Выбор технологических баз и обоснование последовательности устранения дефектов
Точность обработки при восстановлении детали зависит от правильного выбора технологических баз, который требует четкого представления о функциональном назначении поверхностей детали, размерной взаимосвязи между ними, их состоянии.
Технологической базой называется поверхность, сочетание поверхностей, ось или точка, используемые для определения положения детали в процессе обработки.
Технологические базы обрабатываются с высокой точностью. При их выборе руководствуются следующими требованиями:
– при наличии используются базы завода-изготовителя;
– по возможности совмещаются технологические и конструкторские базы;
– точность изготовления базовых поверхностей должна быть не ниже точности изготовления восстанавливаемых поверхностей;
– базовые поверхности обрабатываются или изготавливаются в первую очередь после восстановления формы и целостности детали;
– поверхности, для которых необходимо обеспечить точность относительного положения (соосность, перпендикулярность, параллельность осей), обрабатываются с одной установки;
– принятая технологическая база должна по возможности применяться на всех операциях технологического процесса, а если это невозможно, то за следующую базу необходимо принимать обработанную поверхность детали, размерно-связанную непосредственно с обрабатываемой.
В зависимости от конфигурации детали, характера и величины износа поверхностей рекомендуются следующие схемы базирования:
|
|
– деталь базируется по сохранившейся базе, используемой при ее изготовлении;
– деталь базируется по неизношенным, точно изготовленным поверхностям;
– деталь первоначально базируется по мало- или неизношенным поверхностям для правки существующих или изготовления новых технологических баз с последующим базированием по ним.
Для восстановления валика 50-11307052-Б принимаем следующие технологические базы: наружные и внутренние неизношенные цилиндрические поверхности. В качестве средств базирования принимаем: патрон самоцентрирующийся трехкулачковый ГОСТ 2675–80, центр станочный вращающийся ГОСТ 8742–85, тиски станочные с призматическими губками ГОСТ 21168–75.
При разработке технологического маршрута определяют последовательность выполнения технологических операций и основное оборудование и руководствуются следующими правилами:
– в первую очередь выполняют операции, вызывающие изменение физико-механических свойств и формы детали, возникновение остаточных напряжений (сварка, наплавка, заварка пазов);
– затем, при необходимости, предусматривают операции, устраняющие отрицательное влияние энергетических воздействий (правка, термообработка);
|
|
– для валов при отсутствии их изгиба первыми выполняются операции по восстановлению или изготовлению базовых поверхностей;
– перед нанесением тонких покрытий выполняют операции по удалению дефектных слоев металла, приданию правильной формы (цилиндричность, прямолинейность и т. д.), обеспечению эксплуатационной толщины покрытия и созданию необходимой шероховатости;
– в случае возникновения необходимости создания высокой твердости поверхности термической обработкой последовательность выполнения операций следующая: черновая механическая, термическая, чистовая механическая обработка;
– при изготовлении шпоночных пазов последовательность выполнения операций следующая: черновая механическая обработка цилиндрической поверхности, изготовление шпоночного паза, чистовая механическая обработка цилиндрической поверхности;
– при изготовлении точных отверстий осевым инструментом полная последовательность выполнения операций следующая: сверление (рассверливание), зенкерование, зенкование фасок, развертывание;
– вспомогательные поверхности (фаски, проточки) изготавливаются перед чистовой обработкой основных поверхностей;
|
|
– легкоповреждаемые и точные поверхности обрабатываются в конце маршрута;
– перед наплавкой радиальные отверстия под шплинты на резьбовых концах валов должны быть заглушены вставками из токопроводящих материалов;
– для корпусных деталей операции по восстановлению базовых поверхностей выполняются после восстановления целостности и формы детали (заделки трещин, пробоин и т. д.) перед механической обработкой точных отверстий (посадочных мест под подшипники, валики, оси).
Технологический маршрут описывается действиями с указанием поверхностей, номеров дефектов и основных исполнительных размеров.
Технологический маршрут восстановления валика 50-11307052-Б включает в себя следующие операции: 005 слесарная (деф. 1); 010 фрезерная (деф. 3); 015 электроискровая обработка (деф. 2, 4); 020 слесарная (деф. 2, 4); 025 слесарная (деф. 2); 030 токарная (деф. 4); контрольная (деф. 1–4).
