Расчет допусков размеров, входящих в размерные цепи
Для у казанного сборочного узла
Рисунок 7 схема узла для создания размерной цепи
Составить схему размерной цепи, с представлением эскиза узла и обозначениями на нем размеров, входящих в размерную цепь. По заданному значению поля допуска замыкающего звена и номинальным размерам составляющих звеньев, приведенных в таблице найти допуски составляющих звеньев методом полной взаимозаменяемости.
Таблица 6 Исходные данные для задачи
№п/n | Номинальные размеры составляющих | Замыкающее звено | |||||||
Номинальный размер, мм | Отклонения, мкм | ||||||||
позиция 1 | позиция 2 | позиция 3 | позиция 4 | позиция 5 | позиция 6 | верхнее | нижнее | ||
38 | 108 | X | 22 | 60 | 22 | 6 | X | +600 | +200 |
Рисунок 8 Схема размерной цепи узла
Где А2 - замыкающий размер, т.к. получается последним в процессе сборки узла (его значение и точность зависят от значений и точности остальных размеров цепи).
А1, А3, А4, А5, А6 – составляющие звенья размерной цепи, изменение которых вызывает изменение замыкающего звена (но не может и не должно вызывать изменение исходного звена).
Основное уравнение размерной цепи:
![]() | (5.1) |
где m - число звеньев размерной цепи, включая замыкающее;
n - число увеличивающих звеньев Aj;
(m-1-n) - число уменьшающих звеньев Ak.
Таким образом, номинальный размер замыкающего звена определяется как разность между суммами номинальных увеличивающих и уменьшающих звеньев.
|
|
Допуск замыкающего звена:
![]() | (5.2) |
т.е. равен сумме допусков составляющих звеньев.
Верхнее отклонение замыкающего звена ES = +600 мкм.
Нижнее отклонение замыкающего звена EI =+200 мкм.
TA ∆ = 600-200 = 400 мкм. |
Определим номинальный размер неизвестного звена:
A1+ A2= A3+ A4+ A5+ A6 | (5.3) |
A2= A3+ A4+ A5+ A6 - A1=22+60+22+6-108=2мм
Для определения требуемого квалитета точности определяют коэффициент точности по формуле:
![]() | (5.4) |
где ij - единица допуска (см. табл. 7), соответствующая размеру А i.
Таблица 7
Основные интервалы номинальных размеров, мм | Значение i, мкм |
до 3 мм | 0,55 |
3-6 | 0,73 |
6-10 | 0,90 |
10-18 | 1,08 |
18-30 | 1,31 |
30-50 | 1,56 |
50-80 | 1,80 |
80-120 | 2,17 |
Подбираем по ГОСТ 28428-90 радиальный сферический двурядный подшипник с толщиной В=22мм: 1212
По ГОСТ 520-2002 определяем допуски для подшипников(TA3;TA5)
TA3=120мкм; TA5=120мкм
По таблице 5.3 находим значение единиц допуска для соответствующих звеньев, в мкм:
i1 = 2,17
i4 = 1,80
i6 = 0,90
![]() | (5.5) |
По найденному значению коэффициента точности аср определяют наиболее подходящий квалитет, пользуясь табл. 7, и по таблицам допусков на цилиндрические детали (ГОСТ 25346-89) находим допуски для составляющих звеньев:
|
|
Таблица 8 Значение коэффициента точности a при различных квалитетах
Квалитет IT | Коэффициент точности а |
5 | 7 |
6 | 10 |
7 | 16 |
8 | 25 |
9 | 40 |
10 | 64 |
Для аср= 32.85 принимаем допуски для 9 квалитета.
Т1 = 87мкм; Т4 = 74мкм; Т6 =36мкм.
ΣTAi = Т1+ Т3+ Т4+ Т5+ Т6 = 87+120+74+120+36 =437 мкм.
Таким образом условие, выраженное формулой (5.2) не выполняется и необходимо произвести корректировку. Принимаем допуск звена Т4 и Т6 по 8 квалитету и допуски будут равны соответственно 46мкм и 22мкм что даст в итоге 395мкм — что удовлетворяет условию (5.2)
Назначим отклонения всех составляющих звеньев кроме А1 в «минус», так как все размеры являются уменьшаемые, а размер А1 может иметь отклонения любого знака
А6=5-0,022
А3=18-0,120,
А4=52-0,046,
А5=18-0,120
Отклонение размера А1 определяется из уравнений:
Верхнее отклонение замыкающего звена:
![]() | (5.6) |
Е SA1=292
Нижнее отклонение замыкающего звена:
![]() | (5.7) |
Е IA1=200 мкм
ТА1=92 мкм.
