Оформление технической и технологической документации.
Тема 1.1 Технологические процессы изготовления автотракторной техники Основы технологии машиностроения.
Понятие о технологической дисциплине
Типовые технологические процессы обработки деталей.
Типовые технологические процессы изготовления, применяемое оборудование и оснастка.
Конструктивные особенности, служебное назначение и технические требования, предъявляемые к поршням, гильзам, шатунам двигателей. Материал и заготовки.
К деталям класса рычагов относятся собственно рычаги, тяги, серьги, вилки, балансиры, шатуны.
Рычаги являются звеньями системы машин, аппаратов, приборов, приспособлений. Совершая качательное или враща-
тельное движение, рычаги передают необходимые силы и движения сопряженным деталям, заставляя их выполнять требуе-
мые перемещения с надлежащей скоростью. В других случаях рычаги, например прихваты, остаются неподвижными и фик-
сируют относительное положение сопряженных деталей.
Детали класса рычагов имеют два отверстия или больше, оси которых расположены параллельно или под прямым уг-
лом. Тело рычагов представляет собой стержень, не обладающий достаточной жесткостью. В деталях этого класса, кроме
основных отверстий, обрабатываются шпоночные или шлицевые пары, крепежные отверстия и прорези в головках. Стержни
|
|
рычагов часто не обрабатывают.
Значительное разнообразие конструкций рычагов вызывает необходимость их классификации с целью сужения типовых
технологических процессов. С этой целью рекомендуется следующая классификация:
1 Рычаги, у которых торцы втулок имеют общую плоскость или их торцы лежат в одной плоскости.
2 Рычаги, у которых торцы втулок лежат в разных плоскостях.
3 Рычаги, у которых имеется длинная втулка с отверстием и значительно более короткие втулки.
Технологические задачи
Точности размеров. Отверстия – основные и вспомогательные базы, поверхностями которых рычаги и вилки сопряга-
ются с валиками, проектируют у рычагов и шарнирных вилок по Н7...Н9, а у вилок переключения для уменьшения перекоса
при осевом перемещении – по Н7...Н8. Точность расстояний между параллельными исполнительными поверхностями вилок
переключения назначают по IТ10...IТ12. Расстояние между осями отверстий основных и вспомогательных баз рычагов
должны соответствовать расчетным; допускаемые отклонения в зависимости от требуемой точности колеблются от ± 0,025
до + 0,1 мм.
Точность формы. В большинстве случаев особых требований к точности формы поверхностей не предъявляется, т.е.
|
|
погрешность формы не должна превышать допуск на размер или, в зависимости от условий эксплуатации, погрешности
формы не должны превышать от 40 до 60 % от поля допуска на соответствующий размер.
Точность взаимного расположения. Для хорошего прилегания поверхностей отверстий к сопряженным деталям оси по-
верхностей отверстий – вспомогательных баз рычагов должны быть параллельны осям поверхностей отверстий – основных
баз с допускаемыми отклонениями (0,05...0,3)/100 мм.
У рычагов, имеющих плоские обработанные поверхности, в некоторых случаях (по служебному назначению) задается
перпендикулярность осей отверстий относительно этих плоскостей с допускаемыми отклонениями (0,1...0,3)/100.
Качество поверхностного слоя. Шероховатость поверхности отверстий у рычагов и вилок в зависимости от точности диа-
метров отверстий назначают Rа = 0,8...3,2 мкм, шероховатость исполнительных поверхностей у рычагов Rа = 0,63...3,1, у вилок
переключения 0,8...3,2 мкм. Для увеличения сроков службы твердость исполнительных поверхностей рычагов и вилок уста-
навливают НRС 40...60.
В качестве материалов для изготовления рычагов служат: серый чугун, ковкий чугун и конструкционные стали. Рабо-
|
|
тающие при незначительных нагрузках рычаги изготавливают из пластмассы.
Выбор материала зависит от служебного назначения и экономичности изготовления детали. Рычаги сложной формы мо-
гут быть достаточно экономично изготовлены из заготовки-отливки. Для деталей, работающих в машинах под небольшими,
неударными нагрузками, выбирают серый чугун. Для нежестких деталей, работающих с толчками и ударами, недостаточно
вязкий серый чугун является ненадежным материалом и заменяется ковким чугуном. При получении ковкого чугуна обяза-
тельным становится отжиг, после которого заготовки коробятся и должны дополнительно подвергаться правке.
