Примеры радиационного контроля
4.1. Радиационный контроль стыкового сварного соединения стальных листов толщиной 2В мм в условиях заводской лаборатории. Возможны два варианта: а) для соединений высокой ответственности - требования выявляемости мелких объектов; б) требования наименьшей экспозиции (высокой производительности).
4.1.1. Выбор источника излучения
По рис.1 выбираем схему контроля. По схеме с учетом технологического припуска устанавливаем просвечиваемую толщину d = 30 мм.
По заданному материалу и d согласно ГОСТ20426-82 (табл. 2 и 3) выбираем подходящий источник. Пригодны рентгеновские аппараты с Uа = 250-300 кВ и источники с нуклидами S е75, Zr 192, С s 137. Выбираем передвижной рентгеновский аппарат РАП-150/300-10 (табл.1).
4.1.2. Пленка и экраны.
Для варианта (а) используем высококонтрастную пленку РТ-5 без усиливающих экранов. Для варианта (б) выбираем пленку РТ-2 с усиливающим экраном.
4.1.3. Фокусное расстояние F должно быть не менее 50 см. Принимаем F =75 см.
4.1 4. Экспозиции просвечивания t определяем по номограмме (рис.1). Для стали d=30 мм при "исходной" пленке РТ-1 с металлическими экранами и U =250 кВ требуется I в=6 м A * мин.
t =6/10=0,6 мин.
Принимается ток I =10 м A, получаем t =0.6 мин.
Для других пленок время t, мин, рассчитываем по формуле t = t 0 K /К0,
где t 0 - время просвечивания, определенное по рис.2 для исходной пленки;
К0 - переходной коэффициент для исходной пленки и варианта зарядки касет (табл.5);
|
|
t ,К - время просвечивания и переходной коэффициент для искомой пленки и варианта зарядки кассет.
Тогда:
а) для пленки РТ-5 без экранов время просвечивания составит t =0,61*8,4/0,5=10 мин;
б) для РТ-2 используем две пары экранов: два металлических (К=0,8) и два флуоресцентных (К=0,04).
Тогда t =0,6*0,8*0,02/0,5=0,04 мин =(3сек).
Таблица 5
Коэффициент перехода К по времени просвечивания от пленки
РТ-1 к другим пленкам
Вариант зарядки плёнки | РТ-1 | РТ-2 | РНТМ-1 | РТ-СШ | РТ-4М | РТ-5 |
Без усиливающих экранов | 1 | 1,7 | 2 | 2,5 | 5 | 8,4 |
С металлическими экранами при напряжении > 400 кВ | 0,5 | 0,8 | 1 | 1,25 | 2,5 | 4,2 |
С люминисцентными экранами при U = 80 кВ и времени просвечивания 100 с | 0,5 – 0,22 | 0,04 – 0,015 | 1 – 0,43 | 1,25 – 0,5 | 2,5 – 1,2 | 4,2 – 1,8 |
4.2. Радиационный контроль углового сварного соединения стальных листов толщиной 8 мм. Соединение невысокой ответственности. Контроль в цеховых условиях.
4.2.1. Источник излучения выбираем как в примере 4.1. Применяем фронтальное просвечивание под углом = 450 (рис.1). Просвечиваемая толщина d пр = d * sin 45=8*0,76 мм.
По ГОСТ20426-82 пригодны рентгеновские аппараты с Ua =110-120 кВ и нуклиды Т l 170, S с75, Zr 192.
|
|
С целью обеспечения радиационной безопасности работников цеха используем аппарат МИРА-2Д (табл.1).
4.2.2. Учитывая невысокую ответственность соединения, используем, высокочувствительную пленку РТ-1 с металлическим экраном.
4.2.3. При импульсном излучении фокусное расстояние принимают равным 30-60 см. Принимаем F=30 см. Экспозиция просвечивания по номограмме Рис.3 составляет t =1,6 мин.
4.3. Радиационный контроль таврового сварного соединения алюминиевых листов толщиной d=5 мм. Катет К=4 мм.
4.3.1. Источник питания выбирается по установленному порядку. Принимаем фронтальное просвечивание под углом =450 (рис.1). Просвечиваемая толщина d пр =К* sin 45+ d /со s 45=4*0,7+5/0,7 10 мин.
