Мощность машин и её преобразование в механизмах 5 страница
Характер нагружения
КР.О.-коэффициент
нагружения
рабочего органа
Вид средств механизации
Легкие
Формовочная земля, уголь дробленый,
неабразивные сыпучие грузы: зерно, плоды и др.
Малая пульсация подаваемого материала
с умеренной температурой окружающей среды
1,0…1,2
Ленточные и пластинчатые конвейеры
с малой скоростью перемещения
Средние
Руды, горные породы, кусковые материалы
до 150 мм, штучные грузы 30…100 кг.
Средняя пульсация подаваемого материала,
небольшие толчки
1,2…1,4
Конвейеры скребковые, ленточные, цепные,
пластинчатые, люлечные, тележечные и подъемники
Тяжелые
Руды, горные породы до 350 мм, штучные грузы
массой до 500 кг.
Большая пульсация подаваемого материала,
толчки средней силы
1,4…1,6
Эскалаторы, подъемники для бревен,
пластинчатые, грузотолкающие конвейеры
Весьма тяжелые
Горные породы размером 500 мм, доломит,
бревна диаметром до 900 мм, штучные
тяжелые грузы до 1 т.
Толчки большой силы, опережающие удары,
большая пульсация подаваемого материала
1,6…1,8
Ковшовые цепные элеваторы, цепные
подъемники, грузотолкающие конвейеры
Момент при перегрузке по рекомендациям ВНИИПТмаш берется ниже следующих пределов:
Тпик=Кпер ∙Тном ,
|
|
здесь Кпер-1,1- коэффициент перегрузки для механизма подъема;
Коэффициент перегрузки для механизма передвижения и поворота в зависимости от типа электродвигателя:
- крановый короткозамкнутый – 3,0
- крановый постоянного тока или переменного тока с контактным кольцом– 2,5
- асинхронный двигатель общепромышленного назначения – 1,75
Формула приводимая профессором Снесаревым Г.А. для определения эквивалентной нагрузки имеет вид
THE=KНД∙Tmax=KG∙KT∙Tmax
здесь - коэффициент долговечности.
Как видим, предлагаемое выражение совпадает с методикой ВНИИПТмаш при коэффициенте тренировки равным единице. Механизмы грузоподъемных машин работают в повторно-кратковременном режиме, где продолжительность цикла не превышает 600 °С, поэтому расчеты стандарта ISO 6336-86 и ГОСТ 21354-87 существенно отличаются от предложенной методики Снесарева Г.А.
Кратковременные перегрузки, не учтенные при расчете на усталость деталей машин, могут привести к потере их статической прочности, поэтому необходимо проверить на статическую прочность при перегрузках.
Коэффициент внешней динамической нагрузки при перегрузках приведен в таблице 10. Пиковая нагрузка определяется по выражению
|
|
Тпик=Кпер∙Тном=KAS∙Тном
Выводы и рекомендации
Для расчета машин непрерывного действия при определении эквивалентной нагрузки на выносливость рекомендуется метод расчета Решетова Д.Н. и Винтера Х.
К определению коэффициента внешней динамики конкретной машины необходим дифференцированный подход с учетом конструктивной особенности и условий эксплуатации.
Точный график нагружения любой машины может быть определен только на основе длительного экспериментального исследования в условиях эксплуатации, но на этапе проектирования важен правильный выбор возможного графика нагружения.
Таблица 10. Коэффициент внешней динамической нагрузки при расчетах
на статическую прочность от максимальной нагрузки КAS.
