ПП 01.02 Проведение ремонта оборудования на предприятиях
Транспорта и хранения газа
Фроловское линейное производственное управление магистральных газопроводов (ФЛПУМГ) - один из 18-ти газотранспортных филиалов ООО “Газпром трансгаз Волгоград”. Во Фроловское ЛПУМГ входит – Фроловская КС-1, состоящая из 2-х компрессорных цехов.
Компрессорная станция КС-1 предназначена для компримирования газа, транспортируемого по газопроводам Средняя Азия-Центр: «САЦ-III, САЦ-IV-1, САЦ-IV-2». Промышленная эксплуатация КС- началась с 1974 года.
На станции применена схема с последовательно-параллельной обвязкой ГПА для применения неполнонапорных нагнетателей.
КС-1 Фроловского ЛПУМГ включает в себя два цеха КЦ-1 и КЦ-2, в которых установлены следующее оборудования:
КЦ-1 газоперекачивающие агрегаты: ГТК-10-4 (в кол-ве 6 шт., общей мощностью 60000 кВт) зав. изг. НЗЛ и «Дальэнергомаш» мощностью 10000 кВт, КПД 30%, номинальное частота вращение турбин ТВД 5200 об/мин, ТНД 4800 об/мин, имеет 10-ти ступенчатый компрессор с давлением в нагнетании 3,5 кг с/см2 предназначенный для привода центробежного нагнетателя ЦБН 520-12-1 зав. изг. НЗЛ, в количестве 6 шт., ЦБН неполнонапорный, одноступенчатый, с консольным креплением колеса, степень сжатия 1,27, производительность 29.3 млн куб м/сут, предназначенный для транспортировки природного газа по газопроводу Средняя Азия – Центр «САЦ-III», Ду 1220 мм и номинальным давлением 55 кг с/см2
Район инженерно-технологических изысканий под строительство КЦ-1 расположен в Волгоградской области в 17 км к югу от г Фролово близ х Новая Паника.
|
|
В тектоническом отношении описываемый район приурочен к Доно-Медведицкой дисколации, в геоморфологическом к Арчединско-Донским пескам – зона аккумуляцивного рельефа, созданного поверхностными текущими водами.
В Гидрологическом отношении район характеризуется распространением вод гидрокарбонатного типа, частично с содержанием органических веществ. К бетону вода не агрессивна.
Площадка КЦ-1 расположена в 250 м от дороги г Фролово – Дон на неудобных для посева землях. Абсолютные отметки поверхности площадки 128,4 – 136,33 м.
Естественным основанием фундаментов сооружений КС на глубине заложения 1,5 – 2 м будут мелкие, маловлажные, средней плотности пески, легкие, твёрдые супеси и лессовидные твёрдые суглинки. При строительстве предусмотреть мероприятия в соответствии с СНИП П-Б-2-62, устраняющие проникновение поверхностных и производственных вод в просадочные суглинки.
Климатическая характеристика района расположения площадки КЦ и ЛЭП составлена на основании многолетних метеорологических наблюдений по близрасположенным метеостанциям УГМС СССР.
Климат рассмотренного района относится к зоне степей, который отличается тёплым и сравнительно сухим летом: средняя температура каждого из летних месяцев не ниже 19 о.
|
|
Летом температура не превышает 41 о, а зимой опускается до -42о.
Расположение всех сооружений выбиралось с учётом розы ветров по м/ст Арчеда.
При строительстве и монтаже объектов нефтегазопроводов и нефтегазохранилищ используются следующие машины и механизмы:
- Экскаваторы
Основное назначение экскаваторов - копание и перемещение грунта посредством ковша или механизма непрерывного действия (цепного или роторного). Исходя из этого, экскаваторы подразделяют на одноковшовые, периодического действия, и на экскаваторы непрерывного действия.
Основными частями строительных экскаваторов являются ходовая часть (колесная или гусеничная), поворотная платформа с силовой установкой и сменное рабочее оборудование.
- Погрузочно-разгрузочные машины
Основная цель этих машин и механизмов - работы по перемещению различных грузов. Обычно это самоходные универсальные машины на базе, как правило, колесных транспортных средств. В них тоже применяются быстросъемные рабочие приспособления - захваты, ковши, крановое навесное оборудование и т.д.
|
|
При строительстве газонефтепроводов и газонефтехранилищ наиболее распространены фронтальный погрузчик , бульдозер-погрузчик. Фронтальные погрузчики обеспечивают разгрузку ковша вперед в пределах заданной высоты.
При строительстве железобетонных фундаментов различных сооружений могут использоваться машины для работы с бетонными растворами.
