Указания к выполнению курсового проекта
ОГЛАВЛЕНИЕ
введение 4
1. порядок проектирования 5
2. Указания к выполнению курсового проекта... 5
2.1. Оценка свариваемости основного металла конструкции.. 5
2.2. Выбор способа сварки.. 9
2.3. Выбор сварочных материалов.. 10
2.4. Выбор режимов сварки.. 10
2.5.Выбор сварочного оборудования.. 11
2.5.1. Применение сборочно-сварочных приспособлений.. 15
2.5.2. Применение роботизированных комплексов.. 18
2.6. Мероприятия, обеспечивающие заданные размеры и форму конструкции.. 19
2.6.1.Образование сварочных напряжений и деформаций.. 19
2.6.2. Методы борьбы с деформациями.. 20
2.6.3. Методы снижения сварочных напряжений.. 22
2.7. Контроль качества сварки.. 23
2.7.1. Контроль качества исходных материалов.. 23
2.7.2. Контроль заготовок.. 24
2.7.3. Контроль сборки.. 25
2.7.4. Контроль технологического процесса.. 25
2.7.5. Контроль качества сварки готового изделия.. 25
2.8.Организация технического контроля.. 30
2.9. Разработка технологии сборки и сварки.. 30
2.9.1.Пример технологического процесса сборки и сварки.. 31
2.10.Нормирование сборочно-сварочных работ.. 32
2.11.Расчет уровня механизации.. 33
3. Пример расчета технико-экономических показателей проекта... 34
ЛИТЕРАТУРА.. 38
ПРИЛОЖЕНИЕ: КАТАЛОГ ЧЕРТЕЖЕЙ СВАРНЫХ КОНСТРУКЦИЙ... 39
Введение
Сварка относится к числу прогрессивных и быстро развивающихся технологий. На сегодняшний день сварка в значительной мере определяет общий технический уровень различных отраслей промышленности.
|
|
Современные сварочные технологии являются результатом глубоких теоретических исследований в области выделения и распределения теплоты при сварке, рационального проектирования сварных конструкций, возникновения сварочных напряжений и деформаций, статической и динамической прочности сварных соединений и конструкций, природы хрупкого разрушения и борьбы с ним, расплавления и кристаллизации сварочной ванны, взаимодействия металлической, шлаковой и газовой фазе в сварочной ванне при различных способах сварки, электросварочного оборудования, источников питания, сварочных материалов.
Дисциплина «Производство сварных конструкций» фактически является результирующей изучения целого ряда специальных курсов. При производстве должны быть учтены свойства свариваемого материала конструктивные особенности сварного изделия, условия его эксплуатации.
Особое значение для разработки технологии сборки и сварки конструкции придается грамотному чтению чертежей. Поэтому пособие снабжено каталогом чертежей, которые подобраны так, чтобы студенты могли применять различные способы сварки, различные приспособления и вспомогательное оборудование.
|
|
Контроль качества сварных соединений и меры по снижению напряжений и деформаций напрямую влияют на конкурентоспособность продукции. Этот вопрос подробно рассмотрен с точки зрения микроструктуры сталей, состояния поставки деталей под сварку, применимости в различных случаях тех или иных способов контроля.
Выбор сварочного оборудования является одним из важнейших этапов проектирования. Актуальность этого вопроса особенно очевидна в современных условиях. Наличие большого числа фирм производителей оборудования, в том числе зарубежных, вызывает необходимость изучения рынка. Поэтому в пособии значительное место занимают вопросы расчета технико-экономических показателей. В реальных условиях производства затраты и окупаемость технологии выходят на первый план.
Материал учебно-методического пособия позволяет не только усвоить дисциплину, но и готовит студентов старших курсов к дипломному проектированию.