Вид рабочей машины и условия их эксплуатации
КAS
Примечание
Турбина-генератор при коротком замыкании
до 6
Перегрузка может быть уменьшена при помощи предохранительной муфты
Приводы с асинхронными электродвигателями при пуске
2,5 ... 5
Перегрузка может быть уменьшена путем рационального
|
|
конструирования колебательной системы привода
Главные приводы металлорежущих станков с электродвигателями
асинхронными или постоянного тока
1,8...4
Большие значения при неблагоприятных сочетаниях
конструктивных и технологических параметров
Лебедки, строгальные и долбежные станки, скребковые конвейеры,
фрикционные прессы
1,5...2,2
У ленточных и пластинчатых конвейеров перегрузки несколько меньше
Грузоподъемные машины: механизмы подъема,
механизмы передвижения
1,2...2
1,5...4
Большие значения при подъеме груза с подхватом
Пилы для резки металла, ножницы, мясорезательные машины
1,8...2,5
--
Вентиляторы, воздуходувки
1,4...1,8
--
Трансмиссии машин
1,4...2,5
Меньшие значения у легковых автомобилей
Электрический транспорт
1,6...2,5
--
Вагоноопрокидыватели
1,8...5
--
Мельницы, глиномялки, смесители вязких масс
1,8...2,2
--
Камнедробилки
2,0...3,5
--
Кривошипные и эксцентриковые механизмы
1,8...3,0
--
Прокатные станы (удары при захвате)
2,5...4,5
--
Примечание: При наличии устройства для плавного пуска табличные значения следует уменьшить на 20 – 30%.
|
|
Вопросы для самопроверки
- Что следует понимать под циклом переменных напряжении? Характеристики цикла и соотношения между ними.
- Какой из циклов самый неблагоприятный для работы детали?
- Что называет усталостным разрушением и каковы его причины?
- Что называют пределом выносливости?
- Что такое концентрация напряжений и что ее вызывает?
- Как определяют общий расчетный коэффициент запаса прочности при переменных напряжениях?
- При каких обстоятельствах и где действуют контактные напряжения? По какой формуле определяют их наибольшее значение при начальном контакте по линии?
- В чем сущность усталостного выкрашивания хорошо смазываемых контактирующих под нагрузкой рабочих поверхностей? Как повысить сопротивляемость поверхностей выкрашиванию?
- Как определить число циклов за время работы детали?
- Стальные детали работают на изгиб по одинаковым циклам: одна на пределе выносливости, другая — при меньших напряжениях. Что можно сказать о долговечности этих деталей?
- Какие бывают концентраторы напряжений и как они влияют на выносливость детали?
Раздел 3. Краткие сведения о машиностроительных материалах и основах их выбора
Содержание
Требования к материалам
Основные машиностроительные материалы
Железо и сплавы на его основе
Стали
Чугуны
Цветные металлы
Медь и сплавы на ее основе
Титановые сплавы
Магниевые сплавы
Вольфрамовые сплавы
Магнитно-твердые сплавы
Магнитно-мягкие сплавы
Алюминий и сплавы на его основе
Термическая и термохимическая обработка металлических материалов
Требования к термообрабатываемым деталям
Термическая обработка сварных конструкций
Композиционные материалы
Неметаллические материалы
Керамика
Пластмассы (пластические массы)
Резина
Смазочные материалы
Классификация смазок и их применение
Антифрикционные смазки
Многоцелевые смазки
Термостойкие смазки
Морозостойкие смазки
Химически стойкие смазки
Редукторные смазки (полужидкие)
Приработочные пасты
Узкоспециализированные (отраслевые) смазки
Клеи и клеящие вещества
Другие материалы
Покрытия
Коррозия металлов
Гальванические покрытия
Лакокрасочные покрытия
Обозначение условий эксплуатации
Обозначение покрытий
Требования к материалам
Ресурсосбережение в промышленности подразумевает повышение мощности выпускаемых машин, качества, надежности, экономичности, конкурентоспособности и производительности оборудования и других изделий машиностроения. При этом предполагается уменьшение их габаритов, металлоёмкости, энергопотребления и снижение их себестоимости. Для этого должен быть решен вопрос о расширении и систематическом обновлении номенклатуры и ассортимента конструкционных материалов, внедрении высокоэффективных методов повышения их прочностных свойств; коррозионно- и износостойкости; об увеличении производства новых композитных конструкционных материалов; изделий на основе порошковой металлургии, порошков-сплавов, заменяющих черные и цветные металлы; широком применении малооперационной и безотходной технологии, а также прогрессивной технологии обработки, как электронно-лучевой, лазерной, электроэрозионной, плазменно-механической.
При выборе материала прежде всего учитывают эксплуатационные, технологические и экономические требования, предъявляемые к детали.