Чугунные заготовки рычагов получают обычно литьем в песчаные формы, отформованные по механическим моделям.
При повышенных требованиях к точности отливок заготовки отливают в оболочковые формы. Отливки из ковкого чугуна
следует подвергать отжигу и последующей правке для уменьшения остаточных деформаций. Припуски на обработку и до-
пуски на размеры отливок рычагов определяются соответствующими стандартами.
Стальные заготовки рычагов получают ковкой, штамповкой, литьем по выплавляемым моделям и реже сваркой. При
|
|
штамповке заготовок в небольших количествах применяют подкладные штампы. С увеличением масштаба изготовления
заготовок более экономичной становится штамповка их в открытых и закрытых штампах. В серийном производстве штам-
повки выполняют на штамповочных молотах, фрикционных и кривошипных прессах, а в крупносерийном и массовом про-
изводствах – на кривошипных прессах и горизонтально-ковочных машинах. Для повышения производительности и умень-
шения себестоимости штампованных заготовок их предварительное формование в массовом производстве в ряде случаев
производят на ковочных вальцах.
При фрезеровании торцов втулок за технологическую базу принимают или поверхности стержня рычага, или противо-
положные торцы втулок, при их шлифовании за технологическую базу принимают противоположные торцы втулок.
При обработке основных отверстий в качестве технологической базы выбирают обработанные торцы втулок и их на-
ружные поверхности, что обеспечивает равностенность втулок. Заключительные этапы обработки выполняют при использо-
вании в качество технологической базы одного или двух основных отверстий торцов втулок.
Типовые технологические процессы изготовления, применяемое оборудование и оснастка. Техническая и технологическая документация, применяемая при изготовлении деталей и агрегатов автотракторной техники.
1.7 Типовые маршруты изготовления валов
Рассмотрим основные операции механической обработки для изготовления вала с типовыми конструктивными элемен-
тами и требованиями к ним (рис. 2).
005 Заготовительная.
Для заготовок из проката: рубка прутка на прессе или обрезка прутка на фрезерно-отрезном или другом станке. Для за-
готовок, получаемых методом пластического деформирования – штамповать или ковать заготовку.
010 Правильная (применяется для проката).
Правка заготовки на прессе. В массовом производстве может производиться до отрезки заготовки. В этом случае пра-
вится весь пруток на правильно-калибровочном станке.
015 Подготовка технологических баз.
Обработка торцов и сверление центровых отверстий. В зависимости от типа производства операцию осуществляют:
− в единичном производстве подрезку торцов и центрования на универсальных токарных станках последовательно за
два установа;
− в серийном производстве подрезку торцов раздельно от центрования на продольно-фрезерных или горизонтально-
фрезерных станках, а центрование – на одностороннем или двустороннем центровальном станке. Могут применяться фре-
зерно-центровальные полуавтоматы последовательного действия с установкой заготовки по наружному диаметру в призмы и
базированием в осевом направлении по упору (рис. 35);
− в массовом производстве на фрезерно-центровальных станках барабанного типа, которые одновременно фрезеруют
и центруют две заготовки без съема их со станка. Форму и размеры центровых отверстий назначают в соответствии с их тех-
нологическими функциями по ГОСТ 14034–74. Для нежестких валов (отношение длины к диаметру более 12) – обработка
шеек под люнеты.
020 Токарная (черновая).
Выполняется за два установа на одной операции или каждый установ выносится как отдельная операция. Производится
точение наружных поверхностей (с припуском под чистовое точение и шлифование) и канавок. Это обеспечивает получение
точности IТ12, шероховатости Ra = 6,3. В зависимости от типа производства операцию выполняют:
в единичном производстве на токарно-винторезных станках;
в мелкосерийном – на универсальных токарных станках с гидросуппортами и станках с ЧПУ;
Рис. 35 Схема выполнения фрезерно-центровальной операции
в серийном – на копировальных токарных станках, горизонтальных многорезцовых, вертикальных одношпиндельных
полуавтоматах и станках с ЧПУ;
в крупносерийном и массовом – на многошпиндельных многорезцовых полуавтоматах; мелкие валы могут обрабаты-
ваться на токарных автоматах.