Целью курсового проектирования является закрепление студентами в условиях конкретной задачи знаний по выбору оптимального способа сварки, материалов и оборудования, технологии сборки и сварки заданной конструкции, а также адаптация к дипломному проектированию.
|
|
Порядок проектирования
В зависимости от особенностей конструкции, марки основного металла и программы выпуска продукции студент должен:
1. оценить свариваемость материала конструкции;
2. выбрать способ сварки;
3. выбрать сварочные материалы;
4. на чертеже конструкции обозначить швы сварных соединений в согласно ГОСТ 2.312-72;
5. назначить режимы сварки;
6. выбрать сварочное оборудование и оснастку;
7. предложить меры предупреждения или уменьшения сварочных деформаций;
8. назначить виды контроля сварных соединений;
9. разработать технологический процесс сборки и сварки;
10. оценить уровень механизации сборочно-сварочных работ;
11. произвести нормирование сборочно-сварочных работ;
12. выполнить расчет экономической эффективности проекта.
Указания к выполнению курсового проекта
Курсовой проект должен состоять из расчётно-пояснительной записки объёмом 25…30 листов формата А4, оформленные в соответствии с ГОСТ 2.105-95, ГОСТ 2.106-96 и не менее 2 листов чертежей формата А4, включающих общий вид изделия, сварочного оборудования, приспособлений и оснастки, выполненных в соответствии с ЕСКД.
При выполнении курсового проекта необходимо использовать навыки, приобретенные в процессе изучения дисциплин «Технологические основы сварки плавлением и давлением», «Проектирование сварных конструкций», «Сварка специальных сталей», «Компьютерные технологии», «Моделирование сварочных процессов», «Контроль качества сварки».
|
|
При решении задач курсового проектирования студенты должны пользоваться знаниями, полученными при прохождении инженерно-производственной подготовки в цехах, технологических отделах, конструкторских бюро, сварочных и заводских лабораториях базовых предприятий.
Задание на курсовой проект выдается в виде чертежа сварной конструкции, прилагаемого в Прил., марки основного металла и программы выпуска продукции.
Порядковый номер фамилии студента в групповом журнале должен соответствовать номеру чертежа конструкции (Прил.).
В случае если базовым предприятием или руководителем студенту выдано задание на дипломный проект раньше или одновременно с заданием на курсовое проектирование, то часть дипломного проекта, выполненного в объеме курсового проектирования, может быть использована как курсовой проект.
Пояснительная записка содержит:
1. Титульный лист.
2. Цель работы.
3. Оценку свариваемости, выбор технологии, оборудования, приспособлений и мероприятий по контролю.
4. Экономические расчеты.
5. Выводы.
6. Графическую часть.
2.1. Оценка свариваемости основного металла конструкции
Свариваемость - это свойство металла или сплава образовывать при установленной технологии сварки неразъемное соединение, отвечающее требованиям, эксплуатации конструкции. Различают физическую и технологическую свариваемость.
Физическая свариваемость – свойство материалов образовывать монолитное соединение с межатомной связью. Такой свариваемостью обладают практически все технические сплавы и чистые металлы, а также ряд сочетаний металлов с неметаллами.
Технологическая свариваемость это характеристика металла, определяющая его реакцию на воздействие сварки и способность при этом образовывать сварное соединение с заданными эксплуатационными свойствами.
Технологическая свариваемость зависит от физических и химических свойств материала, его кристаллической решетки, степени легирования, наличия примесей и пр. Кроме технологических характеристик основного металла свариваемость определяется способом и режимами сварки, составом электродного или присадочного металла, флюса, покрытия, защитного газа, а также конструкцией сварного узла.
Основными критериями технологической свариваемости являются:
· окисляемость металла при сварочном нагреве;
· сопротивляемость образованию горячих и холодных трещин;
· чувствительность металла к тепловому воздействию, характеризующаяся склонностью металла к росту зерна, структурным и фазовым изменениям в шве и зоне термического влияния, изменением прочностных и пластических свойств;
· чувствительность к порообразованию;
· соответствие свойств сварного соединения заданным эксплуатационным свойствам;
· обеспечение качества формирования сварного шва;
· удовлетворение требованиям минимальных (допустимых) напряжений и деформаций.
