Определение типа производства
Глава 2
ОСНОВНЫЕ ПОЛОЖЕНИЯ И ПРИМЕРЫ ОФОРМЛЕНИЯ
РАЗЛИЧНЫХ РАЗДЕЛОВ
РАСЧЕТНО-ПОЯСНИТЕЛЬНОЙ ЗАПИСКИ
Определение типа производства
Тип производства по ГОСТ 3.1108-74 характеризуется коэффициентом закрепления операций , который показывает отношение всех различных технологических операций, выполняемых или подлежащих выполнению подразделением в течении месяца, к числу рабочих мест. Так как
отражает периодичность обслуживания рабочего всей необходимой информацией, а также снабжения рабочего места всеми необходимыми вещественными элементами производства, то
оценивается применительно к явочному числу рабочих подразделения из расчета на одну смену:
(2.1)
где – суммарное число различных операций;
– явочное число рабочих подразделения, выполняющих различные операции.
Согласно ГОСТ 14.004-74, принимаются следующие коэффициенты закрепления операций: для массового производства для крупносерийного производства
Практическое значение для массового производства может быть 0,1…1,0.
Коэффициент закрепления операций должен в производственных условиях определяться для планового периода, равного одному месяцу. Последнее обстоятельство учитывает условия серийного производства, для которого характерны большая номенклатура изделий и сравнительно частая смена объектов производства, что и определяется большими значениями коэффициента закрепления операций.
|
|
Для среднесерийного производства лежит в пределах 10 ÷ 20, для мелкосерийного – 20 ÷ 40.
Исходя из формулы (2.1) для коэффициента закрепления операций необходимо установить соотношение между трудоемкостью выполнения операций и производительностью рабочих мест (оборудования), предназначенных для проведения данного технологического процесса при условии загрузки этого оборудования в соответствии с нормативными коэффициентами.
При самостоятельной разработке студентом технологического процесса необходимо этот процесс расчленить на технологические операции
и переходы по обработке элементарных поверхностей, определить основное время выполнения каждого перехода и штучное или штучно-кальку-ляционное время для каждой операции. На данном этапе проектирования нормирование переходов и операций можно выполнить, пользуясь приближенными формулами.
Таблица 2.1
Приближенные формулы для определения норм времени
по обрабатываемой поверхности [4]
Вид обработки | Основное технологическое время То·10-3мин |
Черновая обточка за один проход | 0,17dl |
Чистовая обточка по 11-му квалитету | 0,1dl |
Чистовая обточка по 9-му квалитету | 0,17dl |
Черновая подрезка торца Ra 6,3, мкм | 0,037(D2- d2) |
Чистовая подрезка торца Ra 1,6 мкм | 0,052(D2- d2) |
Отрезание | 0,19D2 |
Черновое и чистовое обтачивание фасонным резцом | 0,63(D2- d2) |
Шлифование грубое по 11-му квалитету | 0,07dl |
Шлифование чистовое по 9-му квалитету | 0,1dl |
Окончание табл. 2.1
|
|
Вид обработки | Основное технологическое время То·10-3мин |
Шлифование чистовое 6-му квалитету | 0,15dl |
Растачивание отверстий на токарном станке | 0,18dl |
Сверление отверстий | 0,52dl |
Рассверливание d=20…60 | 0,31dl |
Зенкерование | 0,21dl |
Развертывание черновое | 0,43dl |
Развертывание чистовое | 0,86dl |
Внутреннее шлифование отверстий 9-го квалитета | 1,5dl |
Внутреннее шлифование отверстий 7-го квалитета | 1,8dl |
Черновое растачивание отверстий за один рабочий ход Ra 12,5 мкм | 0,2dl |
Черновое растачивание под развертку | 0,3dl |
Развертывание плавающей разверткой по 9-му квалитету | 0,27dl |
Развертывание плавающей разверткой по 7-му квалитету (Здесь d– диаметр; l – длина обрабатываемой поверхности; D – диаметр обрабатываемого торца; D - d – разность наибольшего и наименьшего диаметров обрабатываемого торца) | 0,52dl |
Протягивание отверстий и шпоночных канавок (l – длина протяжки, мм) | 0,4l |
Строгание черновое на продольно-строгальных станках | 0,065В l |