025 Токарная (чистовая).
Аналогичная приведенной выше. Производится чистовое точение шеек (с припуском под шлифование). Обеспечивается
точность IТ11...10, шероховатость Rа = 3,2.
030 Фрезерная.
Фрезерование шпоночных канавок, шпицев, зубьев, всевозможных лысок.
Шпоночные пазы в зависимости от конструкции обрабатываются либо дисковой фрезой (если паз сквозной) на горизон-
тально-фрезерных станках, либо пальцевой фрезой (если паз глухой) на вертикально-фрезерных станках. В серийном и мас-
совом производствах для получения глухих шпоночных пазов применяют шпоночно-фрезерные полуавтоматы, работающие
маятниковыми методом.
Шлицевые поверхности на валах чаще всего получают методом обкатывания червячной фрезой на шлицефрезерных
или зубофрезерных станках. При диаметре шейки вала более 80 мм шлицы фрезеруют за два рабочих хода.
035 Сверлильная.
Сверление всевозможных отверстий.
040 Резьбонарезная.
На закаливаемых шейках резьбу изготавливают до термообработки. Если вал не подвергается закалке, то резьбу наре-
зают после окончательного шлифования шеек (для предохранения резьбы от повреждений). Мелкие резьбы у термообраба-
тываемых валов получают сразу на резьбошлифовальных станках. Внутренние резьбы нарезают машинными метчиками на
сверлильных, револьверных и резьбонарезных станках в зависимости от типа производств. Наружные резьбы нарезают:
− в единичном и мелкосерийном производствах на токарно-винторезных станках плашками, резьбовыми резцами или
гребенками;
− в мелкосерийном и серийном производствах резьбы не выше 7-й степени точности нарезают плашками, а резьбы 6-й сте-
пени точности – резьбонарезными головками на револьверных и болторезных станках;
− в крупносерийном и массовом производствах – гребенчатой фрезой на резьбофрезерных станках или накатыванием.
045 Термическая.
Закалка объемная или местная согласно чертежу детали.
050 Шлифовальная.
Шейки вала шлифуют на круглошлифовальных (рис. 17) или бесцентрошлифовальных станках. Шлицы шлифуются
(рис. 18) в зависимости от центрирования:
− по наружной поверхности – наружное шлифование на круглошлифовальных станках и шлифование боковых по-
верхностей на шлицешлифовальном полуавтомате одновременно двумя кругами и делением;
− по поверхности внутреннего диаметра – шлифование боковых поверхностей шлицев и шлифование внутренних по-
верхностей по диаметру, либо профильным кругом одновременно, либо в две операции. Пример шлицевого вала с техноло-
гическими требованиями представлен на рис. 36.
2.3 Типовые маршруты изготовления втулок
Рассмотрим основные операции механической обработки для изготовления втулки с типовыми конструктивными эле-
ментами и требованиями к ним.
1 Обработка за один установ.
005 Токарная.
Подрезка торца у прутка, подача прутка до упора, зацентровка торца под сверление, сверление отверстия, точение чер-
новое наружной поверхности со смятием фасок на свободном торце, точение канавок, предварительное развертывание,
окончательное развертывание, отрезка. При обработке втулки из трубы вместо сверления производят зенкерование или рас-
тачивание отверстия. Выполняется на токарно-револьверном, одношпиндельном или многошпиндельном токарном автомате.
010 Сверлильная.
Снятие фасок с противоположного торца втулки на вертикально-сверлильном или токарном станке.
015 Сверлильная.
Сверление отверстий, нарезка резьбы на вертикально или радиально-сверлильном станке.
020 Контрольная.
2 Обработка за два установа.
005 Заготовительная.
Резка заготовки из проката или трубы или штамповка.
010 Токарная.
В зависимости от типа производства выполняется за одну операцию и два установа (единичное) или за две операции
(серийное и массовое).
Первый установ (базирование по наружной поверхности к торцу в патроне) – подрезка свободного торца, сверление и
зенкерование или растачивание отверстия (с припуском под шлифование), растачивание канавок и фасок.
