Основные процессы, состав, структура, функционирование предприятия как системы, предназначенной для достижения конечного результата.
Основными процессами для обеспечения производственной мощности шахты по добыче угля являются:
– создание безопасных условий труда;
– очистные работы;
– подготовительные работы;
– транспортировка горной массы, материалов, оборудования и людей;
– поддержание горных выработок;
– эксплуатация и поддержания оборудования в работоспособном состоянии;
– проветривание системы выработок и рабочих мест;
– электроснабжение потребителей и освещение выработок и рабочих мест;
– водоотлив;
– организация, контроль и управление процессами.
Структурно шахта построена по иерархической схеме, во главе директор, которому подчиняются главный инженер и заместители директора по производству, безопасности, и др. Главному инженеру подчиняются службы главного механика, главного энергетика и др.
Каждое из структурных направлений содержит участки – очистных работ, подготовительных работа, ВШТ, ремонта выработок и т.д.
Предприятие функционирует как единый системный комплекс, с использованием принципа единоначалия, регулярным планированием объемов и содержания горных и обеспечивающих работ, каждодневным контролем результатов на выходе.
Проблематика, возникающая в процессе деятельности предприятия, связанная с необходимостью улучшения его технико-экономических показателей.
В работе находятся 2 лавы, оборудованные современными механизированными комплексами в составе: 1-я лава №111 - очистной комбайн КДК500, скребковый конвейер СПЦ-230, мехкрепь 3КД90Т, 2-я лава №45 – очистной комбайн К800/3300, скребковый конвейер СПЦ-230, мехкрепь 2ОМТ01С. Расчетные возможности лав по объему суточной добычи угля составляют 200 тыс. т в мес. Фактическая добыча составляет 160-180 тыс. т в месяц. Главная причина – потери времени из-за простоев комплексов. Хронометражные наблюдения процессов в очистных забоях показали, что существенные потери времени в лавах имеют место в связи с незапланированными остановками в системе конвейерного транспорта горной массы, выдающего горную массу по конвейерным ходкам, конвейерным штрекам и наклонному стволу. Коэффициент машинного времени в лавах не превышает 0,72.
|
|
Схема транспорта шахты приведена на рис. 8.1.
Формулирование проблемы как различия между желаемым и существующим состоянием системы, обоснование цели, критерия, принуждающих связей.
Проблема – повысить эффективность очистных работ и в целом всей шахты.
Цель – обеспечить повышение устойчивой добычи из двух лав до максимально возможного уровня.
Критерий – максимально возможный суточный объем добычи за счет повышения коэффициента машинного времени
|
|
Принуждающие связи – сохранение горно-геологических и горно-технологических условий работы шахты, кадрового состава персонала, ограниченный объем инвестиций (задается конкретное значение) для реализации технических решений по повышению коэффициента машинного времени в лавах.
Рис. 8.1 Схема подземного транспорта шахты «Садкинская»: 1,2, 3, 4, 5, 6, 7, 8, 9, 10, 13, 14 – ленточные конвейеры; А, Б, В, Г – узлы слияния грузопотоков
Обоснование структуры и общей последовательности решения проблемы, включая составление имитационной модели и программы ее исследования.
Последовательность решения проблемы
1. Проведение хронометражных исследований формирования грузопотоков в очистных забоях.
2. Анализ результатов исследований и установление причин снижение объемов добычи в сравнении с максимально достижимыми.
3. Проведение исследования причин остановок конвейерных линий, их классификация и оценка возможности устранения причин.
4. Разработка альтернативных решений:
4.1 повышение надежности конвейерных линий от забоев до поверхности;
4.2 установка аккумулирующих емкостей на сопряжении конвейерных ходков и конвейерных штреков.
|
|
5. Оценка инвестиций на реализацию альтернативных решений и сроков окупаемости дополнительных финансовых вложений.
Для варианта 4.1:
– замена конвейерных лент;
– ревизия стыков конвейерных лент;
– установка устройств для предотвращения схода лент в сторону;
– увеличение продолжительности и содержания работ по профилактическому обслуживанию конвейерных линий, включая систему автоматического управления.
Для варианта 4.2:
– определение вместимости аккумулирующих бункеров, обеспечивающих повышение коэффициента машинного времени до 0,8, 0,85, 0,9;
– выбор конструкции и параметров скребковых бункер-конвейеров соответствующей вместимости;
– разработка конструктивно-технологической схемы установки бункер-конвейеров;
– разработка проекта установки бункер-конвейеров.
6. Выбор альтернативного варианта на основе имитационного моделирования:
– формирования случайного грузопотока в лавах;
– отказов в конвейерных линиях;
– процесса заполнения и разгрузки аккумулирующих бункеров;
– оценка достижимости максимального значения критерия.
7. Разработка порядка внедрения оптимального технического решения.
Дата добавления: 2019-02-22; просмотров: 226; Мы поможем в написании вашей работы! |
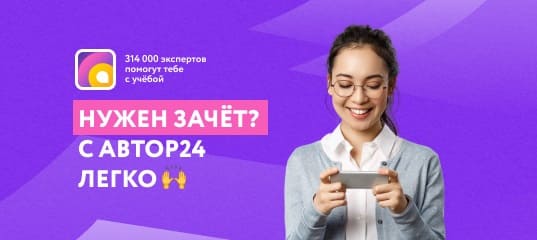
Мы поможем в написании ваших работ!