Работа установки металлизации
В состав каждого модуля металлизации «Мидрекс» входят: участок шахтной печи металлизации; участок реформера (конвертера природного газа); система производства инертного газа: цикла восстановительного и охлаждающего газа и другие системы. Схема работы шахтной печи и газовых циклов модуля металлизации окисленных окатышей ОЭМК представлена на рис. 3.2.
Рисунок 3.2 - Технологическая схема модуля металлизации окатышей «Мидрекс»: А - шахтная печь, Б1 - скруббер колошникового газа, Б2 - то же охлаждающего газа, В1 - концевой холодильник, В2 - охладитель конверторного газа, Г - реформер, Д - рекуператор, Е - каплеулавитель, Ж - компрессор, 1 - конвертированный газ, 2 - восстановительный газ, 3 - колошниковый газ, 4 - технологический газ, 5 - смешанный газ, 6 - топливный газ, 7 - охлаждающий газ на входе, 7а - то же на выходе, 8- инертный газ, 9 - дымовой газ, 10 - природный газ, 11 - воздух на горение
Восстановительная шахтная печь состоит из загрузочного бункера, верхнего динамического затвора с загрузочным распределителем и труботечками, зоны восстановления, промежуточной зоны, зоны охлаждения, огнеупорной футеровки, постоянно действующих питателей, нижнего динамического затвора и маятникового питателя (для выгрузки готового продукта). Общий объем печи составляет 370 м3, внутренний диаметр -5 м, общая высота - 22 м. Зона восстановления распространяется от уровня фурм, через которые вдувается восстановительный газ, до уровня засыпки шихты под сводом печи. Горячий восстановительный газ вводится в зону восстановления объемом 200 м3 по кольцевому каналу на уровне фурм через фурменные блоки. Зоны восстановления и охлаждения разделены промежуточной зоной, верхней границей которой является уровень фурм, а нижней - уровень каналов для отсоса охлаждающего газа. Внизу этой зоны непосредственно над каналами для отсоса охлаждающего газа расположены верхние постоянно действующие питатели. Уровень каналов отсоса охлаждающих газов - это верхняя граница зоны охлаждения, а ее нижняя граница - нижний динамический затвор. Объем зоны охлаждения составляет около 120 м3. Охлаждающий газ входит в зону охлаждения через распре делитель, представляющий собой коническую конструкцию из коаксиальных отрезков труб, сужающихся книзу. В зоне охлаждения расположены средние и нижние постоянно действующие питатели, которые благодаря их возвратновращательному движению обеспечивают равномерный сход столба шихтовых материалов.
|
|
Один из основных и важнейших агрегатов модуля прямого восстановления - реформер. Его корпус представляет собой стальную конструкцию прямоугольного сечения 41x11x9 м. В реформере имеется 288 реакционных труб, размещенных вертикально в четыре ряда. Стены реформера защищены огнеупорной футеровкой, а его трубы заполнены катализатором. Рабочая температура в межтрубном пространстве составляет около 1100 °С. Реформер отапливается с помощью установленных в днище между трубами 120 главных и 36 вспомогательных горелок. Главные горелки работают на топливном газе (смеси колошникового газа с природным) и на воздухе, подогретом до 600 °С. Во вспомогательных горелках сжигается природный газ с холодным воздухом. Дымовые газы отсасываются из межтрубного пространства реформера эксгаустером при температуре около 1100 °С и проходят через два параллельно расположенных рекуператора, где отдают большую часть физического тепла, подогревая воздух для главных горелок, смешанный и природный газы. После этого они выбрасываются в дымовую трубу.
|
|
Шахтная печь в процессе «Мидрекс» работает по принципу противотока. Окисленные окатыши поступают в печь сверху и опускаются вниз под действием силы собственной тяжести по мере того, как в нижней части печи они выгружаются в виде металлизованного продукта. Одновременно горячий восстановительный газ, вдуваемый через фурмы при температуре 760 °С и абсолютном давлении 0,2 МПа, движется навстречу потоку окатышей вверх, где покидает печь в виде колошникового газа при температуре 400 °С. Для предотвращения выбивания из печи печных газов устройства для загрузки исходных окисленных окатышей и выгрузки металлизованного материала уплотнены при помощи так называемых динамических газовых затворов, в которые вдувается инертный (затворный) газ под таким давлением, которое обеспечивает движение этого газа в трубах затворов внутрь печи. Время пребывания окатышей в зоне восстановления при проектной производительности модуля устанавливается таким, чтобы достигалась средняя степень металлизации в пределах 90-94%.
|
|
Развитие различных реакций процесса металлизации и науглероживания железа с образованием карбида (Fe3C) в принципе зависит от температуры восстановительного газа, его химического состава и времени пребывания газа и шихты в восстановительной печи. 11а кинетику восстановительных процессов существенное влияние оказывает химический состав исходных окатышей.