Второй установ (базирование по отверстию и торцу на оправке) – подрезка второго торца, точение наружных поверхно-
стей (с припуском под шлифование), точение канавок и фасок. В зависимости от типа производства операция выполняется:
− в единичном – на токарно-винторезных станках;
− в серийном – на токарно-револьверных станках и станках с ЧПУ;
− в массовом – на токарно-револьверных, одношпиндельных или многошпиндельных токарных полуавтоматах.
015 Сверлильная.
Сверление, зенкерование отверстий, нарезка резьбы. Производится на вертикально-сверлильных станках, сверлильных
станках с ЧПУ, агрегатных станках.
020 Термическая.
Закалка согласно чертежу.
025 Внутришлифовальная.
Шлифование отверстия на внугришлифовальном станке. Деталь базируется по наружному диаметру и торцу в патроне.
030 Круглошлифовальная.
Шлифование наружных поверхностей торца на круглошлифовальном или торцекруглошлифовальном станках.
035 Контрольная.
При обработке тонкостенных втулок (толщина стенки менее 5 мм) возникает дополнительная задача закрепления заго-
товки на станке без ее деформаций.
3 Технология изготовления дисков и фланцев
К деталям класса "диски" относятся детали, образованные наружными и внутренними поверхностями вращения,
имеющими одну общую прямолинейную ось при отношении длины цилиндрической части к наружному диаметру менее 0,5.
Например: шкивы, фланцы, крышки подшипников, кольца, поршни гидро- и пневмоприводов и т.п. Технологические задачи
– аналогичные классу втулок: достижение концентричности внутренних и наружных цилиндрических поверхностей и пер-
пендикулярность торцов к оси детали.
3.1 Типовой маршрут изготовления дисков и фланцев
Основные схемы базирования. Технологические базы – центральное отверстие и обработанный торец, причем корот-
кое отверстие является двойной опорной базой, а торец – установочной.
Обработку шкивов средних размеров (d = 200...400 мм) производят на токарных, в крупносерийном производстве – на
револьверных станках. Крупные шкивы и маховики – на токарных карусельных станках. При обработке на карусельных
станках установку на первой операции выполняют по ступице, в которой обрабатывается центральное отверстие и приле-
гающие к ней торцы. Обод обрабатывают при установке шкива на центрирующий палец по обработанному отверстию и тор-
цу (рис. 45).
Типовой маршрут изготовления дисков
005 Заготовительная.
В большинстве случаев – лить заготовку, ковать или штамповать. Мелкие шкивы – из прутка.
010 Токарная.
Растачивание отверстия с припуском под последующую обработку и подрезка торца. Технологическая база – черная
поверхность обода или ступицы. Выполняется в зависимости от маршрутов и типа производства на токарном, револьверном
или карусельном станке.
015 Токарная
Подрезать второй торец. Технологическая база – обработанные отверстия и торец.
020 Протяжная
Протянуть цилиндрическое отверстие. Технологическая база – отверстие и торец. Станок – вертикально-протяжной.
025 Протяжная или долбежная.
Протянуть или долбить шпоночный паз. Технологическая база – отверстие и торец. Станок – вертикально-протяжной
или долбежный.
030 Токарная (черновая).
Точить наружный диаметр и торцы обода, точить клиновидные канавки. Технологическая база – отверстие. Станок то-
карный или многорезцовый токарный.
035 Токарная (чистовая).
Точить наружный диаметр и канавки. При криволинейной образующей на токарно-копировальном станке или токарном
станке по копиру.
040 Сверлильная.
Сверлить отверстия и нарезать резьбу (если требуется по чертежу). Технологическая база – торец. Станок – сверлиль-
ный.
045 Балансировочная.
Балансировка и высверливание отверстий для устранения дисбаланса. Технологическая база – отверстие. Станок – ба-
лансировочный.
050 Шлифовальная.
Шлифование ступиц (если требуется по чертежу). Технологическая база – отверстие. Станок – круглошлифовальный.
055 Контрольная.
060 Нанесение антикоррозионного покрытия.
