Расчет и выбор средств измерения для гладких цилиндрических деталей
Министерство образования и науки Российской Федерации Федеральное государственное бюджетное образовательное учреждение высшего профессионального образования «Национальный исследовательский Томский политехнический университет» Инженерная школа новых производственных технологий Направление: «Машиностроение» Отделение материаловедения \
КУРСОВАЯ РАБОТА
По дисциплине
«Метрология, стандартизация и сертификация»
Вариант №65
Выполнил
студент гр.4А51 | _______________ | Стебунов Р. Д. |
(подпись, дата) |
Проверил
доцент кафедры ТМСПР | _______________ | Алфёрова Е.А. |
(подпись, дата) |
2.1
Номера задач курсовой работы
Вариант заданий | Номера задач | ||||||
1 | 2 | 3* | 4 | 5 | 6 | 7 | |
Варианты задач | |||||||
65 | 35 | 36 | -* | 37 | 38 | 39 | 40 |
*Исходные данные к решению третьей задачи принимаются по тексту ее решения.
Расчетные задачи
Посадка с гарантированным зазором
Рассчитать, выбрать посадку и построить схему расположения полей допусков из системы ISO (ИСО) для гидродинамических подшипников скольжения при исходных данных приведенных в табл. 1.
Таблица 1
№ п/п | Номинальный диаметр соединения подшипника, d, мм | Длина соединения подшипника l, мм | Частота вращения цапфы n, об/мин | Радиальная нагрузка R, кН | Масло (смазочный материал) | Rz1 (вкладыш), мкм | Rz2 (цапфа), мкм |
35 | 150 | 60 | 2000 | 5 | Турбинное 30 | 1,6 | 2,5 |
1. Определяем относительный зазор по формулам из [16]:
|
|
![]() | (1.1) |
![]() | (1.2) |
Где d-номинальный диаметр соединения подшипника, n- частота вращение цапфы, -окружная скорость. По (1.1) и (1.2) находим:
![]() |
2. Определяем динамическую вязкость для масла «Турбинное 30»
![]() | (1.3) |
Где –динамическая вязкость при tn=50° С по таблица 1.2 [16]
![]() |
3. Находим давление приходящегося на единицу площади проекции опорной поверхности подшипника:
![]() | (1.4) |
Где R-радиальная нагрузка, d-номинальный диаметр соединения подшипника, l-длина соединения подшипника. По (1.4) находим:
![]() |
4. Определяем наименьшую толщину масляного слоя:
![]() | (1.5) |
-принимается в размере 3мкм.
-коэффициента запаса надежности по толщине масляного слоя.
![]() |
5. определяем угловую скорость:
![]() | (1.6) |
По формуле (1.6) находим:
![]() |
Из гидродинамической теории смазки известно, что несущая способность смазочного слоя в подшипнике определяется по формуле:
![]() | (1.7) |
6. Определим из этого уравнения :
![]() | (1.8) |
Вычисляем по (1.8):
![]() |
Из (табл. 1.3 [16]) выбираем Х=0,5
X-относительный эксцентриситет.
7. находим значения Sопт
|
|
![]() | (1.8) |
По формуле (1.8) определяем значения Sопт:
![]() |
8. Определяем предельные функциональные зазоры (SminF , SmaxF)
![]() | (1.9) |
![]() | (1.10) |
=48мкм;
=3346мкм;
9. По ГОСТ 25347-2013 определяем, что ближайшей посадкой для реализации полученных расчетных значений будет посадка
Рассчитаем запас на износ Sи
Рисунок 1 Схема расположения полей допусков
Посадка с натягом
Рассчитать, выбрать и представить схему расположения полей допусков посадки с натягом с указанием размеров, отклонений из системы ISO (ИСО) при соответствующих исходных данных, которые приводятся в табл. 2.
Таблица 2
№ п/п | Передаваемая осевая сила Р, кН | Передаваемый момент Мкр, Нм | Номинальный | Диаметр отверстия пустотелого вала d1, мм | Наружный диаметр втулки d2, мм | Номинальная длина сопряжения l, мм | Материал | Метод запрессовки | Смазка | |
Вала | Втулки | |||||||||
36 | 3 | 16 | 200 | 80 | 270 | 100 | Сталь 30 | Сталь 30 | Механич. | – |
Рассчитаем наименьший натяг, при условии отсутствия относительного смещения деталей.
![]() | (2.1) |
Где – удельное эксплуатационное давление по поверхности контакта, Па; D – номинальный диаметр сопряжения, мм; ED, Еd – модули упругости материалов соединяемых деталей (для стали Е
2,06×1011 Па); С D, Сd – коэффициенты жесткости.
|
|
при совместном действии осевой нагрузки и крутящего момента находится по формуле:
![]() | (2.2) |
где P – осевое усилие, Н; Мкр– крутящий момент, Н×м; D и l – номинальные диаметр и длина соединения, мм; n = 2 – коэффициент запаса прочности соединения на возможные перегрузки и воздействие вибраций; f=0.20 – коэффициент трения сцепления при распрессовке (табл. 2.3 [17]). По формуле (2.2) рассчитаем:
![]() |
СD и Cd рассчитываются по формулам:
![]() | (2.3) |
![]() | (2.4) |
где: D, d1, d2 – соответствующие диаметры сопрягаемых деталей, мм; ,
– коэффициенты Пуассона для металлов охватывающей и охватываемой деталей (табл. 2.2 [17]). По формуле (2.3) и (2.4) найдем:
![]() | |
![]() |
Исходя из этого по формуле (2.1) найдем наименьший расчетный натяг.
![]() ![]() |
Рассчитаем наибольший натяг, при условии обеспечения прочности соединяемых деталей.
Для этого определим предельное допустимое удельное контактное давление.
