Обработка ступенчатых поверхностей
Черновая и чистовая обработка ступенчатых деталей производится на одношпиндельных многорезцовых и гидрокопировальных полуавтоматах, вертикальных многошпиндельных автоматах, на токарных станках, оборудованных гидрокопировальными суппортами, и на универсальных токарных станках обычного типа.
В крупносерийном и массовом производстве ступенчатые детали обрабатывают на одно- и многошпиндельных вертикальных полуавтоматах с точностью до 4 - 5-го классов при предварительном обтачивании и по 4-му классу – при чистовом. Размеры по длине выдерживаются по 4 – 5-му классам точности. При многорезцовой обработке на вертикальных многошпиндельных полуавтоматах последовательного действия благодаря обтачиванию поверхностей за несколько переходов можно достичь 2 – 3-го классов точности.
В мелкосерийном производстве ступенчатые детали обрабатываются на токарных станках обычного типа и оборудованных гидрокопировальными суппортами.
Применение гидрокопировальных полуавтоматов оказывается целесообразным как в массовом, так и в серийном производстве.
При черновой обработке ступенчатых деталей на токарных станках, когда в качестве заготовки взят прокат, важно правильно выбрать последовательность обработки отдельных ступеней.
Рассмотрим черновую обработку одного конца ступенчатого вала из проката диаметром 100мм (рис. 1.22, а).
Возможные варианты обработки ступеней этого вала показаны на рис. 1.22, б — д.
|
|
По первой схеме (рис. 1.22, б) каждая последующая ступень обрабатывается отдельно после получения предшествующей ступени, при этом общая длина рабочего хода резца L0 будет составлять 400 мм ,длина холостых перемещений Lx-=400 мм, глубина резания - от 11 до 3,5 мм .При обработке по второй схеме Lp = 550 мм и Lx= 550 мм ; по третьей схеме - Lр = 650 мм и Lx = 700 мм; по четвертой схеме - Lр = 800 мм и Lx= 800 мм .
Наименьшая длина как рабочего хода, так и холостых перемещений резца получается при обработке по первой схеме. Следовательно, эта схема обеспечивает наибольшую производительность. Однако при недостаточной мощности станка работа с большой глубиной резания (t = 3,5-11мм) может оказаться невыгодной. В этом случае наибольшая производительность будет иметь место при работе по четвертой схеме (см. рис. 1.22, д).
На рациональный выбор той или иной схемы обработки ступенчатых деталей оказывает влияние и жест-. кость технологической системы.
Получение ступенчатых поверхностей во многих случаях связано с подрезанием уступов после продольного точения. В этих случаях чистовая обработка уступов чаще всего осуществляется после обработки всех цилиндрических участков ступенчатой детали (рис. 1.23, а).
|
|
Комбинированными резцами, пригодными как для обработки цилиндрических поверхностей, так и для подрезания уступов и прорезания канавок, чистовую обработку ступенчатых деталей наиболее целесообразно производить по схеме, приведенной на рис. 1.23, б.
Получение требуемых диаметров ступенчатых поверхностей и точного расположения уступов по длине связано со значительной затратой вспомогательного времени.
Для автоматизации обработки ступенчатых деталей токари-новаторы В.Н. Трутнев, В.К.Семинский и другие создали различные конструкции механических копировальных устройств. Наиболее удачным является устройство В.К. Семинского для обтачивания ступенчатых деталей на токарном станке (рис. 1.24).
