Exercise 2. Read Text A. Define the forms and functions of the underlined infinitives. Explain the cases when the infinitives are used without particle “to”.
Exercise 3. Translate the following sentences paying attention to the infinitives:
1. The frame may have fuel and hydraulic fluid tanks.
2. The overhead guard helps to protect the operator from falling objects.
3. Pole attachments are used to lift rolls.
4. The tilt provides an ability to operate on non-level ground.
5. While steering, it is unnecessary to apply steering force to maintain a constant rate of turn.
6. To combine the gravitational and centrifugal forces means to produce a tip-over accident.
7. A forklift should not be used as a personnel lift.
8. The most common task of a telescopic handler is to move the loads.
Exercise 4. Translate the following sentences paying attention to the infinitive constructions:
1. This attachment enables the operator to move the forks.
2. As the boom extends it causes the vehicle to become increasingly unstable.
3. A loader is known to be a heavy equipment machine often used in construction.
4. Draglines are considered to be the largest mobile equipment.
5. UDD is claimed to represent the first fundamental change to draglines for almost a century.
6. Two hoist and one drag ropes permit the operator to have better control.
Exercise 5. Translate Text B without a dictionary:
Text B
DRAGLINE EXAMPLES
The coal mining dragline known as Big Muskie, owned by the Central Ohio Coal Company (a division of American Electric Power), was the world's largest mobile earth-moving machine, weighing nearly 13,000 metric tons and standing nearly 22 stories tall. It operated in Guernsey County, in the US state of Ohio from 1969 to 1991, and was powered by 13,800 volts of electricity.
The British firm of Ransomes & Rapier produced a few large (1400-1800 ton) excavators, the largest in Europe at the time (1960s). Power was from internal combustion engines driving electric generators. One, named Sundew, was used in a quarry from 1957 to 1974. After its working life at the first site in Rutland was finished it walked 13 miles to a new life at Corby; the walk took 9 weeks.
Smaller draglines were also commonly used before hydraulic excavators came into common use, the smaller draglines are now rarely used other than on river and gravel pit works. The small machines were of a mechanical drive with clutches. Firms such as Ruston and Bucyrus made models such as the RB10 which were popular for small building works and drainage work. Several of these can still be seen in the English Fens of Cambridgeshire, Lincolnshire and parts of Norfolk. Ruston's is a company also associated with drainage pumping engines. Electric drive systems were only used on the larger mining machines, most modern machines use a diesel-hydraulic drive, as machines are seldom in one location long enough to justify the cost of installing a substation and supply cables.
|
|
Notes:
pit - яма, шахта, карьер
justify - оправдывать
substation - подстанция
Exercise 6. Translate Text C with a dictionary and make its grammar analysis:
Text C
DRAGLINES IN MINING
1. A large dragline system used in the open pit mining industry costs approximately US$50-100 million. 2. A typical bucket has a volume ranging from 30 to 60 cubic metres, though extremely large buckets have ranged up to 168 cubic metres. 3. The length of the boom ranges from 45 to 100 metres. 4. In a single cycle it can move up to 450 metric tonnes of material.
5. Most mining draglines are not diesel-powered like most other mining equipment. 6. Their power consumption is so great that they have a direct connection to the high-voltage grid at voltages of between 6.6 to 22 kV. 7.A typical dragline, with a 55 cubic metre bucket, can use up to 6 megawatts during normal digging operations. 8. Because of this, many stories have been told about the black-out* causing effects of mining draglines. 9. For instance, there is a long-lived story that, back in the 1970s, if all seven draglines at Peak Downs Mine (a very large BHP coal mine in central Queensland, Australia) turned simultaneously, they would black-out all of North Queensland. 10. However even now, if they have been shut down they are always restarted one at a time due to the immense power requirements of start up.
11. In all but the smallest of draglines, movement is accomplished by "walking" using feet or pontoons, as caterpillar tracks place too much pressure on the ground, and have great difficulty under the immense weight of the dragline. 12. Maximum speed is only at most a few metres per minute since the feet must be repositioned for each step. 13. If travelling medium distances, (about 30-100 km), a special dragline carrier can be brought in to transport the dragline. 14. Above this distance, disassembly is generally required. 15. But mining draglines due to their reach can work a large area from one position and do not need to constantly move along the face like smaller machines.
|
|
*block-out - временное отсутствие электрического освещения
1. Subject and predicate; participle II (function); ing-form.
2. Meaning of “have”.
3. Predicate.
4. Modal verb; meaning of “it”.
5. Meaning of “like”; superlative degree.
6. Noun groups.
7. Ing-forms.
8. Subject and predicate.
9. Translation of “there is”; conditional sentence.
11. Superlative degree; gerund (function); meaning of “as”.
12. Meaning of “since”; modal verb.
13.Infinitives (function).