По ГОСТ20416-82 пригодны рентгеновские аппараты с U а = 130-190 кВ и нуклиды Т l 170, S е75, С s 137. Выбираем дефектоскоп Гаммарид 170/400 [3,4].
Рис.3. Номограмма для определения экспозиций просвечивания t стали толщиной δ излучением от аппаратов МИРA-1Д(1), МИРА-1Д(2) и МИРА-3Д(3) на пленки РТ-1 и РТ-5 с оловянисто-свинцовыми фольгами толщиной 0,005 мм
(F = 30 см, S = 1,8-2,0)
Требуется высокая производительность контроля. Условия монтажа.
4.3.2. Для обеспечения высокой производительности используем высокочувствительную пленку РТ-1 и металлические экраны.
|
|
4.3.3. Фокусное расстояние принимаем F=45 см. Дефектоскоп Гаммарид 170/400 оснащен источником Тm170, имеющим МЭД 3*10 мА/кт. Время, прошедшее до момента просвечивания,130 дн. По номограмме (2, рис.3.22) получаем t = 0,05 ч = 3 мин.
4.4. Радиационный контроль кольцевого стыкового сварного соединения. Стык стальной трубы 600 мм с толщиной стенки 20 мм. Соединение высокой ответственности. Условия монтажа.
4.4.1. Источник излучения выбираем, как в примере 4.1.
а) При диаметре трубы > 500 мм целесообразен панорамный способ просвечивания (рис.1).
б) Просвечиваемая толщина с усилением 22 мм.
в) По ГОСТ20428-82 пригодны рентгеновские аппараты с U а = 200-230 кВ и источники S е75, Zr 192, С s 137. Выбираем дефектоскоп Гаммарид 192/120, который можно применить в полевых условиях.
4.4.2. Используем высокочувствительную пленку РТ-5. Для ускорения процесса принимаем металлические экраны.
4.4.3. Фокусное расстояние равно половине диаметра трубы, т.е. F=30 см.
4.4.4. Экспозицию просвечивания (t) по рис.8.4 и рис.8.5 [21 находим для d=22 мм, пленки РТ-5 и F = 50 см, экспозиционная доза Д=4*0,9 м A /кт. Время просвечивания при F=30 см, t = (Д/Р)( F / F 0 ), где F 0 - фокусное расстояние, для которого построена номограмма (50 см); F - заданное фокусное расстояние (30 см); t = (4*0,9/2,06*10)(30/50) = 63 с.
|
|
5. Ультразвуковая дефектоскопия.
Ультразвуковая дефектоскопия является одним из распространенных методов неразрушающего контроля, в котором используются механические колебания упругой среды, частота которых обычно 0,5-10 мГц. При падении ультразвуковой волны на границу двух сред часть энергии отражается, часть энергии проходит во вторую среду. Коэффициент отражения от трещин, несплавлений и пор близок к единице, если величина раскрытия >10 мм. Коэффициент отражения от шлаковых включений равен 0,15 (для продольных волн), а для поперечных - 0,35-0,65 в зависимости от марки флюса, акустические колебания от генератора излучателя распространяется в материале изделия. При наличии несплошности образуется отраженное поле и поле рассеяния. За несплошностью есть акустическая тень, а поверхность несплошности отражает УЗ - колебания. Регистрируя с помощью приемника-искателя ослабление УЗ - волны или эхо, т.е. осаженную УЗ - волну, можно судить о наличии несплошностей в сварном шве. Существуют 5 основных методов УЗ-контроля: эхо-метод, теневой, зеркально-теневой, эхо-зеркальный, эхо-теневой. Основными являются два главных метода УЗ-контроля: теневой и эхо-метод.
Основные этапы технологического процесса УЗ-контроля сварных соединений следующие: 1) подготовка к контролю; 2) поиск дефектов; 3) измерение дефектов - их размеров, формы и расположения; 4) оценка качества соединения.
Подготовка к УЗ-контролю включает: а) выбор основных параметров контроля и параметров сканирования; б) настройку дефектоскопа по контрольным образцам на заданные параметры: в) очистку поверхности сканирования от брызг металла, грязи, окалины и т.п.; г) нанесение контактирующего смазочного материала на искатели и поверхность сканирования.
