Применение сборочно-сварочных приспособлений
Сборка под сварку – это размещение элементов конструкции в порядке, указанном в технологической карте, и предварительное скрепление их между собой с помощью приспособлений и наложения прихваток. От качества выполнения сборки больше всего зависит качество сварной конструкции и трудоемкость сборочно-сварочных работ.
Существуют следующие способы установки деталей при сборке:
а) по предварительной разметке;
б) по упорам фиксаторам или по шаблонам;
в) по контрольным отверстиям..
При сборке по разметке положение каждого элемента определяется по линиям, нанесенным на сопрягаемые элементы.
Сборку по упорам-фиксаторам производят в сборочно-сварочных приспособлениях или на стендовых плитах.
При сборке по контрольным отверстиям сопрягаемые элементы соединяют, совмещая эти отверстия (они являются технологическими сборочными базами).
Последние два способа сборки обеспечивают более высокую точность взаимного положения деталей при сборке и более высокую производительность. Заданные размеры взаимного положения деталей при сборке этими способами получаются автоматически. Наибольшее распространение получил способ сборки в приспособлениях. Тип приспособления определяется серийностью производства, сложностью конструкции свариваемого узла, видом сварки и применяемым оборудованием.
В технологии машиностроения при механической обработке приспособление рассматривается в системе: станок – приспособление – инструмент – деталь. При изготовлении конструкций с применением сварки, сварочно-сборочное приспособление необходимо рассматривать в аналогичной системе: сварочное оборудование – приспособление – инструмент – свариваемое изделие. Различие состоит лишь в том, что в случаи сварки должно быть обеспечено свободное перемещение конструкции.
|
|
Входящие в сварной узел детали, как правило, различны по конструкции, каждая имеет свои установочные базы и зажимы. Поэтому сборочно-сварочные приспособления представляют собой как бы несколько разных по конструкции одноместных приспособлений, собранных в одном корпусе по заданным размерам взаимного положения деталей сварного узла. Точность этих приспособлений ниже станочных.
К спроектированному и изготовленному приспособлению предъявляют следующие требования:
а) достаточная жесткость корпуса, так как взаимное положение свариваемых деталей в процессе сборки под сварку должно оставаться неизменным;
б) свободное перемещение элементов свариваемой конструкции при усадке швов после сварки (прихватки);
в) свободный доступ к местам сварки сварочного электрода, электронного луча, сварочной горелки и т.д.;
|
|
г) быстрая установка деталей свариваемого изделия и их зажима;
д) свободный съем сварного узла после выполнения сборочно-сварочных операций.
На рис.13 представлено приспособление для автоматической сварки патрубков с торовым воротником. Сварочная головка вращается относительно оси хвостовика 1 под углом 45°, хвостовик центрируется по отбортовке отверстия с помощью основания 5, центрирующей втулки 2 и фигурной медной подкладки 3. Необходимый прижим свариваемых кромок создается затяжкой болта 4.
Рис.13.Приспособление для сварки патрубков.
Для сборки и сварки балок используются сварочные кондукторы с винтовыми зажимами. На рис.14 показана схема кондуктора, применяемого для сборки и сварки элементов двутавровых балок высотой 400-1800 мм. Сварка элементов в этом кондукторе осуществляется сварочным трактором наклонным электродом.
Рис.14.Кондуктор для сварки двутавровых балок.
Стягивающие и распорные приспособления предназначены для стягивания при сборке двух и более деталей или узлов, для выравнивания кромок и вмятин, а также для разжима обечаек (рис.15).
а |
| ||
|
Рис.15. Стягивающее (а) и распорное (б) приспособления: 1-рычаг основной;
2-скоба; 3-гайка;4-винт стягивающий; 5-рычаг; 6-винт зажимной;
7-винт распорный; 8-основание; 9-подпятник.
Рис.16. Сборочно-сварочное приспособление для сборки под сварку прямоугольного каркаса
приспособление собрано на базовой плите 600Х600Х30 мм.
Для сборки деталей в единичном производстве применяются специальные стеллажи и стенды. Стеллажи служат для грубой установки средних и крупных изделий при сборке, сварке, правке и контроле. Для сборки и сварки различных конструкций выполняются универсальные сборно-разборные приспособления (УСПсв), состоящие из базовых деталей – плит, угольников, подкладок, опор, фиксаторов, прижимных элементов, распорок, стяжек, сухарей, болтов, гаек, шпилек и пр. (рис.16).
В условиях достаточной однотипности свариваемых изделий нет необходимости полной перекомпоновки универсальных приспособлений. Достаточно осуществить переналадку отдельных элементов на различные типоразмеры, оставляя базовую часть оснастки.
Особенность технологической подготовки производства изделий с применением УСПсв состоит в том, что вместо специальных приспособлений, изготавливаемых обычным путём по разработанным чертежам, создаётся приспособление путём сборки из элементов комплекта УСПсв, т.е. методом агрегатирования из стандартных элементов. После изготовления партии сварных конструкций оно разбирается на составные элементы, которые используются в новых компоновках.
|
|
УСПсв широко применяются в различных видах сварки, в том числе при механизированной сварке в среде углекислого газа.
Использование УСПсв позволяет:
· сократить сроки на создание приспособления, так как сборка приспособления из готовых элементов УСПсв в 10-20 раз короче, чем проектирование и изготовление оснастки обычным путём;
· поднять уровень оснащённости сборочно-сварочных работ до уровня серийного производства;
· повысить производительность труда сборочно-сварочных работ за счёт сокращения на установку и выверку свариваемых деталей;
· повысить точность взаимного положения деталей конструкции.
Процесс создания приспособления из элементов УСПсв объединяет два процесса, выполняемые одновременно одним человеком: конструирование и сборка элементов и прочное скрепление их между собой при помощи крепёжных элементов. При этом отпадает необходимость в разработке чертежей приспособления. Слесарь –инструментальщик по сборке УСП выполняет компоновку. В качестве исходных данных он имеет чертежи изделия.
Внедрением УСПсв применительно к различным технологическим процессам занимается специальная заводская служба.
Руководство работой по сборке УСПсв осуществляет начальник или мастер участка. Им выполняются следующие работы:
а) сборка компоновок УСПсв по заявкам цехов;
б) выявление целесообразности и возможности сборки УСПсв совместно с ведущими технологами на стадии технологического проектирования;
в) изыскание возможности расширения области рационального применения УСПсв;
г) обучение сборщиков УСП.
При работе с компоновками УСПсв запрещается:
а) устанавливать или снимать свариваемое изделие с резкими ударами по конструкции;
б) пользоваться молоткам, кувалдами, клиньями для подгонки деталей во время сборки;
в) наращивать рукоятки зажимных устройств трубами, ломиками и другими предметами;
г) зажигать сварочную дугу на элементах УСПсв;
д) зачищать абразивным или другим инструментом поверхности элементов УСПсв на рабочем месте сварщика.
2.5.2. Применение роботизированных комплексов
Роботизированными технологическими комплексами (РТК) для проведения сварочных работ называют снабженные роботами технологические ячейки, участки или линии. Компоновка РТК зависит от характера изделия и серийности его выпуска. При дуговой сварке в ряде случаев целесообразно разделять функции между механизмами перемещения сварочной горелки и манипулятором, служащим для перемещения свариваемого изделия. При этом оба устройства работают по единой программе. Такой прием позволяет не только упростить кинематику, и уменьшить число степеней подвижности самого робота, но и снизить требования к системе управления.
Для позиционирования деталей целесообразно использовать поворотные столы с несколькими приспособлениями для сборки. Оператор собирает изделие, которое поворотным столом подается на сварку, после чего возвращается для контроля, подварки и съема изделия.
РТК, представленный на рис.17, имеет вращатели 3 с двумя осями вращения: вертикальный – для вращения планшайбы 2, к которой крепится изделие, и наклонной – для вращения планшайбы вместе с изделием. Причем планшайба смещена с наклонной оси для уравновешивания массы изделия относительно оси вращения. Сварочный полуавтомат 5 для уменьшения нагрузки на руку робота установлен отдельно от робота 1, на консоли 6, прикрепленной к сварочному источнику питания 7. Стойки управления 8 и пульт управления 4 расположены вне рабочей зоны робота.
