Нарезание резьбы вращающимися резцами
Сущность метода нарезания резьбы вращающимися резцами заключается в следующем. Заготовка, на которой должна быть образована резьба, закрепляется в патроне или в центрах станка и вращается с небольшим числом оборотов (обычно 3—40 об/мин.). Резец, установленный в специальной резцовой головке, вращается вместе с ней с большим числом оборотов (обычно 1000—3000 об/мин.).
Ось, вокруг которой вращается резец, смещена относительно оси вращения детали (рис. 3.15). Поэтому резец периодически то входит в контакт с заготовкой, снимая с нее стружку, то выходит из контакта, т. е. процесс резания осуществляется с перерывами.
За один полный оборот заготовки суппорт с резцовой головкой перемещается вдоль оси заготовки на величину, равную шагу резьбы.
В зависимости от того, как расположена траектория вращения резца
относительно оси вращения заготовки, различают два способа нарезания резьбы вращающимися резцами:
1) способ внутреннего касания (охваты-
вание); в этом случае заготовка размещается в отвер-
стии резцовой головки и вращается вокруг оси О, а резцовая головка вращается вокруг оси О1 (рис. 3.15, а);
2) способ внешнего касания (огибание); заготовка находится сбоку от резцовой головки (рис. 3.15, б).
При работе способом охватывания резец плавно врезается в заготовку, длина дуги касания вершины резца и обрабатываемой заготовки составляет примерно 1/3 длины окружности резьбы, сечение среза постепенно увеличивается от нуля до наибольшего значения и затем плавно уменьшается. Стружка получается растянутой и тонкой, и, несмотря на прерывистую работу, резец почти не испытывает ударов — резание протекает плавно.
|
|
При работе способом огибания резец соприкасается с заготовкой на сравнительно небольшой длине дуги окружности, стружка получается короткой и толстой, работа происходит с ударами, и на поверхности резьбы остаются значительные следы обработки. Так как второй способ оказался менее экономичным, он не получил распространения в заводской практике.
Процесс нарезания резьбы способом внутреннего касания представлен в виде схемы, на рис. 3.16, где винтовая нарезка образуется одним резцом.
Деталь имеет наружный диаметр резьбы d2 и внутренний d1. Допустим, что при первом обороте резцовой головки резцом срезан металл на участке АаС. За время одного полного оборота головки деталь повернется в направлении часовой стрелки на некоторый угол φ, и точка К2 займет положение точки К1. В начале второго оборота резец войдет в контакт с деталью в точке К2 и за полный оборот резцовой головки срежет металл на участке К2 bа. При каждом последующем обороте головки резец удаляет точно такие же части металла, и за время одного полного оборота детали образуется винтовая канавка, или виток резьбы.
|
|
Длина дуги bа измеряется в миллиметрах по длине окружности детали. Эта величина обозначается sz и называется круговой подачей на один резец. Величина круговой подачи оказывает влияние на качество резьбы. При подаче детали sz> l мм/резец, особенно при обработке способом огибания, когда следы движения резца на поверхности детали имеют вогнутую форму, огранка становится заметной на глаз. При подачах детали sz = 0,6—0,8 мм/резец и работе способом охватывания огранка становится незаметной невооруженным глазом и на качество резьбы практически не влияет.
Зная круговую подачу, которая выбирается в зависимости от механических свойств металла, можно определить число оборотов нарезаемой детали nд из следующего уравнения:
nд = мм,
где d — наружный диаметр резьбы детали, в мм;
nр — число оборотов в минуту резцовой головки;
z — число резцов в головке.
Число оборотов резцовой головки подсчитывается по следующей формуле:
nр = мм,
где v — окружная скорость резцов в головке, в м/мин;
D — диаметр, на котором расположены резцы в головке, в мм.
|
|
Продольная подача определяется величиной перемещения резцовой головки (в миллиметрах) в осевом направлении за один оборот детали. Она равна шагу резьбы.
Производительность процесса нарезания и качество резьбы в значительной степени зависят от отношения диаметра вращения вершины резцов D и диаметра детали d.
При данной скорости резания число оборотов резцовой головки nр будет тем больше, чем меньше диаметр D1. Следовательно, при данной величине круговой подачи sz увеличение числа оборотов резцовой головки означает и увеличение числа оборотов детали, т. е. повышение производительности.
