Контроль качества сварных соединений
11.3.1 Контроль качества сварочных работ и приемка сварных соединений и узлов на всех стадиях сборки и сварки конструкций должны быть организованы с привлечением специалистов в соответствии с указаниями подраздела 5.7 ГОСТ 23118-2012.
11.3.2 Методы и объемы контроля сварных соединений и готовых изделий должны быть приведены в проектной документации в виде указания конкретных процедур либо в виде ссылки на соответствующие положения НД.
11.3.3 Ремонт обнаруженных дефектных участков сварных швов следует выполнять только по разработанной технологической документации, прошедшей аттестацию.
Требования к контрольным сборкам
12.1 Контрольная и общая сборки конструкций с монтажными болтовыми соединениями должны выполняться, если это оговорено в проектной документации, при этом качество выполненных групп отверстий в этих соединениях должно соответствовать требованиям НД на монтаж конструкций.
12.2 Контрольной сборке подвергают полностью изготовленные элементы до их грунтования и окраски.
Контрольная сборка должна подтвердить совпадение отверстий в монтажных стыках, плотность примыкания в стыках с передачей усилий через поверхности, отсутствие зазоров и депланаций в соединениях.
При сборке конструкций в каждом соединении должно быть поставлено достаточное количество болтов и пробок для обеспечения неизменяемости конструкции и безопасности проведения сборки, но не менее одного болта и одной пробки.
|
|
12.3 При отсутствии требований в НД на монтаж конструкций, собранных в процессе контрольной сборки, несовпадение отверстий в монтажных соединениях на обычных болтах должно быть проверено калибром, диаметр которого на 1,5 мм меньше проектного диаметра отверстия. Калибр должен пройти не менее чем в 75% отверстий каждой группы. В случае если калибр проходит менее чем в 75% отверстий каждой группы, проводят повторную контрольную сборку из других элементов этой конструкции. Если и в этом случае совпадение отверстий окажется недостаточным, то принимается решение о способах исправления отверстий в собранных элементах, в элементах конструкции всей партии и о целесообразности дальнейшего проведения контрольных сборок.
12.4 Несовпадение отверстий в соединениях на болтах с регулируемым натяжением должно быть проверено калибром, диаметр которого на 0,5 мм больше номинального диаметра болта. Калибр должен пройти в 100% отверстий каждого соединения. Процедуру контроля выполняют по 12.3.
12.5 В узлах элементов, прошедших контрольную сборку, должны быть сборочные и фиксирующие приспособления, предусмотренные проектной документацией.
|
|
Требования к проведению термической правки
13.1 Остаточные деформации конструкций, возникшие после сварки и превышающие значения, приведенные в 11.2.2 настоящего свода правил и приложении Б ГОСТ 23118-2012, должны быть исправлены. Исправление осуществляется способами механического, термического или термомеханического воздействия. В процессе правки должно быть исключено образование вмятин, забоин и других повреждений на поверхности стального проката.
Деталям и элементам, подлежащим сварке, следует по возможности придавать предварительное обратное смещение или компенсирующую перемещения и деформации от сварки обратную деформацию.
13.2 Термическую и термомеханическую правку производят местным нагревом металла до температуры не более 700°С (во избежание разупрочнения проката). Для горячекатаного проката допускается нагрев до температуры 900°С.
Термомеханическую правку сложных форм деформаций с применением статических нагрузок (пригрузом, домкратами, распорками) следует производить при температуре зон нагрева 650°С - 700°С. При этом остывание металла ниже 600°С не допускается.
Запрещается охлаждать нагретый металл сжатым воздухом или водой.
|
|
Требования к производству работ при защите от коррозии
14.1 Стальные конструкции в зависимости от их назначения и условий эксплуатации следует защищать от коррозии в соответствии с СП 28.13330 и проектной документацией. Основные требования к производству работ приведены в СП 72.13330. Дополнительные требования приведены в настоящем разделе.
14.2 Процесс получения лакокрасочных покрытий состоит в последовательном выполнении следующих операций: подготовка поверхности, нанесение грунтовочных слоев, сушка каждого грунтовочного слоя, нанесение требуемого числа промежуточных и внешних слоев лакокрасочного покрытия, сушка каждого слоя.
14.3 В соответствии с ГОСТ 9.105 и ГОСТ 9.402 все операции по подготовке поверхности и нанесению лакокрасочных покрытий следует проводить в закрытом помещении при температуре воздуха не менее 15°С и относительной влажности воздуха не более 80%.
14.4 Длительность перерыва между подготовкой поверхности и окрашиванием должна быть не более 24 ч. При хранении конструкций и заготовок на открытом воздухе при условии отсутствия атмосферных осадков, интервал между подготовкой поверхности и окрашиванием должен быть не более 6 ч.
|
|
14.5 Подготовка поверхности перед нанесением лакокрасочных покрытий должна включать следующие операции:
- зачистка сварных швов и рядом расположенных поверхностей конструкций от брызг расплавленного металла, остатков флюсов, шлака;
- удаление заусенцев и острых кромок;
- обезжиривание замасленных металлических поверхностей перед механической очисткой;
- механическая очистка поверхности от ржавчины и окалины;
- обеспыливание обдувкой сжатым воздухом (или промышленными пылесосами).