Рис.17. Робототехнический комплекс с вращателями.
Сварочное оборудование выбирается из условия обеспечения выбранных режимов сварки, применяемогоспособа сварки и свойств основного материала, апри ручной сварке - штучными электродами в зависимостиот марки покрытия и режимов сварки.
Выбор сварочного оборудования, а также конструирование и изготовление приспособлений и оснастки следует сопровождать расчетами, подтверждавшими их экономическую целесообразность, которая может быть произведена по сроку окупаемости оборудования.
Срок окупаемости рассчитывается по следующей формуле:
![]() | (6) |
где К1 и К2 – капитальные затраты по сравниваемым вариантам;
С1 и С2 – себестоимость годовой продукция по тем же вариантам.
Вместо себестоимости годовой продукции допускается использование величины технологических затрат, к которой относятся затраты на заработную плату с начислениями на нее в размере 17% (10% – дополнительная зарплата, 1% – начисления по соцстраху) и на электрическую энергию.
Нормативные значения срока окупаемости для отдельных отраслей машиностроения, как правило, составляют от трех до пяти лет.
2.6. Мероприятия, обеспечивающие заданные размеры и форму конструкции
2.6.1.Образование сварочных напряжений и деформаций
В процессе изготовления сварных конструкций в них возникают сварочные напряжения и деформации. Сварочные напряжения, превышающие предел текучести металла, вызывают его пластическую деформацию. Это приводит к изменению размеров и формы изделия, т.е. к его короблению. Если сварочные напряжения превышают предел прочности, то происходит разрушение сварного шва или соединения, т.е. образуются трещины. Причинами возникновения сварочных напряжений и деформаций являются: неравномерное нагревание металла при сварке, литейная усадка расплавленного металла и структурные превращения в металле в процессе его охлаждения.
Неравномерное нагревание металла. Как известно, все металлы при нагревании расширяются, а при охлаждении сжимаются. При наличии жестких связей между нагретыми и холодными участками металла это приводит к образованию сжимающих или растягивающих внутренних сварочных напряжений. Рассмотрим несколько примеров.
При местном нагреве пластины длиной l , свободно лежащей на сварочном столе, размеры ее по длине увеличатся на величину Δl. Это увеличение будет зависеть от коэффициента линейного расширения данного металла, длины нагретой зоны, а также температуры ее нагрева. В процессе охлаждения, по мере уменьшения температуры, удлинение будет уменьшаться и при начальной температуре оно станет равным нулю. После охлаждения пластина приобретает свои первоначальные размеры и в ней не будет ни внутренних напряжений, ни остаточных деформаций. При местном нагреве этой же пластины, жестко закрепленной с обоих концов, она не может свободно удлиняться, поэтому в ней возникнут сжимающие внутренние напряжения. При высоком нагреве (более 600°С) сжимающие напряжения превысят предел текучести нагретого участка, в нем произойдет пластическая деформация сжатия и на некотором участке он станет несколько толще. Напряжения сжатия при этом частично исчезнут. При охлаждении пластина должна бы укоротиться, но этому препятствует жесткое закрепление, в результате чего в ней возникнут растягивающие напряжения.
Аналогичным образом возникают внутренние напряжения и деформации при наплавке валика на кромку полосы. Наплавленный валик и нагретая часть полосы будут расширяться и растягивать холодную часть полосы, вызывая в ней растяжение с изгибом. Сам же валик и нагретая часть полосы будут сжаты, поскольку их тепловому расширению препятствует холодная часть полосы. В результате такого распределения напряжений полоса прогнется выпуклостью вверх. В процессе остывания наплавленный валик и нагретая часть полосы, претерпев пластические деформации, будут укорачиваться. Этому укорочению снова будут препятствовать верхние слои холодного металла полосы. Теперь уже наплавленный валик и нагретая часть полосы будут стягивать верхние холодные волокна ее. Они сожмутся, и полоса прогнется выпуклостью вниз.
В реальных условиях изменение температур от нагретой к холодной зоне полосы происходит плавно, поэтому на графиках распределения температур переход от растягивающих напряжений к сжимающим также будет более плавным.
Литейная усадка расплавленного металла. В результате остывания и затвердевания жидкого металла сварного шва происходит его усадка. Явление усадки объясняется тем, что при затвердевании металл становится более плотным, в результате чего объем его уменьшается. Ввиду того, что металл шва жестко связан с основным металлом, остающимся в неизменном объеме, который противодействует этой усадке, то в сварном соединении возникают внутренние напряжения.
При сварке происходит продольная и поперечная усадка расплавленного металла, в результате чего образуются продольные и поперечные внутренние напряжения, вызывающие деформации сварных изделий. В результате продольной усадки возникает коробление изделий в продольном направлении. Поперечная усадка, как правило, приводит к угловым деформациям, в сторону большего объема расплавленного металла.
Структурные превращения в металле. При сварке легированных сталей наряду с тепловыми напряжениями сжатия возникают объемные структурные напряжения. Это объясняется тем, что при охлаждении изменяется структура металла. Если сталь испытывает бейнитное или мартенситное превращение, то из-за низкой скорости диффузии углерода к моменту перестройки кристаллической решетки от гранецентрированной кубической к объемноцентрированной, последняя оказывается пересыщенной углеродом примерно в десять раз (бейнит) или еще более раз (мартенсит). Кристаллическая решетка в этих случаях из-за пересыщения углеродом перестает быть кубической, один из ее параметров всегда больше начального. Говорят, что происходит увеличение объема фаз. Такой фазовый наклеп вызывает внутренние напряжения. При сварке низкоуглеродистых и низколегированных не закаливающихся сталей структурные напряжения практически не возникают.
2.6.2. Методы борьбы с деформациями
Методы борьбы с деформациями включают в себя мероприятия, выполняемые до сварки, в процессе сварки и после сварки.
Мероприятия, выполняемые до сварки. Одним из эффективных приемов борьбы с деформациями является рациональное конструирование сварных изделий. В процессе конструирования необходимо ограничивать количество наплавленного металла путем уменьшения угла скоса кромок или уменьшения катетов швов, не допускать пересечения швов, не располагать сварные швы там, где действуют максимальные напряжения от внешних нагрузок, размещать их симметрично, применять преимущественно стыковые швы и т. п.
Рациональная сборка деталей с учетом возможных деформаций. Для компенсации возможных деформаций сварной конструкции часто применяются обратные деформации свариваемых элементов. Зная, что шов после охлаждения всегда сокращается в размерах, можно заранее предугадать характер возможных напряжений и деформаций и произвести предварительный выгиб свариваемых деталей в противоположную сторону. Величина обратного выгиба определяется расчетным или опытным путем. При сборке деталей следует избегать прихваток, которые создают жесткое закрепление деталей и способствуют возникновению значительных остаточных напряжений. Лучше применять сборочные приспособления, допускающие некоторое перемещение деталей при усадке металла.
Мероприятия, выполняемые в процессе сварки. С целью уменьшения деформаций в процессе сварки конструкции следует сваривать так, чтобы замыкающие швы, создающие жесткий контур, заваривались в последнюю очередь. Сварку следует вести от середины конструкции к краям, обратноступенчатым или комбинированным способом. Каждый последующий шов при многослойной сварке рекомендуется накладывать в направлении, обратном наложению предыдущего шва. Если сваривают полотнища из отдельных листов, то в первую очередь нужно выполнять поперечные швы отдельных поясов, что обеспечит их свободную усадку, а затем сваривать пояса между собой продольными швами. В противном случае возможно образование трещин в местах пересечения поперечных и продольных швов. При сварке двутавровых балок в первую очередь сваривают стыковые соединения стенок и полок, а затем производят сварку угловых поясных швов. При сварке цилиндрических сосудов из нескольких обечаек сначала выполняют продольные швы обечаек, а затем сваривают обечайки между собой кольцевыми швами. При ручной и полуавтоматической сварке швов большой протяженности рекомендуется применение обратноступенчатого порядка наложения сварных швов.