Практикой установлено, что для нарезания наружных треугольных резьб целесо-образно принимать = 1,4—1,6. При диаметре D < 1,4 d увеличивается дуга касания резца и детали, вследствие чего резец не успевает охладиться и его стойкость уменьшается.
Вращающимися резцами нарезают как наружные, так и внутренние резьбы (рис.3.17). При нарезании внутренних резьб нормальные условия работы достигаются при
= 0,5—0,55 и при диаметре отверстия d ≥ 45—50 мм. Резьбу нарезают на токарно-винторезных,
резьбонарезных и резьбофрезерных станках с помощью приспособлений.
|
|
Для нарезания внутренних резьб применяют специальную оправку, конический хвостовик которой вставляют в отверстие шпинделя резьбонарезного приспособления и закрепляют при помощи шайбы 5 и винта 6 (рис. 3.18). Для обеспечения равномерности
хода приспособления на оправку 4 насаживают маховик 3, закрепляемый гайкой 2. Твердосплавной резец 1 вставляют в гнездо на передней части оправки и закрепляют торцовым или боковым винтом.
При нарезании наружной резьбы на стальных деталях скорость резания составляет от 150 до 300 м/мин, а на бронзовых — до 500—600 м/мин. Охлаждение не применяется. Круговая подача sz = 0,3— 0,8 мм/резец. Резьбы с шагом до 6 мм нарезаются за один проход. Точность резьбы — 2—3-й классы, а шероховатость поверхности — 5—6-й классы.
Фрезерование резьбы
Фрезерование наружной и внутренней резьб осуществляется в основном дисковыми и групповыми фрезами.
Дисковые резьбовые фрезы применяют для нарезания длинных наружных и внутренних трапецеидальных резьб диаметром от 10 до 82 мм с шагом 2—12 мм. Резьбу обрабатывают за два прохода — черновой и чистовой — фрезами.
Схема фрезерования наружной резьбы дисковой фрезой на универсально-фрезерном станке приведена на рис. 3.19. Фрезу устанавливают относительно заготовки под углом ω, равным углу подъема винтовой линии резьбы. В процессе работы фреза совершает вращательное движение, а заготовка — вращательное и поступательное.
Длинные наружные резьбы можно фрезеровать дисковыми фрезами на универсальном резьбофрезерном станке.
Для нарезания коротких метрических наружных и внутренних резьб с шагом от 0,75 до 6 мм используют групповые (гребенчатые) резьбовые фрезы. Эти фрезы имеют такой же профиль, как* и нарезаемая резьба, но их зубья расположены не по винтовой линии, а по кольцевым поверхностям, перпендикулярным оси фрезы. По наружному цилиндру фреза прорезана продольными канавками, число которых выбирается в зависимости от диаметра фрезы.
Групповые резьбовые фрезы относятся к типу фрез с затылованной формой зубьев. Задний угол на вершине зуба α = 8—10°, передний γ = 0. Длина режущей части фрезы делается больше длины нарезаемой резьбы на 2— 3 нитки.
Схема фрезерования наружной и внутренней резьб групповыми фрезами приведена на рис. 3.20. Фреза и обрабатываемая деталь получают вращательное движение. Кроме того, фреза медленно перемещается вдоль оси — за один оборот детали передвигается на шаг резьбы и в поперечном направлении — на полную глубину резьбы. Когда фреза врезается в деталь на полную глубину резьбы, поперечное перемещение ее автоматически выключается. Для нарезания резьбы на всей заданной длине детали достаточно сделать один оборот. Но если учесть подвод, врезание и отвод фрезы, то весь цикл нарезания резьбы осуществляется за 11/4 оборота детали.
Фрезерование резьбы производится со встречной подачей, поэтому при нарезании наружной резьбы (рис. 3.20, а) фреза и деталь вращаются в одну сторону, а при обработке внутренней — в противоположные.
При нарезании внутренней резьбы (рис. 3.20, б) диаметр фрезы должен быть примерно вдвое меньше внутреннего диаметра резьбы.
Групповыми фрезами можно нарезать конические и многозаходные резьбы, а также некоторые типы специальных резьб на резьбонарезных станках моделей 5М5Б62 и 561.
Наибольший диаметр фрезеруемой на станке мод. 5М5Б62 резьбы: наружной — 100 мм и внутренней — 80 мм; наибольшая длина — 75 мм и шаг — 6 мм.
Станок мод. 561 предназначен для нарезания длинных резьб (до 1500 мм). В условиях мелкосерийного производства на станках мод. 561 можно обрабатывать групповыми фрезами и короткие резьбы.