Основным служебным назначением фланцев является ограничение осевого перемещения вала, установленного на под-
шипниках. Отсюда следует, что основными конструкторскими базами фланца будут поверхности центрирующего пояска по
размеру отверстия в корпусе и торцы. Поскольку в качестве технологических баз при обработке заготовки целесообразно
выбирать основные базы детали, то исходя из этого, следует, что на первых операциях обрабатывают основные базы. В связи
с этим на первой операции в качестве технологических баз используют наружную цилиндрическую поверхность и торец
большого фланца, а на последующих – посадочную поверхность цилиндрического пояска и его торец. На этих же базах об-
рабатывают крепежные отверстия и лыски, если они заданы чертежом.
Типовой маршрут изготовления фланцев
005 Заготовительная.
В зависимости от типа производства и материала – лить, ковать, штамповать заготовку или отрезать из проката.
010 Токарная.
Подрезать торец большого фланца и торец центрирующего пояска, точить наружную цилиндрическую поверхность
пояска с припуском под шлифование, точить канавку и фаски. Технологическая база – наружная поверхность и торец флан-
ца. Станок токарный, многошпиндельный токарный полуавтомат, токарный с ЧПУ.
015 Токарная.
Подрезать второй торец большого фланца, точить его наружную поверхность и фаску. Технологическая база – поверх-
ность центрирующего пояска и его торец.
020 Сверлильная.
Сверлить и зенковать отверстия. Технологическая база – та же. Станок вертикально-сверлильный, сверлильный с ЧПУ,
агрегатно-сверлильный с многошпиндельной головкой.
025 Фрезерная.
Фрезеровать фланец с лысками. Технологическая база – та же плюс крепежное отверстие. Станок – вертикально-
фрезерный.
030 Шлифовальная.
Шлифовать наружную поверхность центрирующего пояска и торец.
Технологическая база – наружная поверхность большого фланца и торец. Станок – универсально-шлифовальный или
торцекруглошлифовальный.
035 Контрольная.
4.1 Типовые маршруты изготовления корпусных деталей
Последовательность механической обработки корпуса призматического типа с плоским основанием и основным отвер-
стием с осью, параллельной основанию следующая.
005 Заготовительная.
Заготовки корпусов из серого чугуна отливают в земляные, металлические (кокиль) или оболочковые формы, из стали –
в земляные формы, кокиль или по выплавляемым моделям. Заготовки из алюминиевых сплавов отливают в кокиль или лить-
ем под давлением. В единичном и мелкосерийном производствах применяют сварные корпуса из стали. Заготовки корпус-
ных деталей перед механической обработкой проходят ряд подготовительных операций.
010 Фрезерная (протяжная).
Фрезеровать, или протянуть плоскость основания начерно и начисто или с припуском под плоское шлифование (при
необходимости). Технологическая база – необработанная плоскость, параллельная обрабатываемой поверхности.
Оборудование:
– в единичном и мелкосерийном производствах – вертикально-фрезерный и строгальный станки;
– в серийном – продольно-фрезерный или продольно-строгальный станки;
– в крупносерийном и массовом – барабанно- и карусельно-фрезерные, плоскопротяжные, агрегатно-фрезерные станки.
015 Сверлильная.
Сверлить и зенковать (при необходимости) отверстия в плоскости основания. Развернуть два отверстия. Технологиче-
ская база – обработанная плоскость основания. Оборудование – радиально-сверлильный станок или сверлильный с ЧПУ, в
массовом и крупносерийном производствах – многошпиндельный сверлильный станок или агрегатный станок.
020 Фрезерная.
Обработка плоскостей, параллельных базовой (при их наличии). Технологическая база – плоскость основания. Обору-
дование – см. операцию 010.
025 Фрезерная.
Обработка плоскостей, перпендикулярных базовой (торцы основных отверстий). Технологическая база – плоскость ос-
нования и два точных отверстия. Оборудование – горизонтально-фрезерный или горизонтально-расточной станок.
030 Расточная.
Растачивание основных отверстий (черновое и чистовое, или с припуском под точное растачивание). Технологическая
база – та же (см. операцию 025). Оборудование:
– единичное производство – универсальный горизонтально-расточной станок;
– мелкосерийное и среднесерийное – станки с ЧПУ расточно-фрезерной группы и многооперационные станки;
– крупносерийное и массовое – агрегатные многошпиндельные станки.