Копировальное приспособление устанавливают на место резцедержателя. В корпусе 2 по скользящей посадке 2-го класса точности расположена пиноль 3 с закрепленным на ней сухарем 4. Пружина 6, упирающаяся одним концом в дно стакана 7, а другим в шайбу 8, создает постоянный контакт между сухарем 4 и копиром 5. При включении механической подачи суппорт станка вместе с копирным приспособлением перемещается по направлению к передней бабке. Резец 1 обрабатывает первую ступень детали, а сухарь 4 скользит по неподвижному копиру, связанному шарнирной парой 11 с кронштейном 10 на станине станка. Встречая на своем пути ступеньку, образованную на копире 5, сухарь 4 сходит с первой ступеньки на вторую, а резец вместе с пинолью под действием пружины 6 отходит назад и начинает обрабатывать вторую ступень большого диаметра.
|
|
Для образования прямого угла между ступенями вала применяется резец с углом в плане 90°. Пиноль 3 в корпусе 2 устанавливается под углом 15°, а переходные уступы на копире имеют наклон к оси 75°. Поэтому резец отходит от детали в направлении, перпендикулярном ее оси.
После окончания обработки детали поперечный суппорт отводят от нее на 20—30 мм и с помощью эксцентрика 9 подают вперед пиноль, чтобы при возвращении суппорта в первоначальное положение сухарь 4 не касался копира. Затем эксцентрик 9 поворачивают в обратную сторону, и сухарь 4 снова приходит в контакт с копиром.
Приспособление настраивают на получение заданной длины только первой ступени первой детали партии. Настройку на заданный диаметр производят по лимбу поперечного суппорта.
Рассмотренное приспособление применяют для обработки ступенчатых деталей с перепадом диаметров между уступами до 5 мм и разницей между наибольшим и наименьшим диаметрами их до 30 мм .
|
|
Точность обработки по диаметру ±0,05 мм , а по длине ±0,2 мм .
На токарных станках различных типов ступенчатые детали можно обрабатывать с помощью копировальных устройств — гидравлических, электрических и механических. Использование таких устройств автоматизирует процесс обработки, что приводит к значительному повышению производительности труда.
Гидрокопировальные устройства позволяют обрабатывать методом автоматического копирования по эталонной детали или плоскому копиру различные заготовки с цилиндрическими, коническими и фасонными поверхностями и подрезать торцы, расположенные под углом 90° к оси.
В промышленности нашел широкое применение гидрокопировальный суппорт КСТ-1, который состоит из копировального устройства с гидравлическим цилиндром дифференциального типа и гидравлическим щупом.
Размещается он на суппорте станка, для чего на направляющих поперечных салазок каретки 1 суппорта (рис. 1.25) устанавливается специальная плита 2, на которой располагается гидроцилиндр 3. Последний, изготовленный за одно целое с копировальным суппортом, снабжен резцедержателем 4. Гидроцилиндр может перемещаться по направляющим плиты под углом 45° к оси обрабатываемой детали. Шток 5 поршня цилиндра скреплен с плитой и находится в неподвижном положении.
Процесс копирования осуществляется следующим образом. Из гидробака при помощи насоса 6 производительностью 5 л/мин масло, проходя через фильтр, поступает через отверстие штока 5 в правую полость 7 гидроцилиндра 3, в котором находится поршень 14. Площадь левой полости 8 цилиндра в 2 раза больше площади правой полости 7. Обе полости сообщаются между собой через имеющееся в поршне 14 отверстие малого' диаметра. Через это отверстие масло попадает в левую полость 8, которая через кольцевое отверстие 9 золотника соединена со сливом.
Плунжер 10 золотника под воздействием пружины 11 прижимает к шаблону 12 рычажный щуп 13. Если под действием шаблона рычажный щуп переместит вверх плунжер 10, то проходное кольцевое сечение 9 будет открыто и масло из полости 8 будет свободно проходить в гидробак, при этом благодаря сопротивлению протеканию масла из полости 7 в полость 8 усилие, действующее на дно цилиндра в полости 7, будет значительно больше,, чем в полости 8. Равнодействующая этих усилий, оказывая давление на дно гидроцилиндра 3 в полости 7, будет отодвигать цилиндр, а следовательно, и суппорт с резцом от обрабатываемой детали.