Из рассмотренных критериев технологической свариваемости наиболее опасными, с точки зрения несущей способности конструкции, являются горячие и холодные трещины.
На чувствительность к образованию горячих трещин существенное влияние оказывает химический состав стали. Зависимость склонности сварного шва к образованию горячих трещин от его химического состава с известным приближением выражается уравнением
![]() | (1) |
где химические символы означают содержание легирующих элементов шва в массовых долях, %.
Если критерий HCS<4, горячие трещины в сварном соединении не образуются. Для высококачественных сталей большой толщины необходима величина HCS< 1,6…2,0.
Склонность металла шва к возникновению горячих трещин может быть определена прямым экспериментом, который учитывает влияние величины температурного интервала хрупкости, величины пластической деформации, которую испытывает металл, а также влияние темпа деформации.
Эти пробы разделяются на две основные группы:
1) испытания на образцах с естественной жесткостью (жесткие пробы);
2) испытания образцов с принудительной жесткостью (с внешней нагрузкой).
Испытания на образцах с естественной жесткостью дают качественную оценку основного металла, сварочных материалов или технологического процесса по степени их влияния на образование горячих трещин. Наиболее эффективным испытанием с естественной жесткостью образца, дающим качественную оценку склонности к горячим трещинам, является кольцевая проба Томаса (рис.1). Четыре сектора из испытуемой стали, со стороны паза, сваривают крестообразным связующим швом. В кольцевой паз накладывают опытный сварной шов. Общее количество трещин определяют на поверхности этого сварного шва при увеличении ×60 крат. Затем сравнивают различные варианты кольцевых проб и лучшим считается тот, количество трещин при котором минимально.
Испытания образцов с принудительной жесткостью (с принудительным деформированием) в процессе сварки на специальном оборудовании по реальному или имитационному циклу сварки позволяют получить достоверные количественные, хорошо воспроизводимые результаты. При использовании таких методик можно сопоставлять результаты отдельных испытаний между собой, если эти испытания проводили на одинаковом оборудовании при одинаковых параметрах.
Рис.1. Схема кольцевой пробы
При помощи исследуемого электрода выполняется сварка углового шва между двумя пластинами размером 50…75 мм и толщиной от 10 до 15 мм. Эти пластины жестко закреплены в двух суппортах, которые могут взаимно поворачиваться вокруг оси, проходящей вдоль испытываемого сварного шва.
Рис.2. Схема пробы «Мюрекс»: 1 – сварной шов; 2 – пластины; 3 – суппорты
Через 5 секунд после начала сварки включается поворот суппортов, скорость которых можно изменять. Во время поворота суппортов начинается образование продольных горячих трещин. Критерием склонности к образованию трещин служит минимальная скорость деформирования изгибом, при которой образуются трещины или общая длина полученной трещины, в которую не входит длина трещины в кратере сварного шва. Начальная скорость изгиба составляет примерно 1°/с.
Образование холодных трещин конструкционных углеродистых и легированных сталей зависит от степени легирования, структуры, содержания примесей и пр. Наибольшее влияние на свариваемость сталей оказывает углерод. С увеличением содержания углерода, а также ряда легирующих элементов свариваемость сталей ухудшается.
Чем выше содержание углерода в стали, тем выше опасность образования холодных трещин. Ориентировочным количественным показателем свариваемости стали является эквивалентное содержание углерода, которое определяется по формуле Сефериана (2)
![]() | (2) |
где [C]х - содержание углерода и легирующих элементов дается в процентах. Рассчитанные значения
химического эквивалента углерода для конструкционных углеродистых и легированных сталей
позволяют классифицировать их по свариваемости в зависимости от химического состава на хорошо,
удовлетворительно, ограниченно и плохо свариваемые.