5.4 Выбор средств технологического оснащения и расчет режимов выполнения технологических операций
При разработке операций технологического процесса восстановления детали последовательно решаются следующие задачи: выбор основного оборудования; выбор вспомогательных материалов (сварочных, наплавочных и т. д.); формирование содержания и последовательности переходов; выбор средств технологического оснащения (приспособлений, вспомогательного, режущего, слесарно-монтажного, специального инструмента и средств измерений); назначение и расчет технологических режимов и норм времени.
|
|
Разработку технологических операций производят, используя литературные источники [2–6].
При выборе основного оборудования учитывается: вид обработки; требуемая точность обработки поверхностей; габаритные размеры детали; принятая схема базирования; экономичность выполнения операции.
При выборе вспомогательных материалов (сварочных, наплавочных проволок, лент и т. д.) учитываются требования к физико-механическим свойствам (твердости, износостойкости) восстанавливаемых поверхностей.
Выбор средств технологического оснащения производится в зависимости от геометрических размеров детали, точности ее установки, физико-механических свойств поверхностей (твердости, пределов прочности), точности обработки и контроля.
Назначение и расчет режимов и норм времени нанесения металлопокрытий производится по рекомендациям [2–7], механической обработки – по [8–10].
Порядок разработки и описания технологической операции:
– номер и наименование;
– выбор основного оборудования (наименование и обозначение);
– выбор вспомогательных материалов (проволок, лент, электролитов и т. д.);
– определение содержания вспомогательного перехода (при его наличии);
– выбор технологического оснащения вспомогательного перехода;
– определение вспомогательного времени на установку и закрепление детали;
– определение содержания технологического перехода с указанием исполнительных размеров и технических требований на его выполнение;
– выбор технологического оснащения технологического перехода;
– назначение и расчет технологических режимов и норм времени (основного вспомогательного, дополнительного);
– обоснование подготовительно-заключительного времени на выполнение операции;
– расчет технической нормы времени.
005 Слесарная. Переход 1 . Содержание операции: рассверлить отверстие Ø8,75 мм, длина L = 12 мм (деф. 1).
Оборудование, технологическая оснастка и инструмент: станок настольно-сверлильный ГС-2112, тиски с призматическими губками ГОСТ 21168–75, сверло Р9 ГОСТ 2092–77/2301-4001.
Режимы обработки: глубина резания t = (0,5 × D)/2 = (0,5 × 8,75)/2 = 2,18 мм, скорость резания V = 32 м/мин. Подача для настольно-сверлильного станка ГС-2112 – ручная, согласно паспортным данным станка.
Число оборотов шпинделя определяется по следующей зависимости:
(5.3)
где V – скорость резания, м/мин;
D – диаметр отверстия, мм.
мин-1.
По паспортным данным настольно-сверлильного станка ГС-2112 принимаем n = 1180 мин-1.
Пересчитаем скорость резания с условием принятой частоты вращения шпинделя:
(5.4)
м/мин.
Переход 2. Содержание: нарезать резьбу М10×1,27-7Н, длина l = 12 (деф. 1).
Оборудование, технологическая оснастка и инструмент: станок настольно-сверлильный ГС-2112, тиски с призматическими губками ГОСТ 21168–75, метчик Р6М5 ГОСТ 3266-81/2620-3721.
Режимы обработки: глубина резания t = (0,5 × D)/2 = (0,5 × 8,75)/2 = 2,18 мм, скорость резания V = 14,3 м/мин. Подача для настольно-сверлильного станка ГС-2112 – ручная, согласно паспортным данным станка.
Число оборотов шпинделя определяется по зависимости 5.3:
мин-1.
По паспортным данным настольно-сверлильного станка ГС-2112 принимаем n = 520 мин-1.
Пересчитаем скорость резания с условием принятой частоты вращения шпинделя:
м/мин.
Переход 3. Содержание: установить резьбовую спиральную вставку М8-6Н (деф. 1).
Оборудование, технологическая оснастка и инструмент: верстак 1468-01-060А, тиски с призматическими губками ГОСТ 21168–75, комплект резьбовых спиральных вставок и приспособлений ОР-5526-ГОСНИТИ.
010 Фрезерная. Содержание операции: фрезеровать шпоночный паз под сегментную шпонку под углом 180° относительно изношенного паза, выдерживая ширину шпоночного паза h = мм, остальные размеры – согласно ремонтному чертежу (деф. 3).
Оборудование, технологическая оснастка и инструмент: универсально-фрезерный станок 6Р82Ш, фреза дисковая Т15К6 ГОСТ 6396/2234-0133, тиски с призматическими губками ГОСТ 21168–75.