Уравновешивание деформаций. Для уравновешивания деформаций двухсторонних швов назначают такую последовательность их выполнения, при которой последующий шов должен вызывать деформации обратного направления по сравнению с деформациями от предыдущего шва. Этот способ эффективен при симметричном расположении швов.
Жесткое закрепление деталей при сварке. Закрепление свариваемых деталей в сборочно-сварочных приспособлениях, обладающих значительной жесткостью, снижают деформации. Однако после сварки в швах возрастут внутренние напряжения.
Мероприятия, выполняемые после сварки. В тех случаях, когда деформации произошли и величина их выходит за пределы допустимых, применяется правка сварных изделий различными способами.
Механическая правка выполняется молотами, домкратами, винтовыми прессами или другими устройствами. С их помощью создается ударная или статическая нагрузка, которая обычно прилагается со стороны наибольшего выгиба изделия.
Следует иметь в виду, что неправильное выполнение механической правки может привести к образованию трещин и надрывов.
Изделия из тонколистового металла можно править путем прокатывания их между валками. При этом на сварные швы предварительно устанавливаются накладки. В результате такой прокатки сварные швы растягиваются, с образованием пластических деформаций. Это не только обеспечивает правку, но и снижает остаточные напряжения.
Термическая правка заключается в местном нагреве небольших участков металла деформированной конструкции. Нагрев, как правило, производят сварочными горелками большой мощности. Он ведется быстро и только до пластического состояния верхних волокон на выпуклой стороне изделия. При охлаждении нагретых участков они сжимаются и выпрямляют изделие. Исправление деформации сварной тавровой балки производится нагревом выпуклой части вертикальной стенки. Ширина полос нагрева 20—30 мм. Полосы нагрева сходятся под углом 30°. При правке сварных швеллеров помимо треугольных участков нагрева, располагаемых на обеих полках, производится нагрев нескольких полос на его стенке. Нагревать нужно ту поверхность, сжатие которой придает изделию правильную форму. Температура нагрева поверхности зависит от толщины металла и может быть выбрана из табл. 1.
Для определения температуры нагрева можно пользоваться таблицами температур, соответствующих различным цветам нагрева стали и появлению цветов побежалости. Особенно внимательно следует выполнять нагрев при правке на улице в солнечные дни, так как наличие яркого освещения искажает цвет нагреваемого участка. Более точно контроль температуры нагрева может осуществляться оптическими или радиационными пирометрами.
Таблица 1
Температуры нагрева стали при термической правке
Толщина металла, мм | до 6 | 7…12 | 13…20 | свыше 20 |
Температура нагрева, °С | 300…500 | 500…650 | 650…800 | 800…850 |
Термомеханическая правка состоит в сочетании местного нагрева и приложения статической нагрузки, изгибающей исправляемый элемент конструкции в нужном направлении. Эта нагрузка может создаваться домкратами, прессами и другими устройствами. Применение дополнительного усилия способствует более интенсивному воздействию нагрева. Такой способ обычно применяется для правки жестких сварных узлов.
Все способы правки целесообразно вести в приспособлениях, позволяющих контролировать размеры выпрямляемых элементов и его прогибы.
2.6.3. Методы снижения сварочных напряжений
Существует несколько методов уменьшения внутренних напряжений. Наиболее часто применяется предварительный или сопутствующий подогрев при сварке, проковка или прокатка сварных швов, статическое нагружение сварной конструкции, отпуск после сварки и др.
Предварительный или сопутствующий подогрев применяется при сварке сталей, склонных к закалке и образованию трещин. Температуру подогрева выбирают в зависимости от марки стали и жесткости конструкции. Обычно она лежит в пределах 100—600° С. Подогрев производится многопламенными горёлками, индукторами или в печах.
Подогрев уменьшает градиент температур между сварочной зоной и основным металлом. Это приводит к уменьшению пластических деформаций сжатия, что значительно снижает остаточные напряжения. При сварке углеродистых сталей наличие подогрева 100…250°С позволяет не применять термическую обработку после сварки. При сварке строительных сталей подогрев до 150…200°С снижает допустимую температуру сварки до минус 25°С. При сварке теплоустойчивых сталей подогрев 150…350°С позволяет увеличить толщину свариваемых деталей с 10 до 25 мм и более. Кроме того, в ряде случаев подогрев благоприятно влияет на структуру металла шва и околошовной зоны.
Послойная проковка швов выполняется пневматическим зубилом с закругленным бойком непосредственно после сварки по горячему металлу (горячая проковка) или после его полного остывания (холодная проковка). Благодаря осадке металла в направлении удара происходит его раздача в разные стороны, что снижает растягивающие напряжения. Проковка рекомендуется при многослойной сварке металла большой толщины, причем во избежание трещин и надрывов первый и последний слои многослойного шва не проковывают. Швы на металле, склонном к закалке, проковывать нельзя. Преимущество проковки состоит в ее простоте и маневренности.
Прокатка шва выполняется при сварке тонколистового металла. В процессе прокатки растягивающие напряжения уменьшаются. Преимущество ее перед проковкой состоит в статическом характере приложения давления и возможности плавном регулировки его.
Статическое нагружение элементов сварной конструкции возможно в процессе сварки или чаще после полного остывания шва. В качестве нагружения применяется растяжение или изгиб с образованием растягивающих напряжений в зонах, где остаточные напряжения максимальны. Это приводит к пластическим деформациям и значительному уменьшению остаточных напряжений.
Отпуск после сварки обычно применяется для выравнивания структуры шва и околошовной зоны, приводит к снижению внутренних напряжений. Отпуск может быть общий, когда нагревается все изделие, и местный, в случае нагрева лишь зоны сварного соединения. Преимущество общего отпуска состоит в том, что снижение напряжений происходит во всей сварной конструкции, независимо от ее сложности. Различают два основных вида отпуска. Наиболее часто применяется высокий отпуск при температуре нагрева 580…680° С. Операция отпуска состоит из четырех стадий: нагрев, выравнивание температуры по длине и сечению изделия, выдержка при температуре отпуска и охлаждение. Выдержка составляет 1 час. Такой отпуск на 80…90% снижает сварочные напряжения за счет их релаксации. Последняя связана с микропластической деформацией или распадом твердого раствора. Такой отпуск преследует только цель снижения напряжений. Если высокий отпуск проводится в течение 2…3 часов, возможно получить положительное изменение механических свойств. В частности, за указанное время происходит выделение вторичных фаз и их коагуляция. В результате снижается твердость, а пластичность и трещиностойкость возрастают. Чтобы падение прочности при этом было незначительным (до 10…20МПа) температура отпуска сварного соединения должна быть несколько меньше температуры отпуска свариваемой стали или свариваемая сталь должна быть легирована ванадием, молибденом.
При сварке сталей III группы свариваемости, при технологиях предусматривающих длительный термический цикл сварки, например, электрошлаковая сварка, вместо отпуска применяют нормализацию для измельчения зерна. Отпуск сварных конструкций значительно превосходит все методы снятия внутренних напряжений.
2.7. Контроль качества сварки
Контроль качества сварочных работ начинается еще до того, как сварщик приступил к сварке изделия. При этом проверяют качество основного металла, сварочных материалов (электродов, сварочной проволоки, флюса и др.), заготовок, поступающих на сборку, состояние сварочной аппаратуры и качество сборки, а также квалификацию сварщиков. Все эти мероприятия носят название предварительного контроля. В процессе выполнения сварочных работ проверяют внешний вид шва, его геометрические размеры, производят обмер изделия, осуществляют постоянное наблюдение за исправностью сварочной аппаратуры, за выполнением технологического процесса. Указанные операции составляют текущий контроль.
Окончательной контрольной операцией является проверка качества сварки в готовом изделии. Для этой цели существуют следующие виды контроля: внешний осмотр и обмер сварных швов, испытание на плотность, просвечивание рентгеновскими или гамма-лучами, контроль ультразвуком, магнитные методы контроля, люминесцентный метод контроля, металлографические исследования, механические испытания.