На количественное значение эквивалента углерода для каждой группы свариваемости существенное влияние оказывает толщина элементов конструкции, определяемая размерным эквивалентом углерода.
Размерный эквивалент углерода Ср равен
![]() | (3) |
где S – толщина свариваемой стали в мм, 0,005 – коэффициент толщины, определенный
экспериментально.
Условия сварки, при которых нет опасности образования холодных трещин, можно определить с помощью лабораторных образцовых методов испытаний. Они основаны преимущественно на использовании реального процесса сварки жестких или составных образцов. Наиболее проста и часто используется «крестовая» проба (рис.3.). Механически обработанные пластины толщиной 6,5…25 мм собирают в крестообразное соединение и выполняют вспомогательные сварные швы. После охлаждения сваренного образца выполняют контрольный угловой шов с катетом около 6,5 мм.
Наличие трещин определяют на металлографических шлифах поперечных сечений контрольного сварного шва на базе 150 мм. Проба пригодна для выбора параметров сварки корневой части стыковых соединений.
Существует достаточно большое количество других технологических проб на свариваемость, которые подробнее рассмотрены в специальной литературе.
Рис.3. Образец выполнения «крестовой пробы»:
1,2,3 – вспомогательные швы; 4 – контрольный шов.
Конструкционные стали с повышенным содержанием углерода, легированные Cr, Mn, Ni и другими элементами, склонны при сварке к образованию в зоне термического влияния неравновесной мартенситной структуры, интенсивность образования которой возрастает с увеличением содержания углерода и легирующих элементов. На образование закалочных структур в околошовной зоне влияют также выбранные режимы сварки, так как они определяют температуру нагрева и скорость охлаждения. Для снижения интенсивности образования мартенситных прослоек в зоне термического влияния, которые могут привести к образованию холодных трещин требуется применение специальных технологических мер. Наиболее эффективным из которых является снижение скорости охлаждения околошовной зоны путем предварительного подогрева. При выборе температуры предварительного подогрева закаливающихся сталей следует учитывать, что недостаточный подогрев приводит к повышению вероятности появления холодных трещин, а излишне высокий - снижает пластичность и особенно ударную вязкость стали вследствие чрезмерного роста зерен аустенита (Ас3 + 100°С). Определение необходимой температуры предварительного подогрева производится с учетом полного эквивалента углерода
![]() | (4) |
Температура предварительного подогрева Тп определяется как
![]() | (5) |
где 350 – температура в °С, принятая как наиболее характерная для мартенситного превращения
большинства закаливающихся конструкционных и теплоустойчивых сталей;
[C] –полный эквивалент углерода; 0,25 – максимальное содержание углерода,
при котором углеродистые стали не закаливаются и не возникает опасность появления трещин в зоне
термического влияния сварного соединения.
На образование холодных трещин влияет также содержание водорода в металле, свойства образующегося мартенсита и уровень остаточных сварочных напряжений. Поэтому с учётом этих факторов температура предварительного подогрева будет несколько выше.
2.2. Выбор способа сварки
![]() ![]() |
При выборе способа сварки заданной конструкции студент должен предложить не более 2-х видов сварки. При этом в зависимости от конструктивных особенностей изделия и заданной преподавателем годовой программы выпуска продукции необходимо определить наиболее выгодные варианты сварки (рис.4). Выбор способа сварки начинается с проработки чертежа конструкций. При этом необходимо руководствоваться следующими положениями:
Рис.4. Диаграмма выбора способов сварки для различных значений тока
· способ сварки, исходя из химического состава свариваемого металла и особенностей
конструкции, должен обеспечивать высокое качество сварного соединения (отсутствие горячих и холодных трещин, пор, шлаковых включений, дефектов формирования);
· способ сварки должен обладать предпочтительными технико-экономическими характеристиками.
При выборе способа сварки предпочтение необходимо отдавать механизированным способам. Если сварку конструкций предполагается выполнять в различных пространственных положениях, то целесообразно использовать механизированные способы в защитных газах.