Если плунжер 10 опустится вниз, то проходное кольцевое сечение 9 перекроется буртиком плунжера, выход масла из полости 8 гидроцилиндра в гидробак прекратится, и давление в полостях 7 и 8 установится одинаковым. Вследствие разницы полезных площадей поршня 14 в полостях 7 и 8 равнодействующее усилие на гидроцилиндр вызовет перемещение суппорта с резцом по направлению к обрабатываемой детали.
Обработка осуществляется при постоянной по величине и направлению продольной подаче. Рычажный щуп скользит по неподвижному шаблону и, перемещая плунжер, заставляет копировальный суппорт передвигаться вперед или назад. В результате резец воспроизводит движение щупа, которое складывается из продольного перемещения каретки суппорта и движения гидросуппорта. Если рычажный щуп скользит по горизонтальной поверхности шаблона, то в полостях 7 и 8 создается такое давление, при котором копировальный суппорт остается неподвижным. В этом случае происходит обработка цилиндрической поверхности за счет продольной подачи суппорта.
Подрезание уступов и торцовых поверхностей (а также и обтачивание фасонных и конических поверхностей) осуществляется благодаря сложению двух движений - продольного перемещения суппорта станка с подачей s1 и перемещения копировального гидравлического суппорта со скоростью s2. В результате сложения этих движений резец перемещается перпендикулярно оси детали со скоростью s.
Схема для определения результирующей скорости перемещения резца s при подрезании уступа приведена на рис. 1.26.
Так как направляющие гидрокопировального суппорта расположены под углом 45°, то, как это видно из треугольника, при подрезании торцов и уступов мы имеем s = s1.
Скорость движения гидрокопировального суппорта будет равна:
s2 = =
1,4s1
С помощью гидрокопировального устройства рассмотренной конструкции можно обтачивать только такие торцовые поверхности, которые обращены в сторону задней бабки, поэтому большинство ступенчатых деталей обрабатывается за две установки. Достижимая точность обработки - в пределах 3-го класса, а шероховатость поверхности – 6-7-го классов.
В серийном и крупносерийном, производстве широко используются многорезцовые и токарно-копировальные станки, полуавтоматы и автоматы.
У многорезцовых станков, как правило, два суппорта - передний и задний. Передний суппорт имеет продольное и поперечное перемещения, а задний — только поперечное. Предназначен он для подрезки торцов, прорезки канавок и снятия фасок. Многорезцовые станки с большим расстоянием между центрами имеют два передних и два задних суппорта. Движение суппорта автоматизировано. Останавливается станок также автоматически.
При обработке ступенчатых деталей на многорезцовых станках возможны различные варианты снятия припуска отдельными резцами при их одновременной работе. У ступенчатых деталей из прутковых заготовок этот процесс осуществляется по трем основным схемам (рис. 1.27):
1) обтачивание с продольной подачей (рис. 1.27, а). При обработке по этой схеме каждый резец устанавливают на определенный диаметр и располагают их таким образом, чтобы они вступали в работу последовательно друг за другом. В этом случае нагрузка на станок возрастает по мере того, как вступает в действие каждый следующий резец. Максимального значения она достигает при одновременной работе всех резцов.
Машинное время определяется здесь длиной рабочего хода суппорта, равной суммарной длине всех обрабатываемых ступеней:
Lпр= l1+ l2+ l3
По первой схеме можно обрабатывать только те детали, у которых диаметры ступеней увеличиваются в направлении движения суппорта;
2) обтачивание с врезанием и последующей продольной подачей (рис. 1.27, б). При обработке по этой схеме резцы 1 и 2 вступают в работу одновременно в различных точках. Врезание резцов на заданную глубину производится под углом по отношению к оси станка. Направление подачи sвр должно быть таким, чтобы угол Θ, определяющий направление врезания, был меньше вспомогательного угла в плане φ1. После врезания резцов суппорт движется в продольном направлении. Каждая ступень детали обрабатывается одним резцом, вследствие чего суппорт передвигается на длину наиболее длинной ступени l1.