Вид контроля качества швов сварных соединений выбирают в зависимости от назначения изделия и требований, которые предъявляются к этому изделию техническими условиями или государственными стандартами. При выборе вида контроля следует руководствоваться ГОСТ 3242 - 79.
Проверка квалификации сварщиков. Квалификацию сварщиков проверяют установлением разряда, при допущении к выполнению ответственных сварочных работ, инспектируемых надзорными органами, непосредственно перед изготовлением ответственной конструкции. В каждом случае проверяют как теоретические знания, так и практические навыки.
Разряд сварщика устанавливают согласно требованиям, предусмотренным тарифно-квалификационными справочниками. Испытание сварщиков перед допуском к ответственным работам производят по правилам аттестации сварщиков, утвержденным Государственным комитетом по надзору за безопасным ведением работ в промышленности и надзорными органами (Ростехнадзор, Регистр, Госатомнадзор и пр.)
После удовлетворительной сдачи испытаний специальной комиссии, сварщикам выдают удостоверение на право выполнения ответственных сварочных работ. В удостоверении указывают конструкции, которые может сваривать сварщик. Сварщики, допускаемые к ответственным работам, должны проходить ежегодные практические и теоретические испытания. Для выполнения ответственных работ по сварке специальных сталей сварщики проходят дополнительные испытания.
2.7.1. Контроль качества исходных материалов
Контроль качества основного металла. Качество основного металла должно соответствовать требованиям сертификата, который посылают заводы-поставщики вместе с партией металла. В нем указывают наименование завода-изготовителя, марку и химический состав стали, номер плавки, профиль и размер материала, массу металла и номер партии, результаты всех испытаний, предусмотренных стандартом, номер стандарта на сталь данной марки. При отсутствии сертификата металл запускают в производство лишь после тщательной проверки: проведения наружного осмотра, выполнения пробы на свариваемость, установления механических свойств и химического состава металла.
При наружном осмотре металла проверяют отсутствие окалины, ржавчины, трещин, расслоения и прочих дефектов. Предварительная проверка металла с целью обнаружения дефектов поверхности является необходимой и обязательной, поскольку она предупреждает применение некачественного металла для сварки изделия.
Механические свойства основного металла определяют испытаниями стандартных образцов. На прессах и копрах в соответствии с ГОСТ 1497 - 73 «Металлы. Методы испытания на растяжение», ГОСТ 14019-80 — «Металлы. Методы технологических испытаний на изгиб», ГОСТ 9454-78 «Металлы. Метод испытания на ударный изгиб при пониженной, нормальной и повышенной температурах».
Контроль качества сварочной проволоки. ГОСТ 2246-70 на сварочную проволоку и ГОСТ 10543-75 на проволоку стальную наплавочную устанавливают марку и диаметры сварочной проволоки, химический состав, правила приемки и методы испытания, требования к упаковке, маркировке, транспортированию и хранению. Каждая бухта сварочной проволоки должна иметь металлическую бирку, на которой указано наименование и товарный знак предприятия-изготовителя, условное обозначение проволоки согласно стандарту и номер партии.
В сертификате, сопровождающем партию проволоки, имеются следующие данные: товарный знак предприятия-изготовителя, условное обозначение проволоки, номерплавки и партии, состояние поверхности проволоки (омедненная или неомедненная), химический состав в процентах, результаты испытаний на растяжение, масса проволоки (нетто) в килограммах.
Таким образом, наличие бирки, прикрепленной к бухте сварочной проволоки, а также сертификата на проволоку является гарантией того, что проволока пригодна для сварки. На поверхности сварочной проволоки не должно быть окалины, ржавчины, грязи и масла. Проволока из высоколегированной стали не должна иметь остатков графитовой смазки.
Сварочную проволоку, на которую не имеется документации, подвергают тщательному контролю. Наиболее важным является проверка химического состава проволоки, для чего от каждой партии отбирают 0,5 % бухт, но не менее двух. Стружку для химического анализа берут от обоих концов каждой контролируемой бухты или из двух участков на расстоянии не менее 5 м один от другого. Произведя химический анализ, устанавливают марку сварочной проволоки и определяют возможность ее применения для сварки в соответствии с технологическим процессом.
Контроль качества электродов. При сварке конструкций, в чертежах которых указан тип электрода, нельзя применять электроды, не имеющие сертификата. Электроды без сертификата можно использовать после тщательной проверки. При этом в соответствии с ГОСТ 9466-75, ГОСТ 9467-75, ГОСТ 10051-75 проверяют прочность покрытия, сварочные свойства электродов, определяют механические свойства металла шва и сварного соединения на образцах, сваренных электродами из проверяемой партии. О пригодности электродов для сварки судят также и по качеству наплавленного металла, который не должен иметь пор, трещин и шлаковых включений. Внешний вид электродов должен удовлетворять требованиям стандарта: покрытие электрода должно быть прочным, плотным, без пор, трещин, вздутий и комков неразмещенных компонентов. Электроды с отсыревшим покрытием в производство не допускаются.
Контроль качества флюсов. Флюс проверяют на однородность по внешнему виду, определяют его химический состав, размер зерна, объемную массу и влажность. Технические требования и методы испытания широко применяемых плавленых флюсов АН-348А, ОСЦ-45, АН-348АН, ОСЦ-45М, АН-8, АН-20С и других регламентированы ГОСТ 9087-81. Например, для определения влажности флюса берут навеску в 100 г, сушат ее при температуре 105+5°С и взвешивают через определенные промежутки времени. Когда результаты предпоследнего и последнего взвешивания будут одинаковы, дальнейшую сушку прекращают. По разности между последним и первым взвешиванием определяют количество содержащейся во флюсе влаги. Во избежание образования пор в металле шва влажность должна быть не более 0,1 %.
Лучшим способом определения качества флюса является его испытание при сварке. Дуга под флюсом должна гореть устойчиво. Поверхность шва должна быть чистой, без пор, свищей и трещин. После остывания шва шлак должен легко отделяться от металла.
2.7.2. Контроль заготовок
Перед поступлением заготовок на сборку проверяют чистоту поверхности металла, габаритные размеры заготовок, качество подготовки кромок и углы их скоса.
Дефекты заготовок в значительной степени сказываются на качестве и производительности сварочных работ. Например, увеличение угла скоса кромок приводит к увеличению количества наплавленного металла, к увеличению времени сварки и к излишнему расходу электроэнергии и электродов. Кроме того, соединение после сварки будет сильнее деформироваться, т. к. чем больше наплавленного металла, тем больше его усадка при остывании. Предупреждение дефектов в заготовках избавит от лишней работы по их исправлению.
2.7.3. Контроль сборки
В собранном узле контролируются зазоры между кромками свариваемых деталей. Отсутствие или малая величина зазора приводит к непровару корня шва, а большая — к прожогу и увеличению трудоемкости процесса сварки. Превышение одной кромки относительно другой в стыковом соединении, как правило, приводит к неравномерному проплавлению, ассиметрии шва и образованию подрезов.
2.7.4. Контроль технологического процесса
Перед тем как приступить к сварке, сварщик знакомится с технологическими картами, в которых указаны последовательность операций, диаметр и марка применяемых электродов, режимы сварки и требуемые размеры сварных швов. Несоблюдение порядка наложения швов может вызвать значительную деформацию изделия, трудно устранимую впоследствии.
Не менее важным является соблюдение режима сварки. Силу сварочного тока и напряжение на дуге контролируют по показаниям амперметра и вольтметра. Скорость сварки и скорость подачи электродной проволоки определяют по сменным шестерням и по положению регулятора скорости, а также непосредственными замерами.
При ручной дуговой сварке, кроме наблюдения за показаниями амперметра, проверяют технику наложения шва. После того как закончена сварка изделия, сварные швы зачищают от шлака, наплывов, а поверхность узла — от брызг металла. Затем готовое изделие проходит ряд контрольных операций.
2.7.5. Контроль качества сварки готового изделия
Внешний осмотр и обмер сварных швов. Внешним осмотром выявляют несоответствие шва требуемым геометрическим размерам. Швы проверяют на наличие наплывов, подрезов, глубоких картеров, прожогов, наружных трещин, непроваров, свищей, пор и других внешних дефектов.