При разработке технологии сварной конструкции необходимо предусматривать максимальный объем применения автоматической сварки.
При выполнении швов большой протяжённости в нижнем положении целесообразно применение сварки под флюсом, так как этот способ обеспечивает высокую производительность процесса изготовления продукции и качество сварных соединений.
Технология сварки должна предусматривать меры борьбы с образованием холодных трещин, т.е. снижение уровня остаточных напряжений. В околошовной зоне закаливающихся легированных сталей развиваются продольные деформации и напряжения. В основном металле напряжения всегда растягивающие, а в металле шва знак напряжений зависит от состава наплавленного металла. Чем ниже температура распада аустенита в металле шва, тем вероятнее развитие в нем сжимающих напряжений. У концов шва напряжения обычно сжимающие, в средней части растягивающие, близкие по величине к пределу текучести стали. Для снижения уровня напряжений студент может предложить способ (режим) сварки с повышенной погонной энергией дуги, предусмотреть наложение второго слоя или отжигающего валика.
2.3. Выбор сварочных материалов
К сварочным материалам относятся штучные электроды, электродная и присадочная проволока, неплавящиеся вольфрамовые, реже угольные и графитовые электроды, сварочные флюсы и защитные газы.
Штучные покрытые электроды для ручной сварки выбираются исходя из требований, предъявляемых условиями эксплуатации конструкции с обязательным учетом химического состава и механических свойств основного металла.
Характеристика покрытых электродов для сварки сталей различных классов отражена в ГОСТ 9466-75. Свойства наплавленного металла для наиболее распространенных углеродистых и низколегированных сталей регламентируются ГОСТ 9467-75. Свойства наплавленного металла, полученного различными электродами, для высоколегированных сталей представлены ГОСТ 10052-75.
В качестве неплавящихся (вольфрамовых) электродов для сварки в инертных газах чаще всего выбирают электроды диаметром 0,8-10,0 мм, легированные окисью лантана ВЛ или окисью иттрия ВИ, поставляемых по техническим условиям ТУ 48-19-221-76.
Сварочная проволока, предназначенная для изготовления покрытых электродов и использования при различных способах механизированной и автоматической сварки, выбирается также в зависимости от условий эксплуатации сварной конструкции, химического состава и механических свойств основного материала. Химический состав сварочной проволоки различных марок регламентирует ГОСТ 2246-70. Стандартом предусмотрено 77 марок сварочной проволоки различного химического состава; выпускается 6 марок низкоуглеродистой проволоки (Св-08, Св-08А, Св-08ГА, Св-10ГА и др.), 30 марок легированной проволоки (Св-08ГС, Св-08Г2С, Св-15ГСТЮЦА и др.), 41 марка высоколегированной проволоки (Св-12Х11НМФ, Св-12Х13,Св-10Х17Т, Св-06Х19Н9Т и др.).
Проволока выпускается следующих диаметров: 0,3; 0,5; 0,8; 1,0; 1,2; 1,,4; 1,6; 2,0; 2,5; 3,0; 4,0; 5,0; 6,0; 8,0; 10,0; 12,0 мм. Проволока с диаметром до 3 мм применяется в основном для сварки в среде защитных газов; от 1,6 до 6,0 – для ручной сварки штучными электродами; от 2,0 до 5,0 мм – для автоматической сварки под флюсом; проволоки больших диаметров – для наплавочных работ.
Защитные газы подразделяются на активные и инертные. Наиболее распространенным активным газом является углекислый газ СО2. Он поставляется по ГОСТ 8050-76 и используется для механизированной и автоматической сварки малоуглеродистых, низколегированных и легированных сталей плавящимся электродом в чистом виде или в виде смесей с кислородом или аргоном.
К инертным газам относится аргон и гелий. Аргон поставляется по ГОСТ 10157-73, а гелий по ТУ 51-689-75. Эти газы в большинстве случаев используются для сварки плавящимся и неплавящимся электродом высоколегированных сталей, меди, алюминия, титана и других металлов и сплавов.