14.Participle II (function).
15.Subject and predicate; infinitives (function); comparative degree.
Unit 7
Grammar: Complex Sentences.
Text A
TUNNEL BORING MACHINES
I
A tunnel boring machine (TBM) is a specially designed machine which is used to excavate tunnels with a circular cross section through a variety of soil and rock strata.That they can bore through hard rock, sand, and almost anything in between is one of their advantages. Tunnel diameters can range from a metre (done with micro-TBMs) to almost 16 metres to date. Tunnels of less than a metre or so in diameter are typically done by horizontal directional drilling rather than TBMs.
Tunnel boring machines are used as an alternative to drilling and blasting (D&B) methods. The reason of this is that a TBM has the advantages of limiting the disturbance to the surrounding ground and producing a smooth tunnel wall. This significantly reduces the cost of lining the tunnel, and makes TBM suitable to use in heavily urbanized areas. The major disadvantage is that TBMs are expensive to construct, difficult to transport and require significant infrastructure. The biggest is built by Herrenknecht AG of Schwanau, Germany to dig the 57 km Gotthard Base Tunnel. It has a diameter of 9.58 meters.
|
|
Tunnel boring machines have one or two large metal cylinders (shields) mounted on a trailing support mechanism. The front of the shield has a rotating cutting wheel. Following the cutting wheel there is a chamber where the excavated material (sand, rock, or any soil mix) is either mixed with water to make a slurry or leftas it is. A system to remove the excavated material completes the tunnel boring machine.
In basic terms, the TBMs work like an earthworm with cycles of digging forward and dragging the rear end afterwards. A series of hydraulic systems pushes the TBM forward (excavating the soil) while the rear end of it is braced against the tunnel wall.When the TBM head has excavated at its maximum length (this depends on many variables including TBM type, soil type, etc) the front end of the TBM is braced against tunnel wall and the rear end is pulled forward. These cycles continue until the complete tunnel has been excavated.
II
Behind the shield, inside the finished part of the tunnel, several support mechanisms which are part of the TBM are located: dirt removal, slurry pipelines if they are applicable, control rooms, and rails for transport of the precast segments. The cutting wheel will typically rotate at 1 to 10 rpm (depending on the size and stratum), cutting the rock face into chips or excavating soil (muck). Depending on the type of TBM, the muck will fall onto a conveyor belt system and be carried out of the tunnel, or be mixed with slurry and pumped back to the tunnel entrance. Depending on rock strata and tunnel requirements, the tunnel may be cased, lined, or left unlined. This may be done by bringing in precast concrete sections that are jacked into placeas the TBM moves forward, by assembling concrete forms, or in some hard rock strata, leaving the tunnel unlined and relying on the surrounding rock to handle and distribute the load.
While the use of a TBM eliminates the need for large numbers of workers at increased pressure, a caisson system is sometimes formed at the cutting head. Workers entering this space for inspection, maintenance and repair need to be medically "fit to dive" and trained in the operation of the locks.
|
|
Modern TBMs typically have an integrated shield. What type of TBM, a single or double shielded, will be chosen depends on the type of rock strata and the excavation speed required.
Double shielded TBMs are normally used in unstable rock strata, or where a high rate of advancement is required. Single shielded TBMs, which are less expensive, are more suitable to hard rock strata.
In urban tunneling it is required that the ground surface should be undisturbed. This means that ground falling must be avoided. The normal method of doing this is to maintain the soil pressures during and after the tunnel construction. There is some difficulty in doing so, particularly in varied rock strata (e.g., boring through a region where the upper portion of the tunnel face is wet sand and the lower portion is hard rock).
TBMs with positive face control are used in such situations. There are three common types: Earth pressure balance (EPB), Bentonite slurry (BS), and compressed air (CA). The compressed air method is the oldest, although it is falling out of application due to the difficult working conditionsit imposes. Both types (EPB and BS) are clearly preferred over open face methods in urban environments as they offer far superior ground control.
Active Vocabulary:
drill - бурить, сверлить
blast - взрыв; взрывать
disturbance - нарушение, повреждение
line - выложить, облицевать
shield - щит, экран
chamber - камера
slurry - жидкая глина
term - термин
brace - скоба, связь; связывать
entrance - вход
case - кожух; обшивать, покрывать
precast - предварительно отлитый, сборный
enter - входить
integrate - составлять целое, объединять
avoid - избегать
impose - налагать
prefer - предпочитать
environment - окружение, окружающая среда
Exercise 1. Answer the following questions:
1. What materials can TBMs bore through?
2. Why are the TBMs used as an alternative to drilling and blasting methods?
3. What main components does a TBM have?
4. What cycles does the TBM’s work consist of?
5. How may the tunnel be finished?
6. Where are double shielded TBMs normally used?
7. What requirements should be met in urban tunneling?
8. Why are EPB and BS types preferred in urban environment?
Exercise 2. Read Text A. Analyze the underlined subordinate clauses, define their types and the forms of their predicates.