Размеры швов должны соответствовать указанным на чертеже. Не допускается уменьшение фактического размера шва по сравнению с заданным (номинальным) размером.
Методы контроля плотности сварных швов. Испытаниям на плотность подвергают емкости для горючего, масла, воды, а также трубопроводы, газгольдеры, паровые котлы и др. Существуют несколько методов контроля плотности сварных швов. Методы испытаний на непроницаемость и герметичность корпусов металлических судов регламентированы ГОСТ 3285-77, метод испытания металлических труб гидравлическим давлением — ГОСТ 3845-75. Нормы и правила гидравлических и воздушных испытаний машин, механизмов, паровых котлов, сосудов и аппаратов судов указаны в ГОСТ 22161—76.
Гидравлическое испытание. При этом методе испытания в сосуде после наполнения его водой с помощью насоса или гидравлического пресса создают избыточное давление. Давление при испытании обычно берут в 1,5—2 раза больше рабочего. Величину давления определяют по проверенному и опломбированному манометру. Испытываемый сосуд под давлением выдерживают в течение 5…10 мин. За это время швы осматривают на отсутствие течи, капель и отпотеваний. Для гидравлического испытания применяют не только воду, но и авиационное масло или дизельное топливо (при контроле плотности швов в масляных и топливных баках, трубопроводах).
Кроме того, испытание может производиться наливом воды. Так испытывают вертикальные резервуары для хранения нефти и нефтепродуктов, газгольдеры и другие емкости.
Пневматическое испытание. При пневматическом испытании сжатый газ (воздух, азот, инертные газы) или пар подают в испытываемый сосуд. Сосуды небольшого объема погружают в ванну с водой, где по выходящим через неплотности в швах пузырькам газа обнаруживают дефектные места. Более крупные сварные резервуары и трубопроводы испытывают путем смазывания сварных швов пенным индикатором. Наиболее распространённым пенным индикатором является водный раствор мыла. Для испытания при отрицательных температурах пригодны смесь мыльного раствора с глицерином, льняное масло и др.
При пневматических испытаниях необходимо строго соблюдать правила техники безопасности. На подводящей магистрали должны быть запорные краны и предохранительные клапаны. Кроме рабочего манометра при испытаниях предусматривают контрольный манометр. При испытании под давлением не допускается обстукивание сварных швов и исправление дефектов.
Вакуум-испытания. Участок шва, проверяемый на плотность, смачивают водным раствором мыла. На шов устанавливают вакуум-камеру, представляющую собой коробку с открытым дном и прозрачной верхней крышкой из плексигласа. По контуру открытого дна вакуум-камера имеет резиновое уплотнение. Из камеры выкачивают воздух до определенного разрежения. По вспениванию мыльного раствора, которое наблюдают через крышку, обнаруживают расположение дефектов. Этот метод нашел применение при контроле стыковых швов днищ резервуаров.
Испытание керосином. Этот метод испытания основан на явлении капиллярности, которое заключается в способности многих жидкостей, в том числе и керосина, подниматься по капиллярным трубкам (трубкам малого поперечного сечения). Такими капиллярными трубками являются сквозные поры и трещины в металле сварного шва. Одну сторону стыкового шва покрывают водным раствором мела, после высыхания которого другую сторону смачивают керосином. Время выдержки изделия после смачивания керосином зависит от толщины свариваемых деталей: чем больше толщина и чем ниже температура воздуха, тем больше время выдержки.
Испытание аммиаком. Сущность этого метода заключается в том, что испытываемые швы покрывают бумажной лентой или марлей, которая пропитана 5 % - ным водным раствором азотнокислой ртути или фенолфталеином. В изделие нагнетается воздух до определенного давления и одновременно подают некоторое количество газа (аммиака). Проходя через поры шва, аммиак оставляет на бумаге черные (бумага пропитана раствором азотнокислой ртути) или красные (фенолфталеиновая бумага) пятна.
Испытания с помощью течеискателей. При этом методе испытания применяют гелиевые или галоидные течеискатели. При применении гелиевых течеискателей внутри испытываемого сосуда создают вакуум, а снаружи сварные швы обдувают смесью воздуха с гелием. При наличии неплотностей гелий проникает внутрь сосуда, а затем поступает в течеискатель, где имеется специальная аппаратура для его обнаружения.
В случае применения галоидных течеискателей внутри испытываемого сосуда создают избыточное давление и вводят небольшое количество галоидного газа. Газ проникает через неплотности шва, отсасывается снаружи сосуда и поступает в специальную аппаратуру. По наличию галоидного газа определяют не плотность шва..
Этот метод обладает высокой чувствительностью и применяется для контроля ответственных сварных изделий. Для контроля соединений конструкций атомной энергетики применяют гелиевые течеискатели ПТИ-6, ПТИ-7, имеющие чувствительность контроля 10 -7-10 -8 м ´ мкм/см. Значительно меньшую чувствительность (10-4 м ´ мкм/с) имеют галоидные течеискатели ГТИ-2, ГТИ-3, ВАГТИ-4.
Рентгеновское просвечивание. Рентгеновские лучи являются электромагнитными волнами. Они обладают следующими свойствами: способностью проникать сквозь непрозрачные тела; действуют на фотографическую пленку, как и световые; под действием этих лучей некоторые вещества, например сернистый цинк, светятся (люминесцируют); вызывают ионизацию газов, в том числе и воздуха, и делают его электропроводным; в больших дозах вызывают вредное физиологическое действие на живой организм, разрушая его ткани.
В промышленности для просвечивания изделий применяют серийные рентгеновские аппараты типа РУП. Так, аппарат РУП-120-5-1 применяют для просвечивания металла из стали толщиной до 25 мм и легких сплавов толщиной до 100 мм.
Источник излучения (рентгеновскую трубку) помещают на определенном расстоянии от шва, так чтобы лучи были направлены перпендикулярно к его оси. С противоположной стороны крепят светонепроницаемую кассету, которая должна плотно и равномерно прилегать к просвечиваемому участку изделия. В кассете расположены рентгеновская пленка и два усиливающих экрана. При просвечивании пленку выдерживают под лучами определенное время, называемое экспозицией. Экспозиция зависит от толщины просвечиваемого металла, фокусного расстояния, интенсивности излучения и чувствительности пленки. Усиливающие экраны служат для сокращения экспозиции. После просвечивания пленку вынимают из кассеты и проявляют. Затем негатив промывают и фиксируют для получения стойкого фотографического изображения. Полученное на негативе изображение участка шва будет неодинаковым по степени потемнения отдельных мест. Лучи, попавшие на пленку, через дефект поглотятся в меньшей степени по сравнению с лучами, прошедшими через плотный металл, и окажут более сильное засвечивающее действие на определенный участок светочувствительного слоя пленки.
При просвечивании рядом со швом (параллельно ему), со стороны источника излучения, устанавливают дефектометр, который служит для определения глубины залегания и величины обнаруженного дефекта. Дефектометр — это пластинка, изготовленная из того же материала, что и просвечиваемый металл. Толщина пластинки должна быть равна выпуклости шва. На дефектометре имеются канавки различной глубины. При одинаковой интенсивности потемнения пленки под одной из канавок с потемнением дефекта, при известной глубине канавки, определяют величину дефекта (по высоте). Кроме пластинчатых дефектометров применяют проволочные эталоны чувствительности. Качество просвеченного сварного шва определяют сравнением пленки с эталонными снимками, установленными для определенного изделия или группы изделий. Просвечиванием можно обнаружить большинство внутренних дефектов: не провары, поры, включения, крупные трещины.
Просвечивание сварных швов гамма-лучами. Гамма-лучи, так же как и рентгеновские, представляют собой электромагнитные волны. Получение гамма-лучей связано со свойствами некоторых элементов (уран, радий, торий) самопроизвольно испускать лучи. Это явление называется радиоактивностью.
Недостатком применения естественных радиоактивных веществ для просвечивания является их дороговизна. В настоящее время при просвечивании применяют более дешевые искусственные радиоактивные вещества. Их получают облучением какого-либо химического элемента ядерными частицами — нейтронами. Из искусственных радиоактивных изотопов чаще применяют изотопы кобальт - 60, тулий - 170 и иридий - 192.