Для улучшения сварочно-технологических свойств защитных газов применяются двойные и тройные смеси газов: аргон с гелием, аргон с углекислым газом, с кислородом.
2.4. Выбор режимов сварки
Режимы сварки выбираются после назначения способа сварки в зависимости от вида сварного соединения и разделки кромок с учетом свойств свариваемого материала. На основании расчёта режимов сварки, а также данных таблиц и номограмм, выбранных из справочной литературы, назначаются сварочные режимы.
Основными параметрами режима при ручной сварке покрытыми электродами являются: род тока и его полярность, диаметр электрода и сила тока. Род тока и полярность назначаются в зависимости от марки электрода. Диаметр электрода выбирается в зависимости от толщины свариваемого металла (вида разделки, размеров и пространственного положения сварного шва). Сила тока зависит от диаметра электрода и определяется по эмпирическим зависимостям или справочным данным. Тип электрода выбирается исходя из требуемых механических показателей металла шва, которые должны соответствовать показателям основного металла.
Чтобы обеспечить удовлетворительную форму шва, площадь поперечного сечения наплавляемого металла за один проход не должна превышать 12d эл.Для корневого прохода площадь поперечного сечения составляет порядка 8 d эл (d эл- диаметр электрода, мм).
При механизированной сварке основными параметрами режима являются: род тока и полярность, диаметр электродной проволоки, сила тока, напряжение на дуге, скорость сварки, скорость подачи электродной проволоки, марка и расход флюса или газа. Выбор всех этих параметров осуществляется в зависимости от способа сварки, типа сварного соединения, диаметра сварочной проволоки и марки свариваемого материала. При этом используются расчетные формулы, таблицы номограммы, взятые из справочной литературы.
Значение сварочного тока и диаметр электродной проволоки оказывают большое влияние на глубину и ширину проплавления основного металла. На рис.5 представлены зависимости этих параметров от сварочного тока при сварке под слоем флюса для различных значений диаметра электродной проволоки.
![]() |
Рис.5.Зависимости глубины и ширины проплавления от тока и диаметра электродной
проволоки при автоматической сварки под флюсом (скорость сварки 30м/ч).
Аналогичный характер изменения глубины проплавления наблюдается и при механизированной сварке в среде углекислого газа (рис.6.).
![]() |
Рис.6.Зависимости глубины проплавления при сварке на скорости 30м/ч от тока обратной
полярности для электродной проволоки Св-08Г2С различных диаметров.
2.5.Выбор сварочного оборудования
Для выполнения сварочных работ необходим комплекс оборудования, обеспечивающий получение сварных швов заданного качества и конфигурации.
Комплект технологически связанного между собой оборудования принято называть сварочным постом или установкой. В их состав в зависимости от оснащённости входят: источник питания и сварочный аппарат; технологические сборочно-сварочные приспособления; механическое и вспомогательное оборудование, предназначенное для манипулирования свариваемого изделия, крепления и перемещения сварочных аппаратов; а также сварочный инструмент. В каждом отдельном случае установка или сварочный пост может включать не все перечисленные элементы. Стационарный сварочный пост для ручной дуговой сварки – это участок производственной площади, снабжённый источником сварочного тока и всем необходимым технологическим оборудованием и инструментом (рис.7).
![]() |
Рис.7.Стационарный пост для ручной сварки: 1-источник питания; 2-сварочный стол;
3-газоотсос; 4-ящик для инструмента; 5-электрододержатель; 6-ящик c электродами
![]() |
Установка для автоматической сварки представлена на рис.8. В ней механизированы, по крайней мере, две основные операции сварочного процесса: подача электрода и перемещение дуги вдоль свариваемых кромок.