Строгание чистовое под шлифование или шабрение | 0,034В l |
Фрезерование черновое торцевой фрезой: за один рабочий ход чистовое | 6l 4l |
Фрезерование черновое цилиндрической фрезой | 7l |
Фрезерование шлицевых валов методом обкатки | 9lz |
Шлицешлифование (здесь l – длина шлицевого валика, мм; z – число шлицев) | 4,6lz |
Нарезание резьбы на валу (d= 32…120) | 19dl |
Нарезание метчиком резьбы в отверстиях (d= 10…24) (Здесь d – диаметр резьбы, мм; l – длина резьбы, мм) | 0,4dl |
Шлифование плоскостей торцом круга (Здесь В – ширина обрабатываемой поверхности, мм; l – длина обрабатываемой поверхности, мм) | 2,5l |
Фрезерование зубьев червячной фрезой (D=80…300) | 2,2Db |
Обработка зубьев червячных колес (D=100…400) (Здесь D – диаметр зубчатого колеса, мм; b – длина зуба, мм) | 60,3D |
В связи с тем, что проводятся пока ориентировочные расчеты, то можно принять для единичного производства:
|
|
(2.2)
для массового производства:
|
|
(2.3)
для серийного производства:
(2.4)
где – основное время, принимаемое по ориентировочным данным (табл. 2.1), мин;
– штучное время на обработку какой-либо поверхности, мин;
– штучно-калькуляционное время, мин.
В соответствии с выданным заданием, где указывается годовая программа изготовления деталей (N), и действительным годовым фондом времени работы оборудования, определяемым по табл. 2.2, определяем количество станков (mp) (2.5):
(2.5)
где N – годовая программа, шт.; – действительный годовой фонд времени, час;
– нормативный коэффициент загрузки оборудования.
Таблица 2.2
Годовые фонды времени работы оборудования
и рабочих мест (в две смены)
Оборудование | Номинальный годовой фонд Fн, ч | Потери Fн, % | Действитель-ный годовой фонд Fд,,ч |
Металлорежущие станки 1…30 категорий ремонтной сложности | 4154 | 3 | 4029 |
Металлорежущие станки свыше 30 категории ремонтной сложности | 4154 | 6 | 3904 |
Автоматические линии | 4154 | 10 | 3738 |
Поточные линии | 4154 | 4 | 3987 |
Рабочие места без оборудования (верстаки, столы) | 4154 | - | 4154 |
Средние значения нормативного коэффициента загрузки оборудования по отделению или участку цеха при двухсменной работе следует принимать: для мелкосерийного производства – 0,8…0,9; серийного – 0,75…0,85; массового и крупносерийного – 0,65…0,75.
Так как на данном этапе тип производства еще не известен, можно принять усредненные значения нормативных коэффициентов загрузки оборудования порядка 0,75…0,8. Это не приведет к большим погрешностям в расчетах, а фактические значения коэффициента загрузки оборудования будут определяться после детальной разработки технологического процесса.
После расчета по всем операциям значений ,
устанавливаем принятое число рабочих мест Р, округляя до ближайшего большего целого числа полученное значение
.
Далее по каждой операции вычисляем значение фактического коэффициента загрузки рабочего места по формуле и записываем эти значения в графы табл. 2.3.
Таблица 2.3
Определение типа производства
Операция | Тшт | mp | p | ![]() | О |
Коэффициент закрепления операций Производство [ ] |
Если операции оказывается выше нормативного, следует увеличить для данной операции количество станков. Если же на каких-то операциях
значительно ниже нормативного, следует проанализировать возможность дозагрузки рабочего места другими, примерно равноценными по трудоемкости, операциями. Тогда количество операций на данном рабочем месте может быть увеличено, а в графу О таблицы будет записано спроектированное значение.
Количество операций, выполняемых на рабочем месте, определяется по формуле
. (2.6)
После заполнения всех граф табл. 2.3 подсчитывают суммарные значения для О и Р, определяют и тип производства.
Пример. Рассчитать коэффициент закрепления операций для технологического процесса, состоящего из трех операций: протяжной, ; токарной,
; зубофрезерной
. Годовая программа, включая выпуск запасных частей, – 60 000 деталей.