Из-за вредного действия гамма-лучей на организм человека радиоактивные изотопы хранят в специальных контейнерах.
Для просвечивания в цеховых условиях промышленность выпускает установки ГУП-Со-0,5-1, ГУП-Со-5-1 и ГУП-Со-50.
Техника просвечивания сварных соединений гамма-лучами подобна технике рентгеновского просвечивания.
По сравнению с рентгеновским контролем просвечивание гамма-лучами имеет следующие преимущества: радиоактивный препарат можно установить в такие места конструкции, где не поместится громоздкая рентгеновская установка; гамма-лучами возможно одновременно контролировать несколько деталей, а также кольцевые швы изделий; контейнер с ампулой удобен в полевых условиях, благодаря легкости его транспортирования; затраты на гамма-просвечивание меньше, чем при просвечивании рентгеновскими лучами.
Препарат радиоактивного изотопа кобальт-60 безотказен в работе и может непрерывно использоваться свыше пяти лет. Недостаток просвечивания гамма-лучами — более низкая чувствительность к выявлению дефектов в швах толщиной меньше 50 мм, чем при рентгеновском просвечивании. Методы контроля сварных швов рентгенографированием и гаммаграфированием регламентированы ГОСТ 7512 — 75.
Длительное воздействие на человека больших доз излучения приводит к лучевой болезни. Радиационная безопасность обеспечивается строгим соблюдением «Основных санитарных правил работы с радиоактивными веществами и другими источниками ионизирующих излучений ОСП —72», «Норм радиационной безопасности НРБ —76», «Правил безопасности при транспортировании радиоактивных веществ (ПБТРВ-73).
Ультразвуковой метод контроля. Этот метод основан на способности ультразвуковых волн отражаться от границы раздела двух сред, обладающих разными акустическими свойствами. При помощи ультразвука можно обнаружить трещины, раковины, расслоения в листах, не провары, шлаковые включения, поры.
Ультразвук представляет собой упругие колебания материальной среды с частотой колебания выше 20 кГц, т. е. выше верхней границы слухового восприятия. Существует несколько способов получения ультразвуковых колебаний. Наиболее распространенным является способ, основанный на пьезоэлектрическом эффекте некоторых кристаллов (кварца, сегнетовой соли) или искусственных материалов (титаната бария). Этот эффект заключается в том, что если противоположные грани пластинки, вырезанной из кристалла, например, кварца, заряжать разноименными зарядами электричества, то она будет деформироваться в такт изменения знаков зарядов. Изменяя знаки электрических зарядов с частотой выше 20 тыс. колебаний в секунду, получают механические колебания пьезоэлектрической пластинки той же частоты, передающейся в виде ультразвука.
Работа ультразвуковых дефектоскопов — приборов для выявления дефектов в изделиях, в том числе и в сварных швах — основана на пьезоэлектрическом эффекте. Для проверки качества сварного шва дефектоскоп подключают к сети переменного тока. Рядом со сварным швом устанавливают пьезоэлектрический щуп с пластинкой из титаната бария. Автоматического изменения знаков зарядов на поверхности пластинки достигают при помощи лампового генератора. Если от этого генератора сообщить пластинке импульс электрических колебаний, то пластинка пошлет в шов короткий ультразвуковой импульс такой же частоты. Первоначальный электрический импульс после его усиления в усилителе будет зарегистрирован на экране катодной трубки в виде пика светящегося луча. Попав в бездефектный шов, пучок ультразвука достигает противоположной стороны сварного соединения и, отразившись от него, снова попадает на пластинку. К этому моменту пластинка уже прекратит испускать ультразвук из-за кратковременности электрического импульса. Вместо источника ультразвуковых колебаний она становится их приемником. Ультразвуковые колебания, отразившиеся от дна изделия и попавшие на пластинку, преобразуются в механические, а затем и в электрические колебания. Последние после усиления попадают на катодную трубку осциллографа. На его экране появится донный сигнал в виде пика.
Если же в шве имеется какой-либо дефект, например трещина, то часть пучка ультразвука отразится от нее, а другая часть отразится от противоположной стороны сварного соединения. В этом случае на экране будут видны уже три пика. По среднему пику устанавливают, что в шве залегает какой-то дефект. Расстояние между пиками позволяет определить, на какой глубине находится дефект.
По принципу отражения ультразвуковых волн работают ультразвуковые дефектоскопы типа УЗД-7, УДМ-1М, УДМ-3, с помощью которых можно обнаружить дефекты, расположенные на глубине 1-2500 мм под поверхностью. Методы ультразвукового контроля сварных швов регламентированы ГОСТ 14782 — 76.
Люминесцентный метод контроля основан на свечении некоторых веществ при действии на них ультрафиолетовых лучей. Люминесцентный метод контроля применим для обнаружения поверхностных дефектов, главным образом мельчайших трещин.
Перед контролем исследуемый участок шва очищают от загрязнений, затем на очищенные места наносят жидкий раствор, содержащий люминофор. Таких веществ — люминофоров — известно несколько. Например, раствор дефектоля в бензине светится ярким желто-зеленым светом при освещении его ультрафиолетовыми лучами. После 10 — 15 мин выдержки раствор смывают и изделие сушат в струе теплого воздуха. Подвергая изделие ультрафиолетовому облучению в затемненном помещении, по свечению раствора, оставшегося в трещинах, обнаруживают дефектные места.
Магнитные методы контроля основаны на принципе использования магнитного рассеяния, возникающего над дефектом при намагничивании контролируемого изделия. Если сварной шов не имеет дефектов, то магнитные силовые линии по сечению шва распределяются равномерно. При наличии дефекта в шве вследствие меньшей магнитной проницаемости дефекта магнитный силовой поток будет огибать дефект, создавая магнитные потоки рассеяния.
В зависимости от способа фиксирования потоков рассеяния существуют метод магнитного порошка и индукционный метод. В первом случае неравномерность поля определяют по местам скопления ферромагнитного порошка, нанесенного на поверхность изделия. Во втором случае потоки рассеяния улавливают индукционной катушкой. Изделие намагничивают электромагнитом, соленоидом или пропусканием тока непосредственно через сварное соединение. При выборе метода намагничивания нужно учитывать, что выявление дефектов магнитным методом возможно только в случае, когда они расположены перпендикулярно к направлению магнитного потока.
Существуют два способа контроля магнитным порошком — сухой и мокрый. При сухом способе порошок окиси железа равномерно наносят на поверхность изделия, применяя ручное сито или пульверизатор. Во многих случаях в качестве порошка используют железную окалину, которую предварительно измельчают в шаровой мельнице и просеивают через тонкое сито. В момент пропускания электрического тока изделие слегка обстукивают, что обеспечивает подвижность частиц порошка, распределяющихся в наведенном магнитном поле. Излишек порошка сдувают с детали слабой воздушной струей. При мокром способе применяют, так называемую, магнитную суспензию — смесь какой-либо жидкости (керосин, трансформаторное масло) с магнитным порошком, мельчайшие частицы которого равномерно распределены по ее объему. Операцию контроля начинают с того, что контролируемый участок сварного соединения поливают или опрыскивают суспензией. Дефекты обнаруживают по скоплениям магнитного порошка. Один и тот же участок проверяют дважды. После проверки качества всех сварных швов изделие размагничивают.
Метод магнитного порошка пригоден для контроля только в ферромагнитных материалах. Этим методом можно обнаружить все поверхностные трещины и те внутренние трещины и непровары, которые залегают на глубине до 6 мм. Для контроля сварных соединений применяют магнитные дефектоскопы, выпускаемые промышленностью, например переносный магнитный дефектоскоп типа 77ПМД-ЗМ.
