Расчет годового фонда времени
Годовые фонды времени рабочих, оборудования, рабочих мест (рабочих постов) определяют исходя из режима работы участка.
Различают два вида годовых фондов времени рабочего: номинальный и действительный.
Номинальный годовой фонд времени рабочего Фи.р.,ч, учитывает полное календарное время работы и определяется по формуле:
Фи.р = (dк - (dв + dп)) × tсм – tск × nп , (2)
Где:
dк = 365- количество календарных дней в году;
dв, dп = 118 - выходных и праздничных дней в году;
tсм - продолжительность рабочей смены, ч (таблица 7);
tск - сокращение длительности смены в предпраздничные дни, ч
nп - количество предпраздничных дней в году с сокращенной продолжительностью рабочей смены (количество рабочих дней, непосредственно предшествующих праздничным дням), nп = 3 дней;
Фи.р = (365 – 118) × 8 – 1 × 3 = 1973
Действительный годовой фонд времени рабочего Фд.р, ч, учитывает фактически отрабатываемое время рабочим в течение года с учетом
трудового отпуска, потерь рабочего времени по уважительным причинам и определяется по формуле:
Фд.р = ((dк - (dв + dп + dо) × tсм – tск × nп ) ηр , (3)
Где:
dо- продолжительность трудового отпуска, календарные дни ;
ηр- коэффициент, учитывающий потери рабочего времени по уважительным причинам (Таблица 7).
|
|
Фд.р = ((365 – 118) × 8 – 1 × 3) × 0,97 = 1728
Таблица 7 - Коэффициенты для расчета годового фонда времени для рабочего
Наименование профессии | tсм, ч | tск, ч | dо, дни | ηр |
Маляры, работающие в камерах | 7 | 0 | 24 | 0,96 |
Прочие профессии | 8 | 1 | 24 | 0,97 |
Номинальный годовой фонд времени работы оборудования Фн.об, ч, учитывает время, в течение которого оно может работать при заданном режиме, и определяется по формуле:
Фн.об = (((dк - (dв + dп )) × tсм – tск × nп) у, (4)
Где:
у - количество рабочих смен.
Фн.об = ((365 – 118) × 8 – 1 × 3) × 1 = 1973
Действительный годовой фонд времени работы оборудования Фд.об, ч, учитывает неизбежные простои оборудования из-за профилактического обслуживания и ремонта и представляет собой время, в течение которого оно может быть полностью загружено производственной работой:
Фд.об = Фн.об × (1 – ηоб), (5)
Где:
ηоб - коэффициент, учитывающий потери времени на выполнение планово-предупредительного ремонта оборудования (Таблица 8).
Фд.об = 1973 × (1 – 0,02) = 1934
Таблица 8 - Коэффициент, учитывающий потери времени на выполнение планово-предупредительного ремонта оборудования, ηоб
|
|
Вид оборудования
| Количество рабочих смен | |
Одна | Две | |
Металлорежущее, заготовительное | 0,02 | 0,03 |
Кузнечно-прессовое | 0,03 | 0,04 |
Защитных покрытий (окрасочное, металлопокрытий): автоматизированное неавтоматизированное | - 0,02 | 0,08 0,03 |
Сварочное | 0,03 | 0,04 |
Сборочное, испытательное механизированное | 0,02 | 0,03 |
Моечно-очистное | 0,03 | 0,04 |
Номинальный Фн.п, ч, и действительный Ф д.п, ч, годовой фонд времени рабочего места (поста) определяется временем, в течение которого оно используется при заданном режиме работы участка.
Расчет годовой трудоемкости работ на участке
При проектировании участков восстановления деталей годовой объем работ (ТГ), используемый для определения количества производственных рабочих, рассчитывается по формуле:
ТГ = t×n×N×Кмр,чел. – ч, (6)
Где:
t - трудоемкость на единицу продукции и для заданных условий, чел-ч;
n - число одноименных деталей в изделии;
N - годовая программа (принимается согласно заданию);
|
|
Кмр - маршрутный коэффициент ремонта (принимается согласно заданию).
На сборку стартера:
ТГ = 0,40× 1× 200 × 0,80 = 64 чел/ч
На разборку стартера:
ТГ = 0,35× 1× 200 × 0,80 = 56 чел/ч.[11]
Корректирование трудоемкости на единицу продукции для заданных условий выполняется по формуле:
T=t1× K1× K2× K3,чел.-ч , (7)
Где:
t1- норма трудоемкости капитального ремонта агрегата для эталонных условий, чел.- ч
K1 - коэффициент корректирования трудоемкости, учитывающий величину годовой производственной программы (по автомобилям или агрегатам каждой модели), [10];
K2 - коэффициент корректирования трудоемкости, учитывающий многомодельность ремонтируемых агрегатов автомобилей, [10];
K3- коэффициент корректирования трудоемкости, учитывающий структуру производственной программы завода (соотношение капитальных ремонтов полнокомплектных автомобилей и комплектов агрегатов),[10];
t=0.75×1.23×1.05×1.04=1.007 чел.- ч
Дата добавления: 2019-11-16; просмотров: 637; Мы поможем в написании вашей работы! |
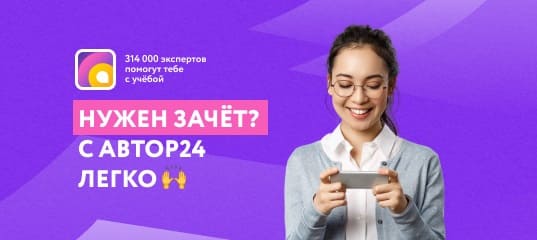
Мы поможем в написании ваших работ!