Обработка цилиндрических и торцовых поверхностей
При изготовлении гладких валов в массовом производстве в качестве заготовок применяют калиброванные прутки 3-го, 3а и 4-го классов точности. В этом случае обработка гладких валов производится на станках шлифовальной группы – предварительное и окончательное шлифование на бесцентрово-шлифовальном станке.
При обработке длинных гладких валов из горячекатаного проката их предварительно обтачивают на бесцентрово-обточных станках мод. 9330А, а затем шлифуют на бесцентрово-шлифовальных станках или обкатывают роликами на правильно-полировальных станках.
В условиях единичного или серийного производства применяют две схемы обработки цилиндрических поверхностей на токарных станках.
1. обработка за один проход резцом, заранее установленным на размер (рис.1.18, а). В процессе обработки всей партии заготовок резец, установленный на размер d, не перемещается в поперечном направлении. После обтачивания детали на длине l ее снимают, а резец отводят в исходное положение.
По этой схеме обрабатывают партию одинаковых небольших по размерам деталей. По ней же выполняют черновую, а иногда и получистовую обработку небольших партий деталей за две установки. После обтачивания одной половины детали до диаметра 30 мм (рис. 1.18, б) она переустанавливается в центрах и при том же положении резца в радиальном направлении обрабатывается вторая половина детали (рис. 1.18, в).
|
|
2. обработка с перемещением резца в поперечном направлении. При обтачивании по этой схеме в конце прохода (рис. 1.19) выключают механическую подачу и отводят резец от обработанной поверхности сначала в поперечном направлении на 5-6 мм, а затем и в продольном в исходное положение.
Если данная поверхность обрабатывается за несколько проходов, то после каждого прохода резец устанавливают на заданный диаметральный размер.
Подрезание торцовых поверхностей в единичном и мелкосерийном производстве осуществляется на обычных токарных или револьверных станках, а в крупносерийном и массовом – на специальных торцоподрезных станках.
Торцы деталей, закрепленных в патроне, целесообразно подрезать проходными резцами, позволяющими применять более производительные режимы резания. Ими можно производить обработку торцов как от периферии к центру (рис. 1.20, а), так и от центра к периферии (рис. 1.20, б).
Чистовая обработка торцов осуществляется подрезными резцами в направлении как от периферии к центру (рис. 1.20, в), так и от центра к периферии (рис. 1.20, г). Подрезание торца с подачей резца от периферии к центру детали приводит к постепенному увеличению глубины резания – резец врезается в деталь, при этом торцовая поверхность получается вогнутой, процесс резания протекает неспокойно, а чистота поверхности ухудшается. При подаче подрезного реза от центра детали к периферии указанные отрицательные явления не наблюдаются. Однако применение этой схемы не всегда возможно из-за трудности врезания резца и невозможности определить длину обрабатываемой детали методом пробных проходов.
|
|
Известен и способ подрезания торцов широкими резцами. Однако точность обработки при этом снижается из-за влияния погрешностей формы режущей кромки резца, а также его установки. Обработка широкими резцами осуществляется на револьверных станках при продольной подаче s. Резец закрепляют в револьверной головке.
В некоторых случаях торцовые поверхности обрабатывают двумя широкими резцами, при этом давление на режущие кромки уравновешивается и работа протекает более спокойно, чем при использовании одного резца.
При обработке детали в центрах подрезать торец можно со стороны задней бабки. Операция выполняется подрезным отогнутым резцом с применением полуцентра (рис. 1.21, а) или при использовании центрового отверстия на детали с предохранительной фаской (рис. 1.21,б).
Дата добавления: 2018-11-24; просмотров: 246; Мы поможем в написании вашей работы! |
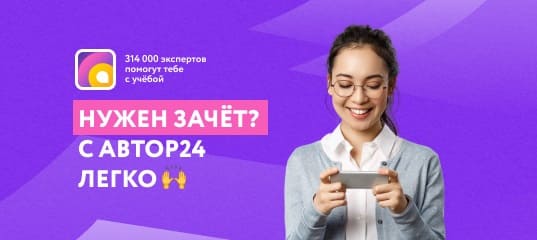
Мы поможем в написании ваших работ!