Exercise 3. Translate the following sentences paying attention to attributive clauses:
a)without a conjunction:
1. A system the excavated material is removed with completes the TBM.
2. The purpose the counterweight is used for is to balance the load.
3. The speed the cutting wheel rotates with depends on the size.
4. The air the piston compresses is heated to the point of ignition.
b)with different meanings of “which”:
1. The carriage is the component to which the forks are mounted.
2. To put the load on high places requires a crane, which is not always practical or time-efficient.
3. Most telehandlers utilize a computer which uses sensors to monitor the vehicle.
4. Some machines are equipped with outriggers, which extend the lifting capability.
5. The operator is able to “steer” the load, which can be useful.
6. The house is able to rotate without limit due to a hydraulic distribution valve which supplies oil to the undercarriage components.
7. The weight is raised, which may involve the use of hydraulics.
Exercise 4. Translate Text B without a dictionary:
Text B
TBMs INVENTION
The first successful tunneling shield was developed by Sir Marc Isambard Brunel to excavate the Thames Tunnel in 1825. However, this was only the invention of the shield concept and did not involve the construction of a complete tunnel boring machine, the digging still having to be accomplished by the then standard excavation methods.
The very first boring machine ever reported to have been built was Henri-Joseph Maus' Mountain Slicer. Commissioned by the King of Sardinia in 1845 to dig the Frejus Rail Tunnel between France and Italy through the Alps, Maus had it built in 1846 in an arms factory near Turin. It basically consisted of more than 100 percussion drills mounted in the front of a locomotive-sized machine, mechanically power-driven from the entrance of the tunnel. Unfortunately, the Revolutions of 1848 affected the financing of the project and the tunnel was not completed until 10 years later, by using also innovative but rather less expensive methods such as pneumatic drills.
In the United States, the first boring machine to have been built was used in 1853 during the construction of the Hoosac Tunnel. Made of cast iron, it was known as Wilson’s Patented Stone-Cutting Machine, after its inventor Charles Wilson. It drilled 10 feet into the rock before breaking down. The tunnel was eventually completed more than 20 years later, and as with the Frejus Rail Tunnel, by using less ambitious methods.
In the early 1950s, F.K. Mitry won a diversion dam contract for the Oahe Dam in Pierre, South Dakota , and consulted with James S. Robbins to dig through what was the most difficult shale to excavate at that time, the Pierre Shale. Robbins built a machine that was able to cut 160 feet in 24 hours in the shale, which was ten times faster than any other digging speed at that time.
The breakthrough that made tunnel boring machines efficient and reliable was the invention of the rotating head, conceptually based on the same principle as the percussion drill head of the Mountain Slicer of Henri-Joseph Maus. But its efficiency was improved by reducing the number of grinding elements while making them to spin as a whole against the soil front. Initially, Robbins' tunnel boring machine used strong spikes rotating in a circular motion to dig out of the excavation front, but he quickly discovered that these spikes, no matter how strong they were, had to be changed frequently as they broke or tore off. By replacing these grinding spikes with longer lasting cutting wheels this problem was significantly reduced. Since then, all successful modern tunnel boring machines have rotating grinding heads with cutting wheels.
Notes:
concept - идея
percussion drill - ударный бур
diversion dam - отводная плотина
shale - сланец, сланцевая глина
Unit 8
Grammar: Functions of “that” and “one”
Text A
PILE DRIVER
I
A pile driver is a mechanical device that is used to drive piles into soil to provide foundation support for buildings or other structures. That term is also used in reference to members of the construction crew that work with pile driving rigs.
One traditional type of pile driver includes a heavy weight placed between guides so that it is able to freely slide up and down in a single line. It is placed upon a pile. The weight is raised, which may involve the use of hydraulics, steam, diesel, or manual labour. When the weight reaches its highest point it is then released and smashes on to the pile in order to drive it into the ground.
Ancient pile driving equipment used manual or animal labour to lift heavy weights, usually by means of pulleys, to drop the weight onto the end of the pile. Modern pile driving equipment uses various methods to raise the weight and guide the pile.
There are several types of pile driving equipment.
Diesel hammer A modern diesel pile hammer is a very large two-stroke diesel engine. The weight is the piston, and the apparatus which connects to the top of the pile is the cylinder. Piledriving is started by having the weight raised by auxiliary means — usually a cable from the crane holding the pile driver — which draws air into the cylinder. The weight is dropped, using a quick-release. The weight of the piston compresses the air, heating it to the ignition point of diesel fuel. Diesel fuel is added/injected into the cylinder. The mixture ignites, transferring the energy of the falling weight to the pile head, and driving the weight back up. The rising weight draws in more fuel-air mixture, and the cycle starts over until the fuel runs out or is stopped by the pile crew.