Наименьший диаметр внутренней резьбы лимитируется жесткостью и прочностью фрезы. Он может составлять 18—20 мм для мелкой метрической резьбы и 27— 30 мм — для крепежной метрической резьбы.
В крупносерийном и массовом производстве групповыми фрезами нарезают резьбы 2—3-го классов точности диаметром свыше 30—40 мм. При меньшем диаметре резьбы фрезерование целесообразно применять только в тех случаях, когда по технологическим и другим причинам нельзя воспользоваться более производительными методами.
Наружная резьба может быть образована также торцовой фрезой, вставные ножи которой заточены по профилю нитки резьбы. Этим способом нарезают резьбы на вертикально-фрезерном станке, где заготовка получает вращение от делительной головки или через особый редуктор, устанавливаемый на рабочем столе станка и приводимый в действие от механизма подачи стола (рис. 3.21).
Для свободного выхода вставного ножа фрезы из канавки при обработке относительно длинных резьб торцовой фрезой небольшого диаметра ее ось должна быть установлена под углом φ < 90° к оси нарезаемой заготовки. При нарезании же коротких резьб этот угол может быть взят равным 90°.
Торцовой фрезой можно нарезать резьбы также на горизонтально-фрезерном станке с поворотной головкой.
Накатывание резьбы
Кроме образования резьбы резанием в промышленности широко применяют метод накатывания резьбы.
Сущность метода накатывания заключается в том, что заготовка обжимается более твердыми накатывающими инструментами и на ней благодаря пластическим свойствам материала остается отпечаток, создаваемый рабочей частью инструмента при соответствующей кинематической связи его с заготовкой.
Образование резьбы накатыванием имеет ряд преимуществ по сравнению с изготовлением резанием. При обычном нарезании резьбы волокна материала перерезаются (рис. 3.22, а), а при накатывании они изгибаются,
располагаясь вдоль профиля резьбы (рис. 3.22,б). Предел прочности на срез накатанных резьбовых ниток на 25—40% выше нарезанных резцом.
Наряду с высокой прочностью метод накатывания обеспечивает высокую износостойкость резьбовых поверхностей, а также значительное увеличение производительности.
Заготовки для накатывания резьбы могут быть изготовлены из сталей различных марок и цветных металлов. Все материалы с относительным удлинением δ ≥ 12% обычно хорошо накатываются. Процесс накатки резьбы сопровождается смазкой.
Качество накатанной резьбы во многом зависит от правильного выбора величины диаметра заготовки, так как при накатывании металл не удаляется и резьба получается только благодаря его пластическим деформациям. Имеется довольно много попыток определить
"диаметр заготовки на основании аналитического расчета или эмпирической формулы. Однако производственная практика показывает, что величину диаметра заготовки целесообразно выбирать пробным накатыванием, исходя из положения, что диаметр заготовки должен быть приблизительно равен среднему диаметру резьбы.
Для определения диаметра заготовок на заводах изготовляют ступенчатую заготовку, у которой диаметр каждой ступени отличается от среднего диаметра резьбы на небольшую величину (порядка 0,02—0,03 мм). Накатывание такой заготовки по всей длине показывает наиболее целесообразный диапазон диаметров, в котором обеспечивается накатывание годной резьбы.
Шероховатость поверхности заготовки должна быть не ниже 4-го класса.
Резьбу накатывают плоскими плашками, круглыми роликами и резьбонакатными головками. Резьбу 1-го и 2-го классов точности получают с помощью роликов, а 2—3-го классов — плашек. Шероховатость накатанной поверхности — 7—8-й классы чистоты.
Накатывание резьбы плашками. Схема накатывания резьбы плашками приведена на рис. 3.23. Неподвижная плашка 1 закреплена на станке, а подвижная 3 — на ползуне станка. Когда ползун с плашкой 3 находится вкрайнем правом положении, заготовка 2 автоматически подается толкателем к заборной части плашек. Затем толкатель отходит, и подвижная плашка 3, перемещаясь с ползуном влево, увлекает за собой заготовку, которая прокатывается между плашками.
Наибольший диаметр накатываемой резьбы — 8 мм.
Основные размеры плашек регламентированы ГОСТом. Изготовляют их из сталей Х12АФ или9ХС с термической обработкой до твердости HRC 58—60. Шероховатость поверхности рабочей части плашек должна быть не ниже 7-го класса.
