Тема 1.2 Технологические процессы сборки
Основные понятия технологических процессов. Технологическая организация процессов сборки
Сборка органически связана со всеми предшествующими про
цессами; при создании же машины высокого качества сборке при
надлежит решающая роль. Поэтому сборочным работам в машино
строении должно быть уделено особое внимание. действия рабочего, неразрывно связанные с осуществлением этого
процесса. Технологический процесс сборки — это совокупность
операций по соединению деталей в определенной технически и эко
номически целесообразной последовательности для получения сбо
рочных единиц и изделий, полностью отвечающих установленным
■для них требованиям. Если при механической и большинстве
других видов обработки понятие «технологический процесс» от
носится к детали, то в сборочном производстве оно имеет отно
шение прежде всего к соединению двух или большего числа де
талей.
При разработке технологического процесса сборки изделие,
исходя из условий его конструкции, расчленяют на части так,
чтобы осуществить сборку наибольшего количества сборочных
-единиц независимо друг от друга. В связи с этим в машине или
механизме различают конструктивные и сборочные элементы. Ус
ловное выделение первых может быть произведено на основе их
назначения в изделии; например, механизмы привода и регули
рования в станке, механизмы газораспределения в двигателях,
|
|
-механизмы управления и пр. При выделении же сборочных эле
ментов обязательным условием является возможность осуществле
ния сборки каждого из них независимо от другого. Конструктив
ные элементы не всегда могут быть сборочными, и наоборот, хотя
такое совпадение встречается часто. В этих случаях элементы на
зываются конструктивно-сборочными.
Процесс комплектования сборочных элементов — сборочных
единиц, изделия для наглядности изображают в виде схем. Эту
схему следует строить так, чтобы соответствующие сборочные еди
ницы — группы, подгруппы и детали были представлены в порядке
их введения в технологический процесс сборки. Так как процесс
сборки начинается с введения в него основной, или, как ее обычно
называют, базовой детали или подгруппы, то, очевидно, и схема
должна начинаться с условного изображения этих составных ча
стей изделия. Детали, подгруппы и группы изображают на схеме
в виде небольших прямоугольников, в которые вписывают индекс,
номера и количества соответствующих частей. Общая схема ком
плектования изделия представлена на рис. 3, a [42].
КЛАССИФИКАЦИЯ СОЕДИНЕНИЙ ДЕТАЛЕЙ
В изделиях машиностроения имеется большое количество раз
|
|
нообразных соединений деталей. В машинах примерно 35—40%
соединений типа цилиндрический вал — втулка, 15—20% пло
скостных, 15—25% резьбовых, 6—7% конических, 2—3% сфери
ческих и др. Все эти соединения характеризуются различными кон
структивными, технологическими и экономическими факторами:
степенью относительной подвижности, возможностью разборки,
технологичностью в сборке и демонтаже, видом контакта сопря
гающихся поверхностей деталей, прочностью, химической стой
костью, затратами труда и средств на сборку и т. д.
По конструкции и условиям эксплуатации соединения деталей
могут быть разделены на подвижные и неподвижные. Детали под
вижных соединений обладают возможностью относительного пе
ремещения в рабочем состоянии по некоторым траекториям, оп
ределяемым кинематической схемой механизма, звеньями которого
эти детали являются. Детали неподвижных соединений в рабочем
состоянии перемещаться не могут.
Подвижные и неподвижные соединения в зависимости от воз
можности их демонтажа подразделяются на разъемные (свободно
разбираемые) и неразъемные (неразбираемые). Количество разъ
емных соединений в современных машинах и механизмах состав
|
|
ляет от 65 до 85% всех соединений. При этом под разъемными
(демонтируемыми) соединениями подразумеваются лишь те, ко
торые могут быть полностью разобраны без повреждения соеди
няющих и скрепляющих их деталей. Остальные соединения отно
сятся к группе неразъемных, хотя в условиях эксплуатации и ре
монта машин нередко подвергается разборке некоторая часть и
этих соединений; однако процесс разборки в этом случае значитель
но усложняется, и часто одна или обе соединяемые детали после
разборки оказываются непригодными к последующей сборке или
же требуют специальных пригонок.
Таким образом, соединения могут быть неподвижные разъем
ные (например, резьбовые, пазовые и конические); неподвижные
неразъемные (например, соединения запрессовкой или разваль
цовкой, а также заклепочные); подвижные разъемные (например,
валы — подшипники скольжения, плунжеры—втулки, зубья ко
лес, каретки—станины); подвижные неразъемные (некоторые
подшипники качения, запорные клапаны).
Такая классификация соединений проста по своей схеме, но
имеет недостаток, так как в каждую группу указанной классифи
кации входит большое количество соединений, различных по своей
|
|
технологической характеристике и способу сборки.
Под точностью сборки подразумевается степень совпадения ма
териальных осей, контактирующихся поверхностей или иных
элементов сопрягающихся деталей с положением их условных
^прототипов, определяемым соответствующими размерами на чер
теже или техническими требованиями.
Точность — один из важнейших технико-экономических по
казателей качества машины. Параметры, характеризующие точ
ность как машины в целом, так и ее конструктивных и сборочных
элементов, устанавливаются исходя из служебного назначения из
делия. Причем, конечно, оправданной является точность, опти
мальная для каждого конкретного соединения, так как чрезмер
ное ее повышение, не вызываемое необходимостью, может быть
причиной значительного роста стоимости обработки.
и к деталям машины.
Сопряжения деталей, образуемые в процессе сборки изделий,
в зависимости от количества степеней свободы, как уже отмеча
лось, будут обладать различными свойствами и могут быть непод
вижными или подвижными. От относительных размеров деталей,
образующих сопряжение, зависит степень его неподвижности или
подвижности. Эти степени характеризуются величиной натягов
или зазоров, выдерживаемых при сборке сопряжений, или, иначе,
величиной и знаком конструктивных и производственных отклоне
ний размеров сопрягаемых деталей.
Осуществляемые в процессе сборки контрольные операции
дают возможность установить в соединениях, сборочных единицах
и в машине степень соответствия относительного положения и пе
ремещения исполнительных поверхностей техническим требова
ниям на сборку. В общем случае методы контроля могут быть раз
делены на визуальные и с применением технических средств,
измерений (универсальных, специальных, механизированных, ав
томатизированных) .
Дата добавления: 2022-01-22; просмотров: 27; Мы поможем в написании вашей работы! |
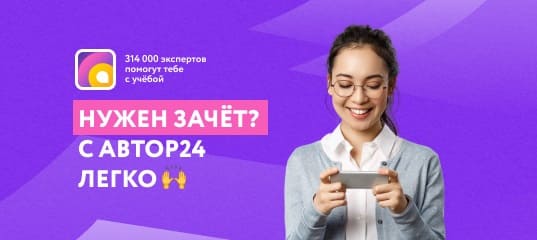
Мы поможем в написании ваших работ!