Машинное время обработки по второй схеме определяется наибольшей длиной ступени l1:
Lпр = l1.
Когда на детали имеется ступень, длина которой значительно больше длины других ступеней, целесообразно обтачивать ее двумя и более резцами, при этом значительно уменьшается длина рабочего хода суппорта - каждый резец совершает путь, равный длине ступени l3:
l3 = l2 =
3) обтачивание с поперечной подачей (рис. 1.27, в). Эта схема обработки характеризуется тем, что каждый резец обтачивает данную ступень с поперечной подачей sпоп, причем ширина каждого резца равна ширине обрабатываемой ступени. Эта схема может быть использована при обработке коротких цилиндрических, конических и фасонных участков детали.
На точность обработки на многорезцовых станках оказывают влияние погрешность взаимного расположения резцов в наладке, неравномерный износ их и неодинаковое отжатие элементов технологической системы вследствие разновременного вступления резцов в работу.
На многорезцовых станках при предварительной обработке достигают 4-5-го классов точности, а при чистовой - 4-го класса. Точность размеров по длине выдерживается - по 4-5-му классам.
Схема обработки ступенчатого вала на многорезцовом полуавтомате приведена на рис. 1.28. Вначале осуществляют черновую обработку одного конца вала (рис. 1.28, а), а затем другого (рис. 1.28, б). Чистовую обработку производят в той же последовательности. Как видно из схемы, длина участков, на которых работают проходные резцы, одинаковы.
По производительности многорезцовая обработка не всегда имеет преимущество перед обработкой на гидрокопировальных полуавтоматах. Это объясняется большими затратами подготовительно-заключительного времени и времени на техническое обслуживание многорезцовых станков, а также тем, что режимы резания на гидрокопировальных станках выше, чем на многорезцовых. В промышленности находят применение гидрокопировальные токарные полуавтоматы моделей 1712, 1722, 1732, 1732А и 1732Б. Они предназначены для обработки в центрах сложных фасонных, конусных и ступенчатых деталей методом копирования. Копировальный суппорт снабжен гидравлическим следящим устройством, позволяющим воспроизводить форму детали по эталону или шаблону. Два подрезных суппорта служат для прорезания канавок, отрезания прибыли и подрезания торцов. Рабочая подача суппортов, ускоренный подвод и отвод их, а также перемещение и закрепление пиноли задней бабки осуществляются с помощью гидросистемы.
Небольшое количество резцов и простота установки копира дают возможность в 2-3 раза сократить время наладки и подналадки полуавтоматов по сравнению с наладкой многорезцовых станков.
На выпускаемых моделях гидрокопировальных полуавтоматов обрабатывают детали диаметром до 320 мм и длиной до 1250 и до 1600 мм .
На гидрокопировальных станках новейших моделей черновую обработку можно осуществлять с помощью многорезцового суппорта, а чистовую – однорезцового копировального суппорта, причем при закреплении детали торцовым поводком обработку можно вести с одной установки. Некоторые модели имеют несколько (до пяти) независимо перемещающихся копировальных суппортов, что значительно повышает производительность станка.
При установке на токарно-копировальных полуавтоматах специальных копирных барабанов можно производить многопроходную обработку.
На токарно-копировальных полуавтоматах достигаются более высокие классы точности обработки (0,05— 0,06 мм ) и чистоты, чем на многорезцовых станках,
Дата добавления: 2018-11-24; просмотров: 463; Мы поможем в написании вашей работы! |
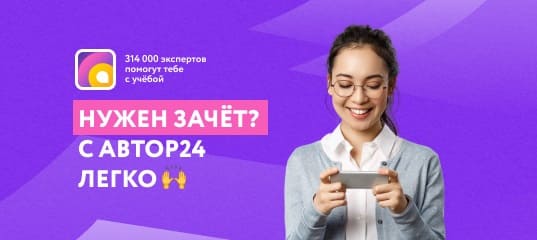
Мы поможем в написании ваших работ!