По своему функциональному назначению эти машины и механизмы бывают трех видов: первые готовят бетонные и растворные смеси, вторые доставляют растворы на стройплощадку, третьи - укладывают и уплотняют смеси и растворы.
Грузоподъемные машины являются машинами прерывного (циклического) действия и широко распространены при производстве строительно-монтажных работ.
Машины грузоподъемные - это отдельная категория высокотехнологичных специальных автоматических и механических устройств, которые ориентированы на использование общего применения. По своим конструкционным особенностям выделяются следующие виды грузоподъемных машин:
· стрелкового типа;
· мостового типа;
· краны с несущими канатами;
· лифты;
· подъемники-вышки.
По способу и методу перемещения они бывают: передвижные, самоходные, прицепные, самоподъемные, стационарные и приставные. Из них наиболее востребованными считаются башенные передвижные и стреловые самоходные краны. В свою очередь и передвижной класс данных кранов разделяется на виды по конструкциям ходовых устройств: шагающие, рельсовые и железнодорожные. Кроме различий по классификации и основным признакам, вышеперечисленные виды грузоподъемных машин различаются по уровню маневренности поворота, конструкции грузозахватного элемента и рабочего оборудования.
|
|
В некоторых ситуациях не обойтись без грузоподъёмных механизмов.
В перечень грузоподъемных механизмов входят самые разнообразные виды оборудования: домкраты всевозможных конфигураций, тали ручные и электрические, тельферы, лебедки, подъемные краны, ножничные и мачтовые подъемники, такелажные системы.
Главным содержанием научно-технической политики ПАО «Газпром» становится ориентация на интенсивные технологии и оборудование, обеспечивающие высокую экономическую эффективность, ресурсосбережение, надежность и экологическую безопасность объектов.
Эффективность газоперекачивающего оборудования при сохранении в течение всего периода эксплуатации нормативных требований по надежности, зависит от следующих основных факторов:
-Времени простоя при проведении ППР;
-Затрат на восстановление работоспособности оборудования;
-Технического состояния оборудования;
-Степени оптимизации загрузки ГПА.
Изготовитель при формировании эксплуатационной и ремонтной документации имеет возможность и закладывает известный только ему «запас» как по срокам, так и по объемам необходимых работ по обслуживанию и ремонту, защищая себя этим от рекламаций. В свою очередь ремонтные службы имеют гарантированные объемы и минимум ответственности. В большинстве случаев при выходе из строя оборудования к ним нет никаких обоснованных претензий. Они вовремя и в полном объеме делают все, что положено по регламенту. Однако оборудование как всегда «не вовремя» ломается, причины остаются невыясненными, виновных нет, ждем, что у нас поломается завтра.
По степени учета технического состояния объекта при технической (межремонтной) эксплуатации и ремонте различают три вида систем эксплуатации:
- система эксплуатации по ресурсу. Когда при техническом обслуживании и ремонте назначают фиксированные объемы работ через заранее запланированные интервалы наработки (календарного времени). Ресурс при этом устанавливается для совокупности объектов или для отдельного объекта, исходя из условия заданного уровня надежности, независимо от состояния каждого объекта;
- система эксплуатации с контролем уровня надежности. Когда для однотипных объектов устанавливается уровень безотказности. Объекты эксплуатируются до тех пор, пока фактический уровень безотказности (параметр потока отказов) ниже заданного. В противном случае должны быть исследованы причины отказов, проведена доработка, ограничен ресурс и введен контроль параметров;
- система эксплуатации «по состоянию». В этом случае эксплуатация
заключается в периодическом или непрерывном контроле параметров, определяющих техническое состояние объекта. По результатам проверки принимается решение о необходимом сроке и объеме профилактических мероприятий диагностического обслуживания. В ремонт направляются только объекты, имеющие отклонения параметров за пределы установленного допуска и дефекты в которых не могут быть устранены профилактическими мероприятиями. Объекты, находящиеся в исправном состоянии, используются по назначению.
В условиях длительного непрерывного производства и интенсивного старения технологического оборудования и трубопроводов, при ограниченности возможных инвестиций, применение технической диагностики становится наиболее эффективным средством, обеспечивающим экономичность, эффективность и надежность работы объектов ПАО «Газпром», позволяющим перейти на ресурсосберегающую технологию эксплуатации «по фактическому состоянию».
Такой подход полностью соответствует «Федеральному закону о промышленной безопасности потенциально опасных объектов» и Постановлению Правительства РФ № 241 «О мерах по обеспечению промышленной безопасности опасных производственных объектов на территории РФ».