При индукционном методе в контролируемом изделии наводят переменный магнитный поток при помощи электромагнита, подключенного к сети переменного тока. Если в шве есть дефект, магнитные силовые линии поведут себя точно так же, как и при контроле методом магнитного порошка. Рассеянные магнитные поля над дефектом обнаруживают при помощи искателя. Индукционный ток усиливается ламповым усилителем, с которым соединена катушка искателя. Усиленные электрические сигналы попадают на телефон, в котором слышатся резко усиленные звуки. Одновременно с этим загорается сигнальная лампа.
В отечественной промышленности применяют следующие индукционные дефектоскопы: ЭМНД-2, ЭМНД-3, ЭМНД-4, ЭМНД-6, ЭМНД-8, ДНМ-500, ДНМ-15, ППД-1, ВД-1, ВД-1ГА, ЭДМ-66 и др.
Разновидностью магнитной дефектоскопии является магнитографический способ контроля, при котором поля рассеяния фиксируются на ферромагнитной ленте. Наиболее совершенными магнитографическими дефектоскопами являются МДУ-29, МГК-1.
Магнитные методы контроля часто применяют для составления предварительного заключения о качестве сварного соединения. Окончательное установление качества производится по снимку, полученному просвечиванием рентгеновскими или гамма-лучами.
Металлографические исследования. Посредством металлографического анализа проверяют качество структуры металла сварного соединения. В зависимости от того, с каким увеличением рассматривают зерно металла, различают макроструктуру и микроструктуру.
Под макроструктурой понимают структуру металла сварного соединения, рассматриваемую или в натуральную величину или через лупу. Макроструктуру исследуют на шлифах, травленых специальными реактивами. После травления на макрошлифе ясно видны дефекты, попавшие в его сечение. Кроме того, на макрошлифе можно обнаружить скопления серы и фосфора по границам кристаллов. Скопление серы выявляют следующим образом: на макрошлиф накладывают засвеченный листок фотобумаги, смоченный 15%-ным раствором серной кислоты. В тех местах, где бумага соприкасалась с сернистыми включениями, на ней остаются коричневые пятна. Макроструктуру исследуют не только на специально обработанных шлифах, но и по излому образцов после их механических испытаний. Макрошлиф или излом сварного соединения исследуют тогда, когда программой испытания предусмотрено изготовление контрольных образцов.
Макроконтроль сварного соединения можно осуществлять также с помощью сверления. В этом случае определенное место шва сверлят так, чтобы образовавшееся углубление вскрыло вершину шва. Засверленное место шлифуют наждачной бумагой, затем травят реактивом, рассматривают через лупу и в случае отсутствия дефектов снова заваривают.
В отличие от макроскопического исследования, которое дает представление о металле шва в целом, при микроскопическом исследовании изучают отдельные участки сварного соединения. Микроисследование проводят при помощи микроскопа с увеличением в 100 — 500 раз. Микроисследование позволяет выявить размер и форму зерен, фазовый состав зоны термического влияния, дефекты структуры, микротрещины и пр.
Для закаливающихся сталей важно определять наличие мартенсита или бейнита, для сталей аустенитного класса металлографически можно определить присутствие и место расположения ферритных включений. При анализе кинетики превращения перлита в аустенит (при нагреве) микроскопически определяется степень растворения карбидной фазы, а, следовательно, гомогенность аустенита.
Такие данные дают возможность выбирать режимы и способы сварки. Например, в условиях автоматической сварки под флюсом и ручной дуговой сварки при малых и средних значениях погонной энергии дуги процесс растворения карбидной фазы, как правило, не завершается. Это приводит в дальнейшем к образованию малолегированного мартенсита с пониженными механическими свойствами.
Микроскопический анализ позволяет определить допустимую скорость охлаждения у закаливающихся сталей. Допустимой считается такая скорость охлаждения, после которой в структуре обнаруживается не более 25…30% мартенсита. Только металлография позволяет определить характер и места залегания холодных и горячих трещин относительно положения шва, зоны термического влияния или линии сплавления.
2.8.Организация технического контроля
Схема контроля качества продукции на заводах определяется условиями производства. На каждом заводе имеется отдел технического контроля (ОТК), который подчиняется непосредственно директору завода. На многих заводах применяется смешанная система контроля. ОТКзавода контролирует исходные материалы и производит окончательный контроль готовой продукции. Контрольные же операции в процессе производства производят контролеры цеха, которые подчиняются начальнику цеха. В случае установившегося технологического процесса контрольные функции могут быть возложены на мастеров, бригадиров и самих рабочих. При этом ОТК производит выборочную проверку качества сварки отдельных узлов, деталей и операций.
Объем контроля зависит от степени ответственности изделия, квалификации производственного и контролируемого персонала, степени освоения технологии производства. Объем контроля указывается в правилах контроля или в технических условиях.
2.9. Разработка технологии сборки и сварки
Под технологией подразумевают указания о выборе вида сварки, способа сборки элементов конструкции, геометрических размеров разделки кромок, химического состава сварочных материалов, режимов сварки и приемов, выполнение которых обеспечивает получение сварного соединения необходимого качества. В технологию входит также общая последовательность сборки и сварки всей конструкции.
При разработке технологии сварки необходимо знание марки основного металла, его химического состава и состояния поставки (тип термообработки и пр.), толщины элементов конструкции в местах их соединений, пространственное положение и эксплуатационные требования к сварному соединению. Эта информация берется из следующих документов: чертежа конструкции[*], технических условий, сертификата качества, государственных стандартов на поставку стали данной марки, эксплуатационных требований, предусмотренных в различных руководящих материалах, а также условий установленных конструктором.
После выбора способа сварки рассматриваемой конструкции на чертеже согласно ГОСТ 2.312-72 следует обозначить виды сварных соединений и швов. Наиболее благоприятными с точки зрения несущей способности конструкции являются стыковые соединения. Однако из конструктивных соображений применяются также тавровые, угловые и нахлёсточные соединения. Сварные соединения, независимо от типа, начиная с определенной толщины свариваемого металла, имеет разделку кромок, предназначенную для обеспечения полного проплавления всего сечения. Параметры разделки для различных типов сварных соединений определяются толщиной свариваемого металла.
Основные типы, конструктивные элементы и размеры для ручной дуговой сварки представлены в ГОСТ 5264-80, ГОСТ 11534-75; для сварки в защитном газе – в ГОСТ 14771-76, ГОСТ 23518-79; для сварки под слоем флюса – в ГОСТ 8713 –79, ГОСТ 11533-75; ГОСТ 14776-79 – соединения сварные точечные, выполняемые дуговой сваркой; ГОСТ 14806-80 – соединения из алюминия и алюминиевых сплавов, выполняемые дуговой сваркой; ГОСТ 15164-78 – соединения сварные, выполненные электрошлаковой сваркой; ГОСТ 15878-79 – соединения, выполняемые контактной сваркой; ГОСТ 16310-80 – соединения сварные и выполняемые из винипласта.
При выборе разделки следует исходить из максимальной производительности и качества сварного соединения. Если при сварке стыковых соединений принята сварка штучными электродами, то лучше всего выбрать соединения с симметричной двусторонней Х-образной разделкой с минимальным углом раскрытия кромок. Это уменьшает количество наплавленного металла, а значит и увеличивает производительность процесса. Кроме того, наличие одинакового количества наплавленного металла с обеих сторон соединения приводит к уменьшению деформаций. При этом следует руководствоваться также доступностью сварного соединения для выполнения его при данном способе сварки. В случае невозможности выполнения сварки соединения с симметричной разделкой применяется соединение с V - образной разделкой кромок и подваркой корня шва. Выбранный тип сварного соединения, способ сварки и условное обозначение шва, должен быть изображен на чертеже.
2.9.1.Пример технологического процесса сборки и сварки
Технологический процесс сборки и сварки элементов технологического трубопровода вольфрамовым электродом в среде аргона:
005 КОМПЛЕКТОВАНИЕ
1. Укомплектовать сборку деталями согласно спецификации совместно с сопроводительной документацией.
2. Оформить технологический паспорт.
010 КОНТРОЛЬ
1. Проверить наличие аттестации: инженерно-технических работников, дефектоскопистов, контролеров, сварщиков.
2. Проконтролировать периодичность проверки исправности сборочно-сварочного оборудования, приспособлений и аппаратуры в соответствии с графиком.