14.6 При подготовке поверхности перед нанесением покрытий необходимо обеспечивать установленную проектной документацией, чертежами КМД, ГОСТ 9.402 и СП 28.13330 степень очистки поверхности конструкций от окалины и ржавчины для различных по степени агрессивности условий эксплуатации.
14.7 Перед нанесением лакокрасочных покрытий не выполняют механическую подготовку поверхности конструкций с цинковыми или алюминиевыми покрытиями, полученными методом газотермического напыления.
Перед нанесением лакокрасочных покрытий на поверхность горячего цинкового покрытия его предварительно подвергают абразивоструйной очистке с применением мелкого абразива для придания шероховатости.
14.8 Перед абразивоструйной очисткой поверхности от окалины и ржавчины поверхность конструкций должна быть обезжирена. Степень обезжиривания должна соответствовать первой степени по ГОСТ 9.402.
14.9 Лакокрасочные покрытия необходимо наносить в такой последовательности:
- выполнение полосового окрашивания;
- сушка покрытия;
- нанесение грунтовочного покрытия;
- сушка грунтовочного покрытия;
- нанесение промежуточных и внешних слоев покрытия с сушкой каждого слоя.
14.10 На конструкции и заготовки лакокрасочные материалы следует наносить одним из следующих методов: пневматическим или безвоздушным распылением, струйным обливом, распылением в электрическом поле, окунанием, кистью.
Метод нанесения лакокрасочных материалов следует устанавливать по ГОСТ 9.105 в зависимости от вида применяемого лакокрасочного материала, габаритов и конфигурации конструкций.
Технологические режимы нанесения лакокрасочных материалов устанавливают в соответствии с НД на конкретный применяемый материал.
14.11 Для поверхностей, очищенных от окалины и ржавчины абразивоструйным способом, минимально допустимая толщина лакокрасочного покрытия должна быть не менее 80 мкм.
14.12 Сушку лакокрасочных покрытий следует осуществлять в соответствии с НД на конкретные материалы.
14.13 При выполнении защиты конструкций от коррозии необходимо проводить контроль качества:
- подготовки поверхности;
- лакокрасочных материалов;
- защитных покрытий.
14.14 Качество подготовленной поверхности перед нанесением лакокрасочных материалов необходимо контролировать по степени очистки от окалины и ржавчины и степени обезжиривания методами, предусмотренными ГОСТ 9.402.
14.15 Контроль качества лакокрасочных материалов следует осуществлять методами, предусмотренными соответствующими НД. Лакокрасочные материалы по всем показателям должны соответствовать НД.
14.16 Правильность выбора растворителей, рабочих вязкостей, методов и параметров нанесения, а также режимов сушки лакокрасочных покрытий при выполнении технологического процесса получения лакокрасочных покрытий следует контролировать в соответствии с НД на конкретные материалы.
14.17 Качество лакокрасочных покрытий необходимо контролировать по внешнему виду, толщине, сплошности и адгезии.
14.18 Качество внешнего вида покрытий следует контролировать визуальным осмотром при естественном или искусственном рассеянном освещении 100% поверхности конструкций. Покрытие должно быть без пропусков, пузырей, трещин, сколов, кратеров и других дефектов, влияющих на защитные свойства, и по внешнему виду должно соответствовать СП 28.13330 и ГОСТ 9.032.
14.19 Сплошность покрытий необходимо контролировать дефектоскопом.
14.20 Толщину покрытия следует контролировать толщиномером электромагнитного типа с погрешностью не более 5% по ГОСТ 31993 в трех точках по длине элемента. Определение толщины покрытия в каждой точке проводят по пяти контрольным измерениям толщины в радиусе 5 мм. За единичное измерение толщины принимают среднее значение из трех измерений; максимальное и минимальное значения не учитываются.
14.21 Адгезию лакокрасочных покрытий определяют методом решетчатых надрезов по четырехбалльной шкале в соответствии с ГОСТ 15140 или по шестибалльной шкале в соответствии с ГОСТ 31149. При определении адгезии по методу нормального отрыва по ГОСТ 32299 измерения проводят приборами с точностью до 0,1 МПа.
14.22 Адгезию покрытия проверяют на контрольных образцах, окрашенных вместе с конструкциями. Адгезия покрытия должна быть не более 2 баллов по методу решетчатых надрезов по ГОСТ 15140 для покрытий толщиной до 200 мкм, не более 1 балла по методу Х-образного надреза по ГОСТ 32702.2 для покрытия толщиной более 200 мкм или по методу нормального отрыва по ГОСТ 32299 - не менее 4 МПа.
Дата добавления: 2021-01-21; просмотров: 52; Мы поможем в написании вашей работы! |
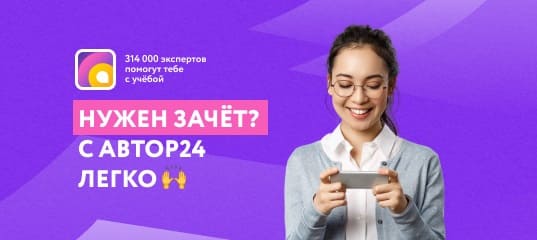
Мы поможем в написании ваших работ!