Hydraulic hammer. A hydraulic hammer is a modern type of piling hammer used in place of diesel and air hammers for driving steel pipe, precast concrete, and timber piles. Hydraulic hammers are more environmentally acceptable than the older, less efficient ones as they generate less noise and pollutants.
II
Hydraulic Press-in. Specialty equipment which installs piles using hydraulic rams to press piles into the ground. This system is preferred where vibration is a concern. There are press attachments that can adapt to conventional pile driving rigs to press two pairs of sheet piles at a time. Additional types of press equipment sit on top of existing sheet piles and grip onto previously driven piles. This system allows for greater press-in and extraction force to be used since more reaction force is developed. The reaction based machines operate at only 69dB at 23ft allowing for installation and extraction of piles in very close proximity to noise and vibration sensitive areas where traditional methods may threaten the stability of existing structures.
Such equipment and methods are specified into portions of the internal drainage system in the New Orleans area after Hurricane Katrina as well as many projects around the world where noise, vibrations and limited access are a concern during the engineering, design and construction phases of the project.
Vibratory Pile Driver/Extractor. Vibratory pile hammers contain a system of counter-rotating eccentric weights, powered by hydraulic motors, and designed in such a way that horizontal vibrations cancel out, while vertical vibrations are transmitted into the pile. The pile driving machine is lifted and positioned over the pile by the power of an excavator or that of a crane, and is fastened to the pile by a clamp and/or bolts. Vibratory hammers can either drive in or extract a pile; extraction is commonly used to recover steel "H" piles used in temporary foundation shoring*. Hydraulic fluid is typically supplied to the driver by a diesel engine powered pump mounted in a trailer or van and connected to the driver head through a set of long hoses. When the pile driver is connected to an excavator, it is powered by the excavator's own diesel engine. Vibratory pile drivers are often chosen to reduce noise, as when the construction is very close to residence or office buildings, or when there is not enough vertical clearance above the foundation to permit use of a conventional pile hammer (for example when fitting additional piles to a bridge column or abutment footing). Hammers are available with several different vibration rates, ranging from about 1200 vibrations per minute to about 2400 vpm; the vibration rate chosen is influenced by soil conditions at the site and other factors such as power requirements and purchase price of the equipment.
* shoring - установка временных (монтажных) опорных стоек
Active Vocabulary:
pile driver - свайный копер
crew - бригада
rig - буровая установка, копер
pile driving rig - сваебойная установка, копер
guide - направляющее приспособление
hammer - молот
manual - ручной; руководство
piston - поршень
auxiliary - вспомогательный
hold - захват; держать
ignite - зажигать, воспламенять
rise - подниматься
run out - истощаться
noise - шум
pollutant - загрязнитель
extract - вытаскивать, извлекать
fasten - прикреплять
hose - рукав, шланг
clearance - зазор, клиренс
Exercise 1. Answer the following questions:
1. What do piles provide?
2. How does a pile driver work?
3. What is the weight in a diesel pile hammer?
4. Why are hydraulic hammers more environmentally friendly?
5. Where are hydraulic press-in systems preferred?
6. When are vibratory pile drivers the most suitable?
Exercise 2. Read Text A and analyze the functions of the underlined words.
Exercise 3. Translate the following sentences paying attention to the functions of “one’ and “that”:
1. The cab is the area that contains a seat for the operator.
2. The truck is powered by the energy of the internal combustion engines or by that of electric motors.
3. The mast is operated by one or two hydraulic cylinders.
4. That type of attachment will speed the loading.
5. The L-2350 uses a diesel electric propulsion system similar to that used in a locomotive.
6. The front loader’s bucket capacity is much bigger than that of a backhoe.
7. One can’t classify loaders as earthmoving machines.
8. Excavators are produced in a wide variety of sizes. The smaller ones are called compact excavators.
9. That vibratory hammers can either drive in or extract a pile make them more widely used.
10.It is known that hydraulic hammers generate less noise.
Exercise 4. Translate Text B without a dictionary:
Text B
Дата добавления: 2018-10-26; просмотров: 207; Мы поможем в написании вашей работы! |
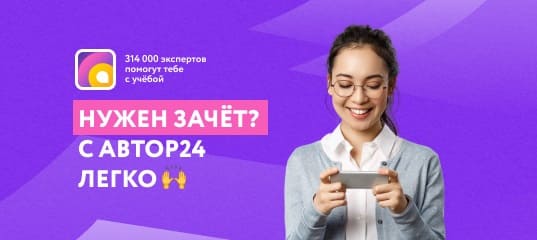
Мы поможем в написании ваших работ!