РдопD = 0.58 ![]() | (2.5) |
Рдопd = 0.58 ![]() | (2.6) |
Где
и
– условный предел текучести или предел прочности сопрягаемых деталей (табл. 2.2 [17]).
По формулам (2.5), (2.6) определим предельное допустимое удельное контактное давление
|
|
РдопD = 0.58 ![]() ![]() | |
Рдопd = 0.58 ![]() ![]() |
В качестве Pнб принимаем наименьшее значение Pдоп. Pнб= Па. Максимальный допустимый расчетный натяг:
![]() | (2.7) |
Вычисляя по формуле (2.7), находим:
![]() |
Для расчёта компенсации влияния микронеровностей воспользуемся формулой для материалов с одинаковыми механическими свойствами:
![]() ![]() | (2.8) |
где – коэффициенты, учитывающие смятие микронеровностей поверхностей отверстия и вала, приведенные в табл. 2.4 [17],
– высота микронеровностей отверстия,
– высота микронеровностей вала (табл.2.5 [17]). По (2.8) найдем:
![]() |
Таким образом, значения натягов при выборе посадок:
![]() ![]() ![]() | |
![]() ![]() ![]() |
Допуск натяга определяется как:
TN= ![]() | (2.9) |
Определим допуск натяга по (2.9):
TN=369-13=356 мкм. |
В соответствии с ГОСТ 25347–2013 принимаем посадку Æ или
Æ — для которой является характерным следующее:
· допуск отверстия Т Dтабл= 0.115 мм;
· допуск вала Т dтабл= 0.072 мм;
· минимальный натяг Nmin табл= 0.051 мм;
· максимальный натяг Nmax тa6л= 0.238 мм;
· допуск посадки TNтабл = Nmax табл–Nmin табл= 0.187 мм
Посадка будет считаться выбранной правильно, если выполняются условия:
≤ Nmin табл ; 13 мкм ≤ 51 мкм;
≥ Nmax тa6л ; 369 мкм ≥ 238 мкм;
Следовательно, делаем вывод, что выбранная посадка является верной.
Рисунок 2 Схема расположения полей допусков для выбранной посадки с натягом
Расчет и выбор средств измерения для гладких цилиндрических деталей
Для выбранной посадки в первой или второй задаче построить схему расположения полей допусков калибров для контроля деталей сопряжения. Определить предельные и исполнительные размеры рабочих и контрольных калибров. Выполнить рабочие чертежи предельных калибров для контроля деталей принятого соединения.
Выбрано соединение Æ . По ГОСТ 25347–82 находим предельные отклонения и устанавливаем предельные размеры контролируемых изделий: Dmax = 200,115мм; Dmin =200,000мм; dmax =200,238мм; dmin =200,166мм. По ГОСТ 24853–81 устанавливаем допуски и предельные отклонения калибров и контркалибров и заносим в табл.3
Таблица 3 Исходные данные
Деталь | Калибры–пробки | Калибры–скобы | Контрольные калибры | ||||||
Параметры, мкм | |||||||||
Z | Y | Н | α | Z1 | Y1 | H1 | α1 | НР | |
Отверстие 200Н9 | 21 | 0 | 10 | 4 | — | — | — | — | 7 |
Вал 200t8 | — | — | — | — | 12 | 7 | 14 | 4 | 7 |
Допуск на форму калибра, мкм | IТ2 | IT3 | IT1 |
Определяем предельные и исполнительные размеры рабочих калибров согласно табл. 1 ГОСТ 24853–81.
Наибольший предельный размер нового проходного калибра–пробки:
Наименьший размер изношенного проходного калибра–пробки:
Наибольший размер непроходного нового калибра–пробки:
Аналогично по методике из ГОСТ- 24853-81 находятся остальные значения, и заносятся в табл. 4.
Таблица 4 Предельные и исполнительные размеры калибров
Предельные размеры, мм | Исполнительные размеры, мм | ||
Калибр–пробка | ПР | dmax=200,026 dmin=200,016 dизн=200,004 | 200,026-0,010 |
НЕ | dmax=200,116 dmin=200,106 | 200,106+0,010 | |
Калибр–скоба | ПР | Dmax=200,233 Dmin=200,219 Dизн=200,245 | 200,219+0,014 |
НЕ | Dmin=200,159 Dmax=200,173 | 200,173-0,014 | |
Контр. калибры | К-ПР | dmax=200,2295 dmin=200,2225 | 200,2295–0.007 |
К-И | dmax=200,2485 dmin=200,2415 | 200,2415+0.007 | |
К-НЕ | dmax=200,1735 dmin=200,1665 | 200,1735–0.007 |
По ГОСТ 2015-84 по табл. 1 выбираем шероховатость для калибра пробки 0.16 калибра скобы 0.16 контрольный калибр 0.08. Рисуем схему полей допусков (Рис. 3).
Рисунок 3 Схема расположения полей допусков калибров
По результатам расчета в соответствии с требованиями и указаниями допуска на форму и шероховатость поверхности выполняются эскизы рабочих калибров.
Рисунок 4 Эскиз проходного калибра
Рисунок 5 Эскиз калибра скобы
Дата добавления: 2019-02-22; просмотров: 358; Мы поможем в написании вашей работы! |
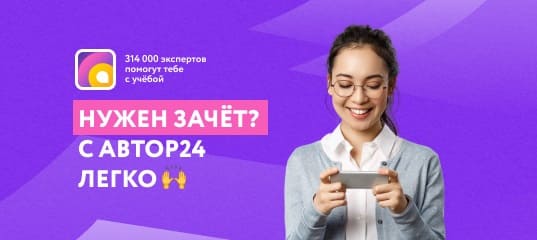
Мы поможем в написании ваших работ!