Сущность системы ППР
Для поддержания технического состояния оборудования магистральных газопроводов, находящихся длительное время в эксплуатации увеличиваются объемы ремонтных работ. Техническое состояние оборудования поддерживается ремонтом.
Планирование работ по техническому обслуживанию и ремонту оборудования включает две составляющие:
-Планирование объектов и объемов работ (натуральные показатели);
-Планирование затрат на техническое обслуживание и ремонт.
Применяется два подхода к планированию объектов и объемов работ по техническому обслуживанию и ремонту оборудования:
-Система планово-предупредительного ремонта;
-Ремонт по техническому состоянию.
Принципиальное отличие указанных подходов заключается в том, что является основанием для определения объекта, сроков и объемов работ.
В системе планово-предупредительного ремонта (ППР) таким основанием является наработка оборудования, а при ремонте по техническому состоянию - фактическое состояние оборудования (за исключением работ по техническому обслуживанию).
В процессе работы отдельные части машин и оборудования подвергаются износу. Восстановление их работоспособности и эксплуатационных свойств достигается путем ремонта и уходом за оборудованием. Ведущую форму системы технического обслуживания и ремонта на предприятиях составляет система планово-предупредительного ремонта оборудования (ППР). Под системой ППР понимается совокупность запланированных мероприятий по уходу, надзору и ремонту оборудования. Работы по обслуживанию и ремонту оборудования при системе ППР включают: межремонтное обслуживание и периодические ремонтные операции. Выполняются эти операции ремонтным персоналом предприятия по заранее разработанному графику.
Межремонтным периодом называется период работы оборудования между двумя очередными плановыми ремонтами.
Ремонтным периодом называется время простоя оборудования в ремонте.
Текущий ремонт представляет собой наименьший по объему вид планового ремонта, выполняемый для обеспечения или восстановления работоспособности агрегата. Он заключается в частичной разборке машины, замене или восстановлении отдельных ее узлов и деталей, ремонте несменяемых деталей.
Средний ремонт отличается от текущего большим объемом работ и числом изношенных деталей, подлежащих замене.
Капитальный ремонт - полное или близкое к полному восстановление ресурса агрегата с заменой (восстановлением) любых его частей, включая базовые. Следовательно, задача капитального ремонта - привести агрегат в состояние, полностью отвечающее его назначению, классу точности и производительности.
Известно, что не следует разбирать и ремонтировать еще хорошее оборудование. Простая разборка и сборка оборудования, даже без замены деталей, может уменьшить ресурс его работы на 30 %. Также нет гарантии, что при ремонте установят комплектующие лучшего качества. А если еще учесть неизбежную послеремонтную наработку узлов агрегата, то вместо пользы будет только вред. Но нельзя и откладывать необходимый ремонт.
Суть эксплуатации «по состоянию» состоит в том, что обслуживание и ремонт производятся в зависимости от реального текущего технического состояния механизма, контролируемого в процессе эксплуатации без каких-либо разборок и ревизий, на базе контроля и анализа соответствующих параметров.
При появлении каких-либо факторов, вызывающих отклонения от нормального состояния механизма, мы наблюдаем реакцию на их воздействие по изменению соответствующих параметров (вибрационных, параметрических и т.д.), которые в силу своей высокой информативности и чувствительности отражают происходящие с механизмом перемены. При этом определяются реальные причины происходящих изменений в каждой конкретной ситуации, принимаются обоснованные решения по их устранению.
Основу технологии перехода на обслуживание и ремонт оборудования по фактическому состоянию составляют методы и средства его диагностики, позволяющие обнаруживать и идентифицировать все потенциально опасные дефекты на начальной стадии развития.
Эксплуатация ГПА «по состоянию» предусматривает оптимизацию ремонтно-технического обслуживания оборудования и управления технологическим процессом на основе данных о реальном техническом состоянии, а также на основе фактических характеристик каждой конкретной единицы оборудования и их изменении во времени.
Состав работ, выполняемых при ремонтах ГПА типа ГТК 10-4Б
Дата добавления: 2019-03-09; просмотров: 338; Мы поможем в написании вашей работы! |
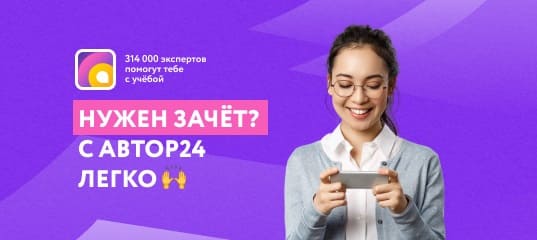
Мы поможем в написании ваших работ!