Эксплуатационные требования к материалу определяются условиями работы детали в механизме. Для выполнения этих требований учитываются следующие свойства материала: прочность – способность материала сопротивляться разрушению или появлению остаточных деформаций, характеризуется пределом прочности σu, пределом текучести σy, условным пределом текучести σ0,2, пределом выносливости σR, твердостью по Бринеллю НВ или Роквеллу HRCэ; износостойкость – способность материала сопротивляться износу, характеризуется твердостью НВ, HRCэ или допустимым удельным давлением qadm; жесткость – способность материала сопротивляться упругим деформациям, характеризуется при растяжении (сжатии) и изгибе модулем упругости Е, при кручении – модулем упругости G; упругость характеризуется пределом упругости σe и модулем упругости Е; антифрикционность характеризуется коэффициентом трения скольжения f; плотность; удельные характеристики – характеристики, приходящиеся на единицу массы; электропроводность, теплопроводность, коррозионная стойкость, жаропрочность и др.
Технологические требования к материалу определяют возможность изготовления деталей с минимальными трудозатратами. При изготовлении деталей методами обработки давлением (штамповка, прессование и т.д.) учитывают пластичность – свойство материала получать без разрушения значительные остаточные деформации; при изготовлении литьем учитывают легкоплавкость и жидкотекучесть – заполняемость без пустот узких полостей различных форм; при изготовлении методами механической обработки учитывают обрабатываемость резанием. К технологическим требованиям относят также термообрабатываемость – способность материала изменять механические свойства при термической (закалка, отпуск, отжиг) и термохимической (цементация, азотирование и т.д.) обработках и свариваемость – способность материала образовывать прочные соединения при сварке.
Экономические требования к материалу определяются его стоимостью и дефицитностью. Более веским экономическим требованием является себестоимость детали, которая включает как стоимость материала, так и производственные затраты на ее изготовление. Производственные затраты в значительной мере зависят от технологического процесса изготовления детали. Например, при массовом и крупносерийном производствах дешевле изготавливать детали штамповкой, прессованием, с помощью литья, а при единичном или мелкосерийном производстве эти технологии из-за большой стоимости оснастки (штампы, пресс-формы, литейные формы) очень дороги, здесь выгоднее применять детали, полученные с помощью механической обработки. Выбор технологии изготовления детали влияет и на выбор материала.
Стоимость материалов, из которых изготовляют машину, составляет 30...60% полной стоимости машины. Экономию на стоимости материалов можно получить как путем уменьшения количества потребного материала на машину, так и путем замены дорогостоящего материала более дешевым. Но не всегда дешевый материал оказывается выгоднее более дорогого. Например, чтобы изготовить небольшую шестерню из чугуна, необходимо сначала сделать модель, отформовать ее, залить чугуном и обточить полученную отливку; скорее, проще и дешевле будет отрезать диск нужной толщины от круглой стальной заготовки соответствующего диаметра и для получения шестерни обработать его на станке.
При применении литья необходимо иметь в виду, что если принять стоимость 1 т отливок из серого чугуна равной единице, то для стоимости различного вида литья ориентировочно принимают следующее соотношение: серый чугун — 1, стальное литье — 2, ковкий чугун — 2 и бронзовое литье — 8.
При проектировании деталей зубчатых передач наиболее ответственный момент в решении - правильный выбор материала для сопряженной пары зубчатых колес. В практике машиностроения зубчатые колеса для силовых передач, как правило, изготовляют из углеродистых и легированных сталей различных марок. Зубчатые колеса из чугуна находят применение только в слабонагруженных малоответственных передачах. Зубчатые колеса из цветных металлов (из бронзы) применяют главным образом при изготовлении червячных колес и в основной комбинированной конструкции: зубчатый венец изготовляют из бронзы, ступицу — из чугуна и стали. Пластмассы также применяются относительно редко и главным образом для передач, работающих в агрессивных средах. Зубчатые колеса из углеродистых конструкционных сталей применяют в менее ответственных случаях, а из легированных сталей - в средненагруженных и тяжело нагруженных передачах, работающих с большими динамическими и ударными нагрузками. Следует заметить, что зубчатые колеса из углеродистых сталей, подвергнутых только нормализации и некоторому улучшению, обладают обычно невысокой контактной прочностью. Поэтому такие колеса используют лишь в единичном и мелкосерийном производстве. Высокую нагрузочную способность имеют зубчатые колеса с твердой поверхностью зубьев и вязкой их сердцевиной. Такими они получаются при изготовлении из углеродистых или легированных сталей после проведения соответствующей термической обработки, связанной с цементацией, азотированием или цианированием, и поверхностной закалкой зубьев. При объемной закалке зубья будут обладать пониженной вязкостью сердцевины, а потому плохо сопротивляться ударным нагрузкам.