Режимы резания:с учетом того что фрезерование производится фрезой диаметром 50 мм, по справочнику можно выбрать подачу фрезы: мм/об [9, 10]. Зная диаметр фрезы, глубину паза и подачу можно выбрать также скорость резания Vр=50 м/мин и частоту вращения шпинделя
мин-1, Sz – подача на зуб, мм/зуб; Sz = 0,1 мм/зуб, согласно паспортным данным станка.
Пересчитаем скорость резания, с учетом диаметра фрезы и принятой частоты вращения шпинделя:
(5.5)
где Dф – диаметр фрезы, мм;
– частота вращения шпинделя, мин-1.
м/мин.
Согласно паспортным данным универсально-фрезерного станка 6Р82Ш принимаем скорость резания м/мин.
015 Токарная. Содержание операции: точить поверхность, выдерживая размеры Ø15 мм, L = 23 мм (деф. 4).
Оборудование, технологическая оснастка и инструмент: станок токарный 16К20, патрон самоцентрирующийся трехкулачковый ГОСТ 2675–80, центр станочный вращающийся ГОСТ 8742–85, резец проходной Р6М5 2101-0501 ГОСТ 18868–73.
Режимы резания: подача S при черновом продольном точении принимаем в зависимости от глубины резания и диаметра детали, предпочтение отдаем одинаковым режимам для упрощения настройки станка. Согласуем подачу с технической характеристикой станка 16К20 и принимаем S = 0,25 мм/об, скорость резания выбираем в зависимости от глубины резания и подачи. Обработку ведем с охлаждающей жидкостью резцом проходным Р6М5 2101-0501 ГОСТ 18868–73. Vр = 34 м/мин, согласно паспортным данным станка.
Припуск на обработку определяем по следующей зависимости:
(5.6)
где D – номинальный диаметр, мм;
d – требуемый диаметр, мм.
Припуск на обработку для дефекта 4:
мм.
Установленную скорость резания проверим на ее соответствие оборотам шпинделя токарного станка, на котором обрабатывается деталь, по формуле:
(5.7)
где Vр – скорость резания, м/мин;
D – номинальный диаметр, мм.
Частота вращения шпинделя для дефекта 4:
мин-1.
Согласно паспортным данным токарного станка 16К20 принимаем частоту вращения шпинделя n = 680 мин-1.
020 Электроискровая обработка. Содержание операции: нанести на дефектный участок поверхности валика под подшипник бугристый слой металлопокрытия, произвести выравнивание нанесенного покрытия оплавлением бугров (деф. 2)
Оборудование, технологическая оснастка и инструмент: электроискровая установка «БИГ-4»; электрод Т15К6, верстак 1468-01-060А; приспособление с опорными роликами для установки тел вращения; набор гаечных ключей ГОСТ 2880–78.
Режимы электроискровой обработки: энергетический режим 5 (I = 3,8 A, V = 96 В, С = 360 мкФ, Е = 1,66 Дж), частота подачи импульсов 250 Гц, скважность 2–3, напряжение на катушке вибратора 24 В, диаметр электрода 2–3 мм, угол наклона электрода к поверхности 30–50°.
025 Наплавочная . Содержание операции: наплавить поверхность, выдерживая размер Ø16,6 мм, L = 23 мм (деф. 4).
Оборудование, технологическая оснастка и инструмент: сварочный полуавтомат ПДГ-312.2, головка ОКС-125 ГОСНИТИ, углекислый газ ГОСТ 8550–75, проволока Нп 0,8 30ХГСА ГОСТ 1050–74. Базирование детали осуществляем в патроне трехкулачковом ГОСТ 2675-80 и центре станочном ГОСТ 8742-85.
Режимы наплавки:диаметр проволоки 0,8 мм, полярность – обратная, сила сварочного тока Iсв = 100 А, напряжение U = 18 В, скорость наплавки Vн = 0,4 м/мин, расход защитного газа (СО2) Q = 8 л/мин, шаг наплавки S = 2d = 2 ∙ 0,8 = 1,6 мм/об, вылет электрода l = 12 мм.
Частота вращения определяется по формуле
(5.8)
где Vн - скорость наплавки, м/мин;
d - номинальный диаметр наплавляемого участка детали, мм.
Частота вращения для дефекта 4:
мин-1.
Согласно паспортным данным токарного станка 16К20 принимаем частоту вращения шпинделя мин-1.