На рабочей поверхности плашек образованы резьбовые нитки, расположенные под углом α подъема резьбы детали по среднему диаметру.
Рабочая сторона плашки имеет заборную l1, калибрующую l2 и выходную l3 части. Подвижная плашка может выполняться с заборной частью и без нее.
Способ накатывания плашками позволяет образовывать резьбы на болтах, винтах, шпильках и других деталях диаметром от 2 до 25 мм и длиной до 125 мм. Производительность процесса — 60—120 деталей в минуту приавтоматической загрузке заготовок и 30—50 деталей — при ручной. Скорость накатывания v = 15—20 м/мин. При накатывании используются различные смазки. Точность накатанной резьбы соответствует 2—3-му классам, шероховатость поверхности — 6—8-му классам.
Накатывание резьбы роликами. При накатывании резьбы роликами можно применять три вида подач: тангенциальную, радиальную и осевую. Наиболее распространена схема накатывания резьбы двумя роликами с радиальной подачей (рис. 3.24).
Резьбу накатывают на специальных станках, обеспечивающих одновременное вращение двух роликов 1 и 2 в одну сторону. Заготовку 3 устанавливают на подпорку 4 между роликами. При накатывании заготовка прижимается к осевому упору 5. Подвижный ролик 2 при вращении получает радиальную подачу и прижимает заготовку к ролику 1. Резьба роликов вдавливается в заготовку и оставляет на ней негативный отпечаток. При достижении требуемой глубины резьбы ролик 2 после небольшой выдержки быстро отводится. Готовая деталь удаляется, и вводится следующая заготовка.
Для получения правильной по профилю и размерам резьбы ролики должны быть установлены по отношению друг к другу в осевом направлении строго в определенном положении. При нарезании однозаходной или многозаходной резьбы с нечетным числом заходов вершина ниток резьбы одного ролика должна располагаться против середины впадины резьбы второго ролика, а при обработке многозаходной резьбы с четным числом заходов вершины резьб обоих роликов должны располагаться друг против друга.
Накатные ролики для образования метрических резьб диаметром 3—45 мм регламентированы ГОСТом. Ролики изготовляют из стали Х12АФ, термически обработанной до твердости HRC 58—60.
Роликами обычной точности нарезают резьбу 2-го класса точности с шероховатостью поверхности профиля 7-го класса, а роликами повышенной точности — не ниже 1-го класса точности с шероховатостью поверхности 8-го класса.
Направление резьбы на роликах противоположно направлению резьбы на детали.
При выборе диаметра накатных роликов учитывают, что процесс накатки улучшается с увеличением диаметра роликов. Чтобы обеспечить одинаковый угол α подъема резьбы на ролике и на заготовке, резьбу выполняют многозаходной, при этом число заходов определяют по формуле:
n = ,
где Dср — средний диаметр ролика;
dср - средний диаметр резьбы заготовки.
Следовательно, ход резьбы роликов Нр будет равен:
Нр = ns,
где s — шаг накатываемой резьбы.
При накатывании на детали многозаходной резьбы с числом заходов пдчисло заходов резьбы роликов будет составлять:
n = nд .
Накатыванием можно образовывать резьбы диаметром от 0,3 до 150 мм на деталях из сталей твердостью до HRC 37, а также из цветных сплавов с точностью до 1-го класса и с шероховатостью поверхности до 7—8-го классов. Скорость накатывания резьбы роликами колеблется в пределах 25—120 м/мин.
Длина получаемой резьбы лимитируется шириной роликов, которая должна быть несколько больше заданной длины резьбы и редко превышает 100—120 мм.
Производительность процесса накатывания зависит от шага и длины резьбы, материала заготовок и колеблется в пределах 80—500 деталей в час.
Лабораторная работа № 4
Тема: Обработка плоских поверхностей
Дата добавления: 2018-11-24; просмотров: 893; Мы поможем в написании вашей работы! |
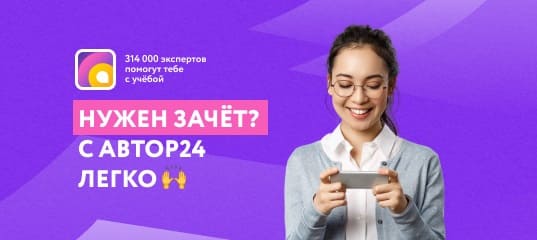
Мы поможем в написании ваших работ!