Произведем проверку, ТАΔ=400 мкм:
ΣTAj = 92+120+46+120+22 = 400 мкм.
Т.е. допуск замыкающего звена равен сумме допусков составляющих звеньев.
|
|
А6=6-0,022
А5=22-0,120
А4=60-0,046,
А3=22-0,120,
Расчет резьбового соединения
По исходным данным определить предельные размеры диаметров резьбы болта и гайки и построить схему расположения полей допусков данного соединения. Определить приведенные средние диаметры резьбы болта и гайки. Дать заключение о годности резьбового соединения в соответствии с заданными требованиями
Таблица 9 Исходные данные задачи
№ п/п | Обозначение резьбового соединения | Измеренный (действительный) средний диаметр, мм | Накопленная погрешность по шагу, мкм | Средняя ошибка угла наклона сторон профиля, мин | |||
d2изм | D2изм | ΔPп.б | ΔРп.г | Δ αб/2 | Δαг/2 | ||
39 | М68×3-7G/8g | 66,050 | 66,200 | +80 | +20 | -40ˊ | -50ˊ |
Приведенный средний диаметр внутренней резьбы:
dпр=d2изм+ fp + fα, | (6.1) |
Приведенный средний диаметр внутренней резьбы
Dпp=D2изм - (fp+ fα), | (6.2) |
Диаметральная компенсация погрешности шага на длине свинчивания fp, мкм
fp= l,732ΔPn | (6.3) |
где ΔРп - накопленная погрешность шага, мкм.
Диаметральная компенсация погрешности угла наклона сторон профиля fα, мкм
|
|
fα= 0,29P Δα/2 | (6.4) |
где Р - шаг резьбы, мм;
Δα/2 - средняя ошибка угла наклона сторон профиля, в минутах.
Из анализа схем следует условие годности резьбы.
Для болта:
d2изм ≥ d2min ; dпр ≤ d2max; | (6.5) |
для гайки:
D2изм ≤ D2max; Dпр≥D2min. | (6.6) |
Согласно ГОСТ 9150-81 в соответствии с заданным резьбовым соединением устанавливаются номинальные значения диаметров:
d(D) = 68.00 мм;
d1(D1) = 64.752 мм;
d2(D2) = 66.051 мм
По ГОСТ 16093-81 устанавливаются предельные отклонения диаметров резьбы и подсчитываются предельные размеры болта и гайки [3]. Отклонения диаметров резьбы болта и гайки.
ei/EI | es/ES |
ei(d2)= -383мкм ei(d)= -648 мкм EI(D1)=+48мкм EI(D2)=+48мкм EI(D)=+48мкм | es(d2)= -48мкм es(d)= -48мкм es(d1)=-48мкм ES(D2)= +403мкм ES(D1)= +678мкм |
Предельные диаметры болта:
d2MIN = d2 + ei (d2) = 65.668 мм
d2MAX = d2 + es (d2) = 66.003мм
dMIN = d + ei (d) =67.352 мм
dMAX = d + es (d) = 67.952 мм
d1MIN – нет
d1MAX= d1 + es (d1) = 64.704 мм
Предельные диаметры гайки:
D2MIN = D2 + EI (D2) = 66.099 мм
D2MAX = D2 + ES (D2) = 66.454мм
DMIN = D + EI (D) = 68.048 мм
DMAX – нет
D1MIN = D1 + EI (D1) = 64.8 мм
D1MAX = D1 + ES (D1) = 65.43 мм
Определим следующие допуски:
TD1= D1max - D1min = 0.63мм.
TD2 = D2max - D2min = 0.355 мм.
Td2= d2max - d2min = 0.355 мм.
Td= dmax - dmin = 0.6 мм.
По полученным результатам строим схему расположения полей допусков заданного резьбового соединения:
Рисунок 9 Поля допусков резьбового соединения
При имеющихся погрешностях по углу, шагу и измеренным (действительным) средним диаметрам d2изм, D2изм устанавливаются приведенные средние диаметры резьб dпр(Dпр).
Приведенный средний диаметр резьбы болта:
dпр=d2изм+ fp + fα
fp= 1.732ΔPn = 138,56 мкм
fα= 0.36P Δα/2 =-43,2 мкм
dпр= d2изм+ fp + fα = 66,145 мм.