Рис.8.Установка для автоматической сварки: 1-сварочный аппарат; 2-источник питания; 3-шкаф
с аппаратурой управления; 4-тележка с колонной; 5-свариваемое изделие; 6-рельсовый путь
тележки; 7-стенд для укладки и вращения изделия; 8-сварочный кабель; 9-провод управления; 10-площадка сварщика
Установки, где механизирована только одна из этих операций, принято называть установками для полуавтоматической сварки (рис.9).
![]() |
Рис.9.Установка для полуавтоматической сварки: 1-сварочный аппарат; 2-гибкий направляющий
канал для электродной проволоки; 3-сварочная горелка; 4-платформа; 5-катушка
с электродной проволокой; 6-подвеска полуавтомата; 7-консоль с рельсом.
Процесс любого способа сварки может быть представлен в виде циклограммы. В качестве примера на рис.10 представлена простейшая циклограмма процесса дуговой автоматической сварки плавящимся электродом в защитной газовой среде.
По команде оператора включается сварочное напряжение на предварительно закороченный на изделие электрод. Одновременно электрод отрывается от изделия и включается подача защитного газа. За время t 1 происходит возбуждение дуги. К моменту t 2 заканчивается установление дугового процесса: напряжение и ток достигают рабочей величины, начинается подача электрода в сторону изделия, образуется сварочная ванна и начинается движение дуги вдоль свариваемых кромок. Время t 2 – t 3 соответствует основному этапу образования шва. Команда на прекращение сварки вызывает остановку подачи электрода и прекращение движения вдоль кромок. Дуга растягивается до естественного обрыва (t 4), сила тока падает до нуля, сварочное напряжение отключается. Некоторое время (t 5) продолжается подача газа для защиты горячего металла от воздуха.
![]() |
Рис.10.Последовательность выполнения операций при сварке плавящимся электродом в защитной
среде: 1-сварочное напряжение; 2-сварочный ток; 3-скорость и направление подачи
электрода; 4-подача защитного газа; 5-движение вдоль свариваемых кромок.
В настоящее время существуют циклограммы для различных способов сварки, определяющие дополнительные опции и последовательность операций. Они могут выполняться вручную или механизированным путём, сварочным аппаратом, содержащим соответствующие устройства.
Основные требования к источникам питания сварочной дуги. Сварочная дуга питается от специальных источников питания. Режим её горения характеризуется силой тока, напряжением и длиной дуги, а также взаимосвязью между ними. Дуга как потребитель энергии и источник питания образует взаимосвязанную энергетическую систему. Напряжение дуги при неизменном токе зависит от расстояния между электродами и имеет линейный характер. Напряжение дуги зависит также от величины сварочного тока. Эту зависимость при постоянной длине дуги принято называть вольт - амперной характеристикой дуги. Различают три участка кривой: крутопадающий, горизонтальный и возрастающий.
![]() |
Рис.11.Внешние характеристики источников питания (1-4, 7) и статические
вольт - амперные характеристики сварочной дуги (5, 6).
Практическое значение имеют режимы горения дуги, соответствующие двум последним участкам. Режимы горения, соответствующие первому участку, относительно неустойчивы и поэтому трудно осуществимы при безопасных для работы напряжениях источников питания. С увеличением длины дуги расположение характеристики изменяется (рис.11, кривые 5 и 6).
Приведённая схема справедлива для сварки неплавящимся и плавящимся электродами. Однако в связи с тем, что в последнем случае металл попадает в сварочную ванну в виде отдельных капель, длина дуги непрерывно меняется, что вызывает колебание тока и напряжения.
Для понимания многих процессов, происходящих при сварке плавящимся электродом, воспользуемся характеристикой, снятой при постоянной скорости подачи электродной проволоки (рис.12, кривые 1 и 2), называемые характеристиками устойчивой работы.
Рис.12.Вольт-амперная характеристика (1 и 2) дуги при постоянной скорости подачи
проволоки и внешняя характеристика (3 и 5) источника питания.