Выбор основных параметров контроля и параметров сканирований производится по АРД-диаграммам, которые объединяют "амплитуду-расстояние-диаметр". Их получают экспериментально или расчетом (2). АРД-диаграммы позволяют определить глубину залегания дефекта Н, мм, или расстояние до него r, мм. АРД-диаграмма располагается на специальном планшете для данного типа искателя. По ней для данной толщины δ находят значение амплитуд, соответствующие отражению от плоскости и от эталонного отражателя (2). Очистка поверхности особенно важна для сварки в СО2, при которой есть приварившиеся брызги металла. Их нужно тщательно очищать.
Для обеспечения акустического контакта искатель-изделие используют жидкие смазочные материалы (минеральное масло, глицерин, воду) или солидол, тавот.
Поиск дефектов обнаружения путем сканирования дефектов с эквивалентной площадью S э, большей чем заданная чувствительность S п. Существуют две схемы сканирования; поперечно-продольная и продольно-поперечная (рис.4). Основные параметры сканирования - шаг l мм t и пределы Ll и Lt перемещения искателя. Для типовых искателей l 2 им, а t зависит от номера шага и угла призмы искателя. Например, при = 40 для шагов 1-9 используют t = 5, 6, 7, 9, 10, 13, 16, 20, 24 мм.
Рис.4. Схемы сканирования при УЗ-контроле:
а - поперечно-продольная; б - продольно-поперечная.
Сварные стыковые соединения обычно контролируют эхо-методом наклонным совмещенный искателем с одной стороны шва и с одной поверхности стыка. Применяют прямой (m=0) и однократно отращенный луч .(m=1) (рис. 5а, б.).
Рис.5. Схемы УЗ-контроля стыковых соединений:
а - прямым; б - однократно отраженным лучом.
Пределы поперечного перемещения искателя рассчитывают по формуле:
при m =0; htmin = n ; htmax = * tg;
при m =1; htmin =z+ tg; htmax =2
* tg.
Угол ввода луча при любом m выбирают из условия пересечения оси симметрии шва акустической осью искателя на глубине 0,5 :
tg >(в+2 n )/б при m =0;
tg >(в+2 z )/б при m =1.
Расстояние z принимается равным 2-8 мм. Значения параметров контроля зависят от толщины (табл.6).
Таблица 6
Примерные значения параметров призматических УЗ-искателей
Сталь ![]() | Частота, МГц | Угол призмы, градус | Стрела n, мм |
4 – 10 | 5 | 55 – 53 | 5 |
> 10 – 15 | 5 | 53 – 50 | 8 |
> 15 – 30 | 2,5 | 50 | 12 |
40 и больше | 1,8 | 40 | 25 |
Для швов на б=(3-8) им используют только прямой луч (m =0) и чем меньше б, тем больше углы ввода. Если = 70-74 , то для стали при f = 5 МГц это соответствует углу призмы 50-55°.
На швах с б>50 мм возможны шлаковые включения, поэтому лучше их выявлять при контроле с обеих сторон шва.
Для швов б>150 мм контроль ведут с обеих поверхностей и целесообразен контроль по слоям [2].
Соединения с угловыми швами контролируют наклонными и раздельно-совмещенными РС - искателями по одной из схем (рис.6):
а) прямым лучом наклонным искателем со стороны привариваемого элемента, а также РС - искателем со стороны основного элемента;
б) прямым лучом наклонный искателем с обеих сторон или прямым и однажды отраженным лучей с одной стороны привариваемого элемента;
в) прямым лучом наклонным искателем и РС-искателем, если отсутствует доступ со стороны привариваемого элемента.
Рис.6. Схемы УЗ-контроля тавровых соединений:
а - доступ с обеих сторон; б - доступ со стороны основного металла запрещен;
в - доступ со стороны приваренного элемента запрещен.
Рекомендации по схемам контроля других соединений представлены в [2,4].
Технические характеристики прямых (П111), прямых РС (П112) и наклонных (П121) представлены в [3].
Технические характеристики дефектоскопов общего назначение представлены в таблице 7.
Пример: произвести ультразвуковой контроль стыковых сварных соединений листов.
Толщина листа 40 мм. Сверка с 2-х сторон.
1.1. Выбираем дефектоскоп ДУК-66ПИ (табл.7) комплект призматических преобразователей, испытательные и стандартные образцы, вспомогательные материалы и инструмент по рекомендациям [3,4].