Точность межосевых расстояний, а также точность положения отверстий достигается с помощью:
– разметки (от ± 0,1 мм до + 0,5 мм);
– пробных расточек (до + 0,02 мм);
– координатного растачивания на горизонтально-расточных станках (до ± 0,02 мм);
– обработки по кондукторам и шаблонам (до ± 0,02 мм, ± 0,03 мм).
035 Сверлильная.
Сверлить (зенковать при необходимости), нарезать резьбу в крепежных отверстиях. Технологическая база – та же. Обо-
рудование – радиально-сверлильный, сверлильный с ЧПУ, многооперационный, сверлильный многошпиндельный и агрегат-
ный станки (в зависимости от типа производства).
040 Плоскошлифовальная.
Шлифовать (при необходимости) плоскость основания. Технологическая база – поверхность основного отверстия или
обработанная плоскость, параллельная базовой (в зависимости от требуемой точности расстояния от базовой плоскости до
оси основного отверстия).
Оборудование – плоскошлифовальный станок с прямоугольным или круглым столом.
045 Алмазно-расточная.
Тонкое растачивание основного отверстия. Технологическая база – базовая плоскость и два отверстия. Оборудование –
алмазно-расточной станок. С целью выдерживания принципа постоянства баз большинство операций обработки (020, 025,
030, 035), за исключением операций подготовки технологических баз (010, 015) и отделки основных поверхностей (040, 045),
часто концентрируют в одну операцию, выполняемую на горизонтально-расточном (единичное производство), многоопера-
ционном (серийное) или агрегатном (массовое) станках.
В маршрут обработки разъемных корпусов дополнительно к вышеприведенным операциям включают:
– обработку поверхности разъема у основания (фрезерная);
– обработку поверхности разъема у крыши (фрезерная);
– обработку крепежных отверстий на поверхности разъема основания (сверлильная);
– обработку крепежных отверстий на поверхности разъема крышки (сверлильная);
– сборку корпуса промежуточную (слесарно-сборочная операция);
– обработку двух точных отверстий (обычно сверлением и развертыванием) под цилиндрические или конические
штифты в плоскости разъема собранного корпуса.
5.2 Типовой маршрут изготовления зубчатых колес
Основные операции механической обработки зубчатого колеса со ступицей 7-й степени точности (рис. 63) следующие.
005 Заготовительная.
Для заготовок из проката – резка проката, для штампованных заготовок – штамповка.
Штампованные заготовки целесообразно выполнять с прошитыми отверстиями, если их диаметр более 30 мм и длина не
более 3-х диаметров.
Заготовки из чугуна и цветных сплавов (иногда из сталей) получают литьем.
010 Токарная.
Точить торец обода и торец ступицы с одной стороны начерно, точить наружную поверхность обода до кулачков па-
трона начерно, расточить начерно на проход отверстие (или сверлить и расточить при отсутствии отверстия в заготовке),
точить наружную поверхность ступицы начерно, точить фаски.
Технологическая база – наружная поверхность обода и торец, противолежащий ступице (закрепление в кулачках токар-
ного патрона).
Оборудование: единичное производство – токарно-винторезный станок; мелко- и среднесерийное – токарно-
револьверный, токарный с ЧПУ; крупносерийное и массовое – одношпиндельный или многошпиндельный токарный полуав-
томат (для заготовки из прутка – прутковый автомат).
Рис. 63 Цилиндрическое зубчатое колесо с односторонней ступицей
015 Токарная.
Точить базовый торец обода (противолежащий ступице) начерно, точить наружную поверхность обода на оставшейся
части начерно, расточить отверстие под шлифование, точить фаски.
Технологическая база – обработанные поверхности обода и большего торца (со стороны ступицы).
Оборудование – то же (см. операцию 010).
020 Протяжная (долбежная).
Протянуть (долбить в единичном производстве) шпоночный паз или шлицевое отверстие.
Технологическая база – отверстие и базовый торец колеса.
Оборудование – горизонтально-протяжной или долбежный станки.
Применяются варианты чистового протягивания отверстия на данной операции вместо чистового растачивания на пре-
дыдущей операции.
025 Токарная.
Точить базовый и противолежащие торцы, наружную поверхность венца начисто.