Горячий запыленный колошниковый газ поступает в скруббер (Б1) сверху через трубу Вентури, где при подаче большого количества воды происходят его резкое охлаждение и одновременно смачивание частиц пыли. Над поверхностью промывочной воды в конусной части скруббера газовый поток поворачивается на 180 град, вследствие чего смоченные частицы пыли вместе с большей частью капель охлаждающей воды отбрасываются (отделяются от потока) силой инерции в воду. Доля газа, необходимого для конверсии (технологический газ), выходит из скруббера насыщенной водяными парами при температуре около 55 °С. Избыток газа (топливный газ) должен быть более полно обезвожен, поэтому он орошается в насадке скруббера промывочной водой, имеющей по возможности более низкую температуру. Для получения различной температуры газа промывочная насадка скруббера разделена перегородкой на зоны технологического и топливного газов.
|
|
Циркуляцию технологического газа обеспечивает группа компрессоров (Ж), причем для регулирования расхода газа предусмотрена байпасная линия, через которую избыточное количество газа возвращается обратно в скруббер колош-никового газа. Основной поток технологического газа поступает из компрессоров в концевой холодильник (В,), в котором с заданной точностью насыщается во-дяными парами благодаря орошению насадки, через которую газ проходит снизу вверх. Таким образом концевой холодильник обеспечивает тонкое регулирование содержания водяного пара в технологическом газе, подаваемом на конверсию природного газа.
После концевого холодильника технологический газ смешивается с при-родным, очищенным от соединений серы и подогретым в рекуператоре. Смешанный газ (природный + технологический) перед процессом конверсии подогревается в рекуператоре до 400°С и затем конвертируется в реакционных трубах реформера с одновременным нагревом до 900 °С. При этом происходит увеличение объема.
Горячий конвертированный газ из реформера частично поступает в холодильник конвертированного газа (В2). В этом холодильнике и непосредственно за ним температура и состав газа корректируются с таким расчетом, чтобы были точно выдержаны конкретные параметры процесса восстановления. Из трубопровода конвертированного газа часть потока охлаждается в холодильнике (В2), при этом содержание паров воды в газе снижается. Температура основного потока газа регулируется количеством вводимого в него охлажденного конвертированного газа. Кроме того, можно повысить содержание метана в конвертированном газе, добавляя природный газ в его охлажденный поток. Газ со строго выдержанными параметрами химического состава и температуры (восстановительный газ) подастся в кольцевой канал и к фурмам шахтной печи.
В рекуператоре (Д) охлаждаются дымовые газы реформера, нагревая воздух, подаваемый к главным горелкам, смешанный и природный газы. После прохождения рекуператора дымовые газы эксгаустером выбрасываются в дымовую трубу. Часть дымовых газов используется для получения затворного газа.
Заключение
металлизация железорудный конвейерный сырье
Несмотря на ограниченное пока распространение, плавильно-восстановительные процессы, по мнению многих специалистов, имеют большую перспективу по следующим причинам:
) некоторые из них могут конкурировать с доменными печами по мощности и объему выпускаемой продукции;
) не требуют предварительного окускования железорудных материалов, т.е. не нужны «грязные» аглофабрики;
) используют угли различных марок (вместо кокса и природного газа);
) пригодны для утилизации различных железосодержащих отходов;
) не предъявляют жестких требований к качеству железорудных материалов.
Перспективы бескоксовой металлургии на ближайший период связаны прежде всего с производством губчатого железа и металлизованного сырья, в том числе и для доменной плавки. Решение проблемы масштабности и создание высокопроизводительных агрегатов бескоксовой металлургии, способных успешно конкурировать с мощными доменными печами, позволят в будущем ставить вопрос о замене существующей схемы металлургического производства.
Библиографический список
1. Князев В.Ф. Бескоксовая металлургия железа. / В.Ф. Князев, А.И. Гиммельфарб, А.М. Неменов. - М.: Металлургия, 1972. 272 с.
2. Тулин Н.А., Кудрявцев В.С., Пчелкин С.А. и др. Развитие бескоксовой металлургии. М.: Металлургия, 1987. 328 с.
. Кожевников И. Ю, Бескоксовая металлургия железа. М.: металлургия, 1970, 336 с.
. Шумаков Н.С., Дмитриев А.Н., Гараева О.Г. Сырые материалы и топливо для доменной плавки. - Екатеринбург УрО РАН, 2007. - 391 с.
Дата добавления: 2021-04-24; просмотров: 146; Мы поможем в написании вашей работы! |
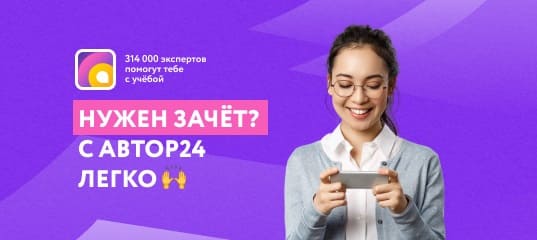
Мы поможем в написании ваших работ!