030 Слесарная . Содержание операции: снять черновой слой нанесенного металлопокрытия, оставляя толщину не более 20 мкм, контролировать толщину оставшегося слоя (деф. 2).
Оборудование, технологическая оснастка и инструмент: верстак 1468-01-060А; шлифовальная машинка с гибким валом; тиски 7200-0008 0160 ГОСТ 14094–80; комплект абразивных накладок на гибкий вал; приспособление с опорными роликами для установки тел вращения; микрометр рычажный ГОСТ 4381–87.
Режимы: скорость вращения вала шлифовальной машины 400 мин-1, подача – ручная.
035 Слесарная . Содержание операции: установить и закрепить валик в патроне станка, установить режимы и включить станок, включить полировальную установку и совершить один проход полировки, выдерживая размеры Ø
мм, L= 13 мм, шероховатость поверхности Ra = 1,25 мкм, контролировать качество поверхности (деф. 2).
Оборудование, технологическая оснастка и инструмент: токарно-винторезный станок 16К20; полировальная установка; комплект абразивных накладок на полировальную установку; эталонный образец.
Режимы: скорость вращения станка n1 = 12,5 мин-1; подача S = 3,5 мм/об; скорость вращения вала полировальной установки n2 = 12 000 мин-1.
040 Токарная . Содержание операции: точить поверхность, выдерживая размеры Ø16,3 мм, L = 23 мм (деф. 4), снять фаску согласно ремонтному чертежу.
Оборудование, технологическая оснастка и инструмент: станок токарный 16К20, патрон самоцентрирующийся трехкулачковый ГОСТ 2675–80, центр станочный вращающийся ГОСТ 8742–85, резец проходной Р6М5 2101-0501 ГОСТ 18868–73.
Режимы резания: подача S при черновом продольном точении принимаем в зависимости от глубины резания и диаметра детали, предпочтение отдаем одинаковым режимам для упрощения настройки станка. Согласуем подачу с технической характеристикой станка 16К20 и принимаем S = 0,25 мм/об, скорость резания выбираем в зависимости от глубины резания и подачи. Обработку ведем с охлаждающей жидкостью, скорость резания Vр = 34 м/мин.
Припуск на обработку для дефекта 4 определим, используя зависимость 5.6:
мм.
Установленную скорость резания проверим на ее соответствие оборотам шпинделя токарного станка, на котором обрабатывается деталь, используя зависимость 5.7:
мин-1.
Согласно паспортным данным токарного станка 16К20 принимаем частоту вращения шпинделя n = 680 мин-1.
045 Токарная . Содержание операции: нарезать резьбу М16-6g (деф. 4).
Оборудование, технологическая оснастка и инструмент: станок токарно-винторезный 16К20, патрон самоцентрирующийся трехкулачковый ГОСТ 2675–80, центр станочный вращающийся ГОСТ 8742–85, резец для наружной метрической резьбы Р6М5 2660-0001 ГОСТ 18885–73.
Режимы обработки: подача – по таблице 27, S=0,6 мм/об, скорость резания – по таблице 30, V =17 м/мин, припуск на обработку h1 = 0,3 мм [9, 10].
Частота вращения шпинделя рассчитаем по формуле (5.7):
мин-1.
Согласно паспортным данным токарного станка 16К20 принимаем частоту вращения шпинделя n = 340 мин-1.
050 Контрольная . Содержание операции: провести контроль восстановленной детали.
Оборудование, технологическая оснастка и инструмент: стол контролера ОРГ-8964–79; штангенциркуль ШЦ-2 ГОСТ 166–89; микрометр гладкий МК-25 ГОСТ 6507–90; лупа 10-кратного увеличения ГОСТ 25706-83; резьбовой калибр-кольцо ГОСТ 17763–72; резьбовой калибр-пробка ГОСТ 24997–81; шпонка сегментная ШВ-5х19 ГОСТ 23360–80, образцы шероховатости ГОСТ 9378–75.
Дата добавления: 2018-11-24; просмотров: 325; Мы поможем в написании вашей работы! |
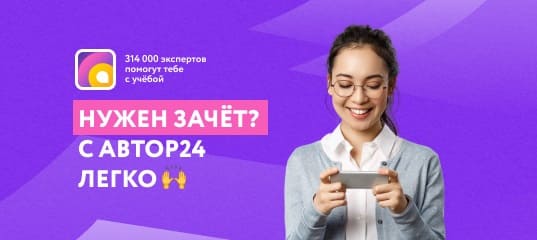
Мы поможем в написании ваших работ!