Из технологических и экономических соображений колеса малых и средних размеров выполняют из поковок или проката. Колеса диаметром более 500 мм рекомендуется изготовлять из стального литья (35Л, 40Л, 50Л), применяя их в паре с кованой шестерней. Назначая материал, нужно стремиться получить одинаковую прочность зубьев шестерни и колеса. Зубья шестерни обычно имеют меньшее значение коэффициента формы зуба и работают в передаточное число раз интенсивнее, чем зубья колеса передачи. Поэтому для шестерни необходимо назначать материал с более высокими механическими характеристиками, твердость материала на поверхности зубьев шестерне рекомендуется принимать на 20...50 единиц НВ выше твердости поверхности зубьев колеса.
Выбирая тип заготовки и материал для изготовления деталей специалист должен идти по пути наименьших затрат на изготовление машины и отчётливо представлять технологический процесс её изготовления. Если, например, закладывается поверхностная термическая или химикотермическая обработка зубьев шестерни, то на предприятии-изготовителе должно быть оборудование для выполнения данной обработки (печь ТВЧ или печь газового азотирования …), а также оборудование для шлифовки зубьев после закалки (зубошлифовальный станок). Это значительно удорожает процесс изготовления и, достигаемое уменьшение габаритов машины может оказаться несоизмеримым с произведенными затратами. Исходя из того, что по чертежам студента предполагается разовое изготовление машины, рекомендуется на начальном этапе проектирования выбирать для изготовления зубчатых передач и валов рядовые конструкционные стали (35; 45; 50) или малолегированные стали (40Х; 40ХН; 35ХМ;…..) и вводить щадящую термообработку (улучшение НВ 210-230 или НВ 260- 290). Зуборезный инструмент как правило изготавливается из быстрорежущей стали и способен обрабатывать стали с твёрдостью до НВ 300. Рамы под приводы рекомендуется выполнять в сварном варианте из стандартных профилей проката марки стали Ст3., которые обладают хорошей свариваемостью. Желательно и корпус редуктора выполнить в сварном варианте, но это потребует больших затрат времени на разработку чертежа и нужно не забыть ввести в требования чертежа пункт: «отпуск после сварки» - иначе после механической обработки размеры корпуса могут измениться из-за поводок от термических напряжений сварки.
При проектировании червячных передач трудно обойтись без использования бронзовых отливок для изготовления венцов червячных колёс, но и здесь желательно по возможности использовать стандартный прокат из цветных металлов.
В последние годы получено вязкое состояние совершенно хрупких тел. Материалом такого типа является гексанит Р, который намного превосходит карбидно-вольфрамовые твердые сплавы.
Широкое применение в машинах нашли пластмассы, которые изготовляются без снятия стружки, где в 5 раз меньше трудоёмкость изготовления и количество отходов.
Дата добавления: 2019-01-14; просмотров: 256; Мы поможем в написании вашей работы! |
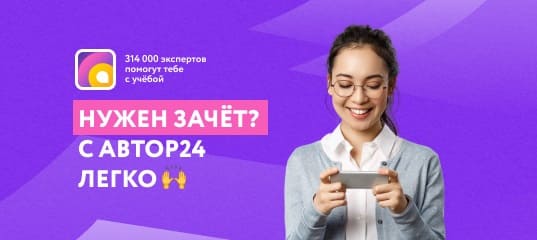
Мы поможем в написании ваших работ!