этих результатов
запоминающим устройствам, ориентация детали и режущего
инструмента и операция устранения дисбаланса производятся
автоматически. В некоторых таких автоматах процессы определе
ния неуравновешенности и ее устранения совмещены (однопсзи-
ционные автоматы); в двухпозиционных же автоматах эти про
цессы разделены.
Для уравновешивания коленчатых валов по проекту ЭНИМСа
создана автоматическая балансировочная линия, оснащенная кон
трольно-измерительной аппаратурой, включающей блоки па
мяти, решающее и коррекционные устройства и т. д. Производи
тельность этой линии — одно изделие в минуту. Она дает воз
можность снизить неуравновешенность в 50 раз.
В целях проведения динамической балансировки на повышен
ных скоростях и сокращения времени на операцию в настоящее
время ведутся опыты по применению кратковременных (менее
1 м-с) импульсов лазера для устранения излишнего металла без
остановки уравновешиваемой детали (сборочной единицы).
Дата добавления: 2022-01-22; просмотров: 28; Мы поможем в написании вашей работы! |
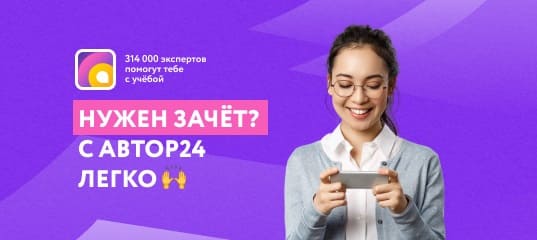
Мы поможем в написании ваших работ!