Расчетное количество станков составит: для первой операции – 0,33; второй – 0,79; третьей – 2,65.
Принятое количество станков: для первой операции – 1, второй – 1, третьей – 3.
Фактический коэффициент загрузки оборудования: для первой операции – 0,33; второй – 0,79; третьей – 0,88.
Коэффициент закрепления операций
(2.7)
т. е. производство будет массовым.
Если в нашем примере все операции имели бы фактический коэффициент загрузки оборудования примерно 0,25, количество операций, которые могли бы выполняться на каждом рабочем месте, О=0,75/0,25=3 и коэффициент закрепления операций
(2.8)
Производство будет крупносерийным.
Действительный фонд времени работы оборудования на год (в часах) можно определить по следующим данным: календарное число дней – 365; количество выходных дней – 104; праздничных дней – 8; предпраздничных дней, сокращенных на 1 ч – 6; рабочих суббот – 1; число смен работы оборудования – 2; продолжительность рабочего дня – 8,2 ч; потерям времени на проведение ремонтов, обслуживания, настройки и подналадки оборудования (в процентах) П : Fд=[(365-104-8+1)8,2-6×1]2(1-П/100).
Номинальный и действительный фонды времени работы оборудования и рабочих мест на год приведены в табл. 2.2.
Расчет режимов резания
Общий порядок расчета режимов резания на большинстве
механических видов обработки
Для расчета режимов резания пользуемся источником [2].
1. Устанавливаем марку станка, на котором будет осуществляться планируемая операция механической обработки. В главе 1 [2] с. 5÷65 для этого станка определяем следующие паспортные значения:
– максимальное и минимальное число оборотов (nmax и nmin);
– количество чисел оборотов, которое дает коробка скоростей (Kn);
– максимальное и минимальное значение подач (Smax и Smin);
– число ступеней подач, которое дает коробка подач (KS);
– мощность электродвигателя привода главного движения (N).
2. По принятой или рассчитанной глубине резания определяем подачу. Здесь и далее необходимо пользоваться формулами и информацией, содержащимися в главе 4 «Режимы резания» [2]. Обычно подача задается
в таблицах главы 4 в пределах S1÷ S2. В этом интервале принимаем паспортное значение подачи – Sпасп.. Всех паспортных значений подачи для каждого конкретного типа станка в справочнике [2] нет, однако существует методика, по которой можно определить все паспортные значения подач для каждого станка. Она будет приведена после общего порядка расчета режимов резания.
3. Определяем расчетную скорость резания (Vрасч) (глава 4 [2]) по приведенным для каждого метода обработки формулам. Значения коэффициентов и показателей степени приводятся следом за формулой.
4. Определяем расчетное число оборотов
(2.9)
где D – диаметр инструмента или обрабатываемой поверхности, мм;
– расчетная скорость резания, м/мин.
5. Определяем паспортное значение числа оборотов по условию . Паспортных значений чисел оборотов для каждой конкретной модели станка в главе 1 [2] также нет. Методика определения паспортных значений подач и чисел оборотов одинакова и будет приведена далее. Паспортное значение числа оборотов может быть больше расчетного, но не более чем на 5 %.
6. Определяем фактическую скорость резания (V факт):
(2.10)
7. Определяем мощность, потребную на резание (N рез.). При точении, фрезеровании, разрезании необходимо пользоваться формулой
(2.11)
где – тангенциальная составляющая силы резания, Н;
– фактическая скорость резания, м/мин.
Сила также определяется по формулам, содержащимся в каждом разделе главы 4 [2], соответствующем методу обработки.
При сверлении, рассверливании, зенкеровании и развертывании для определения мощности, потребной на резание, необходимо пользоваться формулой:
(2.12)
где – крутящий момент, Н·м;
– паспортное число оборотов, об/мин.
Формулы для определения крутящего момента также приведены
в разделе главы 4 [2] для каждого метода обработки. Если выполняется условие , где η- кпд передачи (0,85-0,95), то расчетные режимы резания принимаются.