Технологическая база – поверхность отверстия (реализуется напрессовкой на оправку, осевое положение на оправке
фиксируется путем применения подкладных колец при запрессовке заготовки). Необходимость данной операции вызывает-
ся требованием обеспечения соосности поверхностей вращения колеса.
Оборудование – токарно-винторезный (единичное производство), токарный с ЧПУ (серийное) или токарный многорезцовый
полуавтомат.
030 Зубофрезерная.
Фрезеровать зубья начерно (обеспечивается 8-я степень точности).
Технологическая база – отверстие и базовый торец (реализуется оправкой и упором в торец).
Оборудование – зубофрезерный полуавтомат.
035 Зубофрезерная.
Фрезеровать зубья начисто (обеспечивается 7-я степень точности).
040 Шевинговальная.
Шевинговальная операция повышает на единицу степень точности зубчатого колеса. Операции применяют для термо-
обрабатываемых колес с целью уменьшения коробления зубьев, так как снимается поверхностный наклепанный слой после
фрезерования.
Технологическая база – отверстие и базовый торец (реализуется оправкой).
Оборудование – зубошевинговальный станок.
045 Термическая.
Калить заготовку или зубья (ТВЧ) или цементировать, калить и отпустить – согласно техническим требованиям. Нали-
чие упрочняющей термообработки, как правило, приводит к снижению точности колеса на одну единицу.
050 Внутришлифовальная.
Шлифовать отверстие и базовый торец за один установ. Обработка отверстия и торца за один установ обеспечивает их
наибольшую перпендикулярность.
Технологическая база – рабочие эвольвентные поверхности зубьев (начальная окружность колеса) и торец, противоле-
жащий базовому. Реализация базирования осуществляется специальным патроном, у которого в качестве установочных эле-
ментов используют калибровочные ролики или зубчатые секторы. Необходимость такого базирования вызвана требованием
обеспечения равномерного съема металла и зубьев при их последующей отделке с базированием по отверстию на оправке.
Оборудование – внутришлифовальный станок.
При базировании колеса на данной операции за наружную поверхность венца для обеспечения соосности поверхностей
вращения необходимо ввести перед или после термообработки круглошлифовальную операцию для шлифования наружной
поверхности венца и торца, противолежащего базовому (желательно за один установ на оправке).
Технологическая база – отверстие и базовый торец.
Оборудование – круглошлифовальный или торцекруглошлифовальный станки.
Необходимость отделки наружной поверхности венца колеса часто вызывается также и тем, что контроль основных
точностных параметров зубьев производится с использованием этой поверхности в качестве измерительной базы.
055 Плоскошлифовальная.
Шлифовать торец, противолежащий базовому (если необходимо по чертежу).
Технологическая база – базовый торец.
Оборудование – плоскошлифовальный станок с прямоугольным или круглым столом.
060 Зубошлифовальная.
Шлифовать зубья.
Технологическая база – отверстие и базовый терец.
Оборудование – зубошлифовальный станок (обработка обкаткой двумя тарельчатыми или червячным кругами или ко-
пированием фасонным кругом). При малом короблении зубьев при термообработке (например, при азотировании вместо це-
ментации) операция зубошлифования может быть заменена зубохонингованием или вообще отсутствовать.
Наличие зубошлифовальной или зубохонинговальной операции определяется наличием и величиной коробления зубьев
при термообработке. Двукратное зубофрезерование и шевингование зубьев до термообработки может обеспечить 6-ю сте-
пень точности. При потере точности во время термообработки на одну степень конечная 7-я степень точности будет достиг-
нута. Введение отделочной операции зубошлифования или зубохонингования необходимо только при уменьшении точности
колеса при термообработке больше, чем на одну степень.
065 Контрольная.
Применяются варианты техпроцесса с однократным зубофрезерованием, но с двукратным зубошлифованием.
Наличие упрочняющей термообработки приводит, как правило, к снижению степени точности колес на одну единицу,
что требует введения дополнительной отделочной операции. Для незакаливаемых зубчатых колес шевингование является
последней операцией; перед термообработкой шевингуют зубья в целях уменьшения деформации колеса в процессе термо-
обработки и повышения степени на одну единицу.
6.1 Типовой маршрут изготовления рычагов
Рассмотрим основные операции механической обработки рычагов с общей плоскостью торцов втулок (рис. 64).
