Выбор способов и средств контроля дефектов
Для обнаружения скрытых дефектов, проверки твердости, контроля взаимного положения элементов деталей используют специально предназначенные для этого приборы и приспособления, такие как дефектоскопы, магнитные, ультразвуковые, люминесцентные, твердомеры и т. д.
Для повышения эффективности визуального контроля используются лупы 10-кратного увеличения (ГОСТ 25706–83).
Остукиванием выявляют малозаметные трещины, ослабление заклепочных и резьбовых соединений, появление зазоров в соединениях с натягом.
Опробованием вручную, завертывая и отвертывая резьбовые калибры-кольца, определяется пригодность резьб (ГОСТ 17763–72), состояние подшипников качения и подвижных соединений.
Для контроля отклонения размеров и формы поверхностей применяется специальный (калибры, шаблоны) и универсальный измерительный инструмент.
Для контроля валов используют предельные калибры–скобы (ГОСТ 24851–81, ГОСТ 18355–73, ГОСТ 18356–79), для контроля отверстий – калибры–пробки (ГОСТ 24997–81).
Для определения дефектов, указанных в задании, применяем следующий инструмент: штангенциркуль ШЦ-2 ГОСТ 166–89; микрометр гладкий МК-25 ГОСТ 6507–90; лупа 10-кратного увеличения ГОСТ 25706–83; резьбовой калибр-кольцо ГОСТ 17763–72; резьбовой калибр-пробка ГОСТ 24997–81; шпонка сегментная ШВ-5х19 ГОСТ 23360–80.
При дефектации детали сортируют на три группы: годные к дальнейшему использованию без восстановления, цвет маркировки – зеленый; требующие восстановления, цвет маркировки – белый и подлежащие выбраковке, цвет маркировки – красный.
|
|
Разработка карты дефектации и ремонта
Карта дефектации и ремонта заполняется на основании разработанного технологического маршрута дефектации, а также технологических требований на восстановление детали.
При дефектации валика 50-11307052-Б используется следующее оборудование, технологическая оснастка и инструмент: стол дефектовщика ОРГ-8964–79; штангенциркуль ШЦ-2 ГОСТ 166–89; микрометр гладкий МК-25 ГОСТ 6507–90; лупа 10-кратного увеличения ГОСТ 25706–83; резьбовой калибр-кольцо ГОСТ 17763–72; резьбовой калибр-пробка ГОСТ 24997–81; шпонка сегментная ШВ-5×19 ГОСТ 23360–80.
Технологический маршрут дефектации детали включает следующие операции:
1) контролировать выбраковочные признаки на наличие трещин, коррозии, рисок, надиров и наволакивания. При обнаружении указанных дефектов деталь выбраковывается;
2) контролировать наличие износа и повреждений внутренней резьбы М8-7Н (деф. 1);
3)контролировать износ шейки валика под шарикоподшипник до размера менее Ø19,98 мм (деф. 2);
4) контролировать износ шпоночного паза по ширине до размера более 5,02 мм (деф. 3);
|
|
5) контролировать повреждение наружной резьбы М16-6g (деф. 4).
При наличии износа и повреждений (деф. 1–4) деталь восстанавливать.
Таблица 4.1 – Карта дефектации и ремонта валика 50-11307052-Б
| |||||
№ дефекта | Возможные дефекты и выбраковочные признаки | Метод установления дефекта | Средства контроля | Заключение | Требования после ремонта |
1 | 2 | 3 | 4 | 5 | 6 |
1 | Повреждение внутренней резьбы М8-7Н | Осмотр, опробование | Калибр-пробка ГОСТ 24997–81 | Ремонтировать | М8-6Н, вмятины, забоины, выкрашивание и срыв более двух ниток резьбы не допускается |
2 | Износ шейки валика под шарикоподшип- ник до размера менее Ø19,98 мм | Измерение | Микрометр гладкий ГОСТ 6507–90 | Ремонтировать | Ø ![]() |
3 | Износ шпоночного паза по ширине до размера более 5,02 мм | Измерение, опробование | Штанген- циркуль ШЦ-2 ГОСТ 166–89, шпонка сегментная ШВ-5×19 ГОСТ 23360–80. | Ремонтировать | ![]() |
4 | Износ наружной резьбы М16-6g | Осмотр, опробование | Резьбовой калибр-кольцо ГОСТ 24997–81 | Ремонтировать | М16-6g, вмятины, забоины, выкрашивание и срыв более двух ниток резьбы не допускается |
5 Проектирование технологического процесса ремонта (восстановления) детали
|
|
Дата добавления: 2018-11-24; просмотров: 424; Мы поможем в написании вашей работы! |
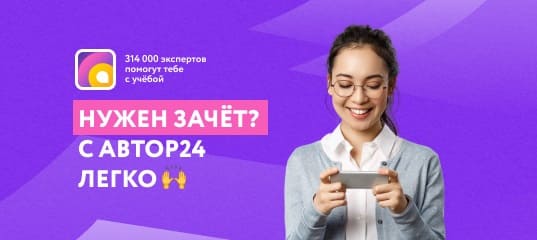
Мы поможем в написании ваших работ!