Выбор и описание режущего инструмента
При выборе режущего инструмента необходимо стремиться применить стандартный инструмент, но, иногда целесообразно, следует применять специальный, комбинированный, фасонный инструмент, позволяющий совмещать обработку нескольких поверхностей. Правильный выбор режущей части инструмента имеет большое значение для повышения производительности и снижения себестоимости обработки. Для обработки стали рекомендуется применять инструмент, режущая часть которого изготовлена из титановольфрамовых твёрдых сплавов (Т5К10, Т14К8, Т15К6, Т15К6Т, Т30К4), быстрорежущих инструментальных сталей (Р18, Р9, Р9Ф4, Р14Ф4), вольфрамовых твёрдых сплавов (ВК2, ВК3М, ВК4, ВК8) и др.
Для обработки чугуна и цветных металлов, и неметаллических материалов используют инструмент из вольфрамовых твёрдых сплавов. Выбор материала для режущего инструмента зависит от формы и размеров инструмента, материала обрабатываемой заготовки, режимов резания и типа производства.
Режущий инструмент необходимо выбирать по соответствующим стан-дартам и справочной литературе в зависимости от методов обработки деталей. Если технологические особенности детали не ограничивают применения высоких скоростей резания, то следует применять высокопроизводительные конструкции режущего инструмента, оснащенные твёрдым сплавом, т.к это экономически выгодней, чем применение быстрорежущих инструментов. Особенно это распространяется на резцы (кроме фасонных, малой ширины, автоматных), фрезы, зенкеры, конструкции которых оснащены твёрдым сплавом, хорошо обработаны.
|
|
В пояснительной записке необходимо дать анализ выбранному режущему инструменту на одну операцию или переход.
В операционных картах технологического процесса обработки детали необходимо правильно указывать условные обозначения режущего и вспомогательного инструмента в соответствии с присвоенным ему стандарте обозначением, например:
сверло с коническим хвостовиком диаметром 20 мм с конусом Морзе 2:
– сверло 20 ГОСТ 2092-77;
сверло диаметром 6 мм, общего назначения, правого исполнения I из твёрдого сплава ВК8;
– сверло 2309-0067 ВК8 ГОСТ 17875-71;
фреза цилиндрическая тип I диаметром D=80 мм, длиной L=125мм, правая;
– фреза 2200-0157 ГОСТ 3752-71.
Выбор и описание измерительных средств
При проектировании технологического процесса механической обработки заготовки для межоперационного и окончательного контроля обрабатываемых поверхностей необходимо использовать стандартный измерительный инструмент, учитывая тип производства, но вместе с тем, когда целесообразно, следует применять специальный контрольно- измерительный инструмент или контрольно-измерительные приспособления.
|
|
Метод контроля должен способствовать повышению производительности труда контролёра и станочника, создавать условия для улучшения качества выпускаемой продукции и снижение её себестоимости. В единичном и серийном производстве обычно применяется универсальный измерительный инструмент (штангенциркуль, штангенглубиномер, микрометр, угломер, индикатор и т.д).
В массовом и крупносерийном производстве рекомендуется применять предельные калибры (скобы, пробки, шаблоны и т.д) и методы активного контроля.
В операционную карту технического контроля необходимо записывать условные обозначения измерительного инструмента в соответствии с присвоенным ему стандартным обозначением, например:
– условное обозначение скобы для контроля длины с полем допуска по Н6:
скоба 8102-0030Н6 ГОСТ 18355-73.
– приёмной скобы П-ПР: скоба 8102-0030Н6-П-ПР ГОСТ 18355-73.
Выбор режимов резания
При определении режимов резания статическим (табличным) методом пользуют нормативные таблицы в зависимости от выбранного типа производства и установленного вида обработки заготовки. Табличный метод широко применяют в производственных условиях, т.к этот метод даёт возможность ускорить разработку технологического процесса и сократить сроки подготовки к запуску изготовления данного изделия. В курсовом проекте расчет режимов резания выполнить на одну технологическую операцию.
|
|
Определение режимов резания выполняют в следующей последовательности:
1) Устанавливают глубину резания на обрабатываемую поверхность. При черновой обработке следует назначать наибольшую глубину резания, равную всему межоперационному припуску на обработку, если это позволяют жёсткость крепления заготовки режущего инструмента, а также жёсткости станка и мощности выбранного станка.