Каждой скорости подачи (vn1, vn1…) соответствует небольшой диапазон токов, в котором дуга горит устойчиво и электродная проволока плавится стабильно. При этом небольшие изменения тока вызывают значительные изменения напряжения. Устойчивость горения дуги и стабильность режима сварки зависят от условий существования дугового разряда, свойств и параметров источников питания и электрической цепи.
Внешней характеристикой источника питания называют зависимость напряжения на зажимах от силы тока нагрузки (кривые 3, 4 и 5 на рис.12). Каждая внешняя характеристика соответствует вполне определённому положению регулировочного устройства источника питания.
Различают следующие внешние характеристики (рис.11.) источников питания: падающую 1, пологопадающую 2, жёсткую 3 и возрастающую 4. Выбор источника питания по типу внешней характеристики производится в зависимости от способа сварки. Условия устойчивого горения дуги будут выполнены, если в течение длительного времени дуговой разряд существует непрерывно при заданных значениях напряжения и тока. Установившийся режим работы системы сварочная дуга-источник питания определяется точкой пересечения внешней характеристики источника питания и вольт - амперной характеристики дуги 5.
Равновесие по току и напряжению имеет место в двух точках А и В. Дуга будет гореть устойчиво, при падающей статической характеристики дуги, если внешняя характеристика источника питания также будет падающей., причём в точке А она должна иметь большую крутизну, чем статическая характеристика дуги. Физически это можно объяснить следующим образом. Если по какой-либо причине ток дуги, соответствующий точке А, уменьшится, напряжение её окажется меньше установившейся величины напряжения источника питания; это приведёт к увеличению силы тока, т.е. в точку А. Наоборот, при случайном увеличении силы тока установившееся напряжение источника питания окажется меньше напряжения дуги; это приводит к уменьшению тока и, следовательно, к восстановлению режима горения дуги. Из аналогичных рассуждений ясно, что в точке В дуга горит неустойчиво. Всякие случайные изменения тока развиваются до тех пор, пока ток не достигает величины, соответствующей точке устойчивого равновесия А или до обрыва дуги.
В реальных условиях, особенно при ручной сварке, возможны резкие изменения дуги, поэтому она должна обладать достаточным запасом устойчивости (эластичностью). При возрастающей статической характеристике дуги эластичность наибольшая и при падающей – наименьшая. При прочих равных условиях эластичность тем больше, чем больше крутизна падения внешней характеристики источника питания. Поэтому для ручной сварки применяют источники с падающими характеристиками. Это даёт сварщику удлинять дугу, не опасаясь её обрыва, или уменьшать дуговой промежуток без чрезмерного увеличения тока.
При автоматической или полуавтоматической сварке плавящимся электродом последний подаётся в зону сварки со скоростью, равной скорости его плавления. При случайном уменьшении дугового промежутка (точка В кривой 6 на рис.11) увеличивается ток. Поскольку скорость плавления электрода, в первом приближении, пропорциональна току дуги, то проволока начинается плавиться быстрее. В итоге дуговой промежуток постепенно удлиняется и приобретает первоначальную длину. Аналогичный процесс произойдёт при случайном удлинении дуги. Этот процесс называется саморегулированием дуги.
Таким образом, при выборе сварочного источника питания для определенного вида сварки необходимо руководствоваться как его мощностью, так и видом внешних вольт - амперных характеристик.
Дата добавления: 2021-06-02; просмотров: 66; Мы поможем в написании вашей работы! |
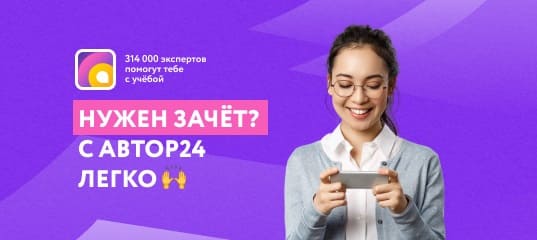
Мы поможем в написании ваших работ!