Методика определения паспортных значений подач
и числа оборотов для конкретной модели станка
В отечественном станкостроении значения подач и чисел оборотов, формируемых в коробках подач и коробках скоростей, определяются с помощью нормализованных значений показателей ряда φ по следующей методике:
(2.12)
где – знаменатель ряда подач для коробки подач;
(2.13)
где – знаменатель ряда чисел оборотов для коробки скоростей;
В связи с этим для каждой модели станка можно определить значения стандартных показателей φ как для коробки подач, так и для коробки скоростей (эти значения не всегда одинаковы для одного станка) по следующей формуле (2.14):
(2.14)
Стандартных значений φ семь: 1,06; 1,12; 1,26; 1,41; 1,58; 1,78; 2,00 [8].
Пример. Определить паспортное число оборотов токарно-винто-резного станка 16К20, если известно [2] nmax=1600 об/мин; nmin=12,5 об/мин; К n=22. Определяем значение знаменателя φn:
(2.15)
Определяем паспортные числа оборотов станка 16К20
(2.16)
Значения нормализованных знаменателей рядов φ, возведенных в степень, приведены в табл. 2.4 и взяты из [4].
Примеры расчетов режимов резания при различных методах обработки.
Пример 1. Точение. Требуется провести черновое обтачивание вала из стали 45, заготовка – прокат Ø45 мм, глубина резания t =1,5 мм. Выбрать оборудование, режущий инструмент и назначить режим обработки.
Решение
1. Выбираем оборудование. По табл. 9 с. 15 [2] принимаем токарно-винторезный станок модели 16К20, поскольку наибольший диаметр прутка, проходящий через отверстие шпинделя этого станка, равен 53мм, поэтому заготовка из задания проходит через отверстие. По этой же таблице принимаем паспортные данные станка 16К20: nmin=12,5 об/мин; nmax=1600 об/мин; Число скоростей шпинделя К n=22; Smin=0,05 мм/об; Smax=2,8 мм/об; число ступеней подач KS=24; мощность электродвигателя главного привода N эл=11 кВт.
2. Выбираем режущий инструмент из следующих соображений.
В большинстве случаев при токарной обработке заготовок из чугуна используются однокарбидные твердые сплавы, имеющие в своем составе карбид вольфрама и чистый кобальт и имеющие обозначение ВК-10, ВК-10(ОМ), ВК8, ВК6, ВК4. Буквы и цифры означают следующее: В – карбид вольфрама (Термин «вольфрам» родился в 16 веке от двух немецких слов: вольф – волк, фрам – сливки. Он родился в связи с тем, что мешал выплавке олова, переводя его в шлак); К – кобальт; ОМ – особо мелкозернистая структура.
Цифры показывают процентное содержание кобальта в составе твердого сплава. Например: ВК8 – кобальт – 8 %, карбид вольфрама – 92 %.
Кобальт в составе твердого сплава выступает в качестве связки между зернами карбидов, входящих в состав и имеющих наряду с высокой твердостью низкую ударную прочность. Поскольку черновые виды точения и фрезерование торцевыми фрезами испытывают большие ударные нагрузки из-за неравномерности припуска, ведения процесса обработки на больших глубинах резания и подач, то необходимо применять твердые сплавы с большим количеством кобальта, который как бы демпфирует, ослабляет воздействие ударных нагрузок на зерна карбидов, тем самым предохраняя их от разрушения.