3. Проверить комплектность заготовок по спецификации.
4. Проверить изготовление входящих деталей по техническому паспорту.
5. Проверить результаты входного контроля сварочных материалов.
6. Проверить маркировку.
7. Результаты контроля зафиксировать в технологическом паспорте.
015 СЛЕСАРНАЯ
Плита сборочная, инструмент слесарный,
Очки защитные ГОСТ 12.4.013-85,
1. Зачистить на деталях места под сварку и зоны, прилегающие к ним до чистого металла и обезжирить.
АЦЕТОН ГОСТ 2603-79; БЯЗЬ ГОСТ 11680-83
НЕФРАС С4-155/200 (УАЙТ-СПИРИТ) ГОСТ 3134-83.
2. Зачистку производить на ширине не менее 20 мм от края свариваемых кромок.
020 КОНТРОЛЬ
Согласно инструкции ЛА-8-208.00 000 ТИ.
1. Проверить чистоту поверхностей под сварку согласно инструкции ЛА-8-208-00.000 ТИ.
2. Произвести контроль кромок визуальным и измерительным контролем согласно инструкции
ЛА-8-208. 00.000ТИ.
3. Наличие грязи, жировых и окисных пленок, сколов, трещин не допускается..
4. Результаты контроля зафиксировать в технологическом паспорте.
025 СБОРКА
Сборку производить в соответствие с ЛА-8-208.00.000ТИ.
Плита сборочная слесарь 5
1. Застропить и установить на сборочно-сварочной плите детали конструкции за счет болтов и опор, выставив необходимые размеры.
Прихватить собранные детали на режимах (см. операция "СВАРКА").
2. Смещение кромок не более 0,5 мм..
3. Результаты контроля зафиксировать в журнале учета контроля сборочно-сварочных работ.
030 КОНТРОЛЬ
согласно инструкции ЛА-8-208.00.000ТИ, контролер.
1. Проверить сборку под сварку на соответствие требованиям чертежа.
2. Проверить качество прихваток визуальным осмотром, дефекты не допускаются.
3. Результаты контроля зафиксировать в журнале учета контроля сборочно-сварочных работ.
035 СВАРКА
Согласно инструкции ЛА-8-208.00.000ТИ.
Пост автоматической аргонодуговой сварки электросварщик, 3-й разряд:
-расход аргона в горелку (8-10) л / мин;
-диаметр вольфрамового электрода 3 мм;
-ток постоянный, прямой полярности;
-сила тока для корневого шва (100-110) А;
-сила тока для заполнения разделки (160-180) А;
1. Прихватить детали аргонодуговой сваркой в 2-3 точках. Длина прихваток 4-7 мм.
2. Проверить на отсутствие смещения кромок.
3. Сварить детали, собранные в операции 025, аргонодуговой сваркой согласно чертежу.
Аргон "ВС" ГОСТ 10157 (8-10) л/мин.
Вольфрам ЭВИ-3 ТУ 11 СУ.021.099-72 ф3 мм.
Проволока Св-08Г2С ГОСТ 2246-70 ф1,4 мм.
040 КОНТРОЛЬ
Согласно инструкции ЛА-8-208.00.000ТИ, контролер.
1. Визуальный и измерительный контроль в процессе сварки.
2. Результаты контроля зафиксировать в журнале учета контроля.
045 СЛЕСАРНАЯ
1. Сварные швы клеймить клеймом сварщика.
2. Маркировать порядковым номером сборочной единицы Способ маркировки - ударный.
050 КОНТРОЛЬ
Согласно инструкции ЛА-8-208.00.000.ТИ, контролер.
1. Проверить качество сварного соединения визуальным и измерительным контролем.
2. Проверить маркировку.
3. Результаты зафиксировать в журнале учета контроля сборочно-сварочных работ.
4. Оформить протокол.
055 КОНТРОЛЬ ВИЗУАЛЬНЫЙ
Согласно инструкции ЛА 8-208.00.000.ТИ.
1. Проверить качество сварных швов визуальным контролем методом, в объёме 100%.
2. Результаты зафиксировать в журнале учета контроля сварных соединений.
3. Оформить заключение.
060 КОНТРОЛЬ РАДИОГРАФИЧЕСКИЙ ГОСТ 7512-82 или УЛЬТРАЗВУКОВОЙ ГОСТ 14782-86
1.Ультразвуковой контроль выполнять в соответствии с требованиями ОСТ 262044-83, а радиографический - в соответствии с ОСТ 26-11-03-84.
2. В сварных соединениях не допускаются внутренние дефекты перечисленные в п.3.11.4. настоящей ТИ.
3. Проверить наличие клейм сварщика на поверхности деталей согласно п.4.28. настоящей ТИ.
4. Все сварные соединения подвергнуть гидравлическому испытанию при Рпроб., указанному в чертежах согласно требованиям п.5.11 ОСТ 26291-94, предварительно очистив поверхности швов от флюса и окислов согласно п.5.10 настоящей ТИ.
2.10.Нормирование сборочно-сварочных работ
Основное время (t0) для всех способов сварки плавящимся электродом определяется по формуле
![]() | (7) |
где – масса наплавленного металла;
I – сила тока;
ан – коэффициент наплавки.
Общее время для всех способов можно округлять, используя коэффициент загрузки сварочного оборудования (k3), величина которого изменяется в широких пределах. Для расчетов в курсовом проекте k3 может быть принят равным 0,7...0,8. Тогда полное время будет
![]() | (8) |
Некоторые трудности представляет нормирование операций сборки изделий. Допускается использование следующего метода. По данным предприятия и пронормированных технологических процессов для аналогичных изделий или их частей (сварных узлов) устанавливается отношение трудоемкости сборки к сварке
![]() | (9) |
где – трудоемкость сборки;
– трудоемкость сварки;
k1 – коэффициент приведения трудоемкости сборки к трудоемкости сварки.
2.11.Расчет уровня механизации
Уровень механизации сварочных работ согласно методике Института электросварки им. Е.О.Патона выражается в процентах по формуле
![]() | (10) |
где – уровень механизации;
k – коэффициент приведения, с помощью которого трудоемкость механизированных работ
приводится к трудоемкости ручной сварки;
Тр – трудоемкость ручной сварки;
Тм – трудоемкость механизированной сварки.
В том случае, когда сварка данного изделия производится различными способами (автоматическим, полуавтоматическим, контактным и т.п.), уровень механизации определяется по формуле
![]() | (11) |
где k1, k2, ki – коэффициенты приведения трудоемкости применяемых механизированных процессов
сварки к трудоемкости ручной сварки.
Величины этих коэффициентов приведения для расчетов в курсовых проектах следующие:
1. Автоматическая сварка под флюсом:
на обычных режимах – 3;
на форсированных режимах – 4,5.
2. Полуавтоматическая сварка под флюсом – 1,5.
3. Автоматическая и полуавтоматическая сварка в среде защитных газов – 2.
4. Контактная сварка:
на машинах с механизированным приводом – 7;
на машинах с немеханизированным приводом – 3,5;
на специализированных высокопроизводительных машинах – 8.
Расчет годового выпуска продукции на одного производственного рабочего определяется по формуле
![]() | (12) |
где g – выпуск продукции, т/чел;
n – число производственных рабочих;
Q – годовой выпуск продукции, т.
Расчет съема продукции с 1м2 площади участка определяется по формуле
![]() | (13) |
где g – годовой съем продукции, т/м2;
F – площадь участка, м2;
Q – годовой выпуск продукции, ч.
Дата добавления: 2021-06-02; просмотров: 999; Мы поможем в написании вашей работы! |
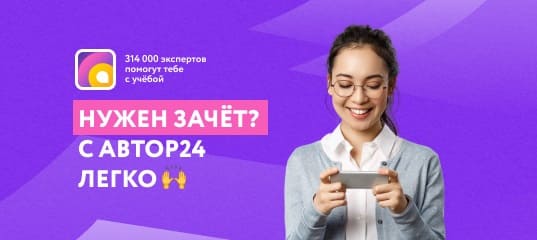
Мы поможем в написании ваших работ!