Глубина резания при сверлении составляет t = 0,5D, при рассверливании, зенкеровании, развёртывании и растачивании t = 0,5(D-d),
где d и D – диаметры до обработки и после её.
2) Устанавливают подачи станка исходя из прочности державки пластинки из твёрдого сплава, жёсткости станка и характера установки заготовки. При чистовой обработке поверхности детали величина подачи зависит от технологических факторов (точности и качества обработки поверхности).
Для резцов с пластинками из твёрдого сплава выбранную подачу необходимо согласовать по прочности пластинки по табличным нормативам.
|
|
3) Определяют скорость резания. Скорость резания устанавливается по табличным нормативам для определённых условий работы, и если конкретные условия отличаются от данных таблицы, тогда скорость резания, взятая из таблицы, умножается на поправочные коэффициенты. После установления скорости резания по табличным нормативам определяют частоту вращения шпинделя станка и уточняют её по паспорту станка. Обычно принимают ближайшее меньшее значение станка, однако допускается принимать ближайшее большее число частоты вращения шпинделя станка, если оно превышает не более, чем на 10 % по паспорту станка. После установления частоты вращения шпинделя по паспорту станка определяют действительную скорость резания.
4) Проверяют режимы резания по мощности станка. Потребная мощность для резания, взятая из нормировочных таблиц, не должна превышать фактической мощности электродвигателя станка. При недостаточной мощности привода станка рекомендуется уменьшать скорость резания, а не подачу или глубину резания, т.к одинаковое изменение указанных параметров, обеспечит больше повышение стойкости режущего инструмента.
Определение вспомогательного времени:
Вспомогательное время Тв состоит из времени на установку и снятие детали; времени, связанного с переходом (установки инструмента по лимбу, разметке; предварительного промера; взятия пробной стружки и др); времени, связанного с переходом на приёмы не вошедшие в комплексы (изменения частоты вращения шпинделя станка, изменения подачи, поворота резцовой головки и др.); вспомогательного времени на контрольные измерения, которые устанавливают по нормативным таблицам в зависимости от точности измерения; размеров измерительных поверхностей с учётом коэффициента периодичности.
Вспомогательное время на технологическую операцию:
Тв=(Туст+ԐТпер+ ԐТпер.к+ ԐТизм).Кtв , | (1) |
где Туст – вспомогательное время на установку и снятие детали, мин; |
Тпер – вспомогательное время, связанное с переходом, мин;
Тпер.к– вспомогательное время, связанное с переходом на приёмы, не во-шедшие в комплексы, мин;
Тизм– вспомогательное время на контрольные измерения, мин;
Кtв– поправочный коэффициент на вспомогательное время в зависимости от размера партии обрабатываемых изделий (по таблицам).
Время на техническое обслуживание рабочего места, затрачиваемое на установку, снятие и замену затупившихся режущих инструментов, на заправку шлифовальных кругов, смазывание и подналадку станка, уборку стружки в процессе работы и т.д.
Тт.о=(То+Тв).(ат.о /100), | (2) |
где ат.о- время на техническое обслуживание рабочего места в % к оператив-ному времени, которое выбирается по нормативным таблицам в зависимости от типа производства.
Время на отдых и физические надобности | |
Топ= (То+Тв) . (ао.п /100), | (3) |
где ао.п- время на отдых физические потребности (в %) к оперативному вре-мени, которое выбирают по нормативным таблицам.
В серийном и единичном производстве за техническую норму времени принимается штучно- калькуляционное время
Тш.к=Тш+(Тп.з /nД), | (4) |
где Тп.з – подготовительно- заключительное время, затрачиваемое на подго-товку и наладку станка для обработки данной партии деталей, получение необходимой технологической оснастки, документации, а также на сдачу обработанных деталей, документации и оснастки;
nД – число обрабатываемых деталей в партии.
Дата добавления: 2019-01-14; просмотров: 208; Мы поможем в написании вашей работы! |
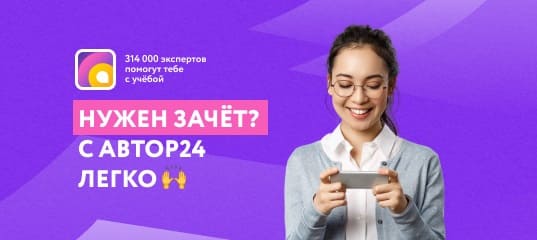
Мы поможем в написании ваших работ!