Таблица 2.4
Значения нормализованных знаменателей рядов φ, возведенных в степень
φ | 1,06 | 1,12 | 1,26 | 1,41 | 1,58 | 1,78 | 2,00 |
φ 2 φ 3 φ 4 φ 5 φ 6 φ 7 φ 8 φ 9 φ 10 φ 11 φ 12 φ 13 φ 14 φ 15 φ 16 φ 17 φ 18 φ 19 φ 20 φ 21 φ 22 φ 23 φ 24 φ 25 φ 26 φ 27 φ 28 φ 29 φ 30 φ 31 φ 32 φ 33 φ 34 φ 35 φ 36 φ 37 φ 38 φ 39 φ 40 φ 41 φ 42 φ 43 φ 44 φ 45 φ 46 φ 47 φ 48 φ 49 φ 50 | 1,12 1,19 1,26 1,34 1,41 1,49 1,58 1,67 1,78 1,89 2,00 2,12 2,24 2,36 2,50 2,65 2,81 2,98 3,16 3,35 3,55 3,77 4,00 4,24 4,48 4,75 5,04 5,34 5,64 5,98 6,32 6,70 7,12 7,55 8,00 8,48 8,96 9,50 10,08 10,68 11,28 11,96 12,64 13,40 14,24 15,09 16,00 16,96 17,92 | 1,26 1,41 1,58 1,78 2,00 2,24 2,50 2,81 3,16 3,55 4,00 4,48 5,04 5,64 6,32 7,12 8,00 8,96 10,08 11,28 12,64 14,24 16,00 17,92 20,16 22,56 25,28 28,48 32,00 35,84 40,00 44,96 50,56 56,80 64,00 | 1,58 2,00 2,50 3,16 4,00 5,04 6,32 8,00 10,08 12,64 16,00 20,16 25,28 32,00 40,00 50,65 64,00 80,64 101,61 | 2,00 2,82 4,00 5,64 8,00 11,28 16,00 22,56 32,00 45,12 64,00 | 2,50 4,00 6,32 10,08 16,00 25,28 40,00 64,00 | 3,16 5,64 10,08 17,92 32,00 56,80 | 4,00 8,00 16.00 32,00 64,00 |
Для обработки стальных заготовок используют двух- и трехкарбидные твердые сплавы. В двухкарбидные твердые сплавы входят карбид вольфрама, карбид титана и кобальт. Наиболее распространенными являются марки: Т5К10, Т15К6, Т30К4. Буква Т обозначает карбид титана, стоящие за ней цифры – процентное содержание карбида титана в составе твердого сплава, буква К и стоящие за ней цифры обозначают кобальт
и его процентное содержание.
Например: Т5К10 – карбид титана (TiC) – 5 %, кобальта – 10 %, карбида вольфрама (WC) – 85 %.
Трехкарбидные твердые сплавы имеют в своем составе еще и карбид тантала (ТаС) и поэтому их обозначение может быть следующим: ТТ7К12, ТТ8К6, ТТ20К9 и др. Две первые буквы Т означают карбид титана и карбид тантала, цифры после них означают их суммарное процентное содержание в твердом сплаве. Буква К и следующие за ней цифры означают кобальт и его процентное содержание. Количество карбида вольфрама, как
и в случае одно- и двухкарбидных твердых сплавов не указывается и определяется как остальное вычитанием из 100 содержания кобальта, карбидов титана и тантала.
Например. Марка твердого сплава ТТ7К12 расшифровывается следующим образом: ТТ – карбид титана и карбида тантала, 7 - их совместное процентное содержание в составе твердого сплава, К12 – 12 % кобальта
и 81 % карбида вольфрама.
Для того, чтобы правильно выбрать марку твердого сплава для различных видов механической обработки (черновое, получистовое, чистовое, тонкое точение, растачивание, фрезерование и др.) необходимо знать следующее.
На последующих этапах обработки, когда припуск на обработку становится равномерным и можно увеличить скорость резания, применяют твердые сплавы с уменьшенным содержанием кобальта и повышенным содержанием карбидов.
Например. Черновое обтачивание стали – Т5К10, ТТ7К12, чистовое обтачивание стали – Т15К6, тонкое обтачивание стали – Т30К4.
Более подробную информацию о применимости различных марок твердого сплава можно найти в [9, 42].
В зависимости от обрабатываемого материала и характера образующейся стружки ТС подразделяются на 6 групп по областям применения: Р, М, К, N, S и Н (табл. 2.5) [42].
Группы резания подразделяются в свою очередь на группы применения, которые обозначаются буквой (группа резания) и числовым индексом (группа применения). Чем выше число индекса в обозначении группы применения, тем ниже износостойкость твердого сплава и допускаемые скорость резания и толщина среза (подача и глубина резания).