005 Заготовительная.
Чугунные заготовки получают литьем в песчаные формы или оболочковые. Отливки из ковкого чугуна следует подвер-
гать отжигу и последующей правке для уменьшения остаточных деформаций. Стальные заготовки – ковкой, штамповкой,
литьем по выплавляемым моделям, а в единичном производстве – сваркой.
010 Фрезерная.
Фрезеровать торцы втулок с одной стороны начерно или начисто и с припуском под шлифование (при необходимости).
Рис. 64 Рычаг
Технологическая база (установочная) – поверхность стержня или противоположные торцы втулок. Направляющую и
опорную базы выбирают из условий удобства установки детали. Станок – вертикально-фрезерный или карусельно-
фрезерный.
015 Фрезерная.
Аналогично предыдущей операции, но с другой стороны. Технологическая база – обработанные торцы втулок. В серий-
ном и массовом производствах обработка торцов втулок может выполняться одновременно с двух сторон, на горизонтально-
фрезерном станке набором фрез. Технологическая база – поверхность стержня или поверхность втулок. Если заготовки про-
ходят чеканку (т.е. торцы втулок обжаты прессом), то фрезерную обработку не производят.
020 Обработка основных отверстий.
Технологическая база – обработанные торцы втулок и их наружные поверхности, что обеспечивает равностенность вту-
лок. В зависимости от типа производства операцию выполняют:
– в единичном и мелкосерийном производствах на радиально- и вертикально-сверлильных станках или расточных стан-
ках по разметке со сменой инструмента;
– в мелкосерийном и серийном производствах – на сверлильных станках с ЧПУ, на радиально- и вертикально-сверлильных
станках по кондуктору со сменой инструмента и быстросменных втулок в кондукторах;
– в крупносерийном и массовом производствах – на агрегатных многошпиндельных одно- и многопозиционных стан-
ках, вертикально-сверлильных станках с многошпиндельными головками и на протяжных станках.
Маршрут обработки основных отверстий имеет варианты:
– сверление, зенкерование, одно- или двукратное развертывание или двойное растачивание;
– сверление и протягивание (для отверстий диаметром более 30 мм), полученные в заготовке прошиванием или литьем,
сверление заменяют предварительным зенкерованием.
Обеспечение параллельности осей и межосевого расстояния основных отверстий достигается следующим образом (в
порядке убывания точности):
– одновременной обработкой несколькими инструментами на многошпиндельных станках;
– последовательной обработкой при неизменном закреплении заготовки;
– последовательной обработкой на разных станках, в разных приспособлениях.
030 Обработка шпоночных пазов или шлицевых поверхностей в основных отверстиях.
035 Обработка вспомогательных отверстий с нарезанием в них резьб (если нужно), пазов и уступов.
Технологическая база – основные отверстия (одно или два) и их торцы.
040 Плоское шлифование торцов втулок.
Выполняется при повышенных требованиях к шероховатости и взаимному расположению торцов втулок на плоско-
шлифовальном станке с переустановкой. Технологическая база – торцы втулок.
045 Контрольная.
В зависимости от конкретных условий последовательность обработки поверхностей рычагов может изменяться. При-
меняют варианты маршрута, в которых операции 010 и 020 меняются местами или объединяются.
Маршрут обработки рычагов с торцами втулок в разных плоскостях:
– обрабатывают торцы втулок с одной стороны;
– обрабатывают основные отверстия с той же стороны;
– обрабатывают торцы втулок с другой стороны;
– обрабатывают оставшиеся поверхности.
Оформление технической и технологической документации.
Дата добавления: 2022-01-22; просмотров: 39; Мы поможем в написании вашей работы! |
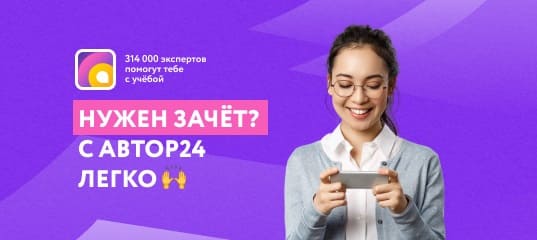
Мы поможем в написании ваших работ!