Таблица 7
Технические характеристики дефектоскопов
Тип | Номинальная частота, МГц | Регулировка усиления, дБ | Глубина прозвучивания, мм | Питание, В | Масса, кг | |
От сети | Автономно | |||||
ДУК-66 | 0,62; 1,25; 5; 10 | 89 | 2500 | 220 | - | 24,5 |
ДУК-66П | 1,25; 2,5; 5,0; 10,0 | 79 | 1200 | 220 | 9 | 9,5 |
УД-10УА | 1,5 – 6,0 | 80 | 5000 | 220 | - | 28 |
УД-10П | 0,6; 1,25; 2,5; 5,0; 10,0; 25,0 | 0 – 40 (плавное) 0 – 50 (ступенчатое) | 5000 | 2200 | 24 – 26 | 12 |
УД-11ПУ (ЭКОН-2) | 1,25; 2,5; 5,0; 10,0 | 0 – 62 (ступенчатое) | 2 – 180 | 220 | 12 | 7 |
УД-12ПУ (ЭКОН-7) | 1,25; 1,8 | 0 – 62 (ступенчатое) | 0,5 – 180 | 220 | 36 | 7 |
УД-11УА (ЭКОН-4) | 1,25; 2,5; 5,0; 10,0 | 40 | 0,5 – 180 | 220 | 12 | 25 |
УД-13П (ЭКОН-8) | 25 | 0 – 30 (плавное) | 2 – 50 | 24; 36 | От батарей | 1,5 |
УД-2-15 (ЭКОН-9) | 2,5; 5,0 | 0 – 120 (плавное) | 1000 | 12; 24 | - | 6,4 |
УД-23УМ (ЭКОН-7) | 0,2; 0,4; 0,6; 1,25 | 0 – 40 (плавное) | 3 – 200 | 220; 36 | 12 | 9 |
1.2. Настраиваем скорость развертки, координаты и чувствительность дефектоскопа для контроля прямым лучем.
1.3. Выбираем из комплекта преобразователь на частоту 2,5 МГц с углом 500 по табл.6.
1.4. Согласно паспорту установить стрелу преобразователя 12 мм и провести настройку дефектоскопа на стандартных образцах.
1.5. Установить преобразователь на поверхность испытываемой детали перемещая его, установить положение, когда появляется эхо-сигнал, измерить координаты дефектов.
1.6. Произвести сканирование шва.
1.7. Установить координаты дефекта.
Литература
1. Сварка в машиностроении: Справочник / Под ред. Ю. Н. Зорина.- М.: Машиностроение. 1979.- Т.4. 512 с.
2. Волченко В.Н. Контроль качества сварных конструкций.- П.: Машиностроение, 1986,- 152 с.
3. Справочник по оборудованию для дефектоскопии сварных швов, - К.: Техника, 1987.- 126 с.
4. Алешин Н. П., Щербинский В.Г, Радиационная, ультразвуковая и магнитная дефектоскопия металлоизделий.- М.: Высш. шк., 1991.- 271 с.
Учебное издание
методические указания
к выполнению домашнего задания по курсу
"Контроль качества сварки"
(для студентов специальностей 7.092301; 7.092303)
Составители:
Константин Васильевич Воронков
Михаил Иванович Черноморов
Редактор И. А. Морозова
Техн. редактор Т. .М. Дроговоз
Оригинал - макет И. В. Ширманова
Подписано к печати
Формат 60x84 1/16- Бумага офсетная. Гарнитура Times.
Печать офсетная. Ум.др.
Тираж 50 экз. Вид. № . Заказ. № Цена договорная.
Издательство ВНУ имени Владимира Даля
Адресс издательства: 91034, г. Луганск, кв. Молодежний, 20а
Телефон: 8(0642)41-34-12. Факс: 8(0642)41-31-60
Е- m аі l : uni@snu.edu.ua
http://www.snu.edu.ua
Дата добавления: 2021-02-10; просмотров: 216; Мы поможем в написании вашей работы! |
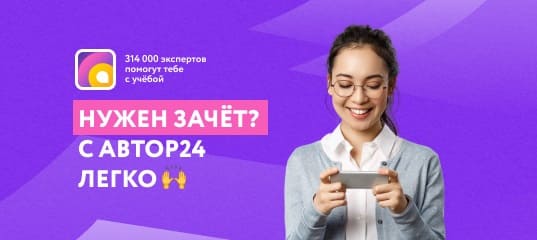
Мы поможем в написании ваших работ!