Таблица 2.5
Группы резания твердых сплавов
Группа (цвет маркировки) | Область применения |
Р (синий) | Обработка материалов, дающих сливную стружку (в основном стали) |
М (желтый) | Обработка материалов, дающих как сливную стружку, так и стружку скалывания (коррозионно-стойкие стали и сплавы) |
К (красный) | Обработка чугунов, дающих стружку скалывания |
N (зеленый) | Обработка алюминиевых и медных сплавов |
S (коричневый) | Обработка труднообрабатываемых материалов (жаропрочные стали и сплавы, титан и его сплавы) |
Н (серый) | Обработка закаленных и литейных чугунов |
Инструменты, оснащенные ТС, широко применяются при точении и фрезеровании, а также при сверлении, зенкеровании, развертывании и протягивании чугунных деталей.
Применение твердосплавных инструментов эффективно при следующих условиях:
– достаточный уровень мощности, жесткости, виброустойчивости станков. Этим условиям в основном отвечают станки токарной и фрезерной групп и обрабатывающие центры на их базе;
– конфигурация детали и технологическое оснащение должны
допускать обработку с уровнем скорости резания, характерным для ТС;
– наличие особых требований к производительности обработки.
Крупные производители создают два класса твердых сплавов:
– специализированные марки для определенного обрабатываемого материала и типа операций (черновая, чистовая), которые обеспечивают наивысшую производительность при максимальной скорости.
– универсальные марки для обработки различных материалов и типов операций, которые во всех допускаемых случаях обеспечивают необходимую производительность и стойкость.
Для массового или крупносерийного производства характерно применение специализированных марок твердого сплава. Однако большая номенклатура специализированных марок приводит к увеличению затрат на хранение и обслуживание с приростом вероятности ошибок при замене.
При обработке часто сменяемых малых партий детали из различных материалов используют универсальные марки твердых сплавов. В этом случае сокращаются затраты на переналадку станков, на хранение и обслуживание инструмента. Однако, производительность и стойкость универсальных марок ниже на 10...25 %, чем специализированных марок.
С учетом вышесказанного крупные производители стремятся создать сплавы, максимально сочетающие преимущества универсальных и специализированных марок.
На сегодня в производстве твердосплавного инструмента в России сохраняется специализация марок для узкой области применения. Основными изготовителями российских марок ТС являются ОАО «Кировград-ский завод твердых сплавов» (КЗТС), ГУП «Всероссийский научно-исследовательский и проектный институт тугоплавких металлов и твердых сплавов» (ВНИИТС) и ОАО «Московский комбинат твердых сплавов» (Сандвик-МКТС) (табл. 2.6)
Рекомендации по применению марки ТС всегда являются ориентировочными и применительно к конкретным операциям требуют уточнений. Например, невысокая жесткость технологической системы может явиться причиной применения более прочных ТС. С другой стороны, если заданная производительность чистовой обработки обеспечивается применением ТС для черновой обработки, то это предпочтительно, так как обеспечивает повышенную надежность. Ниже, на примере группы резания Р, даны основные рекомендации по применению марок твердых сплавов производства КЗТС.
Группа Р01 предназначена для тонкого точения стальных деталей Основная марка – Т30К4.
Группа Р10 предназначена для чистовой обработки (за исключением операций тонкого точения). Основная марка – Tl 5К6.
Группа Р20 предназначена для получерновой обработки, рекомендуется также для черновой обработки при благоприятных условиях резания; применяется для чистого точения – в том случае, когда прочность сплава Т15К6 недостаточна. Основная марка – Т14К8. Улучшение условий теплоотвода от режущих кромок за счет уменьшения угла в плане и эффективного применения СОЖ повышает уровень критического порога режима резания и позволяет использовать повышенную износостойкость.
Группа Р25 включает твердые сплавы, обладающие повышенным сопротивлением циклическим, динамическим и тепловым нагрузкам при прерывистом резании, в частности при фрезеровании. Основная марка – ТТ20К9.
Таблица 2.6
Дата добавления: 2019-02-12; просмотров: 349; Мы поможем в написании вашей работы! |
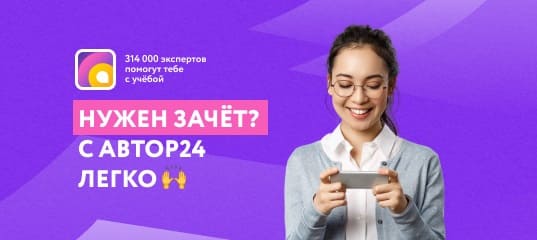
Мы поможем в написании ваших работ!