Приведенный средний диаметр резьбы гайки:
Dпp=D2изм - (fp+ fα) =69.13556 мм.
fp= 1.732ΔPn=34,64 мкм.
fα= 0.36P Δα/2 = -54 мкм.
Dпp=D2изм - (fp+ fα) =66,219 мм.
По формулам (6.5), (6.6) проверяется годность резьбы:
для болта
66,050 ≥ 65.668; 66,145 ≥66,003
для гайки
66,200 ≤ 66.454; 66,219 ≥ 66.099
Заключение о годности резьбового соединения: резьбовое соединение является годным.
2.8
Шлицевое соединение
Для шлицевого соединения с заданным числом зубьев n, внутренним диаметром d, внешним диаметром D и шириной зубьев b, работающего при заданных условиях, выбрать:
а) вид центрирования;
б) тип посадки и определить допуски и предельные размеры всех элементов соединения;
в) построить схемы расположения полей допусков;
г) дать сборочный чертеж шлицевого соединения.
Таблица 10 Исходные данные для задачи
№ варианта | Соединение | Число зубьев, n | Диаметры, мм | Твердость втулки | Условия движения | |
d | D | |||||
40 | Подвижное | 8 | 42 | 46 | Высокая | Нереверсивное |
Так как втулка имеет высокую твердость и центрирование принимается для подвижных соединений при нереверсивном движении, то целесообразно выбрать центрирование по внутреннему диаметру d. [1 c.334-336]
Номинальные размеры шлицевого соединения: 8×42×66 (n×d×D). По ГОСТ 1139-80 находим ширину зубьев b=8 мм.
В соответствии с рекомендациями и ГОСТ 1139-80 выбираем посадки:
Для размера d- для размера b
. Обозначим выбранное шлицевое соединение:
.
По значениям для данной посадки ГОСТ 25-346 строим схему расположения допусков:
Рисунок 10 Схема расположения полей допусков шлицевого соединения
Рисунок 11 Сборочный чертеж соединения
Список литературы
1. Якушев А.И., Воронцов Л.Н., Федотов Н.М. Взаимозаменяемость, стандартизация и технические измерения М.: Машиностроение, 1987, 352 с. Учебник для втузов. 6-е изд., перераб. и дополн.
2. Допуски и посадки: Справочник. В 2–х ч. / Под ред. В.Д. Мягкова. – Л.: Машиностроение, 1982. – 817 с.
3. ГОСТ16319–80. Цепи размерные. Основные положения, термины, обозначения и определения. – М.: Изд–во стандартов, 1982. – 20 с.
4. ГОСТ25346–82. Единая система допусков и посадок. Общие положения, ряды допусков и основных отклонений. – М.: Изд–во стандартов,1983. – 24 с.
5. ГОСТ16775–71 – ГОСТ16780–71. Калибр–скобы гладкие и калибр–пробки гладкие, оснащенные твердым сплавом. – М.: Изд–во стандартов., 1984. – 27 с.
6. ГОСТ18358–73 – ГОСТ18369–73. Калибр–скобы диаметром от 1 до 360 мм. Конструкция и размеры. М.: Изд–во стандартов, 1985. – 71 с.
7. ГОСТ2015–84. Калибры гладкие нерегулируемые. Технические требования. – М.: Изд–во стандартов, 1984. – 5 с.
8. ГОСТ8.051–81. Погрешности, допускаемые при измерении линейных размеров до 500 мм. – М.: Изд–во стандартов, 1983. – 10 с.
9. ГОСТ9150–81. Резьбы метрические. Основные нормы взаимозаменяемости. – М.: Изд–во стандартов, 1982. – 4 с.
10. Червач Ю.Б. Метрология, стандартизация и сертификация: учебное пособие / Ю.Б. Червач; Томский политехнический университет. – Томск: Изд-во Томского политехнического университета, 2010. – 55 с.
Дата добавления: 2019-02-22; просмотров: 950; Мы поможем в написании вашей работы! |
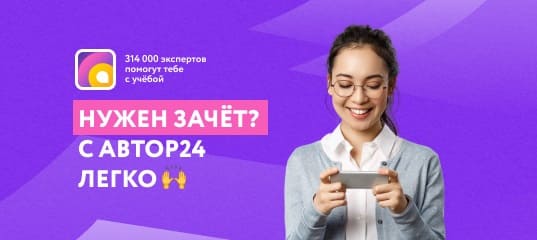
Мы поможем в написании ваших работ!